- Joined
- Jan 20, 2021
- Messages
- 296
Started on my first lathe project last night. Not sure exactly what to call it... I’m making a lever handled nut for the top of the quick change tool post. It replaces the nut on top with a lever similar to the one already there for the wedge.
This is an example of what I’m making.
I cut a chunk of material from one of the rusty bars I bought from the scrap yard and got to making it smaller. Finish seems alright thus far.
I think the next step will be to bore and tap the thread that goes in place of the existing nut. Then part it off a bit long and flip it around to do a taper and clean up the top. I need some material for the handle yet. I don’t have a ball turning setup so I’m thinking I’ll make a more rectangular knob. So far so good. It’s only a 3” or so part and I have a few feet of material to turn into mistakes before I would need more material
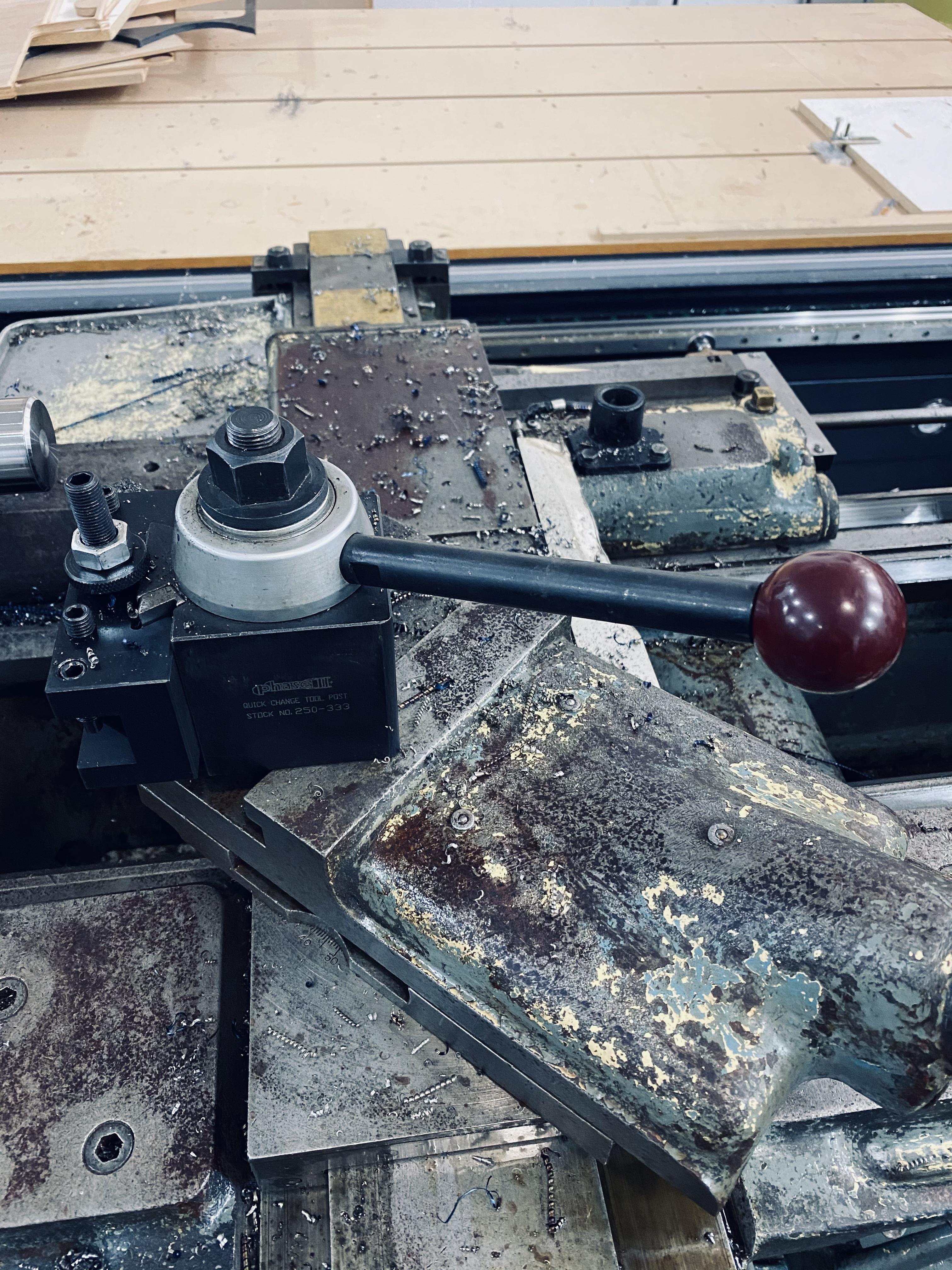
This is an example of what I’m making.

