- Joined
- Jul 11, 2014
- Messages
- 496
It looks like quite a nice little dividing head how many teeth on the worm wheel. You say you had problems, but what were they, and how did you solve them. Maybe we can all learn here.
Bob.
First was the spindle. I cut the worm threads too deep on the original spindle/shaft. Broke in two when I was handling it so had to machine a new spindle. The centerbore on the new spindle has a thicker wall. Then the lock for the spindle did not work when I put the wormshaft in, they were too close, so I had to move the locking lever to the other side of the dividing head and flip the locking piece. I had to "lap" the shaft and lock mechanism to get the fit right. That's not so much a problem as its a normal process of machining the project. Now I have the degree 'defrugaltie' to resolve. Mostly minor when you take them alone but revealing about my methods when taken together. But "Hey!" I'm doing what I like to do. The frustration is minor compared to that.
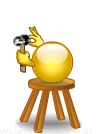
I do actually sketch out most of my projects. That avoids some of the type of 'defrugalties' I ran into on this one. But sometime I think I don't need to do that and find out I do. So somewhere in the near future I will make a sketch/CAD drawing, to try and catch all the possibles that may still come up as it progresses.
Whyemier, revealing all his deep dark secrets and inadequacies.