- Joined
- May 8, 2018
- Messages
- 336
The Chinese 10x22 lathes like my Grizzly G0572/G0602 and many others I'm sure have a single mounting point in each foot. While one can add shims to get the ways co-planar that seemed like it would be a tedious process. Given that this procedure is not a one time deal, I wanted something more easily adjusted. I did a lot of research and received a TON of help from @mikey . Thanks to him as always for all his help!
This phot that Mikey sent me shows the basic idea of the leveling plates...
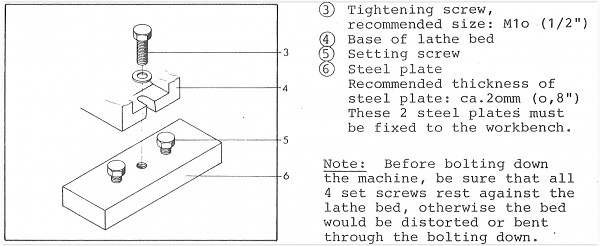
I made 2 leveling plates from 1/2" steel plate. The plates are 5" long so they are slightly wider than the feet and 2" wide.
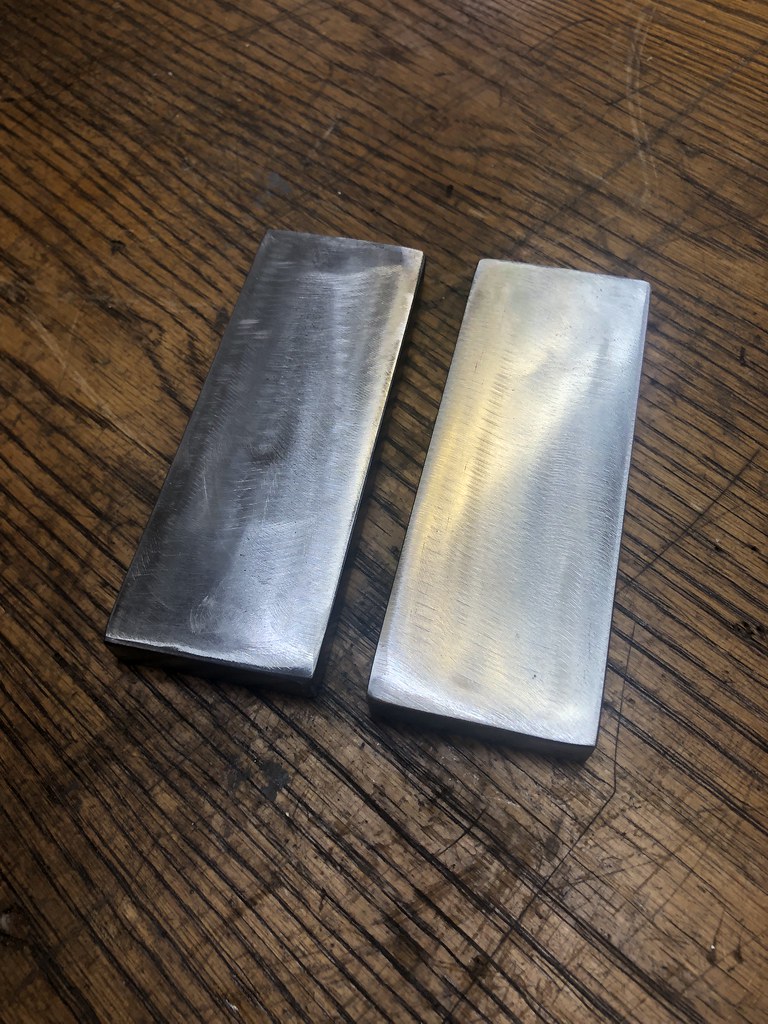
There are 5 holes necessary in each plate. 3 are thru holes and 2 are tapped holes for the leveling bolts. I used 1/2x20 grade 8 hardware for this project.
I drilled and tapped the 4 leveling bolt holes and drilled the 6 thru holes on the mill. I also faced the bolt heads to remove the grade markings and provide a flat bearing surface. Jam nuts are used on the bolts.
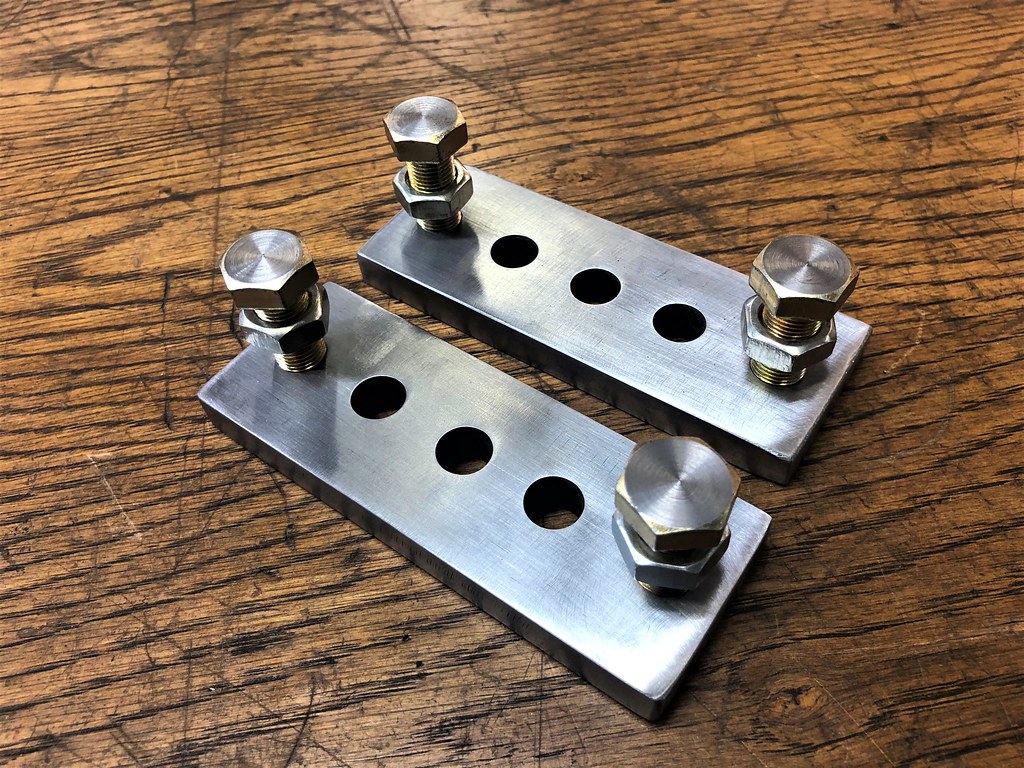
The feet on this lathe are not exactly conducive to doing this mod. There is an open area in the center with a round cast boss for the hold down bolt. I cut 1/4" steel plates for each foot, 5x6 for the tail stock end and 5x7 for the head stock end. Those plates are bolted to the feet with 1/4x28 bolts.
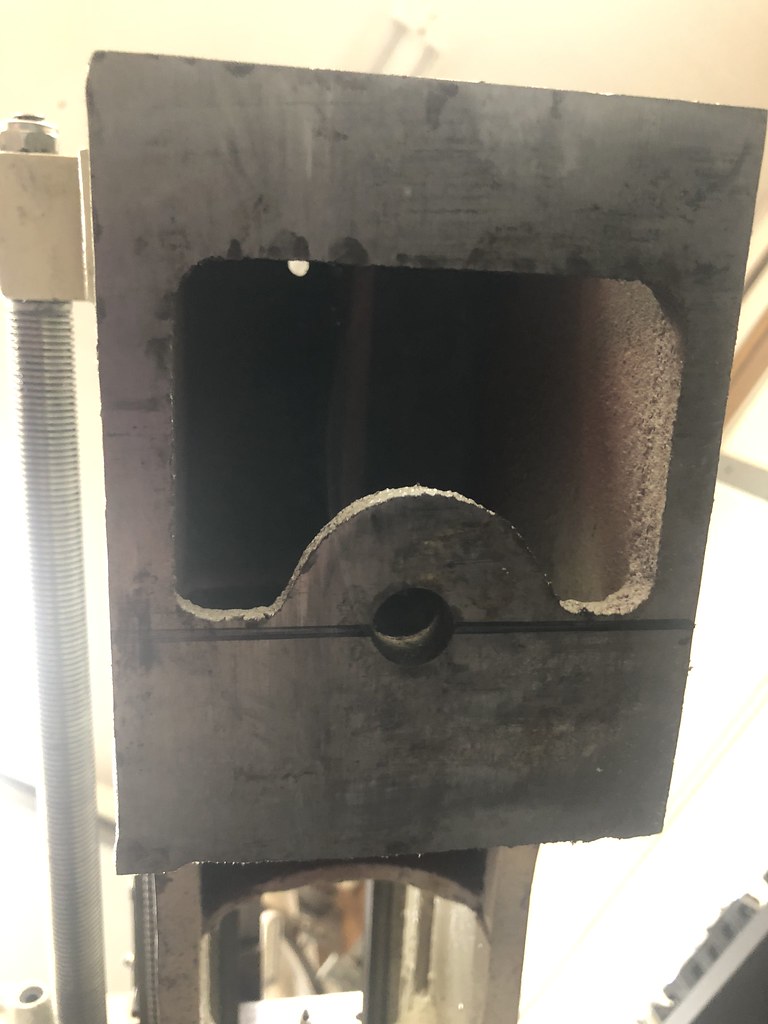
On my application the chip pan is meant to be mounted on the factory stand which has reinforcing plates on the top of each end. This means the chip tray does not sit flat at the through hole. I cut 2 - 6" x 6" aluminum spacers.
