- Joined
- Sep 1, 2018
- Messages
- 74
Hi all,
I'm about to cut my first set of threads for a project I'm working on. 1/2-20 both right and left hand. I'll be going by the Machinerys Handbook to learn. I know the basics, compound at 29 1/2 deg. 60 deg tool, major and minor diameters, cutting fluid, machine feed rates(20tpi), not to sure about spindle speed (I think it's just cold rolled 5/8 rod so 4 x 100 / dia. ?) but that's about it. I will be doing a couple test pieces to make sure I get this right. Also, I think I'll be grinding my own tool for the first time instead of using one my dad gave me... Any advice ? The pic is of a couple test passes just to get use to the lathes controls... No ryme, reason or size to the threads in the pic.....Any advice ?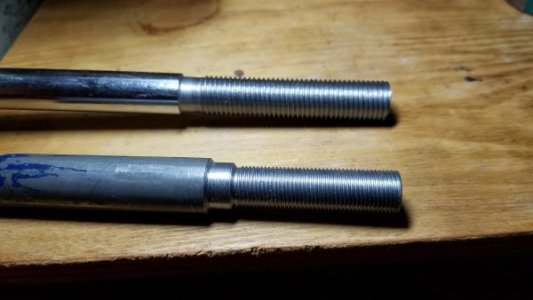
I'm about to cut my first set of threads for a project I'm working on. 1/2-20 both right and left hand. I'll be going by the Machinerys Handbook to learn. I know the basics, compound at 29 1/2 deg. 60 deg tool, major and minor diameters, cutting fluid, machine feed rates(20tpi), not to sure about spindle speed (I think it's just cold rolled 5/8 rod so 4 x 100 / dia. ?) but that's about it. I will be doing a couple test pieces to make sure I get this right. Also, I think I'll be grinding my own tool for the first time instead of using one my dad gave me... Any advice ? The pic is of a couple test passes just to get use to the lathes controls... No ryme, reason or size to the threads in the pic.....Any advice ?
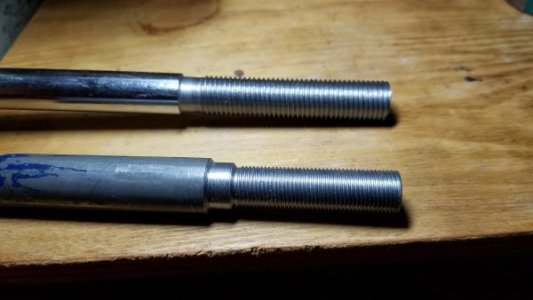