You are not going to be able to align the bed on a flimsy rolling cabinet with only a piece of plywood on top, the bed is stronger than what you have attached it to. The forces acting on the cut are not all downwards, but also towards the front of the machine, which could lift the back of the carriage. I do not see how a cut that is constant throughout the length of the cut could create a taper situation. Do an experiment and add weight to the back of the carriage to hold it down, perhaps 10 - 20 lbs weight and see if it makes a difference.
I have it mounted through 3/4 inch solid wood top sandwiched between the 11 ga, chip pan & 11 ga. metal the cabinet is constructed of. Is that not sufficient ?? I'll try to find a way to attach a 20 lb. plate to the back of the carriage, though there isn't a lot to work with back there, and see if it helps.
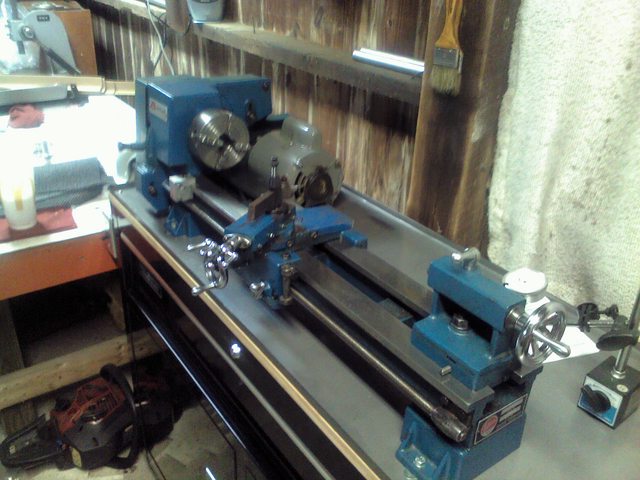