- Joined
- Jun 12, 2014
- Messages
- 4,819
I agree with Mikey, although ER chucks have a wide clamping range, the accuracy diminishes significantly as one clamps them through the range and also the holding power. I do not advise a metric set because they claim that there is a 1 mm clamping range, this is a selling point from the vendors but you will find that using a 12 or 13 mm ER collet for a 1/2" end mill is going to have significant run out. Much better off with an imperial set for the mill. On the lathe maybe a bit different if you are just doing a single op and then cutting off the piece, but the effective clamping range is much less then stated but still better than a 5C. The other significant factor is that an ER collet requires having the end mill or stock held the full length of the collet, otherwise the collet will distort and collapse on the back end as it is clamped.
You will also find that many of the higher end ER collets are for a specific size end mill, with a very small rated clamping range. So a 12mm collet is for a 12mm end mill a 1/2" collet is for 1/2" end mill. Try it any other way the you spring the collet and the run out becomes significant. When I need accuracy in my mill I use a high quality ER collet at the rated diameter.
Me recommendation would be to use an ER32 on the mill, it is more compact, and the diameter is significantly less. Typically the largest end mill one uses is 3/4". One exception would be if you have any 1" tooling that will not fit an R8. An ER32 collet is going to require less nut torque, but buying a good quality ER nut (either coated or bearing style) makes tightening significantly easier and also improves accuracy. End mills typically run in fixed shank diameters, I mostly used 1/4", 3/8", 1/2", 5/8" and 3/4" probably 99% of the time when using an ER32 chuck. You do not need a full range set for the mill, buy a few higher quality types or maybe a 1/8" increment set. Techniks are quite good at the price point, but look at some better quality ones for your mill. Decent collets are about $15 each. Get a power or bearing nut. I have both Iscar and and the higher end Shar's nickle plated R8 ER collets holder for my mill and they are all under 0.0002" TIR, almost not measurable on my 0.0001" indicator, but has been discontinued. On my mill my edge finder requires a high level of accuracy when centering, I can only do this with my ER32 R8 setup with a 12mm collet. Most R8 collets have too much runout/skew.
www.hobby-machinist.com
www.glacern.com
Lathe is a different kettle of fish. Unless you have a small lathe, most people use an ER40 collet system, Shar's sells a set-true style ER chuck (32 or 40) that is quite popular. On a larger lathe (12" or greater) I would go with an ER40. As mentioned ER collets work for stock that passes through the full length of the collet, and for high accuracy work, I would try to use them in a reduced clamping range. They do work well for odd size diameter work, so rough stock that is a bit oversized , threaded stock or knurled. On the lathe I have a 1/32 ER40 imperial collet set which has a bit smaller clamping range between collets. I use a less expensive set for my lathe, but they are still decent quality. I also have a few Shar's ER40 collets that are decent and were in the $7 a piece range.
You will also find that many of the higher end ER collets are for a specific size end mill, with a very small rated clamping range. So a 12mm collet is for a 12mm end mill a 1/2" collet is for 1/2" end mill. Try it any other way the you spring the collet and the run out becomes significant. When I need accuracy in my mill I use a high quality ER collet at the rated diameter.
Me recommendation would be to use an ER32 on the mill, it is more compact, and the diameter is significantly less. Typically the largest end mill one uses is 3/4". One exception would be if you have any 1" tooling that will not fit an R8. An ER32 collet is going to require less nut torque, but buying a good quality ER nut (either coated or bearing style) makes tightening significantly easier and also improves accuracy. End mills typically run in fixed shank diameters, I mostly used 1/4", 3/8", 1/2", 5/8" and 3/4" probably 99% of the time when using an ER32 chuck. You do not need a full range set for the mill, buy a few higher quality types or maybe a 1/8" increment set. Techniks are quite good at the price point, but look at some better quality ones for your mill. Decent collets are about $15 each. Get a power or bearing nut. I have both Iscar and and the higher end Shar's nickle plated R8 ER collets holder for my mill and they are all under 0.0002" TIR, almost not measurable on my 0.0001" indicator, but has been discontinued. On my mill my edge finder requires a high level of accuracy when centering, I can only do this with my ER32 R8 setup with a 12mm collet. Most R8 collets have too much runout/skew.
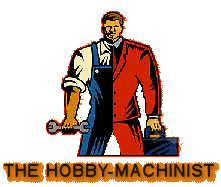
buying er32 collets
My Beall Collet chuck arrived and what a work of art it is. now to populate the collet rack. er32 collets can cost from a little to a lot. obviously "a lot" means different things to different people, but it is not my first choice. So the question is, If one buys moderately priced collets...
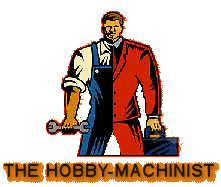
Glacern Machine Tools - ER Collet Chucks
Glacern Machine Tools manufacturers CNC Machine Vises, Precision Tool Holders, and Indexable Milling Cutters for vertical and horizontal cnc milling machines.
Lathe is a different kettle of fish. Unless you have a small lathe, most people use an ER40 collet system, Shar's sells a set-true style ER chuck (32 or 40) that is quite popular. On a larger lathe (12" or greater) I would go with an ER40. As mentioned ER collets work for stock that passes through the full length of the collet, and for high accuracy work, I would try to use them in a reduced clamping range. They do work well for odd size diameter work, so rough stock that is a bit oversized , threaded stock or knurled. On the lathe I have a 1/32 ER40 imperial collet set which has a bit smaller clamping range between collets. I use a less expensive set for my lathe, but they are still decent quality. I also have a few Shar's ER40 collets that are decent and were in the $7 a piece range.
Last edited: