- Joined
- Nov 23, 2014
- Messages
- 2,606
I have a buddy who impulse bought a Harbor Freight 90A flux-core wire feed welder. I have to admit to looking at them too, especially when they go on sale for under $90. They’re probably not a bad deal for the occasional weekend welding project, plus the 110V portability is nice. But as my dad constantly told me as a kid “you get what you pay for”.
Bottom line is the welds look terrible. Penetration is poor and there is a lot of spatter. Problem with the stock welder is it’s AC output, not DC. Current flows back & forth from the puddle to the wire which causes the flux-core wire to spatter even more than DC flux-core wire welding. All other HF wire feed welders are DC if that tells you anything. I did a little web research, watched a few YouTube videos and found that it’s fairly easy to convert these units from AC to DC. The two pieces of hardware needed are a full-wave rectifier and an electrolytic filter capacitor.
The rectifier takes the sine wave AC and flips the negative wave to the positive side so the output looks like “hills” running from 0V to peak voltage and back down, then back up again. The capacitor smooths out the “hills” to a relatively straight line or DC output. The videos I watched recommended a minimum 47,000 uF electrolytic capacitor with 30V minimum rating (welder outputs 28V). I found a number of eBay sources for the rectifier rated at 1000V and 100A for $10. Found a Siemens electrolytic cap rated at 40V and 47,000 uF for $25 delivered.
Another important component is a shunt resistor across the two leads of the capacitor. The resistor drains the capacitor after welding, otherwise the wire is still grounded and your ground clamp is still hot! Some guys on their conversion discharged the capacitor by touching the wire to the ground clamp; expect a nice spark. The capacitor I found had a shunt resistor already there, drains the cap in about 3 seconds.
The conversion is pretty simple; cut the output leads from the welder’s transformer and jump them to the AC side of the rectifier. The transformer output leads each have a small lead that runs to the welder’s circuit board, so the splicing takes place downstream from that point.
The rectifier has two output leads; + positive and – negative. Those leads run to the appropriate terminals on the capacitor. For flux-core wire, the welder ground clamp should be DC positive. So, the welder’s ground clamp lead is tied to the capacitor’s + Positive lead. The weld gun is tied to the capacitor’s – Negative lead.
One thing I didn’t care for on the on-line conversions is how they mounted the rectifier and capacitor. All of the examples had the rectifier mounted on the side of the case. They mounted the capacitor by drilling a couple of holes in the case and tie strapped in down. I guess that’s probably how Harbor Freight would do it . . .
I chose to mount the rectifier on the back of the case, just looks cleaner to me. Also made a sheet metal bracket to mount the capacitor next to the transformer. The cooling fan had to be moved down to make room for the rectifier. New fan holes were made in the case, in retrospect I should have removed the back panel and punched them on my Roper Whitney #218 press, but went the quicker route of drilling the holes. Then spent 15 minutes cleaning up burrs . . .
You can see from the example welds that the DC conversion makes a world of difference on the quality of the welds. I ran a bead using flux-core wire from my Hobart Handler 190, the HF stock AC and HF after the DC conversion. Much, much reduced spatter and much better penetration. The welder sounds better too, just a sizzle while welding instead of lots of spattering.
So what did I learn? Since everything in my shop will end up being my son’s someday, I went out and bought another Hobart, now have a Handler 140 (110V) to compliment my 190 (220V only). Sure, the Handler 140 110V welder is $500 compared to the bottom line about $150 for the HF 90A converted to DC. But I don’t want my son to inherit my shop and say, “Wow, dad bought a lot of cheap junk!” On the other hand, money doesn’t grow on trees so if you do have one of these HF 90A welders, consider spending around $50 and make some better welds.
Bruce
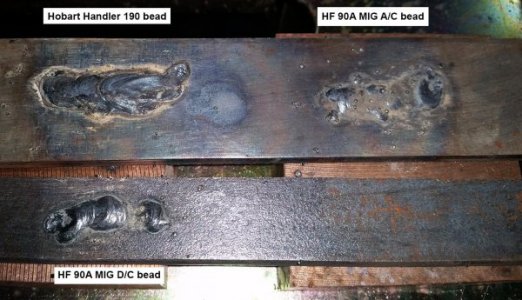
Bottom line is the welds look terrible. Penetration is poor and there is a lot of spatter. Problem with the stock welder is it’s AC output, not DC. Current flows back & forth from the puddle to the wire which causes the flux-core wire to spatter even more than DC flux-core wire welding. All other HF wire feed welders are DC if that tells you anything. I did a little web research, watched a few YouTube videos and found that it’s fairly easy to convert these units from AC to DC. The two pieces of hardware needed are a full-wave rectifier and an electrolytic filter capacitor.
