- Joined
- Mar 2, 2021
- Messages
- 84
Hello all!
I thought I would share the experience of scraping my first straightedge. I am just getting going on it in earnest so I’ll share progress posts here as I go.
Over the past few months. I have been watching many YouTube videos, purchased and watched Richard King’s scraping videos, reading books like Machine Tool Reconditioning and collecting hand scraping supplies.
I bought a few different straightedge castings and decided to start with Denis Foster’s 8” Featherweight casting. I am glad I did because it’s both a beautiful casting and also because Denis is awesome and has been a great source of advice and recommendations about machining the casting.
Here is what the casting supplied by Denis looked like:
Denis offers them machined, but I opted for a raw casting to maximize the learning. Despite being unmachined, Denis does a nice job cleaning up the gate and any flashing and egregious uneven high spots.
After explaining the machines in my shop to Denis (a PM-1054 mill with a 6” Kurt vise), Denis suggested I could mount the vise parallel to the bed, remove the vise jaw plates, and clamp up the casting with some thin pieces of plywood for both friction and to take up some of the irregularity of the sides of the casting.
I started by machining the back of the casting using a cheap 3” shell mill with carbide inserts that I had lying around.
After machining the back, I rotated the casting and indicated it in with light taps using the back as a reference to machine the sole of the straightedge.
After checking squareness on the surface plate, and finding it was pretty darn square, rather than indicate and tap in the top, I just clamped it in the Kurt using the back and sole as a reference against the fixed jaw and throat of the vise. I used the thin plywood to take up the irregularity of the unmachined thin edge of the 45 degree face and cut the top flat.
In that same setup, I side milled the ends for aesthetics.
Finally, I used a small high quality rafter square to set up the 45 degree face