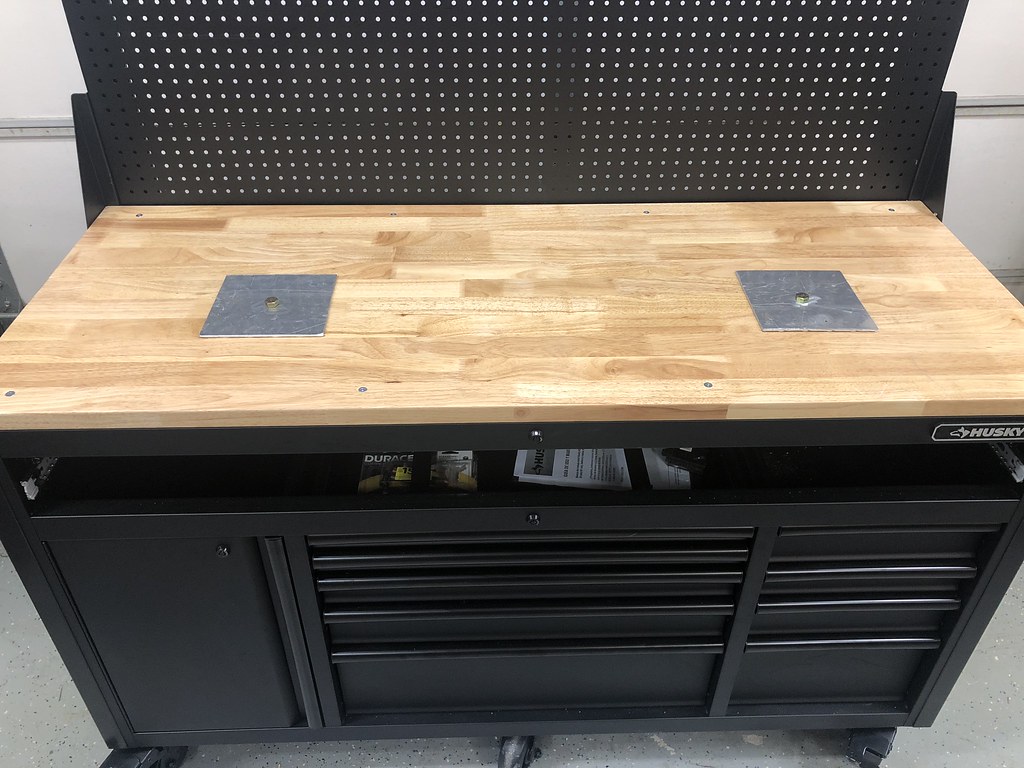
I used transfer punches to mark the holes so I could drill them in the chip pan, spacers and bench top. The leveling plates were then mounted to the bench.
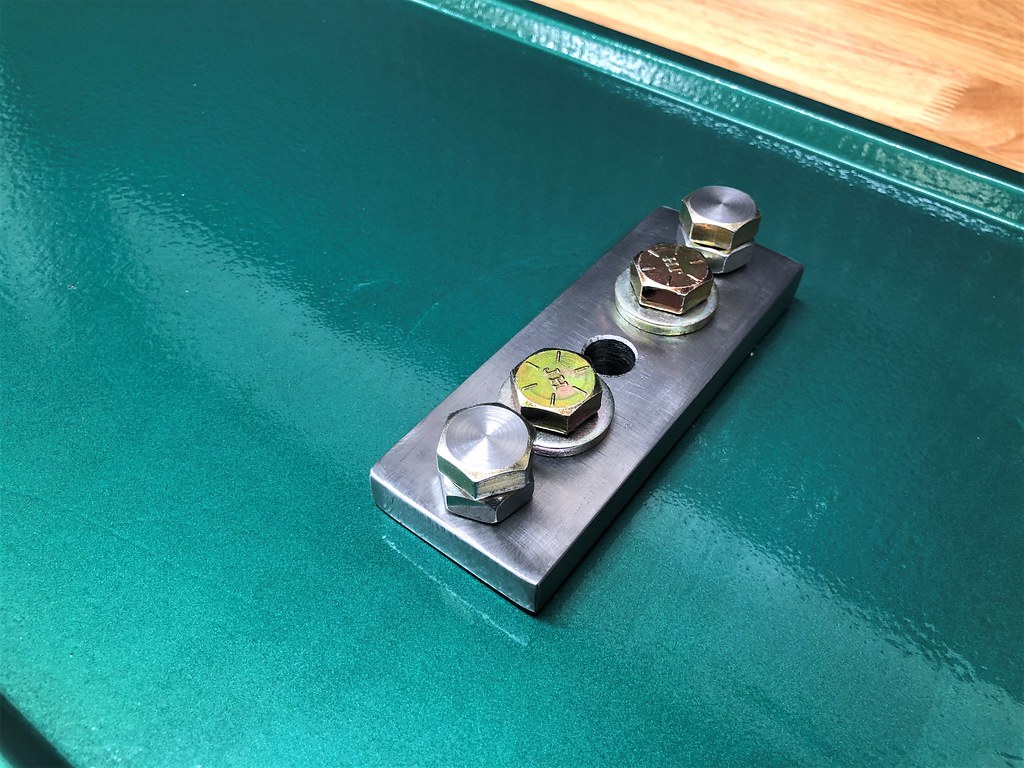
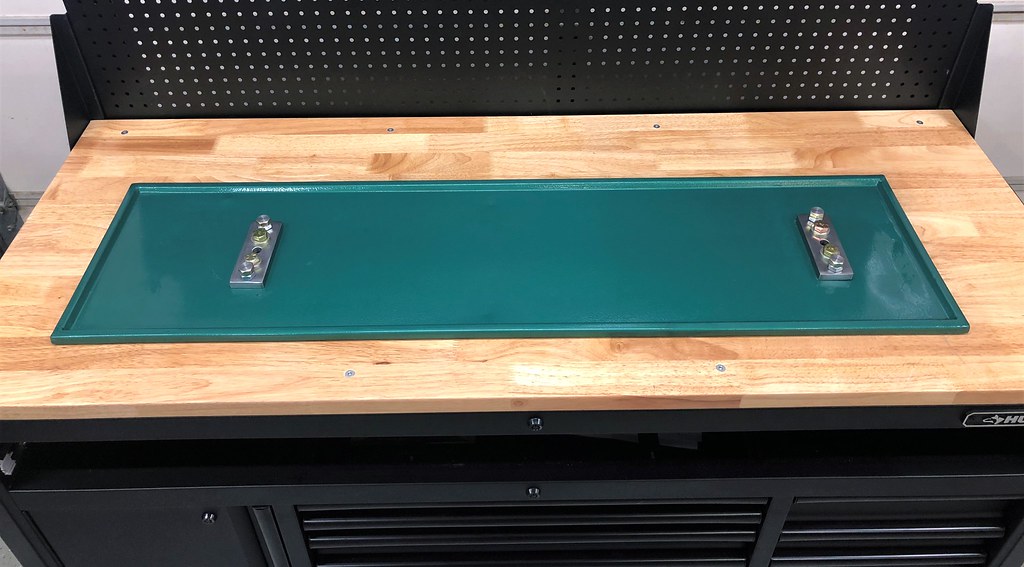
At this point it's time to set the lathe on the levers.
Here you can see how the leveling bolts contact the plates on the feet.
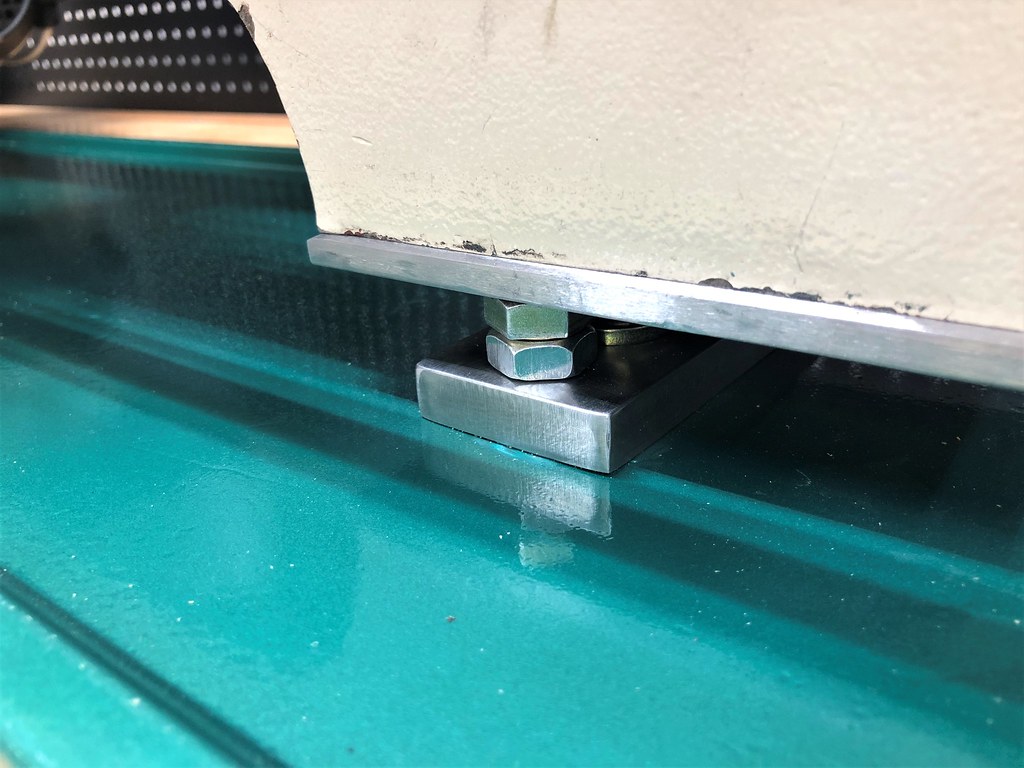
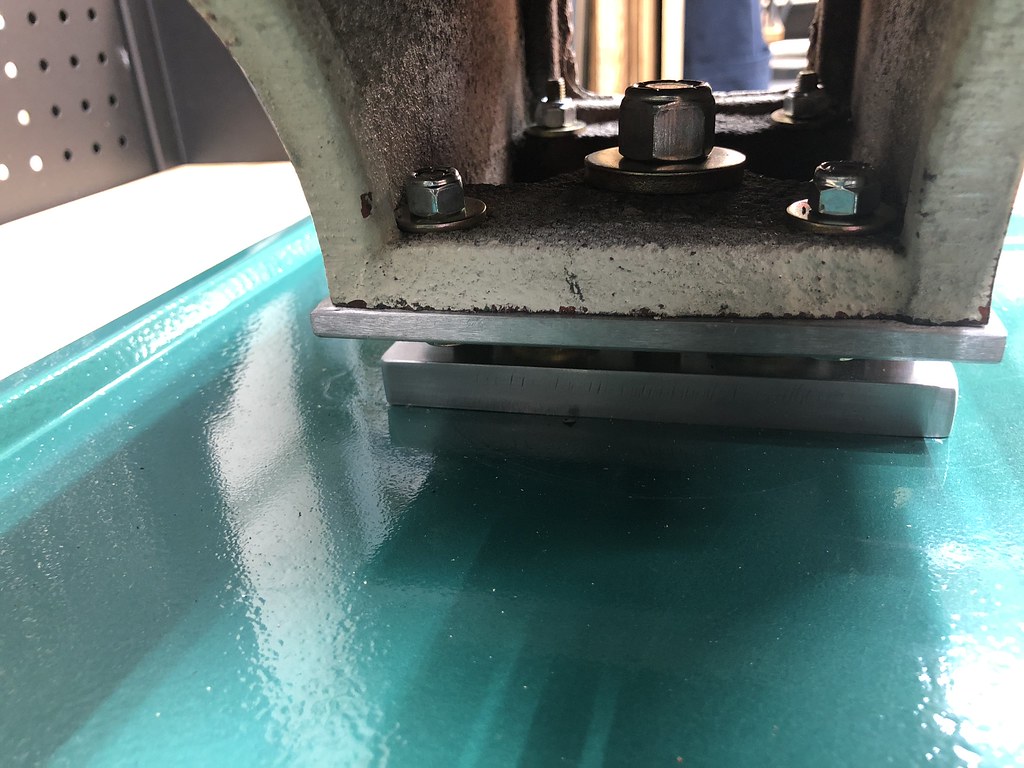
Once the lathe was placed on the bench I loosely installed the mounting bolts and began the leveling process. For me the only adjustment needed was to the rear leveling bolts so I locked down the front bolts and moved on with the process of adjusting. I began at the head stock. This is the first time I have ever done this and I was very much amazed at how little adjustment it took to make a huge difference. It is a must to use fine thread bolts for the levelers.
