@Beantown
OK, Some comments:
You will find the Hitachi WJ200 technical manual at:
I draw your attention to page: 4-5 or pdf page #209.
This simplified drawing shows the connections to the VFD, including the logic connections
You may also wish to look at page: 3-115, pdf page 197 which shows more details about how to hook up devices to the intelligent inputs. Note that if current flows through the internal LEDs that are shown then the intelligent inputs become active. As an example, if you look at the bottom right diagram you will see a photo transistor connected to the P24 (Volt supply) and to the input#7/EB. If the external sensor photo transistor is turned on by illumination then current flows from P24 into input #7. This then goes through the internal resistor and LED which turns on the circuit transistor(not shown here). (This is what I meant by a current controlled device.) Note that there are two internal LEDs connected in parallel, but with reverse polarity. If the external power supplies are turned around so that current flows out of the intelligent input#7 then the input is again active. This polarity choice is explained a little more at page 4-4, pdf page#208 and is dependent upon how the PLD terminal is connected.
Now find the Yaskawa technical manual at:
This is a similar drawing showing the connections to the VFD.
Again the intelligent inputs are shown and appear to operate in a similar manner to those of the Hitachi device in their construction.
The internal LED current limiting resistors are not shown on the Hitachi drawing, but are mentioned in the note on this drawing, to the left of the inputs, to have a value of 4.7K Ohm. This resistance, plus the internal LED forward voltage drop, the external voltage, plus what ever is externally connected to the inputs determine the current into the LED and so how strong the signal is going to the optically isolate internal device. As I described in my write up I measured this current Vs. reliable operation before I designed my circuits. It was pretty easy to do. However, if you think about it a bit you will see that when using a 24V supply and assuming the LEDs have forward voltage drop of a couple of volts, then the maximum current flow would be (24-2)/4700= 4.7ma. Any sensor, or switch between the supply and the input terminal would decrease this. I discussed this and the minimum current needed in my write up.
The exact function of these intelligent inputs when active or non-active is "somewhat" controlled by the firmware coding, but the two VFDs are very similar in concept.
Also, note that both devices have a facility for speed control via a potentiometer. In both cases approximatly 10v to the input and the VFD is at full speed. (This seems to be pretty standard.)
By the way, the physical size of the Hitachi WJ200 is 108mm(W) x 128mm(H) x 170.5mm(D) (see page 2-10, pdf 56).
The physical size of the Yaskawa model B012A (I think this is the one) is 140mm(W) x 128(H) x 163(D) (see page 330).
These two are about the same H and D but the Yaskawa is 32mm wider (thicker). I slipped the heat sink down into the bottom cabinet of my built. But, to fit, yours might have to be raised up about an inch in the electronics cabinet in the lathe stand. You would have to look into this phsycal space. If you look at the photo of my build (URL below) you will see that the heat sink of the VFD goes down into the hole about an inch, but there appears to be room for your VFD to fit if it is higher as there is considerable room between the top of the VFD and the circuit boards above it. What is not so visiable in the photo is that I replaced the steel cover with a piece of 0.25 thick plexiglass and as long as I was doing this I built a frame out of black Nylon, that I had laying around, on the two sides and top to push the plexiglass out about an inch. I left the bottom open to allow cool air to enter. The Nylon forms a three sided box and does not let anything in on the top of sides. Everything fit without this extra 1" of Nylon provided space, but I did this because I I wanted to mount that exhaust fan on the inside ... and just wanted to give it some extra room away from any wires. Turned out that was not necesssary and that even the exhaust fan was probably not required. The heat sink of the VFD has a fan built into it to draw or push air through the heat sink fins. In the Hitachi you can flip the fan over to reverse the air direction if you want to do so. I did so, so that the air would flow through the heat sink and then flow around the e-braking resistors that are visible in the photo, mounted at the right hand side of the VFD. (The best I can tell these resistors never get warm anyway. One certainly does not need the physically big resistors that are commonly sold for big power breaking applications like you might see in a paper mill. I suspect that they use these in paper mills and maybe new paper printing where the speed of 5-6 ft rolls of paper must be continuously controlled.)
www.hobby-machinist.com
Dave L.
OK, Some comments:
You will find the Hitachi WJ200 technical manual at:
I draw your attention to page: 4-5 or pdf page #209.
