I picked up a Logan 12 x 24 lathe in January just before I left for a 3 month work assignment in Japan. Had just enough time to clean the main machine ways and go over it to see what it needed before I left and ordered parts while I as gone. Found it on Craigslist, they guy had bought it intending to teach himself machine work, replaced the 440 3 phase motor with a 220 single phase (2hp), then never hooked it up. Sat for 8 years in his wood shop that way.
This is where I found it...
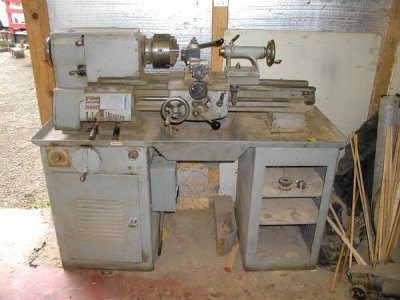
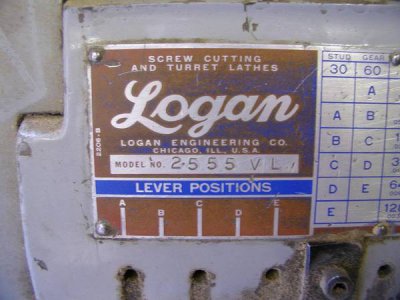
A bit of cleaning got it to here, which is where I left it while I was gone...
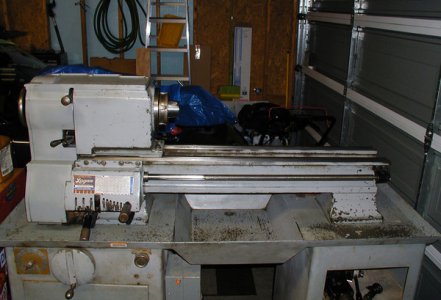
The last couple days I disassembled, cleaned, and reassembled the taper attachment...
Before:
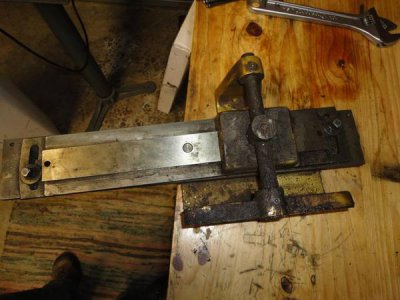
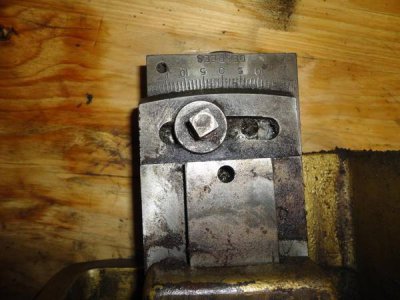
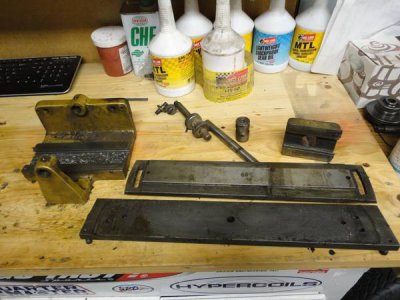
After:
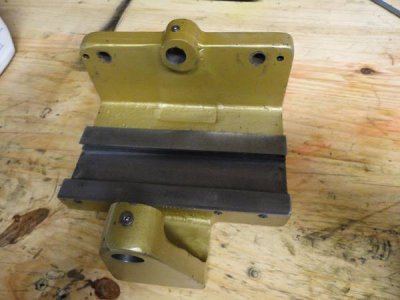
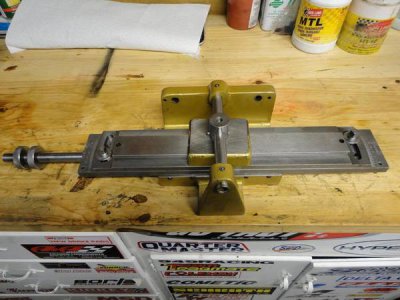
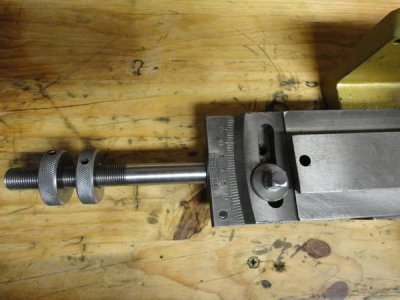
Tonight I started on the saddle/crosslide...