Yes, that is far from a precision setup, but in discussion with Denis he suggested the 45 degree is not intended to be a precision angle, to not give myself fits trying to make that perfect and it greatly simplified an already fussy setup. I did use an indicator to double check squareness to the sole and back faces.
Checking my work on the surface plate with my steel Starrett master square, and despite my nascent machining skills, the cuts all came out surprisingly parallel and square! Even the 45 degree angle ended up as dead nuts as I could measure with my Mitutoyo precision bevel protractor. Score one for the rafter square!
Next up: my first attempt at scraping!
I thought I would share the experience of scraping my first straightedge. I am just getting going on it in earnest so I’ll share progress posts here as I go.
Over the past few months. I have been watching many YouTube videos, purchased and watched Richard King’s scraping videos, reading books like Machine Tool Reconditioning and collecting hand scraping supplies.
I bought a few different straightedge castings and decided to start with Denis Foster’s 8” Featherweight casting. I am glad I did because it’s both a beautiful casting and also because Denis is awesome and has been a great source of advice and recommendations about machining the casting.
Here is what the casting supplied by Denis looked like:
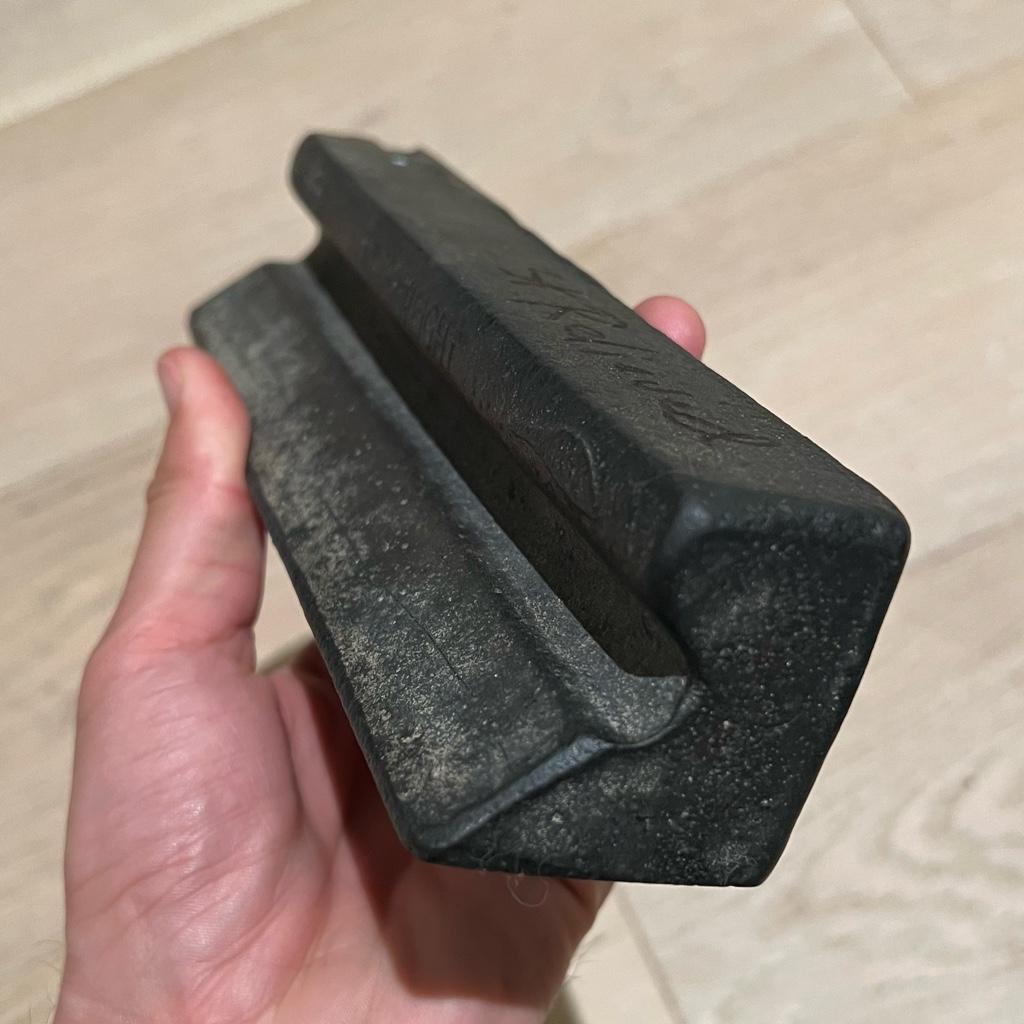
Denis offers them machined, but I opted for a raw casting to maximize the learning. Despite being unmachined, Denis does a nice job cleaning up the gate and any flashing and egregious uneven high spots.
After explaining the machines in my shop to Denis (a PM-1054 mill with a 6” Kurt vise), Denis suggested I could mount the vise parallel to the bed, remove the vise jaw plates, and clamp up the casting with some thin pieces of plywood for both friction and to take up some of the irregularity of the sides of the casting.
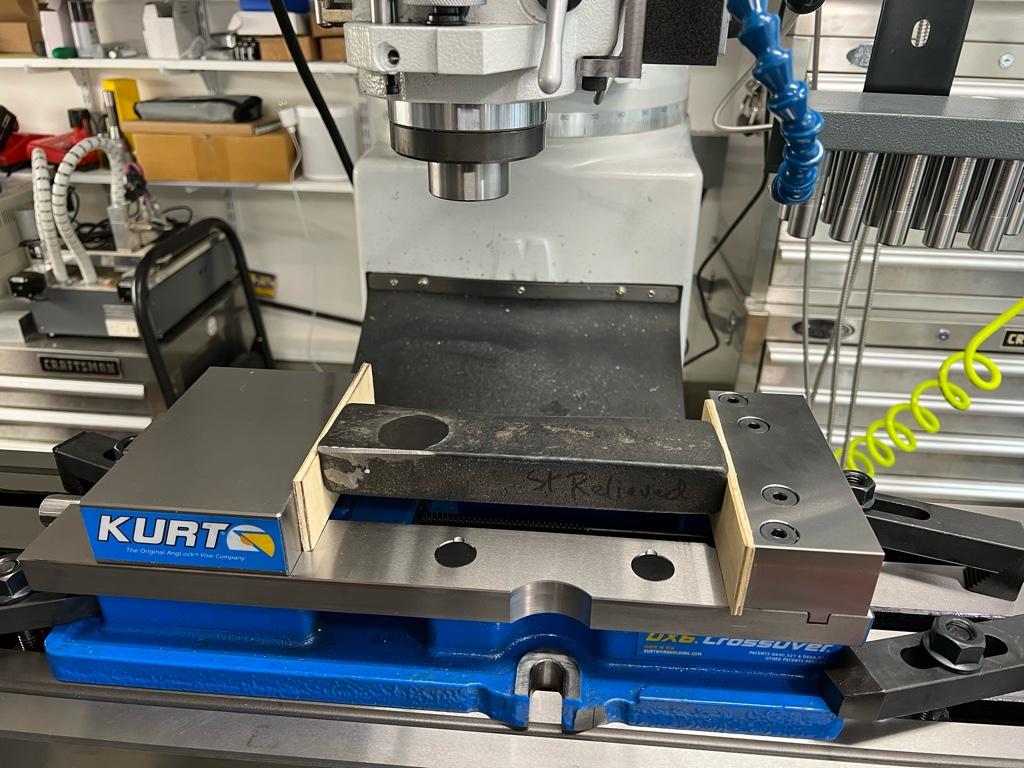
I started by machining the back of the casting using a cheap 3” shell mill with carbide inserts that I had lying around.