I cut a chunk of material from one of the rusty bars I bought from the scrap yard and got to making it smaller. Finish seems alright thus far.
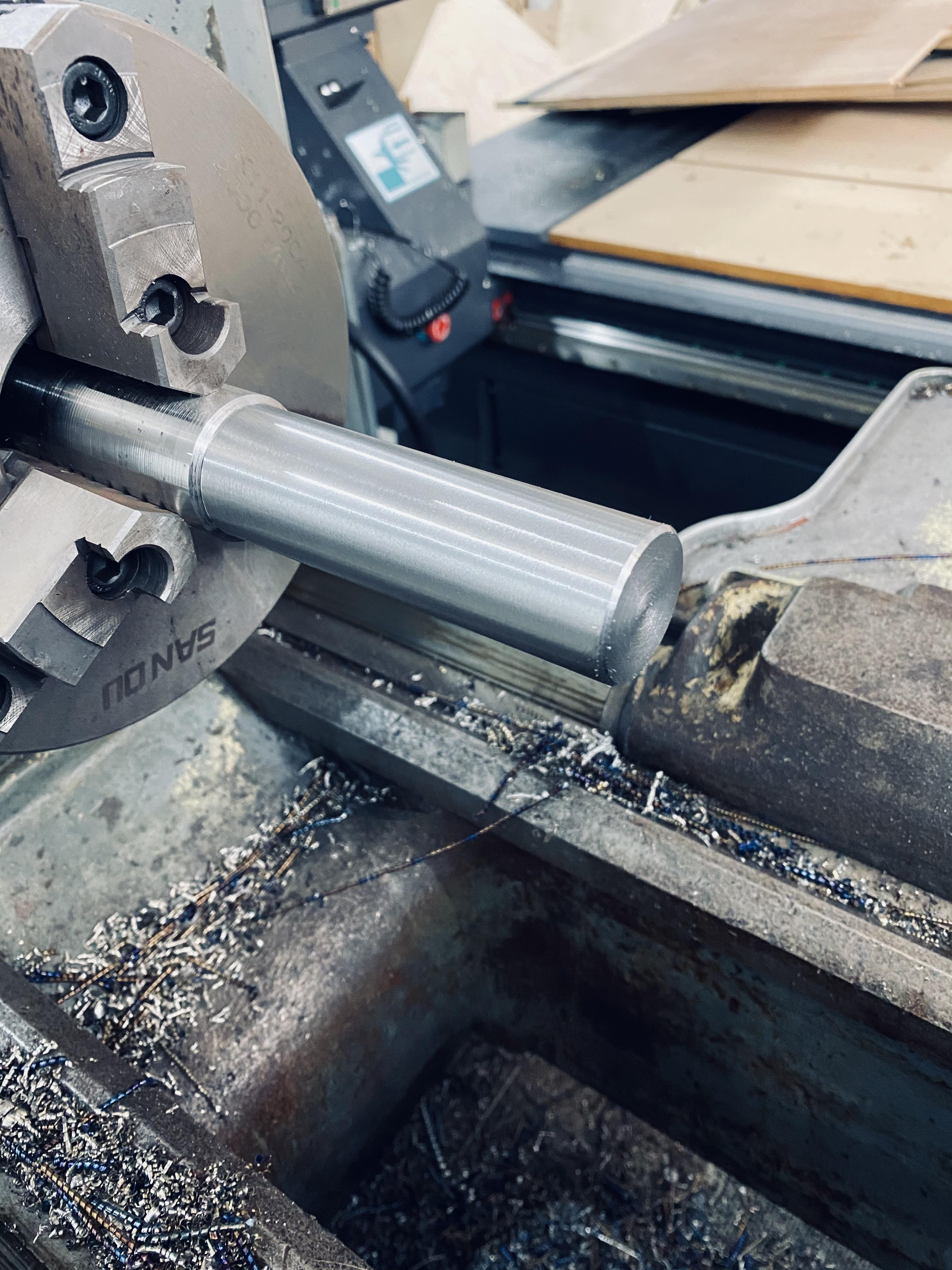
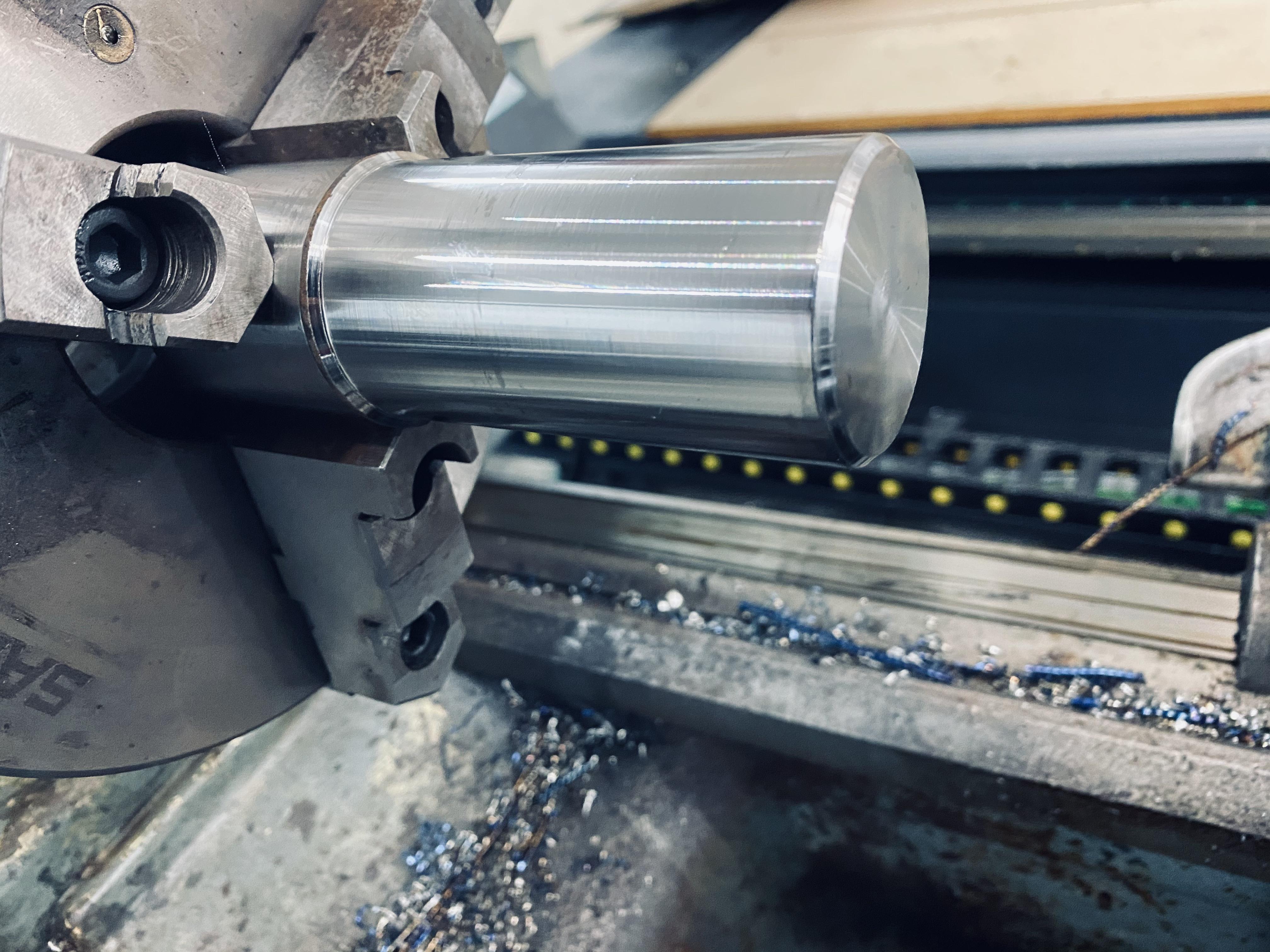
I think the next step will be to bore and tap the thread that goes in place of the existing nut. Then part it off a bit long and flip it around to do a taper and clean up the top. I need some material for the handle yet. I don’t have a ball turning setup so I’m thinking I’ll make a more rectangular knob. So far so good. It’s only a 3” or so part and I have a few feet of material to turn into mistakes before I would need more material