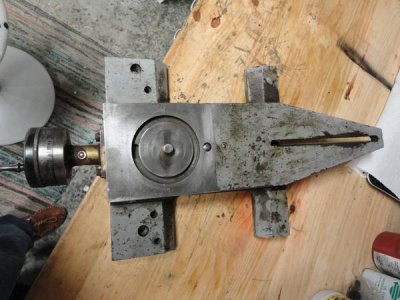
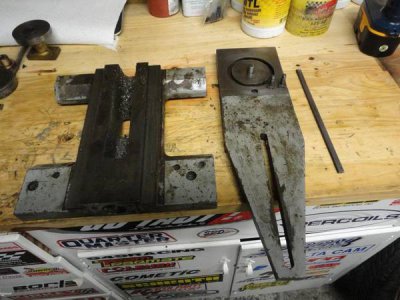
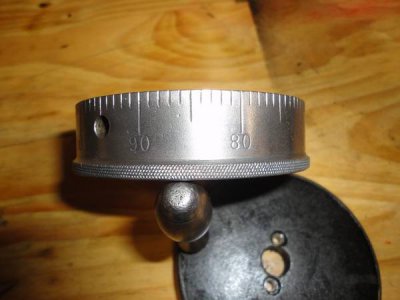
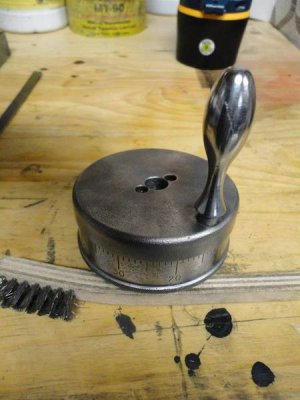
- - - Updated - - -
Oh, and the day I got back from Japan I picked this up... because I need more projects :rofl:
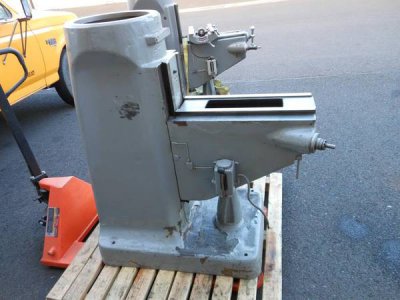
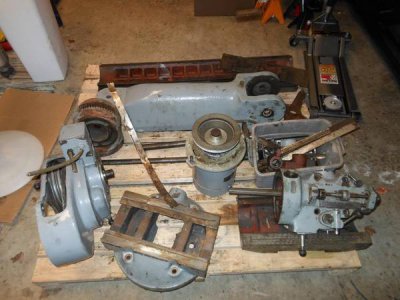
This will be another thread though...
This is where I found it...
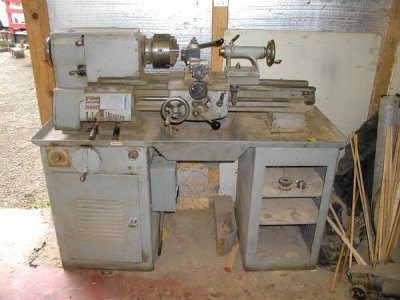
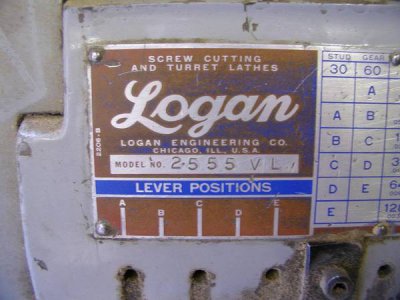
A bit of cleaning got it to here, which is where I left it while I was gone...
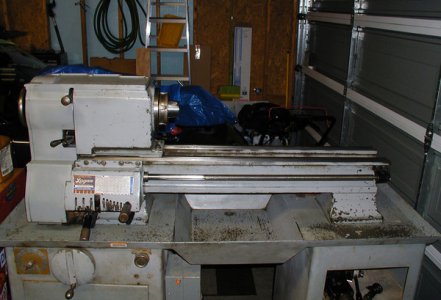
The last couple days I disassembled, cleaned, and reassembled the taper attachment...
