Finally have my Atlas 10100 Mk.2 sitting on the rolling tool storage cart that's going to be it's home and need some advice on how to get it to stop cutting a 0.001 per inch taper !! I have a Starrett 98 8" level that I'm trying to use in conjunction with the 2 collar cut test to get rid of the but it's driving me a bit nuts. As it sits right now... I have a 1" dia. X 5. 75 steel bar mounted in the 4-jaw that I dialed in to less than 0.001 with the DTI indicated in the middle of the 5" sticking out of the chuck, which seemed to average the run out at each end (measured with DTI at chuck jaws & far end of bar) to 0.005.
At this point the lathe has 2 1/64 auto body shims (measured 0.037) under the tailstock end front foot & mounting bolts are tightened down. I mark the test bar for 1" collars at each end of the 5 inch bar and dial in a 0.005 cut on the compound (compound set at 60 degrees) to cut the center of the bar down 0.030 to make the barbell shape that forms the collars. I make the cut, stop the lathe, take a measurement...the 3" section of the 0.005 cut I made has a taper of 0.003...the end sticking out farthest from the chuck measures 0.0032 taper coming in at 0.993 according to the 2 cheap mics I have. At the point closest to the chuck the measurement is spot on 0.990.
According to the level the tailstock end of the bed is one mark + higher than the headstock end on the front side. I've watched the YT vids explaining the effect of bed twist on how the cutting tool "sees" the work as it traverses the bed while cutting and I'm scratching my head thinking that with that much shim (0.037) under the tailstock front foot, that the cutting tool should be cutting into the work way more at the end farthest from the chuck ?????... In the videos the shim amount to address the taper is small and the effect fairly drastic/immediate in eliminating the taper.
I also noticed in the manual for the lathe in the section on leveling it states not to swap the level end for end during the leveling process, Anyone know why that would be so ?? Shouldn't the level, if properly calibrated, read the same even if the ends were swapped during the leveling process ?? This is my first time trying to level a machine properly & the proof seems to be in the cut it makes, but I'm hesitant to add anymore shims under the tailstock front foot to address the taper fearing I'll induce cracking of the bed feet when tightened down due to the disparity of the surfaces. Here's a pic of how it's set up...
Level reading at headstock...
Level reading at tailstock...
At this point the lathe has 2 1/64 auto body shims (measured 0.037) under the tailstock end front foot & mounting bolts are tightened down. I mark the test bar for 1" collars at each end of the 5 inch bar and dial in a 0.005 cut on the compound (compound set at 60 degrees) to cut the center of the bar down 0.030 to make the barbell shape that forms the collars. I make the cut, stop the lathe, take a measurement...the 3" section of the 0.005 cut I made has a taper of 0.003...the end sticking out farthest from the chuck measures 0.0032 taper coming in at 0.993 according to the 2 cheap mics I have. At the point closest to the chuck the measurement is spot on 0.990.
According to the level the tailstock end of the bed is one mark + higher than the headstock end on the front side. I've watched the YT vids explaining the effect of bed twist on how the cutting tool "sees" the work as it traverses the bed while cutting and I'm scratching my head thinking that with that much shim (0.037) under the tailstock front foot, that the cutting tool should be cutting into the work way more at the end farthest from the chuck ?????... In the videos the shim amount to address the taper is small and the effect fairly drastic/immediate in eliminating the taper.
I also noticed in the manual for the lathe in the section on leveling it states not to swap the level end for end during the leveling process, Anyone know why that would be so ?? Shouldn't the level, if properly calibrated, read the same even if the ends were swapped during the leveling process ?? This is my first time trying to level a machine properly & the proof seems to be in the cut it makes, but I'm hesitant to add anymore shims under the tailstock front foot to address the taper fearing I'll induce cracking of the bed feet when tightened down due to the disparity of the surfaces. Here's a pic of how it's set up...
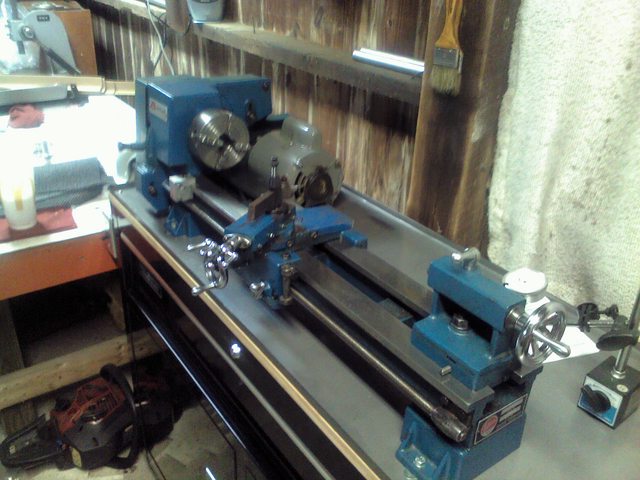
Level reading at headstock...
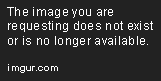
Level reading at tailstock...
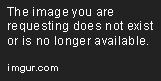