- Joined
- Jul 6, 2022
- Messages
- 498
My Smart and Brown SAB has an MT3 spindle taper, so I just tried out a collet chuck in it to try holding some work in the collet chuck for the first time.
Out of interest, I wanted to see what the runout was at the collet. I can see no measurable runout on the inside of the spindle itself, but when I measure it in the collet chuck, I get about 0.08mm runout:
I’ve tried with three seperate collet chucks and they all get around the same runout. I’ve double and triple checked that the internal runout of the spindle, and I still see no movement at all:
I’ve checked the spindle runout at various depths to see if there was any burrs on the inside and I can find nothing.
So my question is this - is that runout at the end of the collet chuck expected?
Sent from my iPhone using Tapatalk
Out of interest, I wanted to see what the runout was at the collet. I can see no measurable runout on the inside of the spindle itself, but when I measure it in the collet chuck, I get about 0.08mm runout:
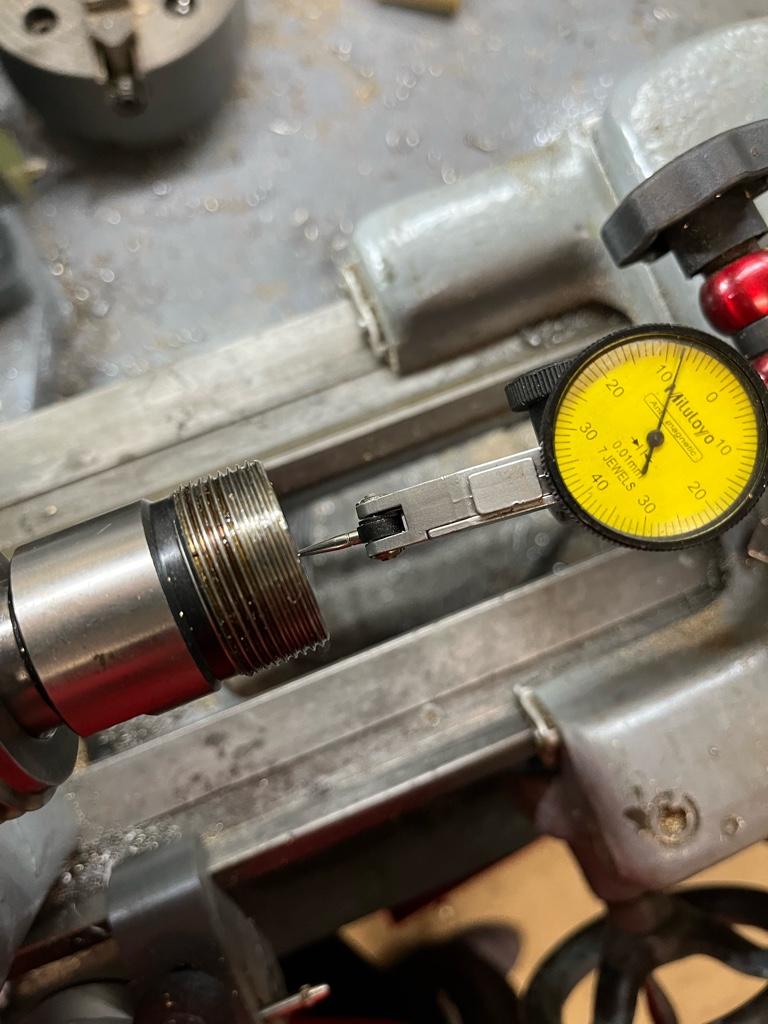
I’ve tried with three seperate collet chucks and they all get around the same runout. I’ve double and triple checked that the internal runout of the spindle, and I still see no movement at all:
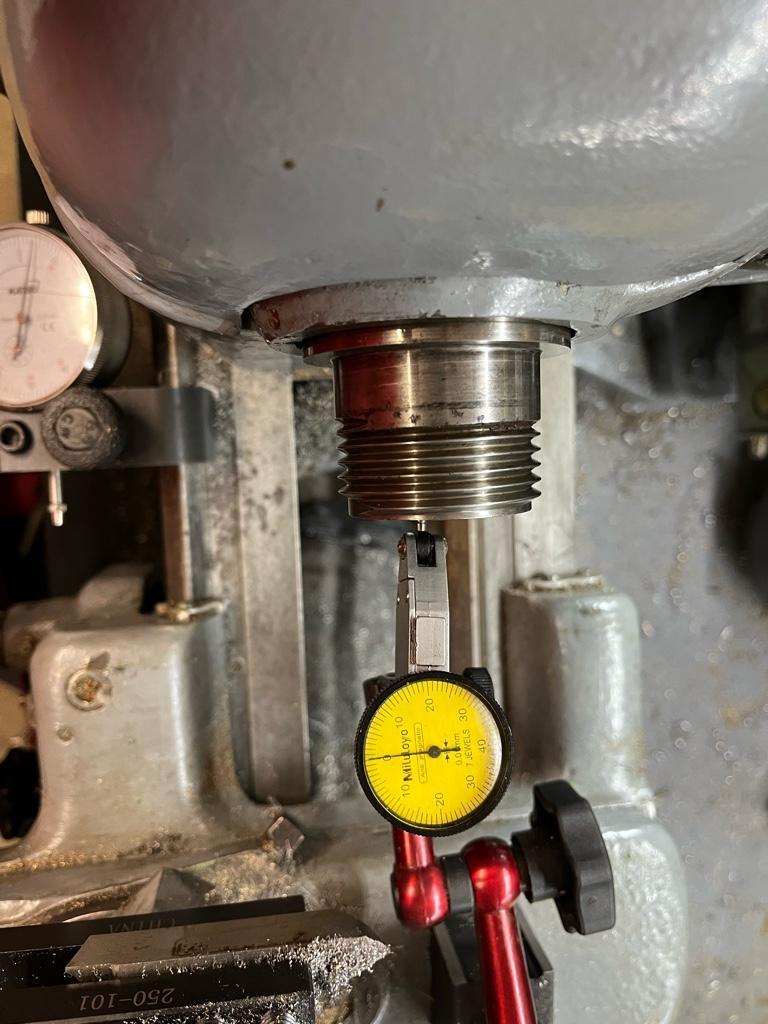
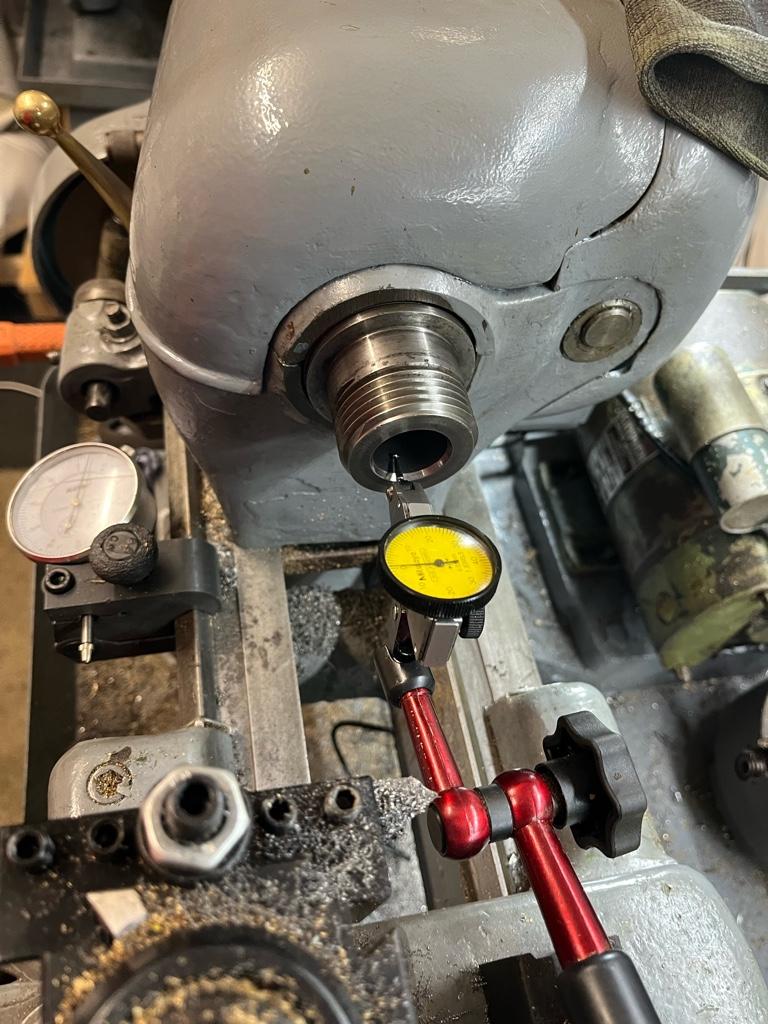
I’ve checked the spindle runout at various depths to see if there was any burrs on the inside and I can find nothing.
So my question is this - is that runout at the end of the collet chuck expected?
Sent from my iPhone using Tapatalk