I used 123 blocks on the ways and a Mahr 12" machinist's level for this process.
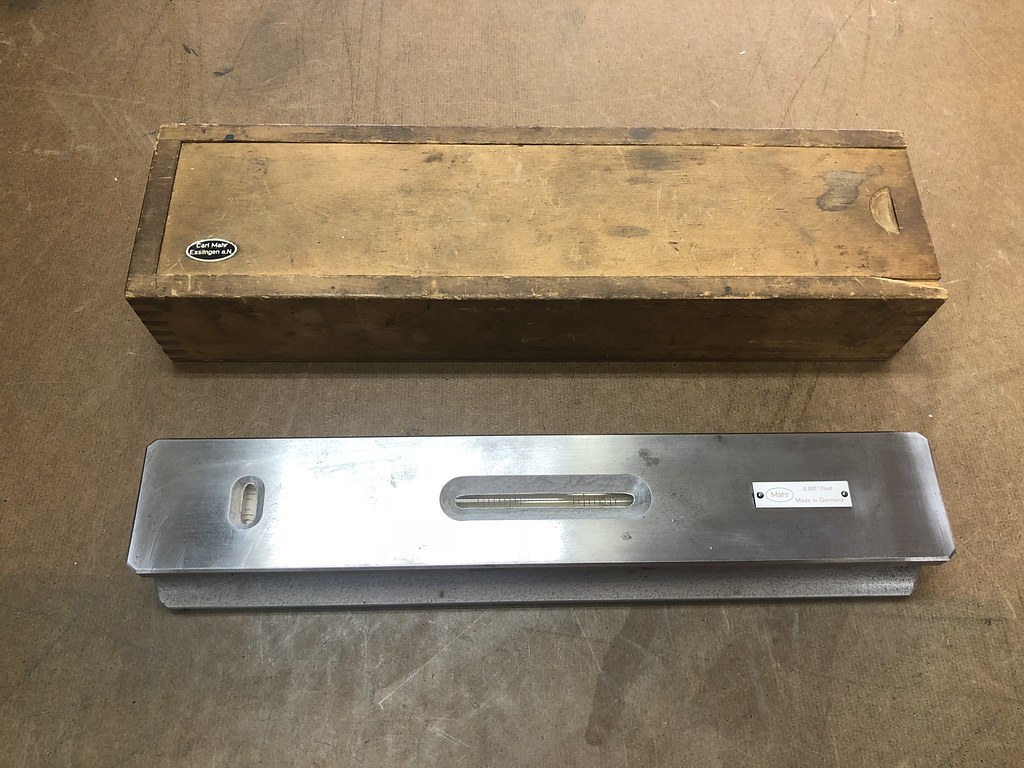
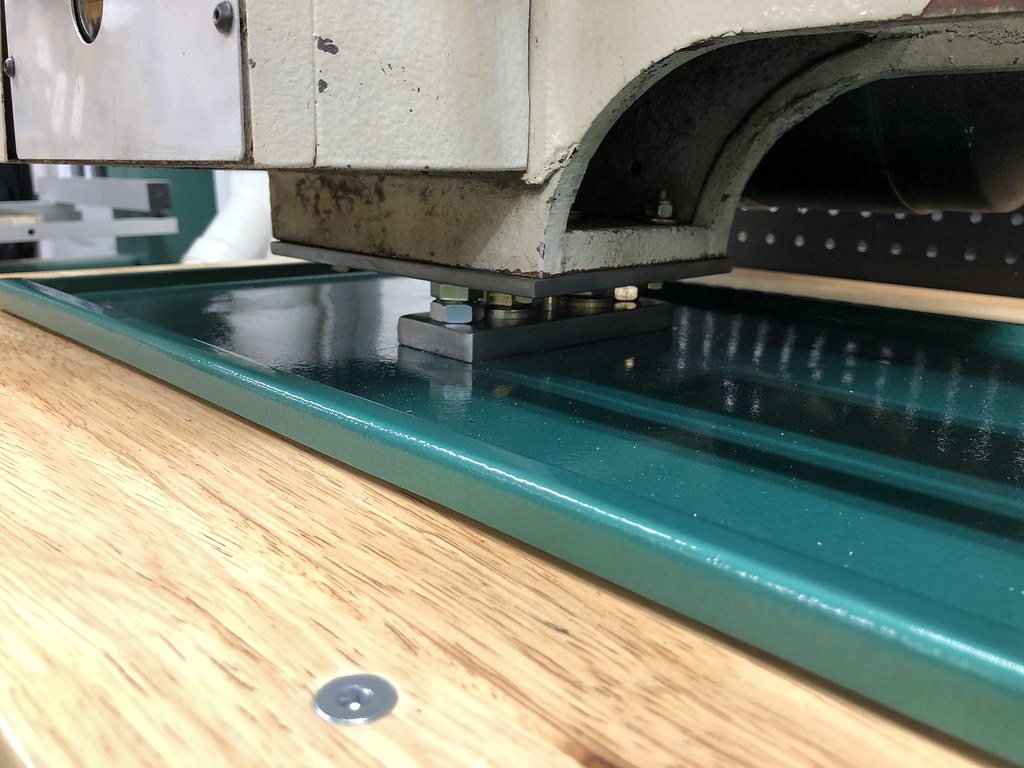
It only took a few minutes to get the head stock end perfectly level. I did figure out that once I get very close if I very lightly snugged the mounting bolt it helped me to see the very slight movements as I adjusted the lever.
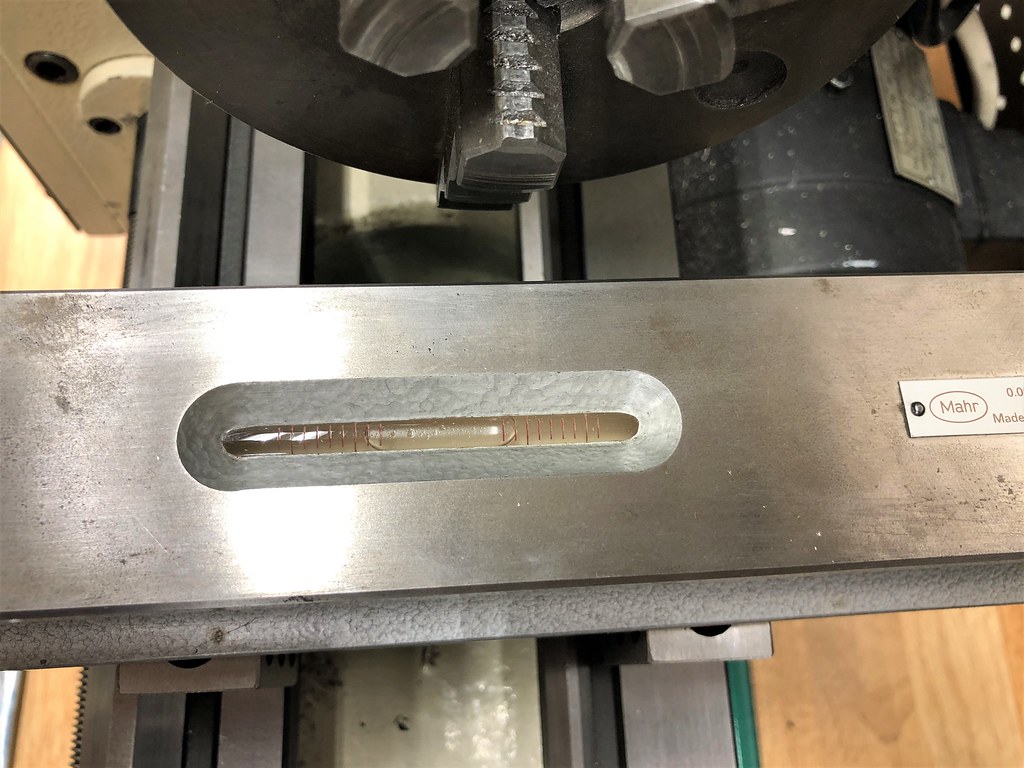
Moved to the tail stock end. Only a couple of minutes to get it perfectly in plane with the head stock.