This simplified drawing shows the connections to the VFD, including the logic connections
You may also wish to look at page: 3-115, pdf page 197 which shows more details about how to hook up devices to the intelligent inputs. Note that if current flows through the internal LEDs that are shown then the intelligent inputs become active. As an example, if you look at the bottom right diagram you will see a photo transistor connected to the P24 (Volt supply) and to the input#7/EB. If the external sensor photo transistor is turned on by illumination then current flows from P24 into input #7. This then goes through the internal resistor and LED which turns on the circuit transistor(not shown here). (This is what I meant by a current controlled device.) Note that there are two internal LEDs connected in parallel, but with reverse polarity. If the external power supplies are turned around so that current flows out of the intelligent input#7 then the input is again active. This polarity choice is explained a little more at page 4-4, pdf page#208 and is dependent upon how the PLD terminal is connected.
Now find the Yaskawa technical manual at:
https://ga500.yaskawa-perform.de/wp-content/uploads/2019/04/Documentation/GA500_Technical_Manual.pdf
Similarly look at page: 3.5, page 78. (Repeated at page 51)This is a similar drawing showing the connections to the VFD.
Again the intelligent inputs are shown and appear to operate in a similar manner to those of the Hitachi device in their construction.
The internal LED current limiting resistors are not shown on the Hitachi drawing, but are mentioned in the note on this drawing, to the left of the inputs, to have a value of 4.7K Ohm. This resistance, plus the internal LED forward voltage drop, the external voltage, plus what ever is externally connected to the inputs determine the current into the LED and so how strong the signal is going to the optically isolate internal device. As I described in my write up I measured this current Vs. reliable operation before I designed my circuits. It was pretty easy to do. However, if you think about it a bit you will see that when using a 24V supply and assuming the LEDs have forward voltage drop of a couple of volts, then the maximum current flow would be (24-2)/4700= 4.7ma. Any sensor, or switch between the supply and the input terminal would decrease this. I discussed this and the minimum current needed in my write up.
The exact function of these intelligent inputs when active or non-active is "somewhat" controlled by the firmware coding, but the two VFDs are very similar in concept.
Also, note that both devices have a facility for speed control via a potentiometer. In both cases approximatly 10v to the input and the VFD is at full speed. (This seems to be pretty standard.)
By the way, the physical size of the Hitachi WJ200 is 108mm(W) x 128mm(H) x 170.5mm(D) (see page 2-10, pdf 56).
The physical size of the Yaskawa model B012A (I think this is the one) is 140mm(W) x 128(H) x 163(D) (see page 330).
These two are about the same H and D but the Yaskawa is 32mm wider (thicker). I slipped the heat sink down into the bottom cabinet of my built. But, to fit, yours might have to be raised up about an inch in the electronics cabinet in the lathe stand. You would have to look into this phsycal space. If you look at the photo of my build (URL below) you will see that the heat sink of the VFD goes down into the hole about an inch, but there appears to be room for your VFD to fit if it is higher as there is considerable room between the top of the VFD and the circuit boards above it. What is not so visiable in the photo is that I replaced the steel cover with a piece of 0.25 thick plexiglass and as long as I was doing this I built a frame out of black Nylon, that I had laying around, on the two sides and top to push the plexiglass out about an inch. I left the bottom open to allow cool air to enter. The Nylon forms a three sided box and does not let anything in on the top of sides. Everything fit without this extra 1" of Nylon provided space, but I did this because I I wanted to mount that exhaust fan on the inside ... and just wanted to give it some extra room away from any wires. Turned out that was not necesssary and that even the exhaust fan was probably not required. The heat sink of the VFD has a fan built into it to draw or push air through the heat sink fins. In the Hitachi you can flip the fan over to reverse the air direction if you want to do so. I did so, so that the air would flow through the heat sink and then flow around the e-braking resistors that are visible in the photo, mounted at the right hand side of the VFD. (The best I can tell these resistors never get warm anyway. One certainly does not need the physically big resistors that are commonly sold for big power breaking applications like you might see in a paper mill. I suspect that they use these in paper mills and maybe new paper printing where the speed of 5-6 ft rolls of paper must be continuously controlled.)
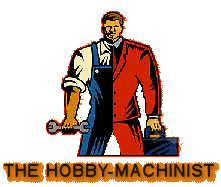
VFD conversion via solid state electronic components. PM1440GT, VFD, 3-phase
VFD conversion using solid state electronic components. I finally finished documenting my PM1440GT lathe VFD conversion and want share it. It took me longer to write this up than it did to actually build the new electronics! (Are these sorts of things every really finished?) I apologize...
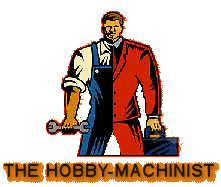
Dave L.