- Joined
- Feb 28, 2017
- Messages
- 23
Hi folks 
I thought it was about time I stop being a lurker and actually post something.
About two years ago, I started putting my home machine shop together, I had little knowlege back then and no formal training but heaps of enthusiasm and a thirst to learn.
A few months after getting my Grayson lathe, I went and bought a Dore Westbury Mk1 milling machine. Unfortunately it was pretty beat up so I concentrated on getting good with the lathe until I'd learned what I needed to fix the mill.
Having then got it up and running some time after, the knowlege I had gained all that time made it plainly obvious I was going to have to it properly and so a few months ago, I tore it down and got stuck in.
Here she is just before teardown:
Main casting and their sundries after cleanup:
Castings after paint removal:
I then tackled a persistent problem with the lower pulley section. Initially I thought the bore was out of true as it had a terrible kilter which was casing vibration and had wrecked the original bushings.
However, it transpired that the mating surface on the bottom, apon which the whole pulley rests and spins, was out of true, not the bore and a quick skim with the boring bar finally vanquished the issue once and for all:
I then got creative on the support column casting with a brass wheel and blow torch and used a little known technique to plate the two bands as I decided on a black and brass colour scheme throughout and I felt that brassing the bands would enhance the easthetics.
However, in most cases it is not good practice to heat cast iron unevenly as it leads to warping or snapping as it cools. The casting I treated has a long split down the back of it, allowing for the iron to flex without hindrance but in doing so, it could have still warped on me but I took an educated risk that the thickness of the banding would help to retain its shape:
Here are the main castings after painting, I used a hard wearing skip paint which is resistant to anything I will likely throw at it and gave the parts two good coatings so it should hold up for quite awhile:
After painting the castings, I set about turning a ruck of brass washers for all the various bolts about the machine to keep with the theme:
I then cobbled this stand together and used the old chuck that came with my lathe to hold all the bolts for blacking. For that I used linseed oil and an old rag and repeatedly alternated between heat and oil till each bolt head turned a deep black:
Using the same stand, I then brass plated parts of the various levers, making sure to account for the alternating colours:
Once the levers had been plated, I made a start on painting some of the other parts:
Once dry, I couldn't help myself reassembling it to see how it looked, I'll need to take it down again for final polishing and assembly but I think she is going to look mighty perdy when complete:
That's as far as I've got with it so far, I had to take a short break to make a workshop press so o can install a new set of bearing I got for the quill but if anyone is interested in seeing the process in more detail, I've been documenting it and uploading the footage to my youtube channel, this link will take you to the playlist so far:
https://www.youtube.com/playlist?list=PLGgeJ0jNxfJJOypmxmrNIVVl88D30waze
I'm hoping to get the press finished by the end of next week so I can get on with the restoration and will post again as soon as I have more.
Until then, stay happy, stay safe and keep those chips flyin'
I thought it was about time I stop being a lurker and actually post something.
About two years ago, I started putting my home machine shop together, I had little knowlege back then and no formal training but heaps of enthusiasm and a thirst to learn.
A few months after getting my Grayson lathe, I went and bought a Dore Westbury Mk1 milling machine. Unfortunately it was pretty beat up so I concentrated on getting good with the lathe until I'd learned what I needed to fix the mill.
Having then got it up and running some time after, the knowlege I had gained all that time made it plainly obvious I was going to have to it properly and so a few months ago, I tore it down and got stuck in.
Here she is just before teardown:

Main casting and their sundries after cleanup:

Castings after paint removal:

I then tackled a persistent problem with the lower pulley section. Initially I thought the bore was out of true as it had a terrible kilter which was casing vibration and had wrecked the original bushings.
However, it transpired that the mating surface on the bottom, apon which the whole pulley rests and spins, was out of true, not the bore and a quick skim with the boring bar finally vanquished the issue once and for all:

I then got creative on the support column casting with a brass wheel and blow torch and used a little known technique to plate the two bands as I decided on a black and brass colour scheme throughout and I felt that brassing the bands would enhance the easthetics.
However, in most cases it is not good practice to heat cast iron unevenly as it leads to warping or snapping as it cools. The casting I treated has a long split down the back of it, allowing for the iron to flex without hindrance but in doing so, it could have still warped on me but I took an educated risk that the thickness of the banding would help to retain its shape:

Here are the main castings after painting, I used a hard wearing skip paint which is resistant to anything I will likely throw at it and gave the parts two good coatings so it should hold up for quite awhile:

After painting the castings, I set about turning a ruck of brass washers for all the various bolts about the machine to keep with the theme:


I then cobbled this stand together and used the old chuck that came with my lathe to hold all the bolts for blacking. For that I used linseed oil and an old rag and repeatedly alternated between heat and oil till each bolt head turned a deep black:



Using the same stand, I then brass plated parts of the various levers, making sure to account for the alternating colours:

Once the levers had been plated, I made a start on painting some of the other parts:


Once dry, I couldn't help myself reassembling it to see how it looked, I'll need to take it down again for final polishing and assembly but I think she is going to look mighty perdy when complete:

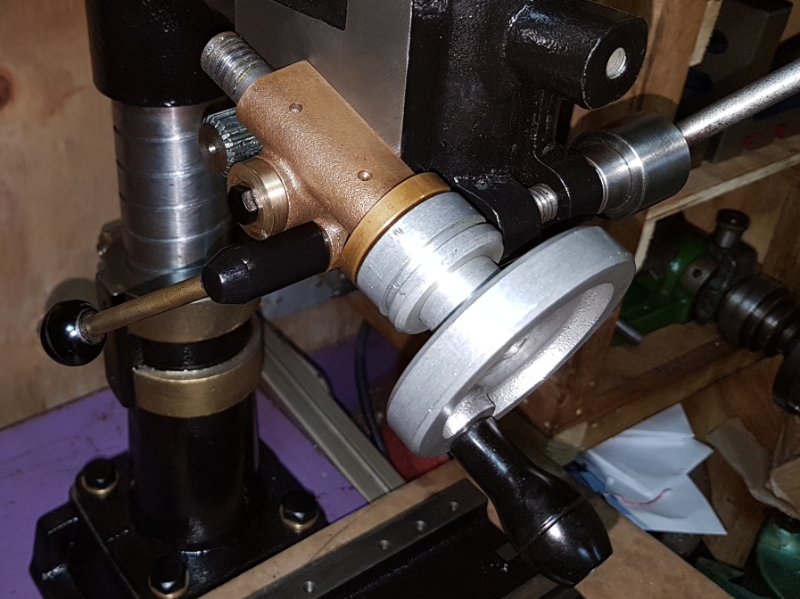




That's as far as I've got with it so far, I had to take a short break to make a workshop press so o can install a new set of bearing I got for the quill but if anyone is interested in seeing the process in more detail, I've been documenting it and uploading the footage to my youtube channel, this link will take you to the playlist so far:
https://www.youtube.com/playlist?list=PLGgeJ0jNxfJJOypmxmrNIVVl88D30waze
I'm hoping to get the press finished by the end of next week so I can get on with the restoration and will post again as soon as I have more.
Until then, stay happy, stay safe and keep those chips flyin'