- Joined
- Jan 31, 2012
- Messages
- 212
My HF/Central Pneumatic 47065 compressor recently ran unattended a whole night with the pressure switch diaphragm broken. That means non-stop.
Once the switch was replaced, everything went fine for a while then it would not hold its pressure. The air was bleeding through the unload valve.
In fact, the Check Valve was the culprit with 2 little pieces of steel keeping it open.
After that was fixed, the compressor would hold its pressure but would not go over 20-30 PSI.
Time to go to the top! I took the head off, and sure enough the exhaust (high-pressure side) reed valve was broken.

It is just a U-shaped piece of spring sheet.
I can only guess that the night long run made it overheat and harden, making it brittle.
The pieces of steel in the check valve were in fact splinters from it.
Of course, no parts are to be found @ HF, so as any machinist would do I started building replacements.
The spring stock and gasket material were obtained from McMaster-Carr.


The thin steel can be rough-cut with [cheap HF] household scissors. Just make sure to stay away from any pair that may belong to SWMBO.

Getting the part to final shape is easily done with a Dremel tool; make sure to keep it cool enough not to harden it.

Cutting the gaskets to shape is done on a cutting board with an X-Acto knife. Marking the cuts is easily done by hammering the material onto the head or cylinder with a soft mallet.

The old gaskets were incredibly hard to scrape off, perhaps because of the excessive heat that started all this.


After a good cleaning, everything goes back together.


The cylinder is somewhat scored, but nothing too bad. There is still good compression.

The head bolts are Metric 8mm, grade 8.8. In the absence of manufacturer's instructions, 17 ft-lbs per standard tables was used to torque them down.
Total cost $27.64 in materials and a lot of experience gained.

Once the switch was replaced, everything went fine for a while then it would not hold its pressure. The air was bleeding through the unload valve.
In fact, the Check Valve was the culprit with 2 little pieces of steel keeping it open.
After that was fixed, the compressor would hold its pressure but would not go over 20-30 PSI.
Time to go to the top! I took the head off, and sure enough the exhaust (high-pressure side) reed valve was broken.

It is just a U-shaped piece of spring sheet.
I can only guess that the night long run made it overheat and harden, making it brittle.
The pieces of steel in the check valve were in fact splinters from it.
Of course, no parts are to be found @ HF, so as any machinist would do I started building replacements.
The spring stock and gasket material were obtained from McMaster-Carr.




The thin steel can be rough-cut with [cheap HF] household scissors. Just make sure to stay away from any pair that may belong to SWMBO.

Getting the part to final shape is easily done with a Dremel tool; make sure to keep it cool enough not to harden it.

Cutting the gaskets to shape is done on a cutting board with an X-Acto knife. Marking the cuts is easily done by hammering the material onto the head or cylinder with a soft mallet.

The old gaskets were incredibly hard to scrape off, perhaps because of the excessive heat that started all this.


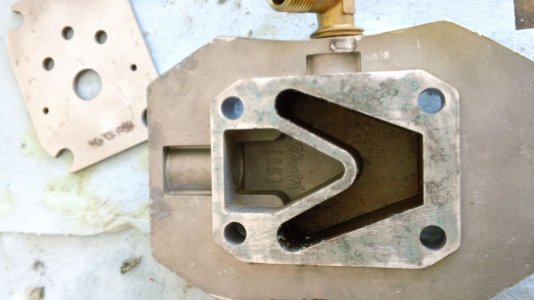

After a good cleaning, everything goes back together.





The cylinder is somewhat scored, but nothing too bad. There is still good compression.


The head bolts are Metric 8mm, grade 8.8. In the absence of manufacturer's instructions, 17 ft-lbs per standard tables was used to torque them down.
Total cost $27.64 in materials and a lot of experience gained.














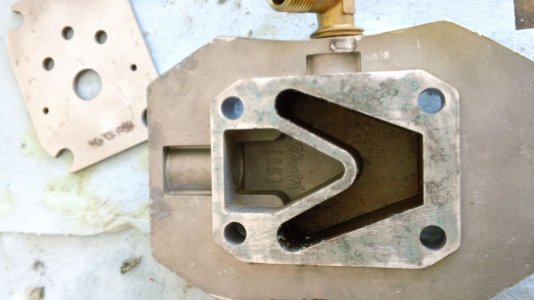



