- Joined
- Feb 2, 2013
- Messages
- 3,627
it will do but you can do it for a lot less money
there are many ways of doing it, but it doesn't get much cheaper than this...
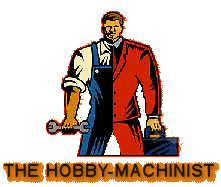
Rpc simple design unbalanced
Rpc simple design Here's a simple plan for an unbalanced 220/240 v single to 3 phase converter. this design will start ANY 3 phase motor of ANY horsepower with a change of start capacitors! keep in mind,the contactor coil is 220v in this design, adjust coil voltage for high voltage use(480v)...
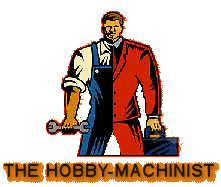
Last edited: