- Joined
- Aug 22, 2012
- Messages
- 4,121
Rigidity is the key, since I removed the top slide and replaced it with a solid block
www.hobby-machinist.com
my 9x20 parts like a hot knife through butter.
I use "T" shaped HSS parting blades now, a quick touch up with a diamond hone before starting and cut as close to the chuck as possible.
Blade tip on dead centre, but I often just eyeball the blade at 90', sometimes I'm a bit out so the cut curves slightly but its never been a problem.
On large diameters I will start parting then withdraw and move over half the blade width and continue a bit deeper and keep swapping back and forth for faster chip clearance.
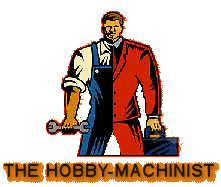
Plinth For Qctp On 9 X 20 Lathe
In my never ceasing search for more rigidity in my lathe I decided to make a plinth for the qctp. In its normal configuration I can often see the complete top slide assembly flex slightly. (I think I punish my lathe a bit) After seeing Bill G's plinth I felt it was time to go. I forgot to take...
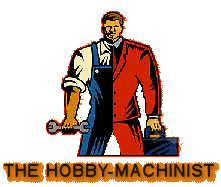
I use "T" shaped HSS parting blades now, a quick touch up with a diamond hone before starting and cut as close to the chuck as possible.
Blade tip on dead centre, but I often just eyeball the blade at 90', sometimes I'm a bit out so the cut curves slightly but its never been a problem.
On large diameters I will start parting then withdraw and move over half the blade width and continue a bit deeper and keep swapping back and forth for faster chip clearance.