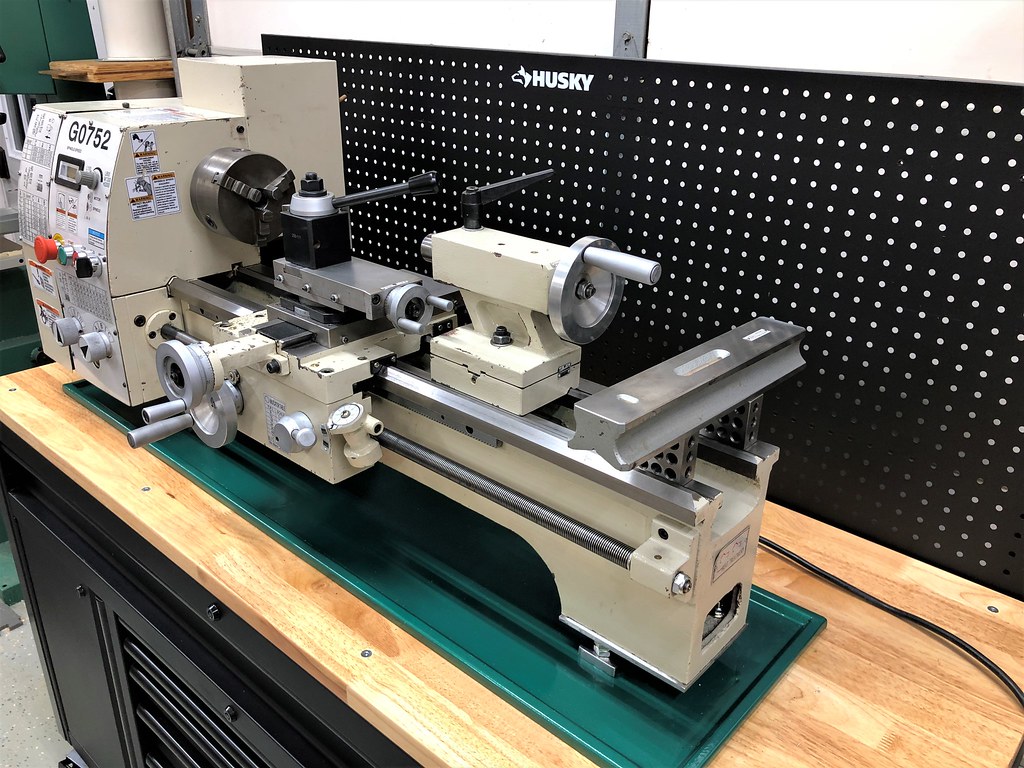
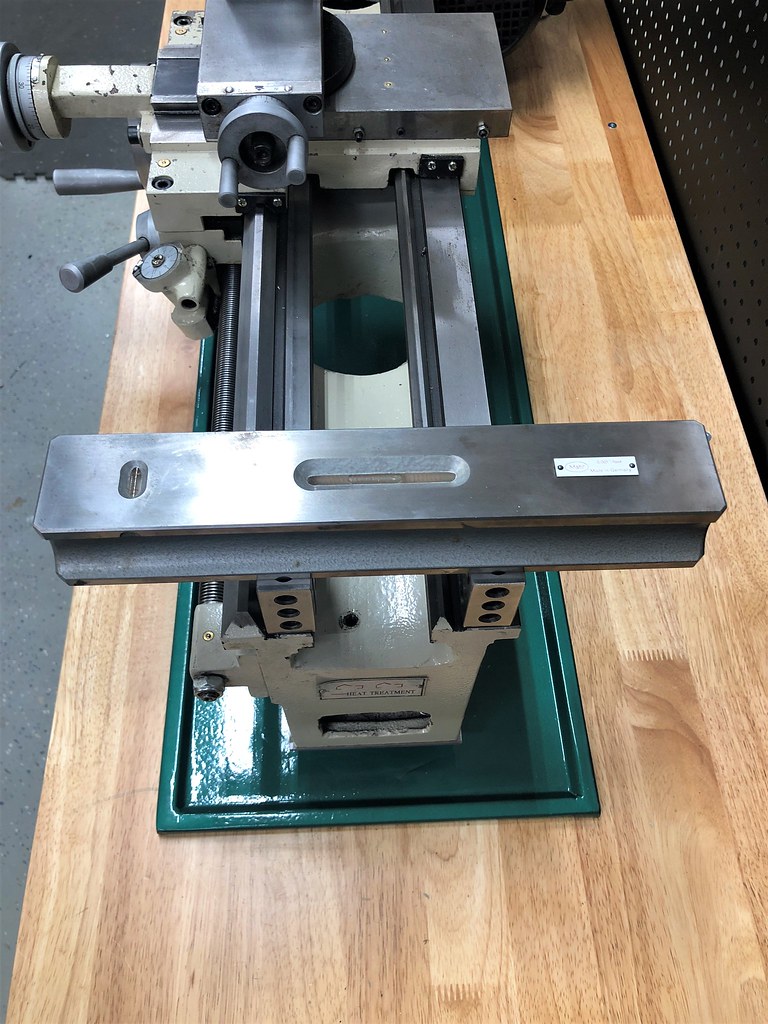
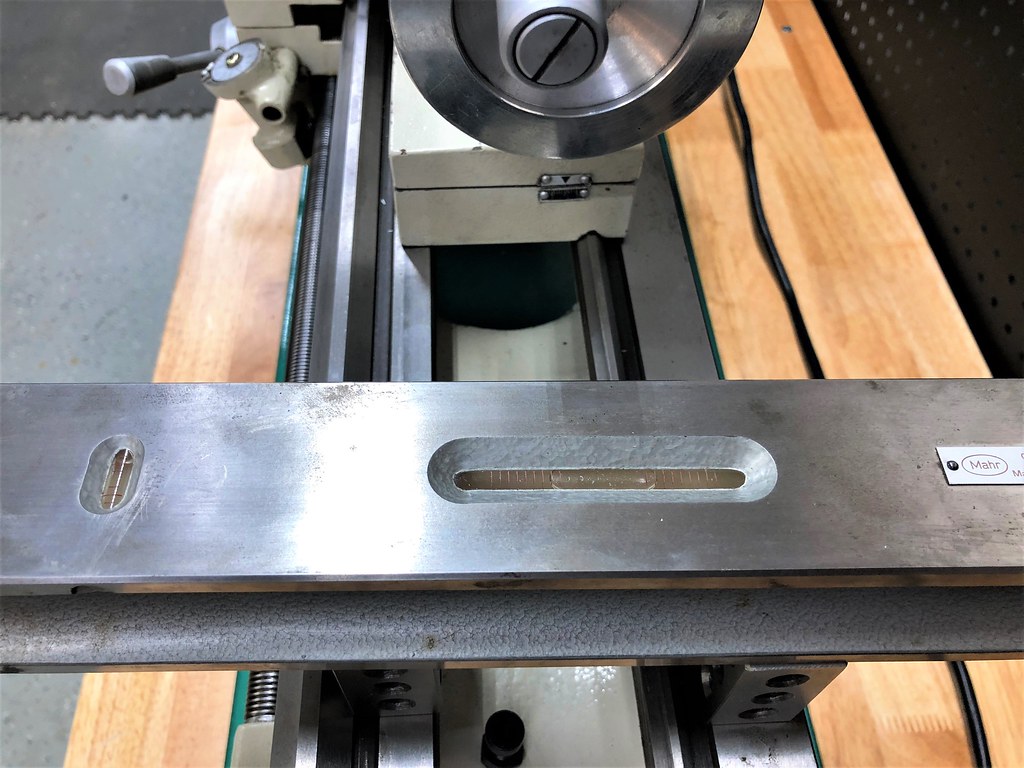
I also like the added height that the levelers make between the bed and the chip tray. Much more room to clean out the chips.
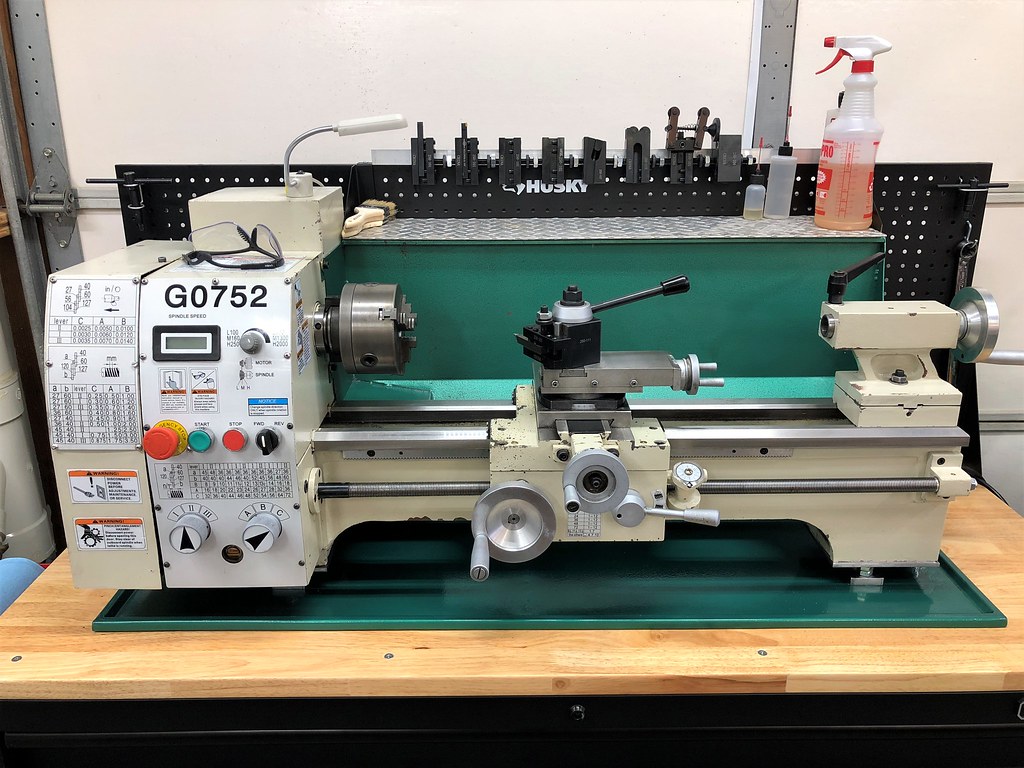
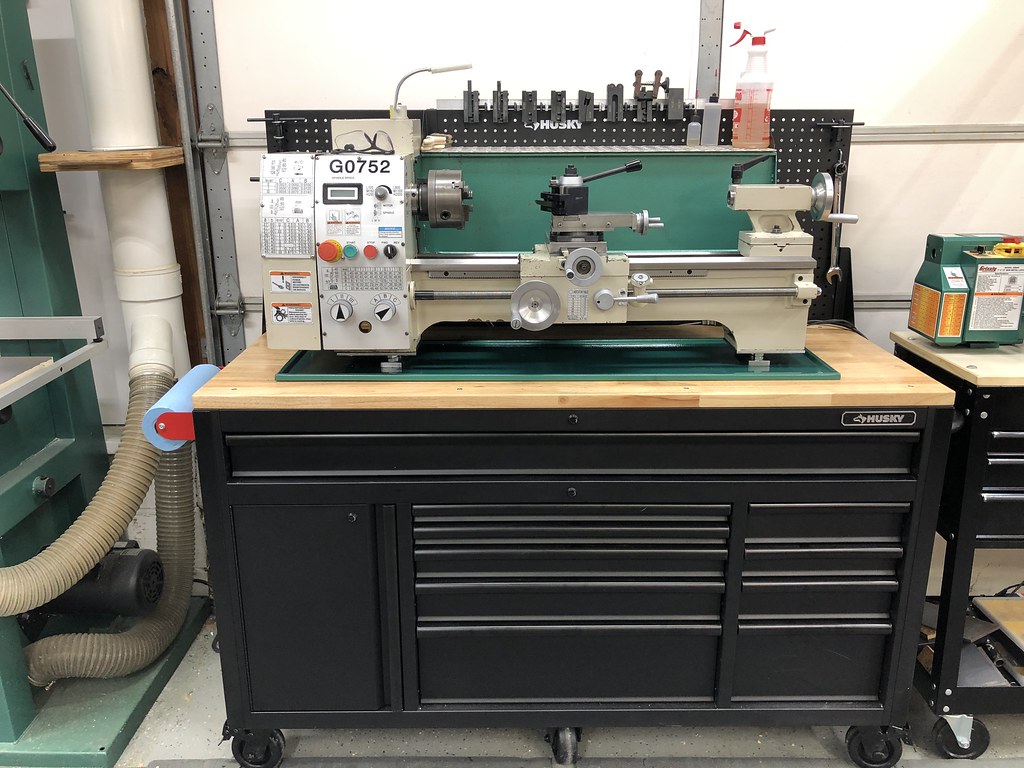
Thanks for looking and I hope this is helpful to someone.
