- Joined
- Jul 14, 2017
- Messages
- 2,446
I've been looking for a good and affordable saw, right now i only have an 4" angle grinder, looked at band saws, very expensive, looked at electric hacksaws all are worn out broken and not functional, than a friend suggested build your self an beast of an chop saw, at first i thought no way i have already couple of projects but after looking i shows that ones selling most of them are home made and are 10 times the price of the parts, so aside all other projects i'll be starting a 14" Cut-Off Saw, for the base and drive i have it all figured out, but i'll like some advice for the hold down vice, i need to be able to turn so i can cut pieces at an angle, to give you all idea i've attached a picture what it will look like.
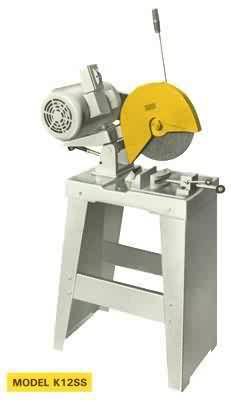
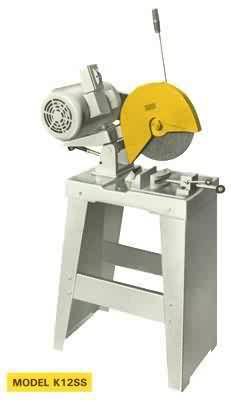