Before:
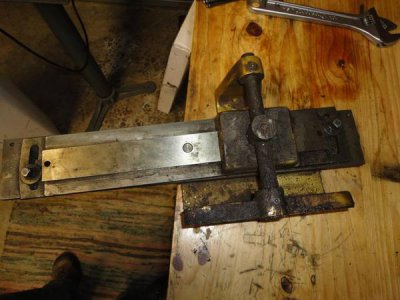
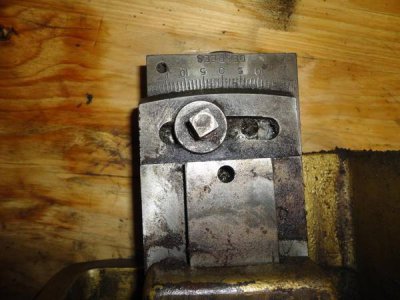
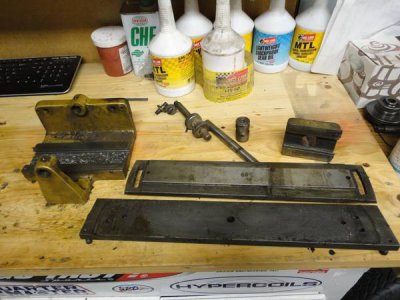
After:
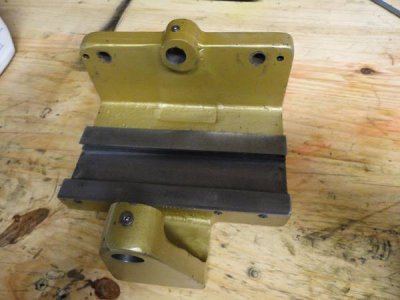
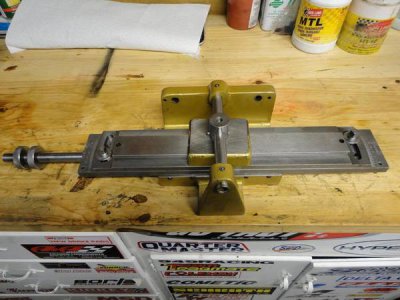
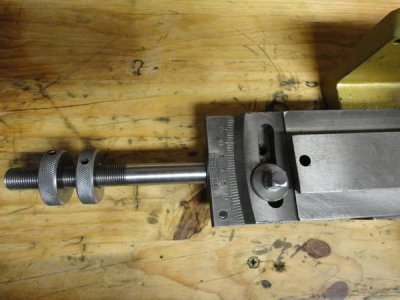
Tonight I started on the saddle/crosslide...
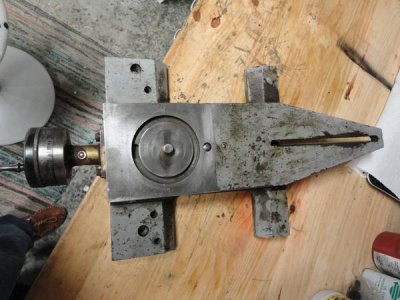
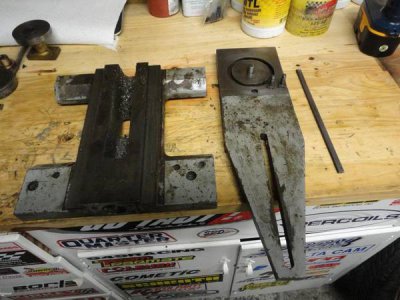
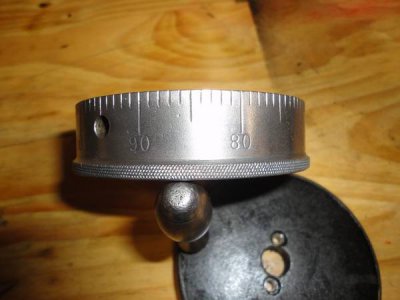
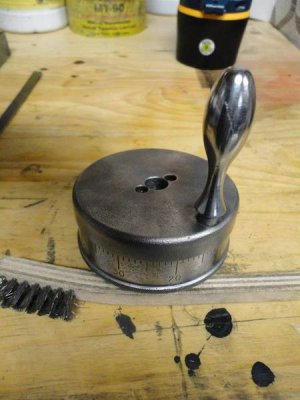
- - - Updated - - -
Oh, and the day I got back from Japan I picked this up... because I need more projects :rofl:
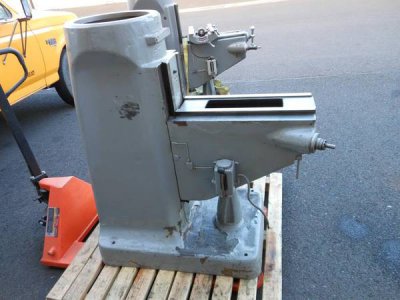
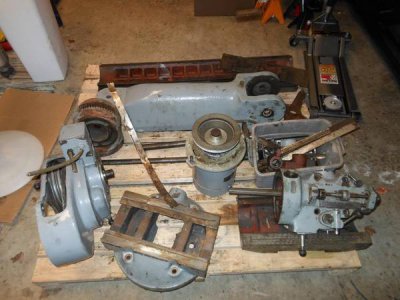
This will be another thread though...