This phot that Mikey sent me shows the basic idea of the leveling plates...
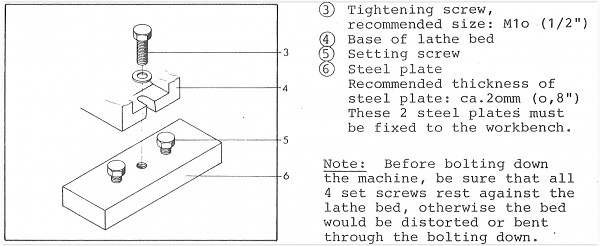
I made 2 leveling plates from 1/2" steel plate. The plates are 5" long so they are slightly wider than the feet and 2" wide.
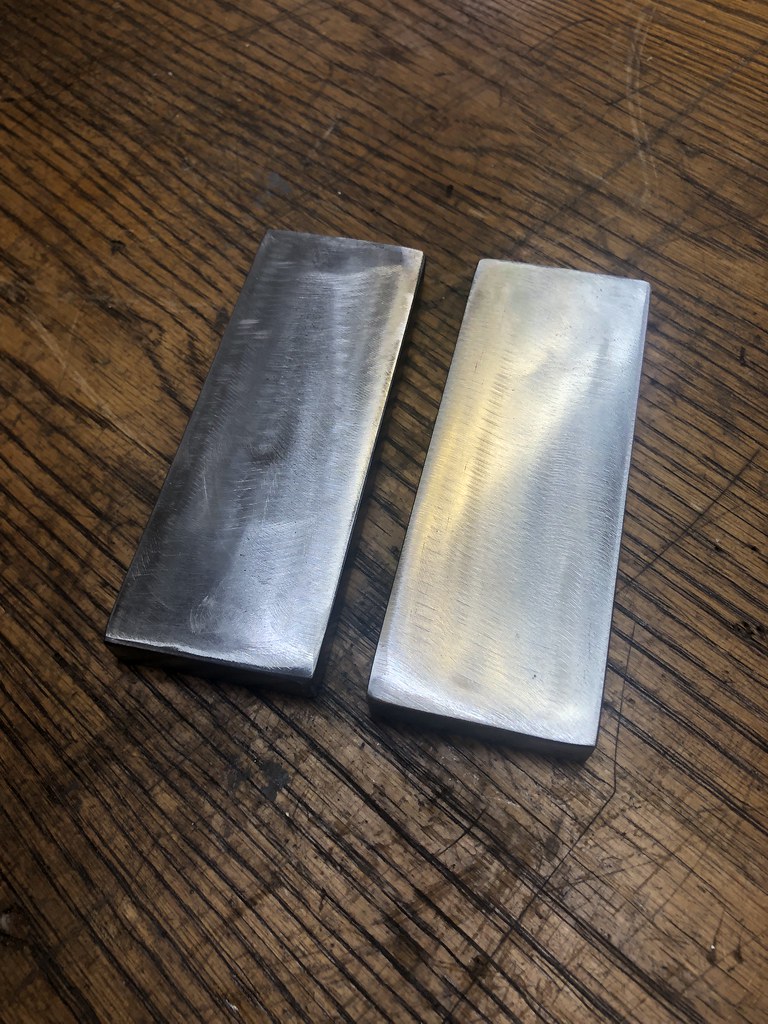
There are 5 holes necessary in each plate. 3 are thru holes and 2 are tapped holes for the leveling bolts. I used 1/2x20 grade 8 hardware for this project.
I drilled and tapped the 4 leveling bolt holes and drilled the 6 thru holes on the mill. I also faced the bolt heads to remove the grade markings and provide a flat bearing surface. Jam nuts are used on the bolts.
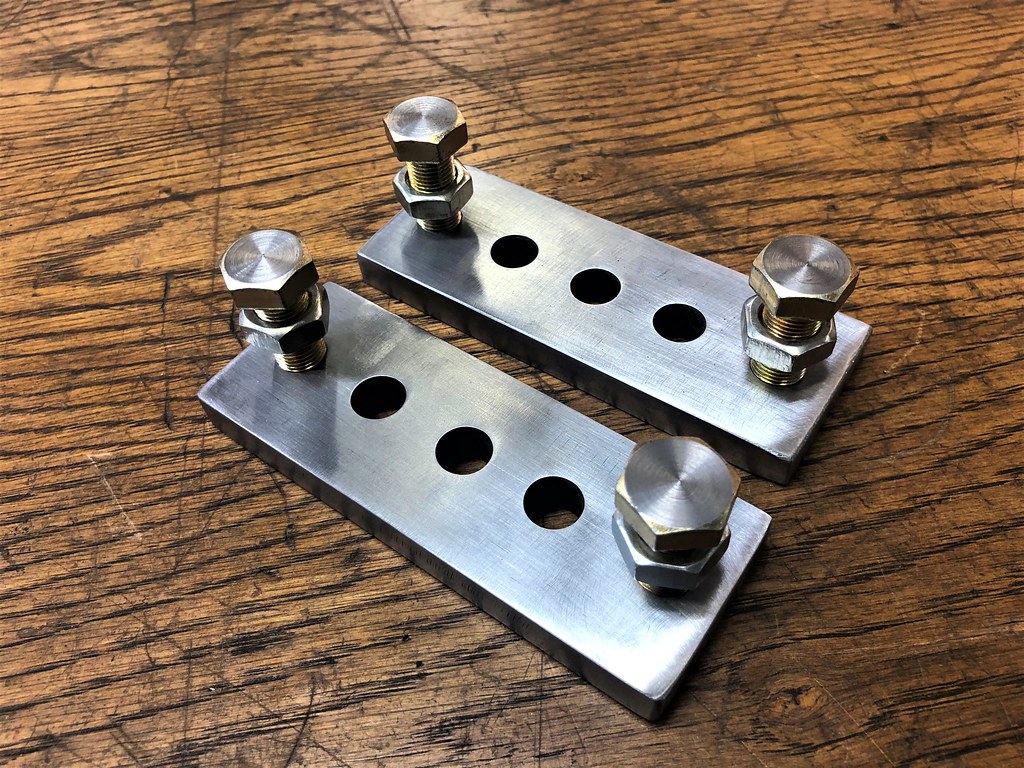
The feet on this lathe are not exactly conducive to doing this mod. There is an open area in the center with a round cast boss for the hold down bolt. I cut 1/4" steel plates for each foot, 5x6 for the tail stock end and 5x7 for the head stock end. Those plates are bolted to the feet with 1/4x28 bolts.
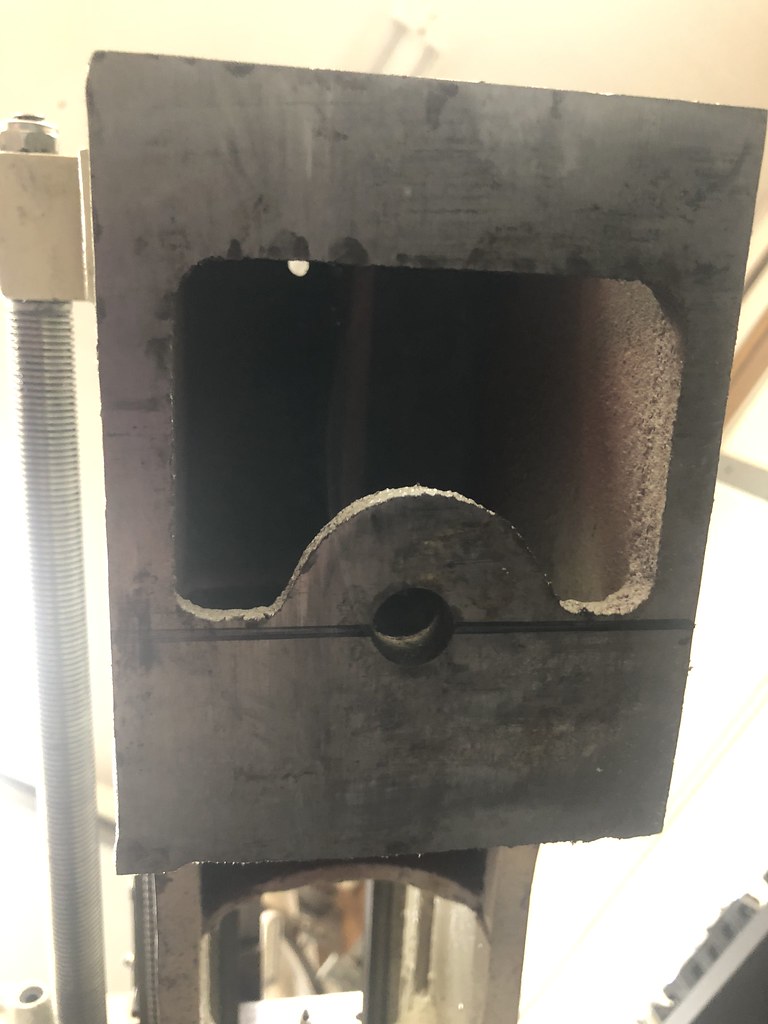
On my application the chip pan is meant to be mounted on the factory stand which has reinforcing plates on the top of each end. This means the chip tray does not sit flat at the through hole. I cut 2 - 6" x 6" aluminum spacers.
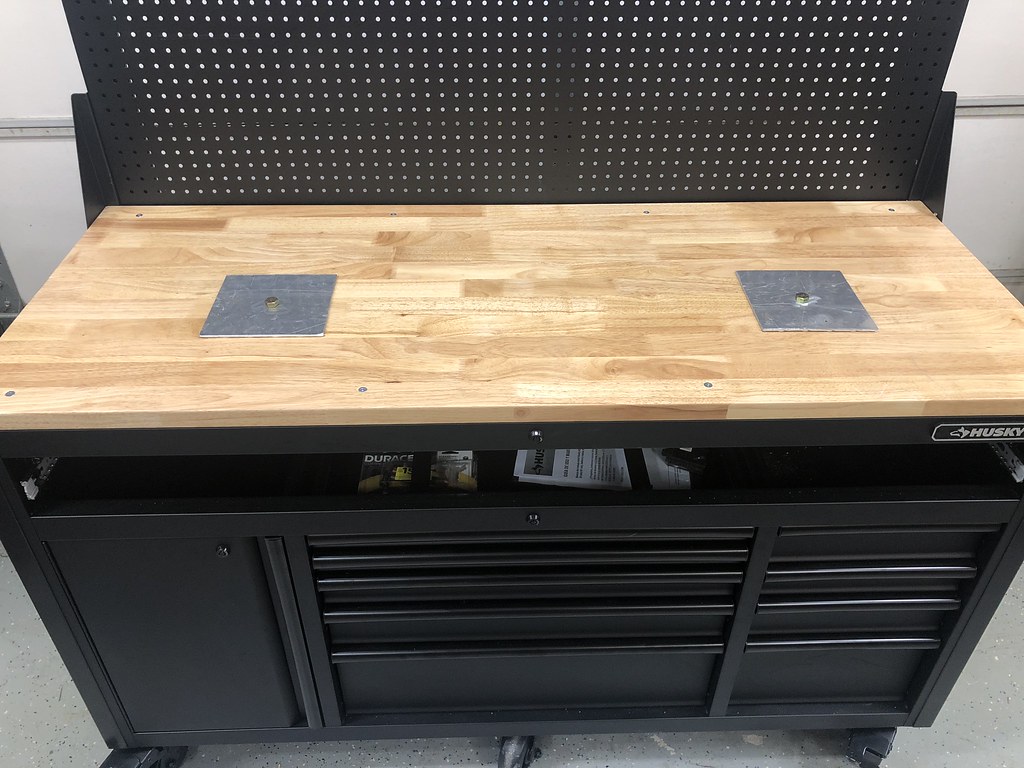
I used transfer punches to mark the holes so I could drill them in the chip pan, spacers and bench top. The leveling plates were then mounted to the bench.
