- Joined
- Mar 16, 2016
- Messages
- 40
Before I start the history about my ongoing restoration of my lathe, a few things about myself would be appropriate, I'm born in 62, got my apprenticeship as a machinist in 79, and finished in 83, worked a couple of years with agricultural and forest machines, then 13 years at the Lego factory, making automatic machines for assembly and decoration. The last many years I have been working at a tool factory repairing molds, and the last four years, testing the new molds on our four plastic injecting molding machines.
I admit, I am a cheapskate, if I can't get it for free, I want money to take it with me, that have proven to be a bit of a challenge when dealing with this type of machines.
IN 2012 I decided I wanted my own lathe and mill for when I am retiring, and started to look for the right size equipment, and I quickly discovered that the small size lathes I was dreaming about, came with a substantial price tag, or were way too old and missing many parts.
Every day for quite a while I was looking in our version of Craigs list, an one day this ad came up, "Good and old lathe for sale, motor dismounted, otherwise in working condition $500" (well the price was in Danish Kroner but i exchanged it to USD) i went to see it, and it turned up to be a Colchester / Clausing Triumph 7 1/2 x 48 (15 x 48 in the states) a bit rusty on the bedways, but nothing a bit of TLC wouldn't cure.
I bought it on the spot, and collected it the following Saturday.
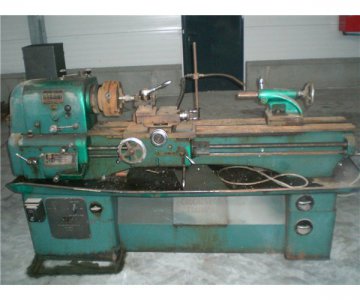
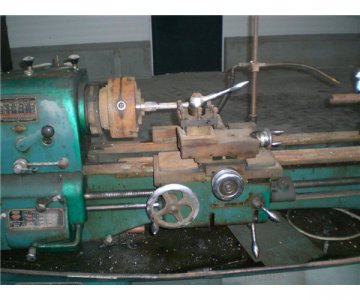
This was the state I found it in at the tractor and machine shop that had it for sale.
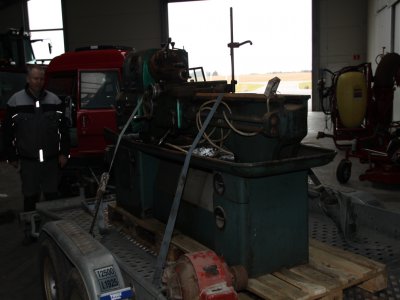
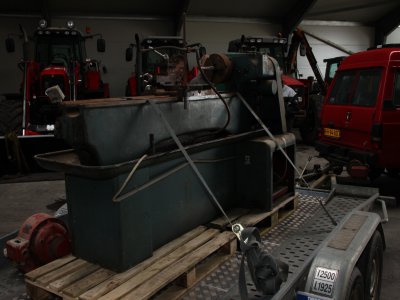
The following Saturday a friend and I got it loaded on a trailer, and got it home.
.
I admit, I am a cheapskate, if I can't get it for free, I want money to take it with me, that have proven to be a bit of a challenge when dealing with this type of machines.
IN 2012 I decided I wanted my own lathe and mill for when I am retiring, and started to look for the right size equipment, and I quickly discovered that the small size lathes I was dreaming about, came with a substantial price tag, or were way too old and missing many parts.
Every day for quite a while I was looking in our version of Craigs list, an one day this ad came up, "Good and old lathe for sale, motor dismounted, otherwise in working condition $500" (well the price was in Danish Kroner but i exchanged it to USD) i went to see it, and it turned up to be a Colchester / Clausing Triumph 7 1/2 x 48 (15 x 48 in the states) a bit rusty on the bedways, but nothing a bit of TLC wouldn't cure.
I bought it on the spot, and collected it the following Saturday.
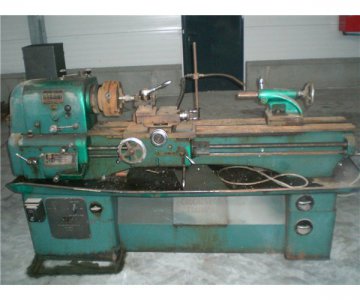
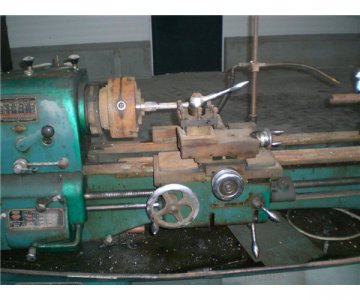
This was the state I found it in at the tractor and machine shop that had it for sale.
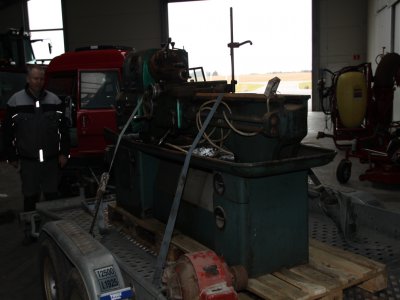
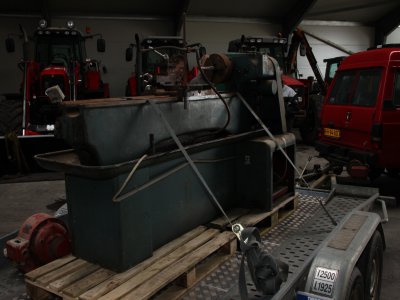
The following Saturday a friend and I got it loaded on a trailer, and got it home.
.