After machining the back, I rotated the casting and indicated it in with light taps using the back as a reference to machine the sole of the straightedge.
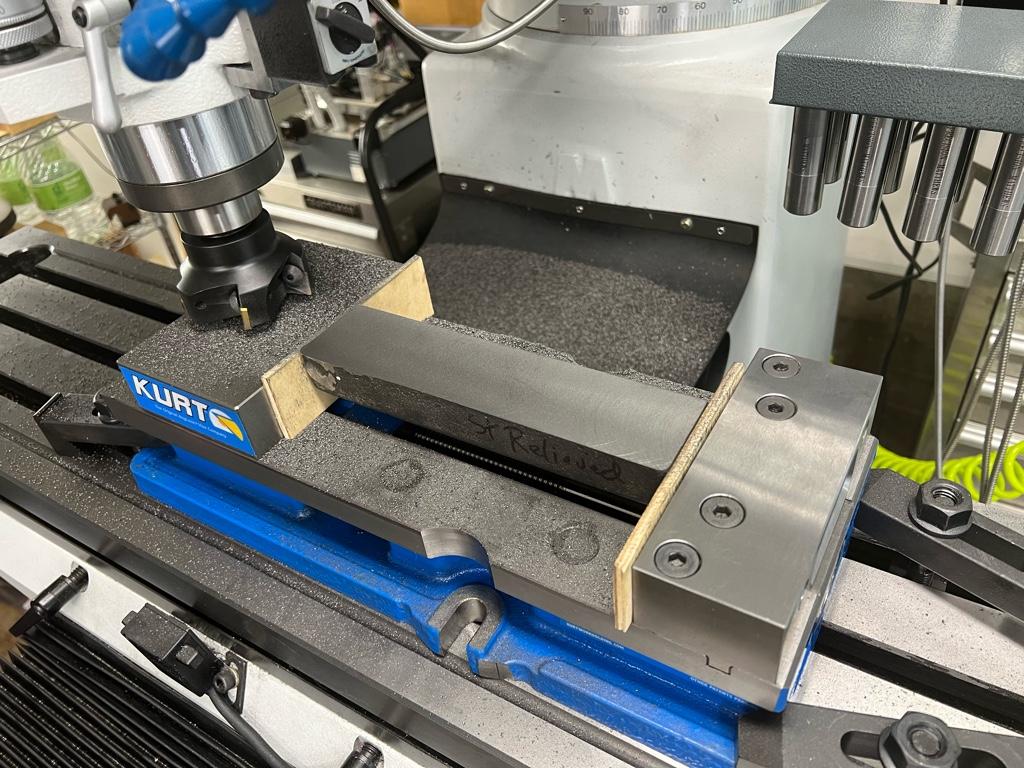
After checking squareness on the surface plate, and finding it was pretty darn square, rather than indicate and tap in the top, I just clamped it in the Kurt using the back and sole as a reference against the fixed jaw and throat of the vise. I used the thin plywood to take up the irregularity of the unmachined thin edge of the 45 degree face and cut the top flat.