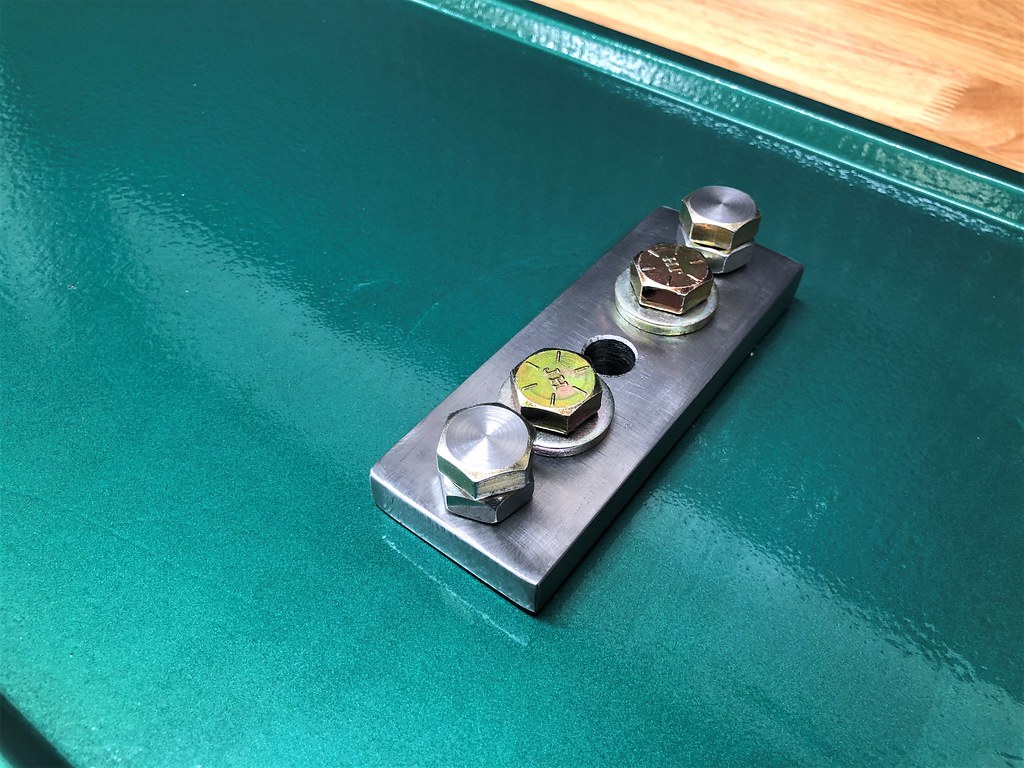
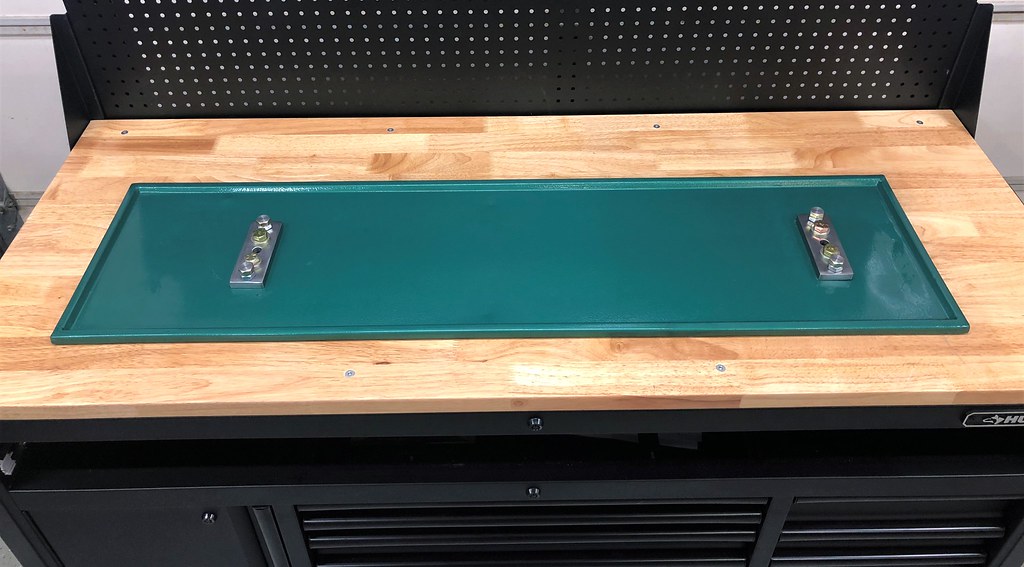
At this point it's time to set the lathe on the levers.
Here you can see how the leveling bolts contact the plates on the feet.
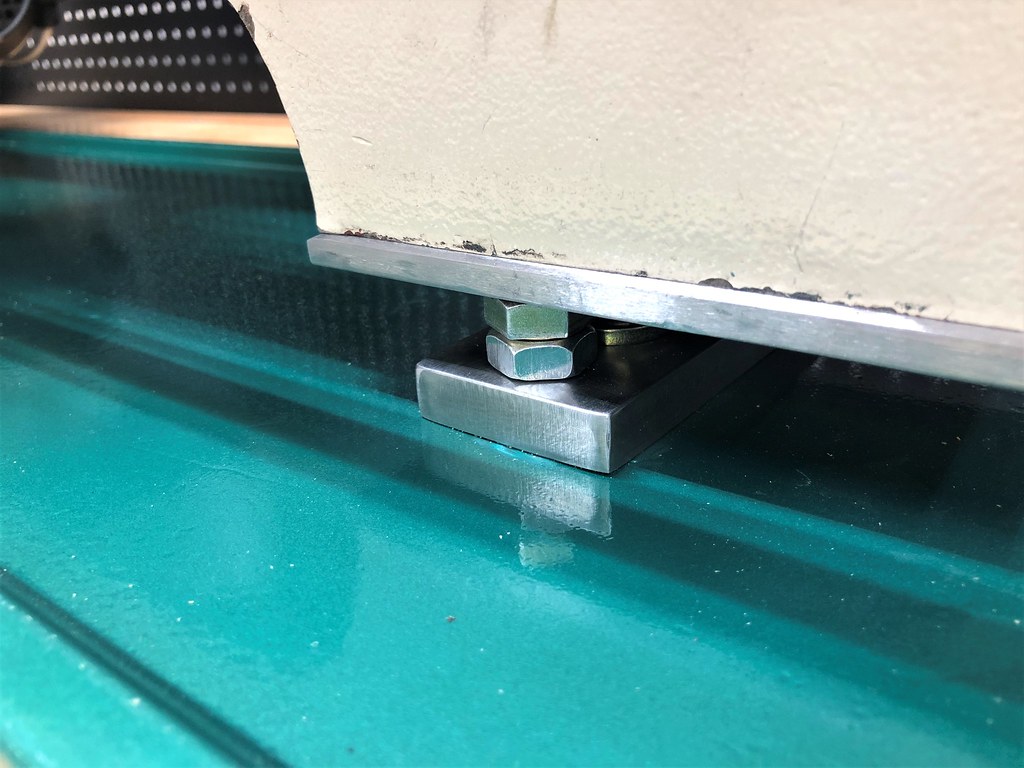
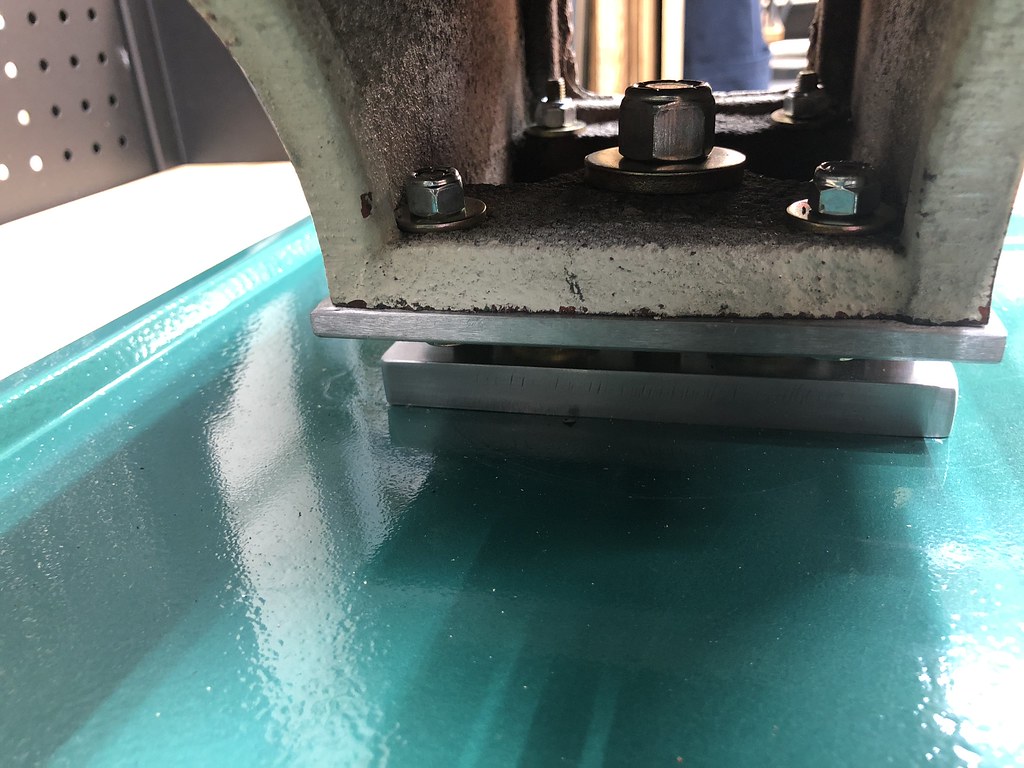
Once the lathe was placed on the bench I loosely installed the mounting bolts and began the leveling process. For me the only adjustment needed was to the rear leveling bolts so I locked down the front bolts and moved on with the process of adjusting. I began at the head stock. This is the first time I have ever done this and I was very much amazed at how little adjustment it took to make a huge difference. It is a must to use fine thread bolts for the levelers.