The rectifier takes the sine wave AC and flips the negative wave to the positive side so the output looks like “hills” running from 0V to peak voltage and back down, then back up again. The capacitor smooths out the “hills” to a relatively straight line or DC output. The videos I watched recommended a minimum 47,000 uF electrolytic capacitor with 30V minimum rating (welder outputs 28V). I found a number of eBay sources for the rectifier rated at 1000V and 100A for $10. Found a Siemens electrolytic cap rated at 40V and 47,000 uF for $25 delivered.
Another important component is a shunt resistor across the two leads of the capacitor. The resistor drains the capacitor after welding, otherwise the wire is still grounded and your ground clamp is still hot! Some guys on their conversion discharged the capacitor by touching the wire to the ground clamp; expect a nice spark. The capacitor I found had a shunt resistor already there, drains the cap in about 3 seconds.
The conversion is pretty simple; cut the output leads from the welder’s transformer and jump them to the AC side of the rectifier. The transformer output leads each have a small lead that runs to the welder’s circuit board, so the splicing takes place downstream from that point.
The rectifier has two output leads; + positive and – negative. Those leads run to the appropriate terminals on the capacitor. For flux-core wire, the welder ground clamp should be DC positive. So, the welder’s ground clamp lead is tied to the capacitor’s + Positive lead. The weld gun is tied to the capacitor’s – Negative lead.
One thing I didn’t care for on the on-line conversions is how they mounted the rectifier and capacitor. All of the examples had the rectifier mounted on the side of the case. They mounted the capacitor by drilling a couple of holes in the case and tie strapped in down. I guess that’s probably how Harbor Freight would do it . . .
