I bought a die holder for my lathe and it didn't seem to hold the die flat enough for my liking. With the admittedly cheap die, it rocked. It gave me no confidence that the die would start correctly. Perhaps I don't understand how it should work, but I'd think one would want to have the die supported uniformly on the back face. I am definitely considering making my own. It seems like it would make a nice lathe project
I have the same issue with some dies in my shop made holder.
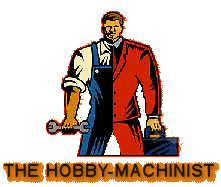
Tailstock Die holder
Made from stainless steel. A lot of lathe work, and somenmill work. single point threading, mt3 taper turning. first time turning between centers, used a diy lathe dog made from 1/2 steel plate and 3/8 bolts.. Not actually tried it yet .. It was fun to make, learned alot.
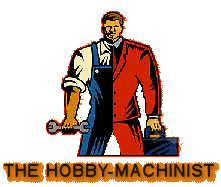
Just shim behind the die to stop the rocking. A fiber washer works great.