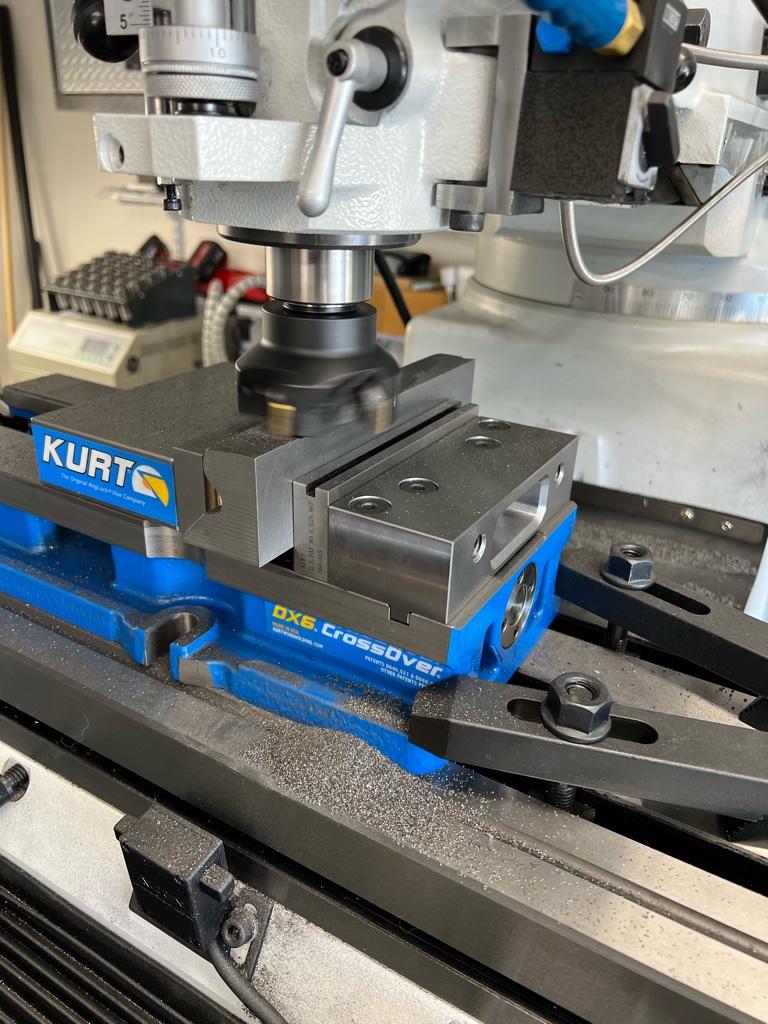
In that same setup, I side milled the ends for aesthetics.
Finally, I used a small high quality rafter square to set up the 45 degree face

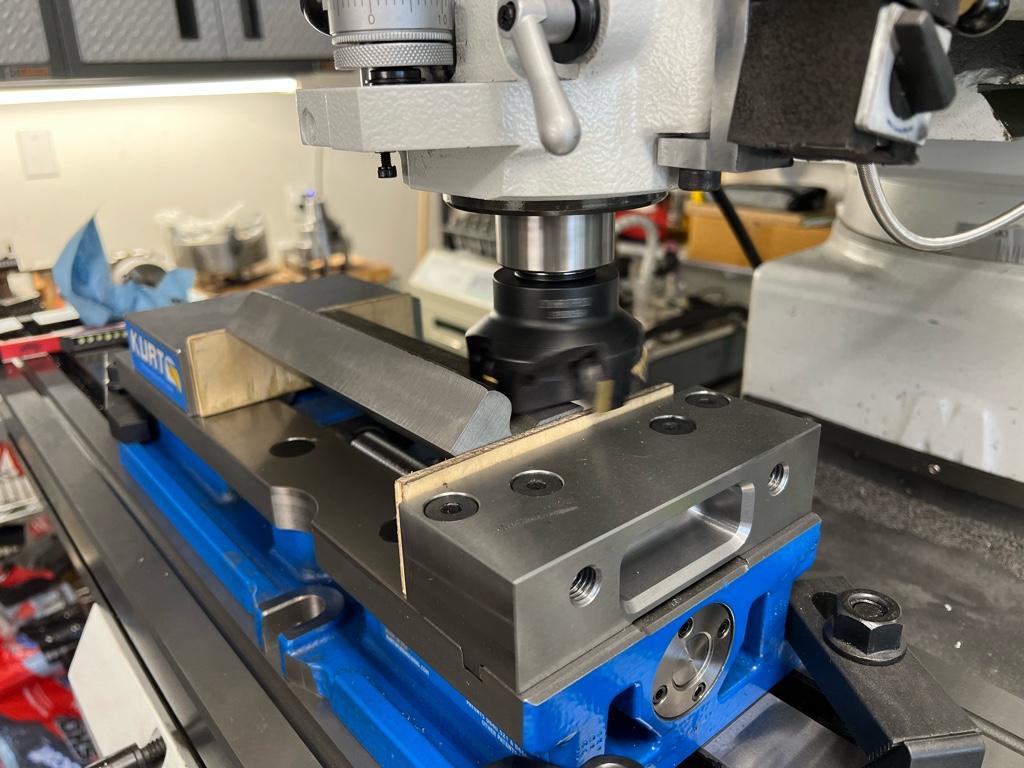
Checking my work on the surface plate with my steel Starrett master square, and despite