I chose to mount the rectifier on the back of the case, just looks cleaner to me. Also made a sheet metal bracket to mount the capacitor next to the transformer. The cooling fan had to be moved down to make room for the rectifier. New fan holes were made in the case, in retrospect I should have removed the back panel and punched them on my Roper Whitney #218 press, but went the quicker route of drilling the holes. Then spent 15 minutes cleaning up burrs . . .
You can see from the example welds that the DC conversion makes a world of difference on the quality of the welds. I ran a bead using flux-core wire from my Hobart Handler 190, the HF stock AC and HF after the DC conversion. Much, much reduced spatter and much better penetration. The welder sounds better too, just a sizzle while welding instead of lots of spattering.
So what did I learn? Since everything in my shop will end up being my son’s someday, I went out and bought another Hobart, now have a Handler 140 (110V) to compliment my 190 (220V only). Sure, the Handler 140 110V welder is $500 compared to the bottom line about $150 for the HF 90A converted to DC. But I don’t want my son to inherit my shop and say, “Wow, dad bought a lot of cheap junk!” On the other hand, money doesn’t grow on trees so if you do have one of these HF 90A welders, consider spending around $50 and make some better welds.
Bruce
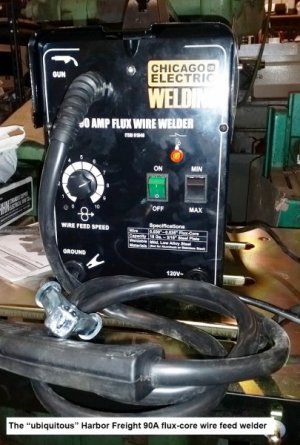
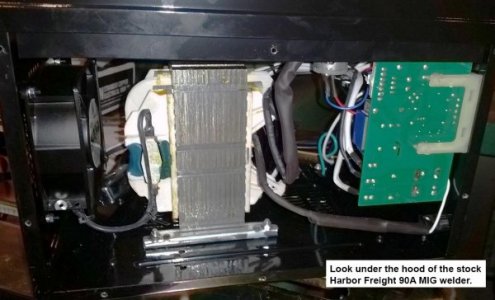
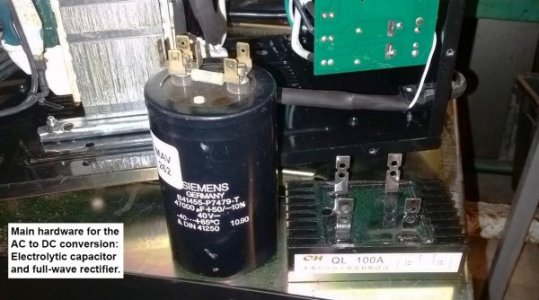
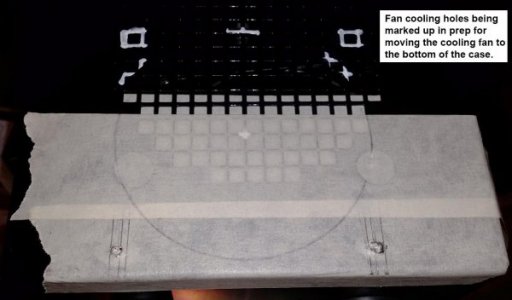
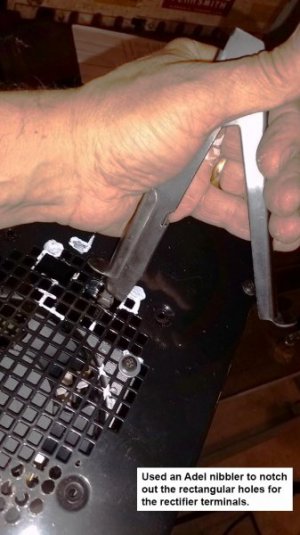
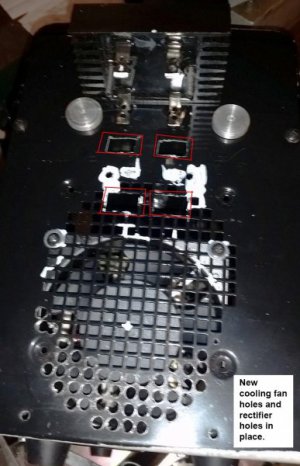
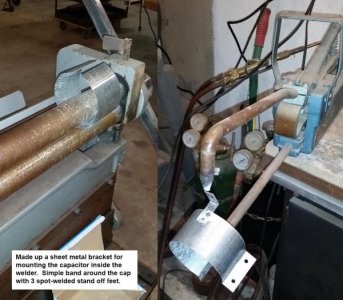
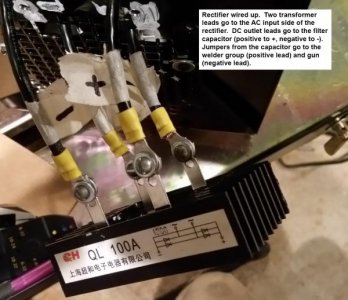
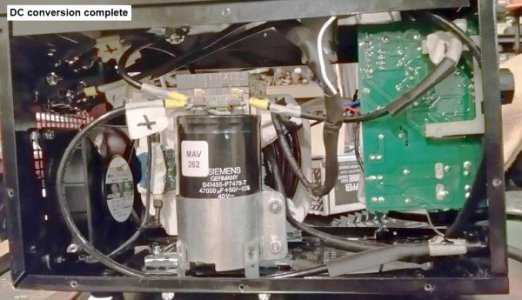
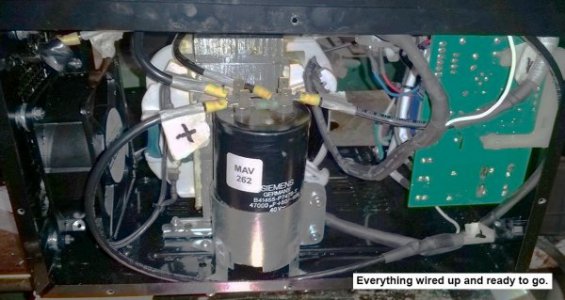
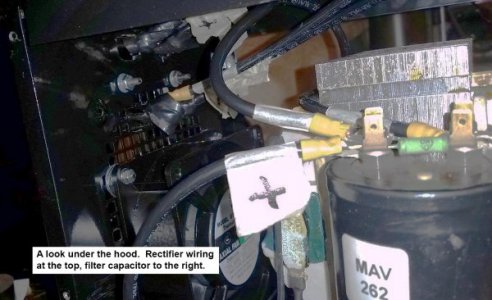
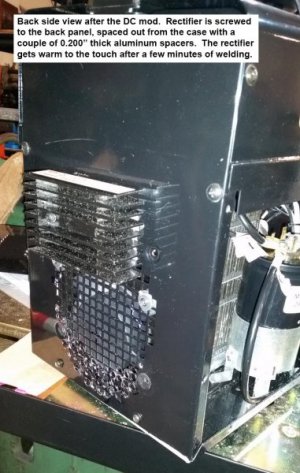
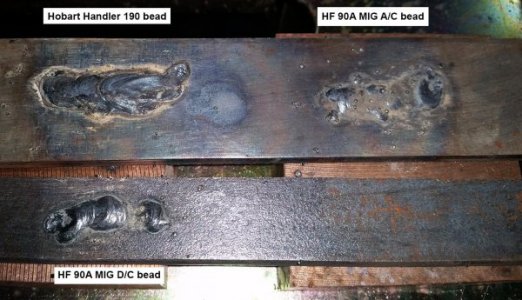