- Joined
- Jun 17, 2012
- Messages
- 2,220
I made this press brake to fit on my HF 20 ton shop press. I thought I'd share it with you guys over here. I've seen several different variations of these for sale online at places like Northern Tool and on ebay. Some of them were pre-cut weld yourself kits others were already made. I had the steel laying around my shop so I decided to build one.
So here's what it looks like complete:
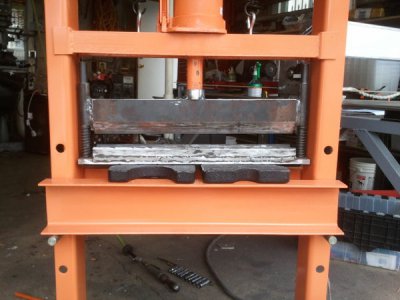
These are the parts mostly precut and ready for welding. The spring came from a storm door air cylinder that I had laying around. I cut it open to retrieve the spring.
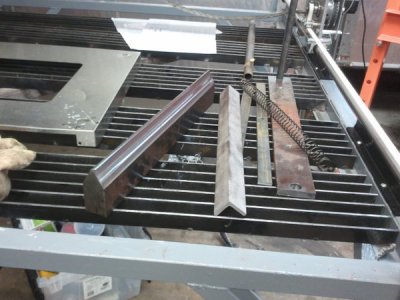
This is my Bridgeport hogging out the 60 degree wedge shape on the 1 1/2" x 3 1/2" piece of steel for the punch side of the brake. Some of the iterations of this brake I've seen only have an angle iron welded to the top punch to achieve the wedge shape or a 90 degree wedge shape but the result is that achieving a 90 degree bend is nearly impossible because of the flex-back of the material. With a 60 degree wedge on top a 90 degree + bend is easily achievable.
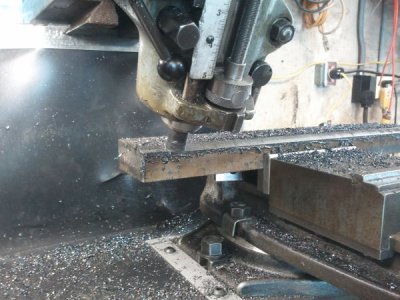
Heres a picture of how it's put together from the side.
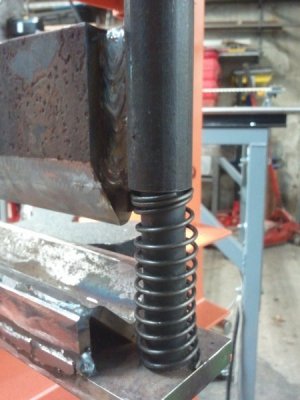
It can bend up to 110 degrees. which is the reason why I put a 60 degree angle on the wedge to achieve the beyond 90 capability.
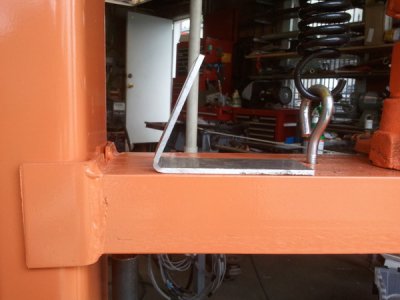
I did most of this on a Saturday afternoon and finished welding it up the next Sunday morning. The longest part was hogging the wedge shape out on the Bridgeport at .040 bites at a time with a 1" carbide indexed end mill. I tried it with a larger HSS end mill and the result was way too slow for my taste. Gotta get me some of those Large indexable facing and hogging shell mills.
Have Fun
Marcel





So here's what it looks like complete:
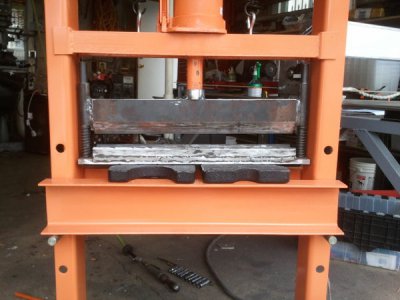
These are the parts mostly precut and ready for welding. The spring came from a storm door air cylinder that I had laying around. I cut it open to retrieve the spring.
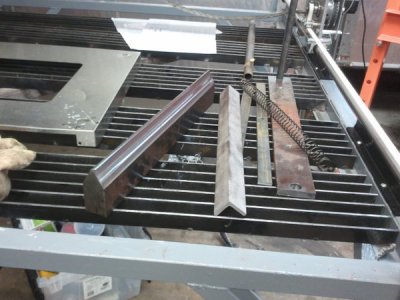
This is my Bridgeport hogging out the 60 degree wedge shape on the 1 1/2" x 3 1/2" piece of steel for the punch side of the brake. Some of the iterations of this brake I've seen only have an angle iron welded to the top punch to achieve the wedge shape or a 90 degree wedge shape but the result is that achieving a 90 degree bend is nearly impossible because of the flex-back of the material. With a 60 degree wedge on top a 90 degree + bend is easily achievable.
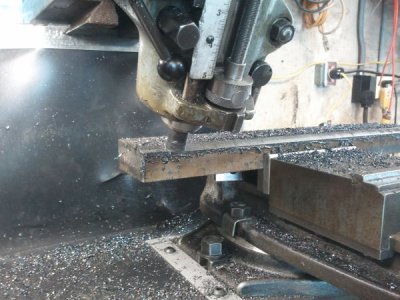
Heres a picture of how it's put together from the side.
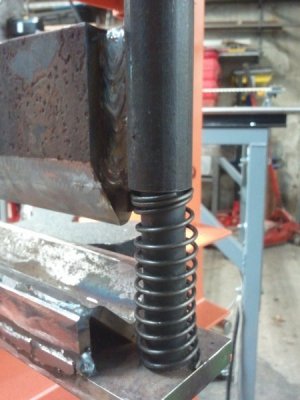
It can bend up to 110 degrees. which is the reason why I put a 60 degree angle on the wedge to achieve the beyond 90 capability.
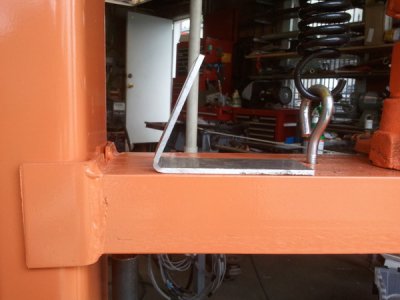
I did most of this on a Saturday afternoon and finished welding it up the next Sunday morning. The longest part was hogging the wedge shape out on the Bridgeport at .040 bites at a time with a 1" carbide indexed end mill. I tried it with a larger HSS end mill and the result was way too slow for my taste. Gotta get me some of those Large indexable facing and hogging shell mills.
Have Fun
Marcel