I used 123 blocks on the ways and a Mahr 12" machinist's level for this process.
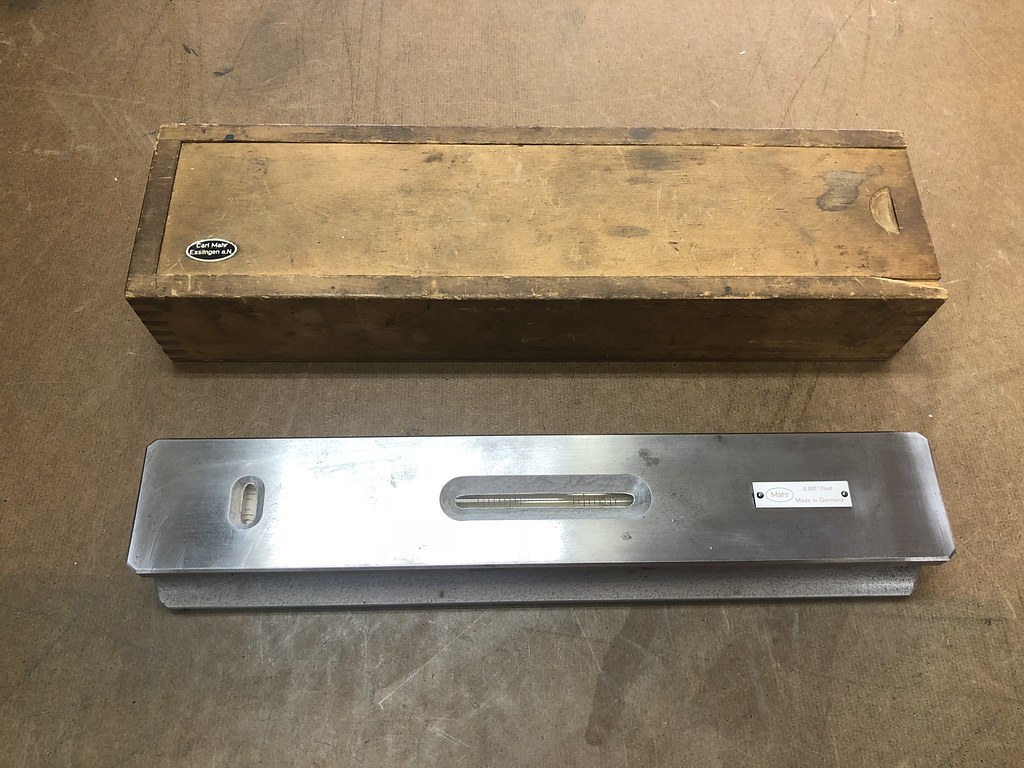
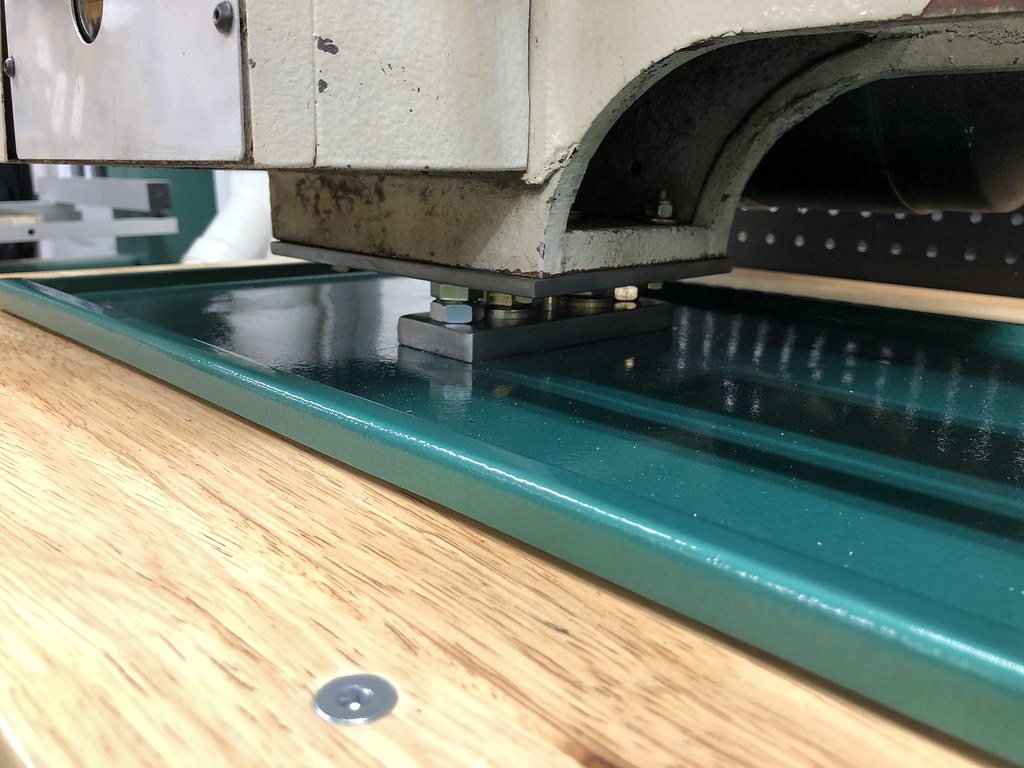
It only took a few minutes to get the head stock end perfectly level. I did figure out that once I get very close if I very lightly snugged the mounting bolt it helped me to see the very slight movements as I adjusted the lever.
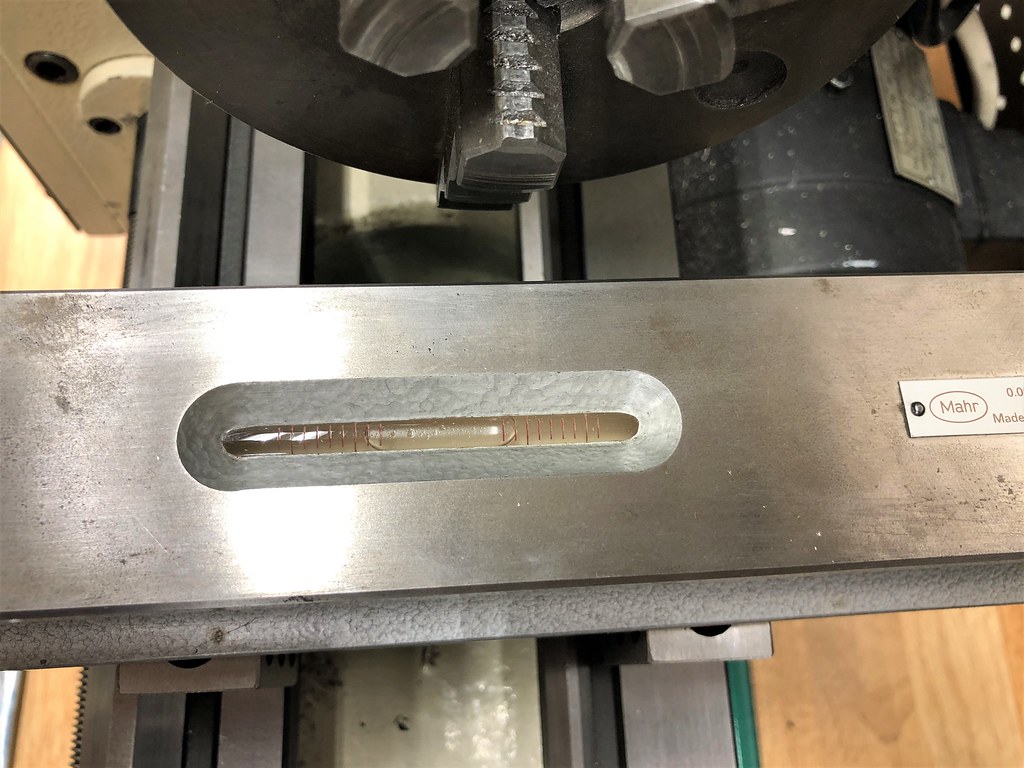
Moved to the tail stock end. Only a couple of minutes to get it perfectly in plane with the head stock.
