Finally got the plate roller on castors. This has been on my "to do list" for some time, in fact, I design the brackets back when I built Mark's (mksj) rolling mill base and built all eight at the same time.
3/8" CR flat bar.
These have been on standby for several months.
First order of business was to move the roller out to remove the four angle clips. I don't like to grind too much in the shop and the day was beautiful with a high of 88 degrees.
A 4.5" cutoff wheel was used to grind off the factory welds keeping the parent metal intact.
All four clips removed and the frame cleaned up.
Brought the machine back into the shop and began laying out the location. I kept the machine at a comfortable height for this. Wood cribbing was used as safety blocks since I was working in the danger zone.
Used tape as a guide for stripping paint. I used a 3M roloc green stripper disc.
All four caster brackets tacked and ready for verification prior to burning in.
A level was used to verify the new brackets to the main frame.
I used a straight section of tubing spanning the two brackets.
And checked the main frame for same results.
Now its time to burn in the brackets.
The 350P was used at 425 IPM in pulse mode. All vertical welds up hill. A wet rag was used near any wiring that passed through the main frame (to the right of weldment). All four weldment are directly inline with cross members on the main frame preventing distortion and preserving rigidness.
Installed the casters and lowered the machine to the floor for a test drive

.
This is the business side of the machine.
Checked with a level and they where dead on x 2.
Close up of upper frame. spot on!
Good on side too.
Tomorrow, I need to notch the end cover (x 2) to fit over the new caster brackets. I laid them out prior to removing the cover. I will probably go 3/8" beyond the lines to ensure clearance (cut once).
Notice the Heat affected zone (HAZ) on the backside of the CR flat bar.
The color represents between 840-1,000 degrees resulting in good fusion. Floor clearance came to 1.25" as planned for a working hight of 32"
The final measurement hight (plate feed hight) came to 32" from floor. This matches the hight of a table used to roll full sheets to the plate roller.
The castors all swivel and all have locks. This should allow reconfiguration of work space for larger jobs that come in. I have most of the machines/tables on castors with the exception of mills and lathe for obvious reasons. The machine requires moderate effort to roll around.
I will paint the brackets bright orange to match the rest of the machines on castors as well as touch up the hammer tone blue/green paint.
A good day all in all.
Thanks for looking.
Turn and burn!
Paco
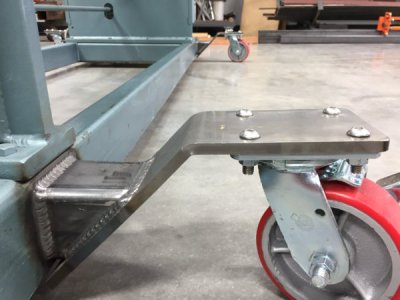