my nascent machining skills, the cuts all came out surprisingly parallel and square! Even the 45 degree angle ended up as dead nuts as I could measure with my Mitutoyo precision bevel protractor. Score one for the rafter square!
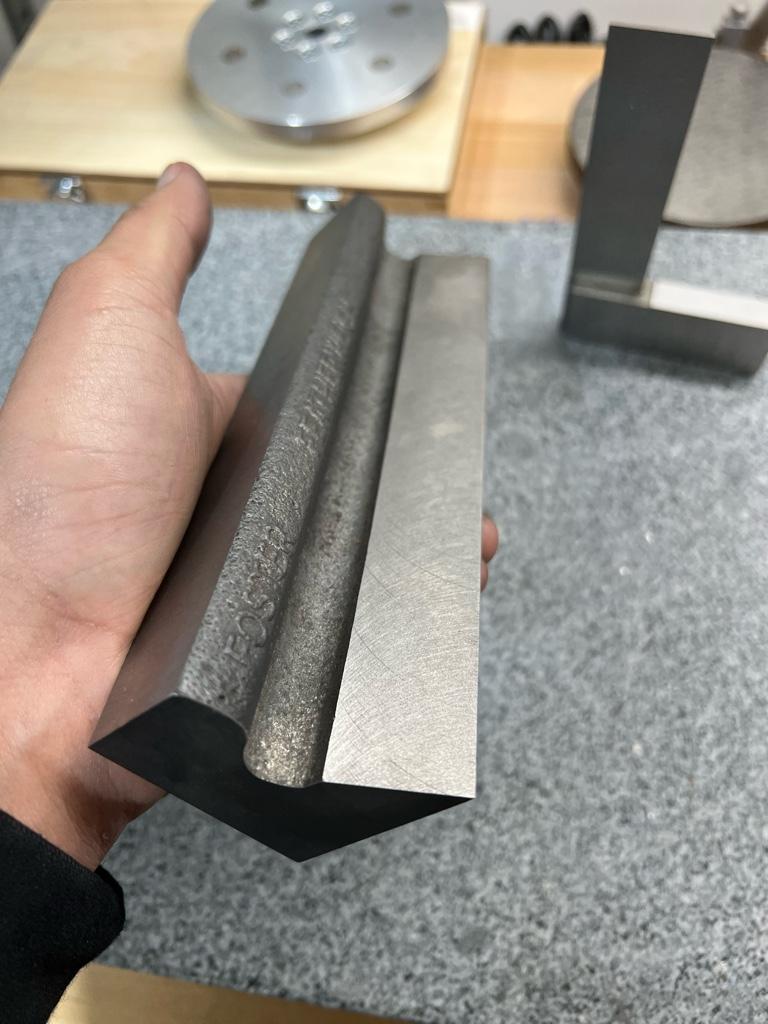
Next up: my first attempt at scraping!