- Joined
- Sep 29, 2017
- Messages
- 2,251
I have a little problem wich I have to solve so I have to determine what causes the problem so I hope someone can help. Lately I discovered that when ever I want to mill something on my mill/drill to get two sides parallel to each other,something goes wrong and it ends up slightly taper(ish).
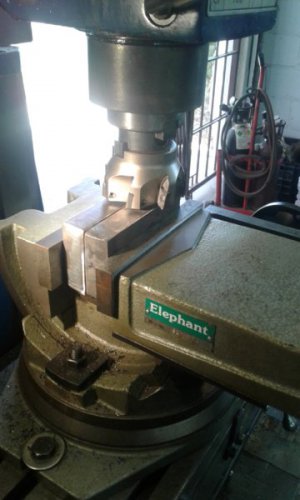
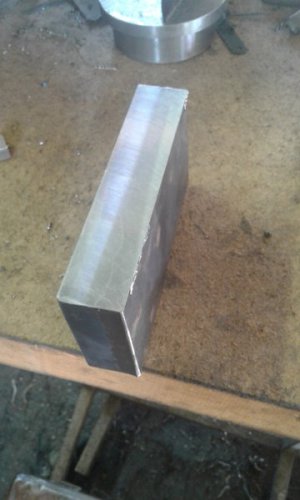
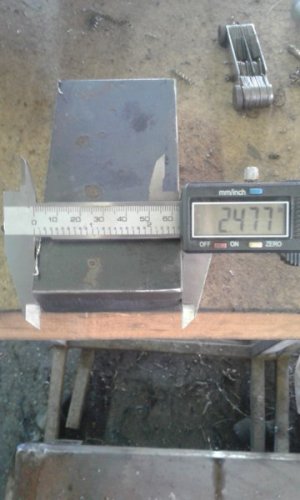
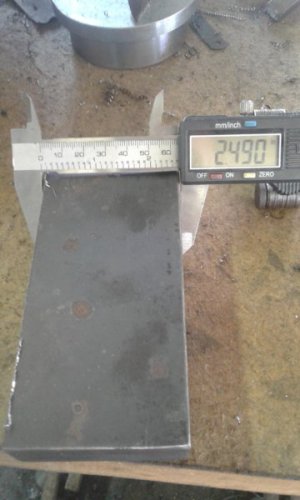
I would mill one side flat,turn the stock around and put the flat side on the bottom and my head tells that if I run the mill over the other side,then the two sides SHOULD be the same, but they are not. I usually work metric,but I will give the sizes imperial so you don't have to do the convertions. The sides are off by about 0.013 inches over a distance of 4.724inches. It's not much it won't work for me. I doubt that there is something wrong on the vice,because it is brand new.
It is as if the bed runs down to one side. Could this be a gib problem or something bigger. I guess I can run a dial indicator down the length of the bed to check if the bed is worn down to one side . Any other ideas would be appreciated FIX the problem
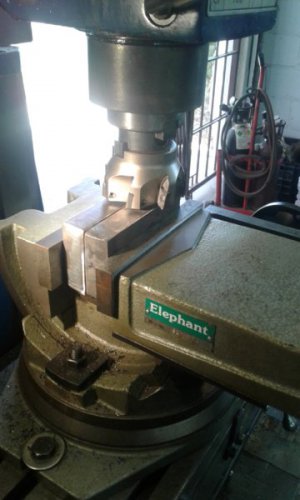
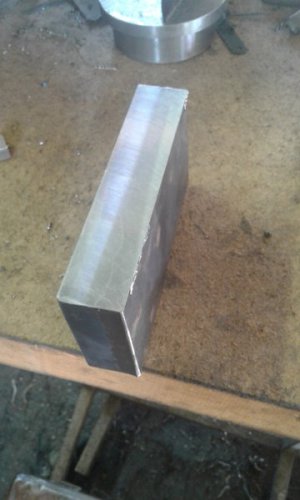
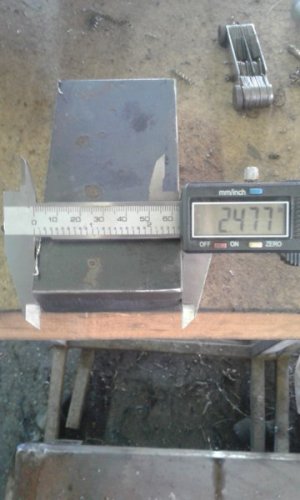
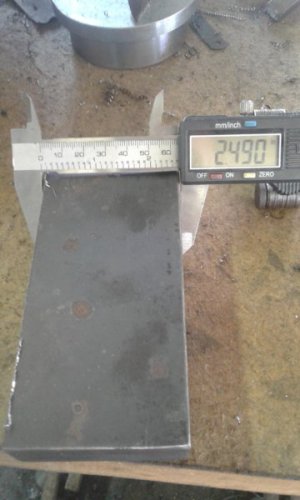
I would mill one side flat,turn the stock around and put the flat side on the bottom and my head tells that if I run the mill over the other side,then the two sides SHOULD be the same, but they are not. I usually work metric,but I will give the sizes imperial so you don't have to do the convertions. The sides are off by about 0.013 inches over a distance of 4.724inches. It's not much it won't work for me. I doubt that there is something wrong on the vice,because it is brand new.
It is as if the bed runs down to one side. Could this be a gib problem or something bigger. I guess I can run a dial indicator down the length of the bed to check if the bed is worn down to one side . Any other ideas would be appreciated FIX the problem