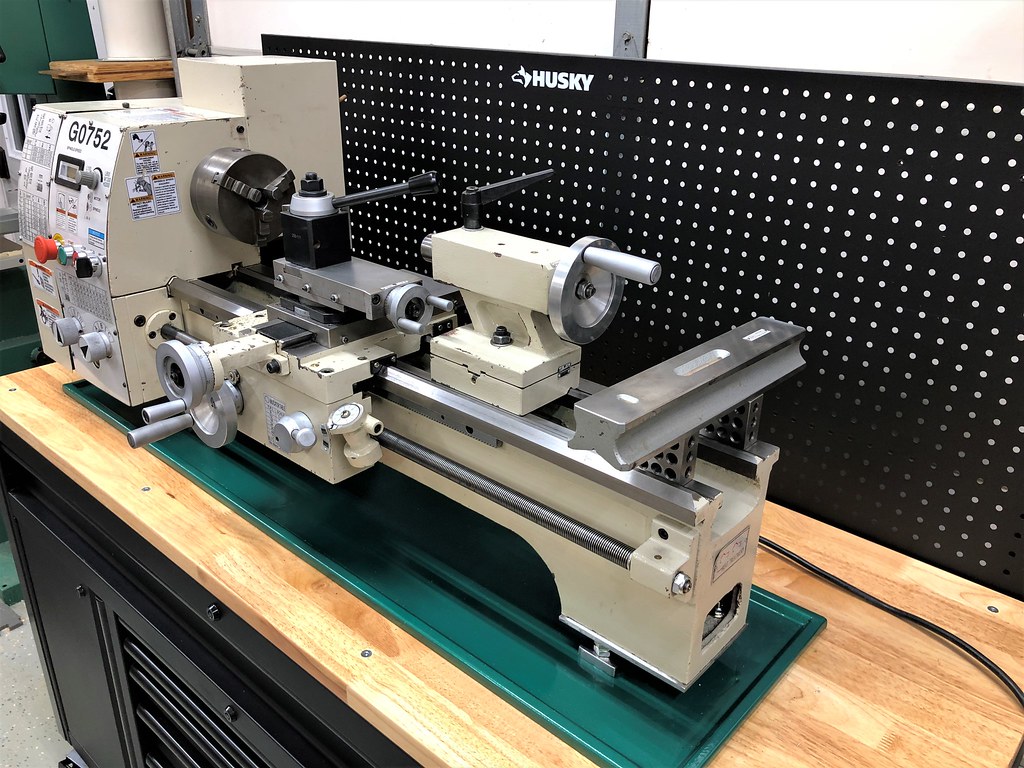
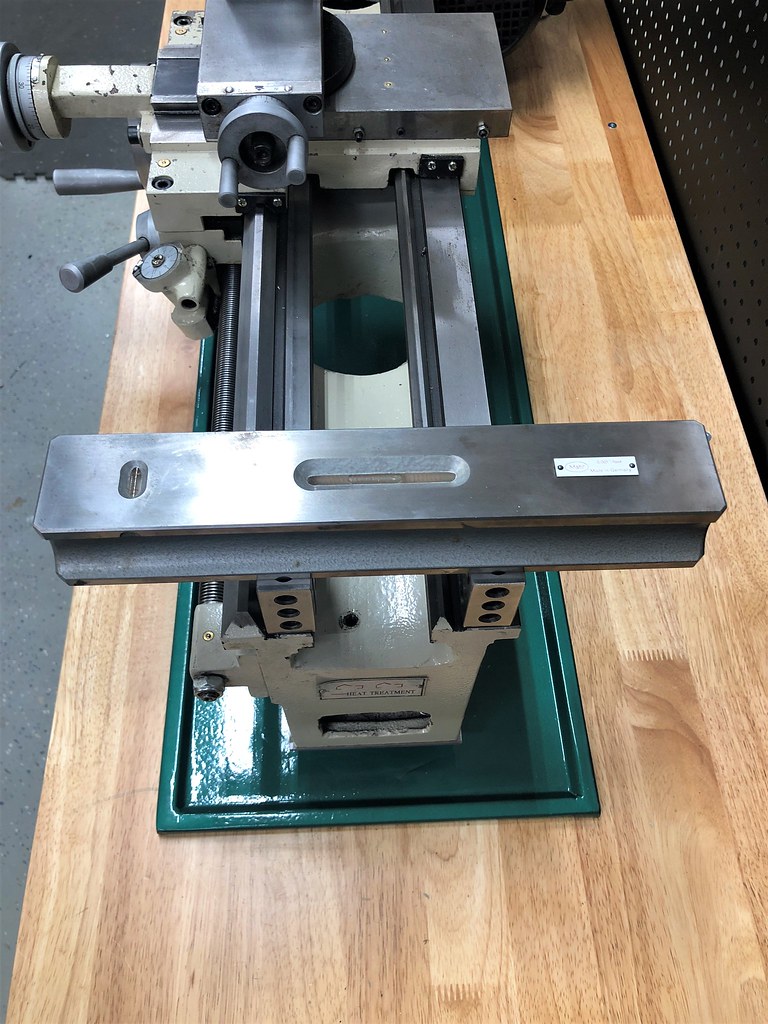
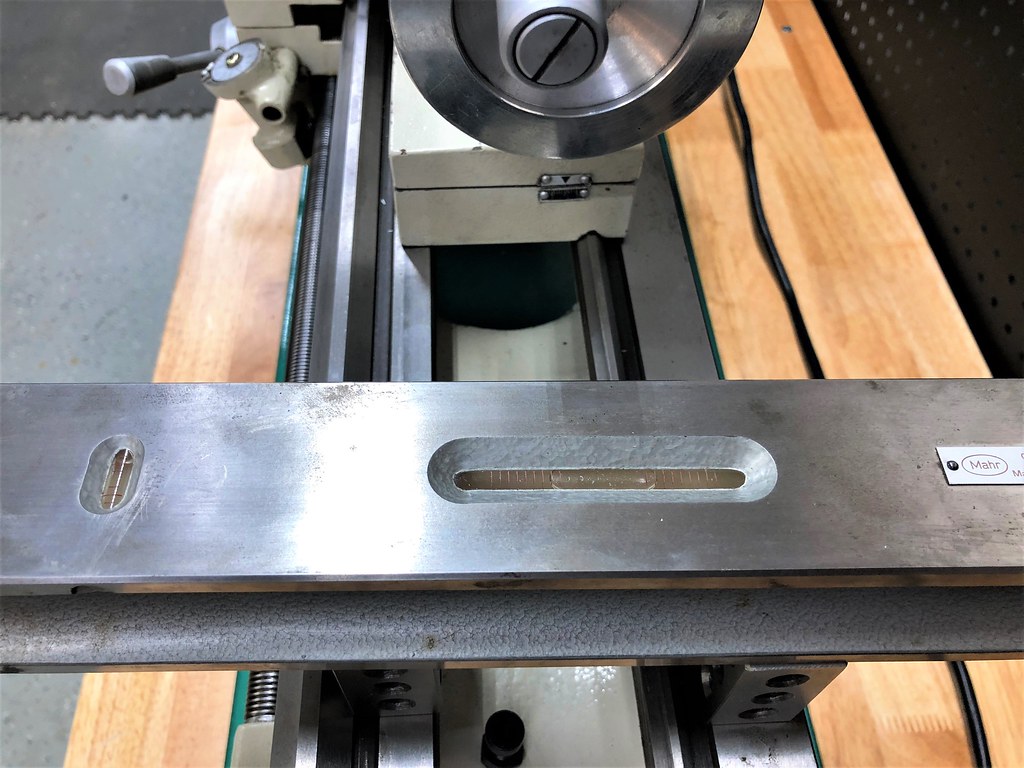
I also like the added height that the levelers make between the bed and the chip tray. Much more room to clean out the chips.
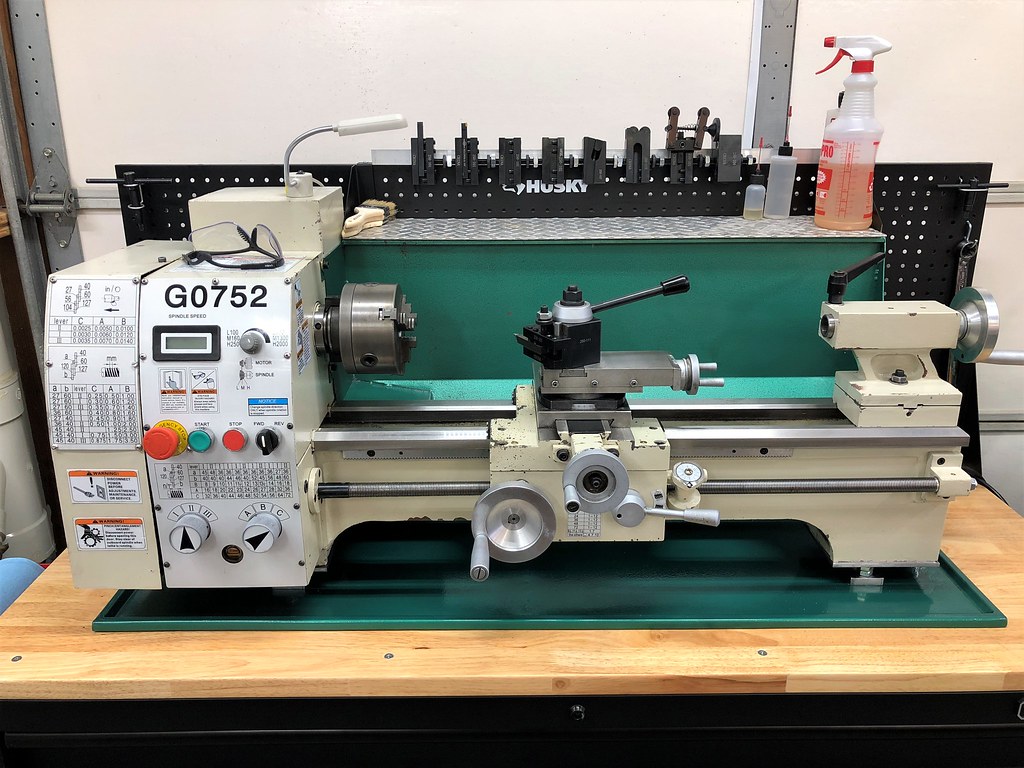
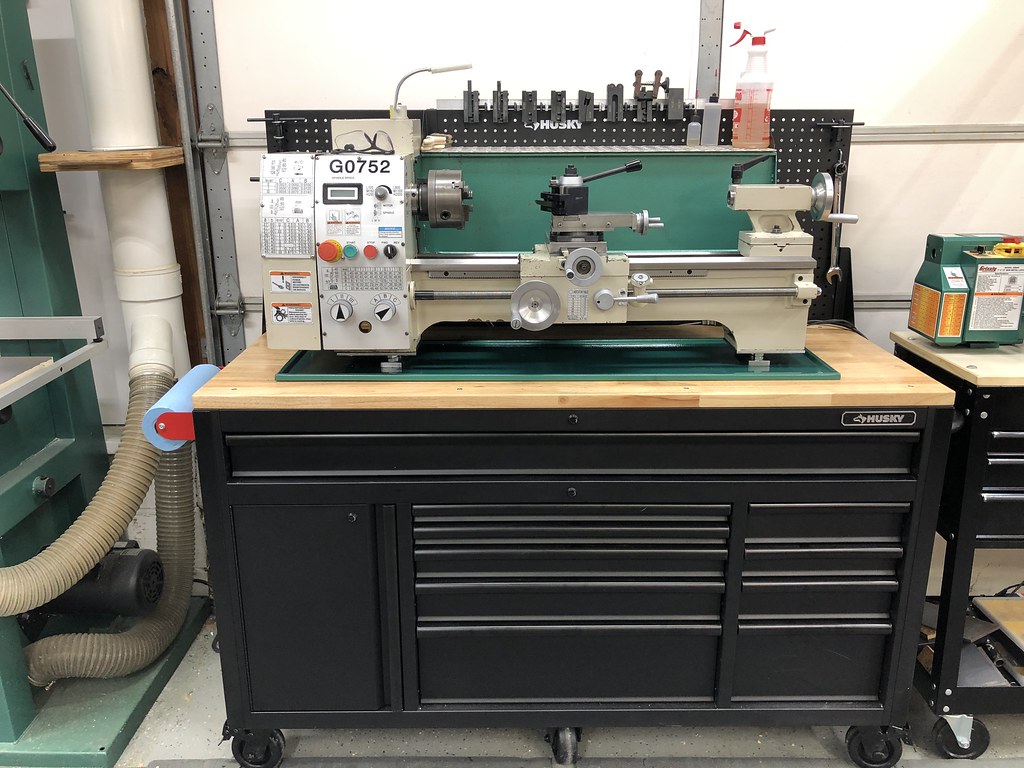
Thanks for looking and I hope this is helpful to someone.
Last edited: