I restored a Delta DP220 drill press and made my own speed reduction assembly. Offset the pulley a bit from center to allow belt tensioning by the column insert rotating as the motor is tensioned. Herad good things about the link belts so thought I'd give one a try. Picked up a harbor freight link belt along with an aluminium 4-groove pulley off amazon and got the column insert turned on the lathe, drilled & tapped for an axle bolt to mount the pulley with a broze sleeve bearing. Set up look good and function fine until under load...First time use yesterday drilling 0.250 in. hole in some angle steel for another project and the bit would bind and belt would slip or belt would slip & bit would bind in work as a result. Either way the belt is slipping with some frequency. Anyone else run into this ?? the alum. pulley is fairly polished while the spindle pulley & motor pulley is painted cast metal from what I can tell. Don't seem to have much issue with the same belt slipping between the motor drive pulley & alum. speed reduction pulley. The slipping seems to occur between the spindle pulley & aluminum speed reducing pulley.....
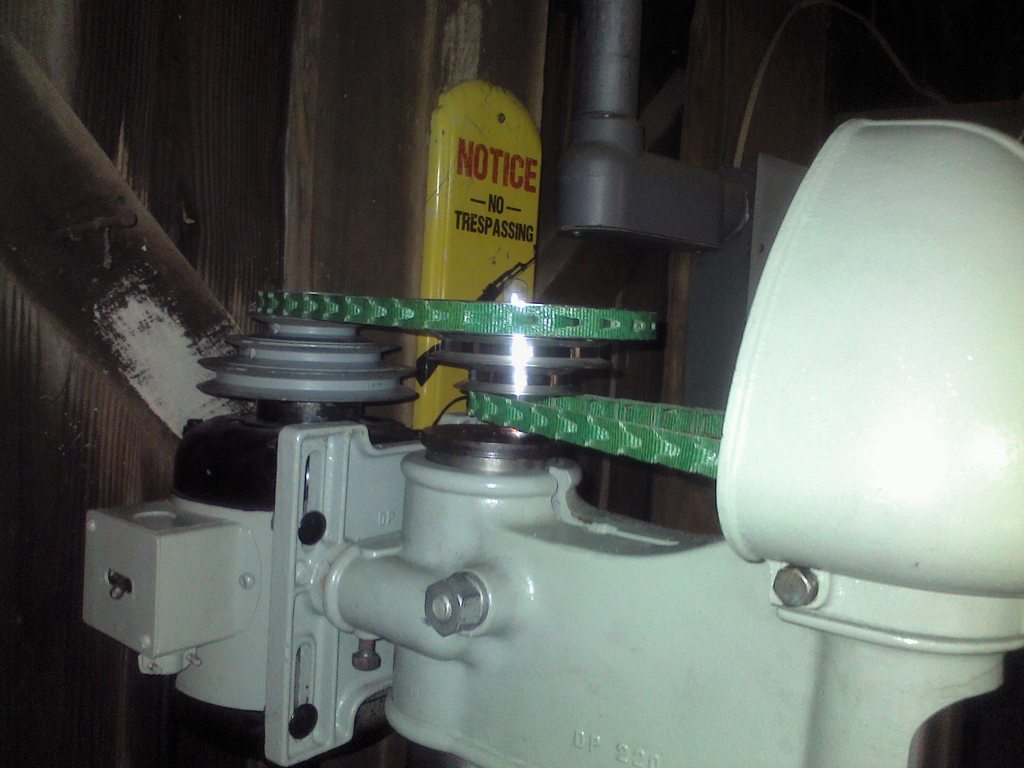