Not a lot of activity on this forum, but figured its the appropriate place to post this.
Having a go at my first knife, and some constructive criticism from experienced knife makers would be helpful. I bought the blank on a whim, while placing an order with SWAG Offroad. I had just purchased a heat treat oven not long ago( and built a 2"x72" belt grinder ), so when I saw this item figured hell for 20 bucks, why not give it a try.
www.swagoffroad.com
I wasn't wild about the bottle opener sticking out, so that was the first thing to go. Also put a little more drop in the point. The blanks are 3/16"thick, which seemed kinda clunky for it's size, so they spent a few sessions on the surface grinder, until it looked and felt right, which ended up being .160". Wasn't sure of the state of the 1095 steel, and there was no info with it, so I normalized and annealed it before starting to shape the blade, and drill holes.
Just did a straight bevel grind on the blade, keeping it simple. Right off the bat started the plunge line too far back, so that's kinda permanently screwed up....oh well. Swiss cheesed the handle a bit to lighten it up, and balance it better. Rough ground the blade bevel, and then quenched and tempered. It hardened really well, somewhere between 60-65 RC. I think the temper was a bit too warm, as it was on the darker side of straw, and the hardess files show it between 55-60 RC. Finished grinding the bevel, and its at the 400 grit belt stage, as shown in the photo. Also dusted off the flats on the surface grinder.
Trying to decide to what level of finish to take the metal to. As ground, hand sand smooth, high polish, tumbled, etc......Not sure yet. Handle scales will be basic black canvas Micarta. Waiting on some epoxy to arrive for them. It'll likely sit idle for a few days, until the glue gets here, and then I'll post up the finished knife.

Having a go at my first knife, and some constructive criticism from experienced knife makers would be helpful. I bought the blank on a whim, while placing an order with SWAG Offroad. I had just purchased a heat treat oven not long ago( and built a 2"x72" belt grinder ), so when I saw this item figured hell for 20 bucks, why not give it a try.
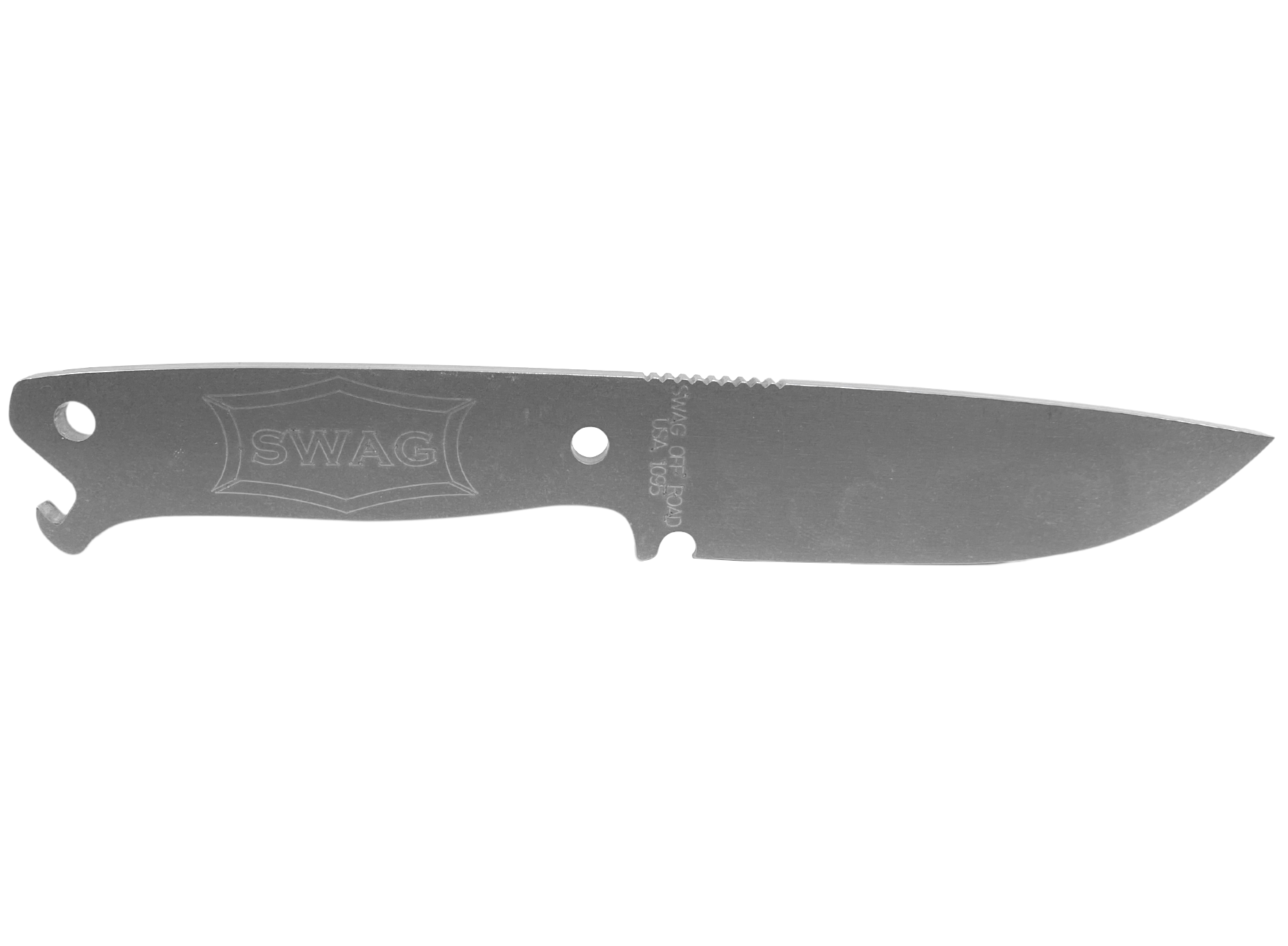
SWAG 1095 Bottle Opener/Knife Blank
SWAG 1095 Bottle Opener/Knife Blank Whether you want to create a knife or pop a bottle top, the SWAG Knife Blank has you covered. Cut out of 1095 High Carbon Forging Steel, this blank can be used to make a useful knife that will actually hold an edge. If you don't have a belt grinder, its also a...

I wasn't wild about the bottle opener sticking out, so that was the first thing to go. Also put a little more drop in the point. The blanks are 3/16"thick, which seemed kinda clunky for it's size, so they spent a few sessions on the surface grinder, until it looked and felt right, which ended up being .160". Wasn't sure of the state of the 1095 steel, and there was no info with it, so I normalized and annealed it before starting to shape the blade, and drill holes.
Just did a straight bevel grind on the blade, keeping it simple. Right off the bat started the plunge line too far back, so that's kinda permanently screwed up....oh well. Swiss cheesed the handle a bit to lighten it up, and balance it better. Rough ground the blade bevel, and then quenched and tempered. It hardened really well, somewhere between 60-65 RC. I think the temper was a bit too warm, as it was on the darker side of straw, and the hardess files show it between 55-60 RC. Finished grinding the bevel, and its at the 400 grit belt stage, as shown in the photo. Also dusted off the flats on the surface grinder.
Trying to decide to what level of finish to take the metal to. As ground, hand sand smooth, high polish, tumbled, etc......Not sure yet. Handle scales will be basic black canvas Micarta. Waiting on some epoxy to arrive for them. It'll likely sit idle for a few days, until the glue gets here, and then I'll post up the finished knife.
