- Joined
- Sep 22, 2018
- Messages
- 11
Has anyone adapted a Bridgeport/knee mill style power feed to their RF-30 or RF-31 mill? All of the power feeds I see for these look like they have some flaws I'd like to avoid putting on my mill. Plus, they are typically 2-3 times more expensive for some reason, even though they use the same motors as the other power feed/drive units.
Basically, I want to put one of these:
On this:
www.grizzly.com
Basically, I want to put one of these:
Mophorn Power Feed Al-310S X-Axis Torque 450 in-lb Power Feed Milling Machine 200PRM Power Table Feed Mill Fits Bridgeport Acer (450 in-lb X-Axis Torque) - - Amazon.com
Mophorn Power Feed Al-310S X-Axis Torque 450 in-lb Power Feed Milling Machine 200PRM Power Table Feed Mill Fits Bridgeport Acer (450 in-lb X-Axis Torque) - - Amazon.com
www.amazon.com
On this:
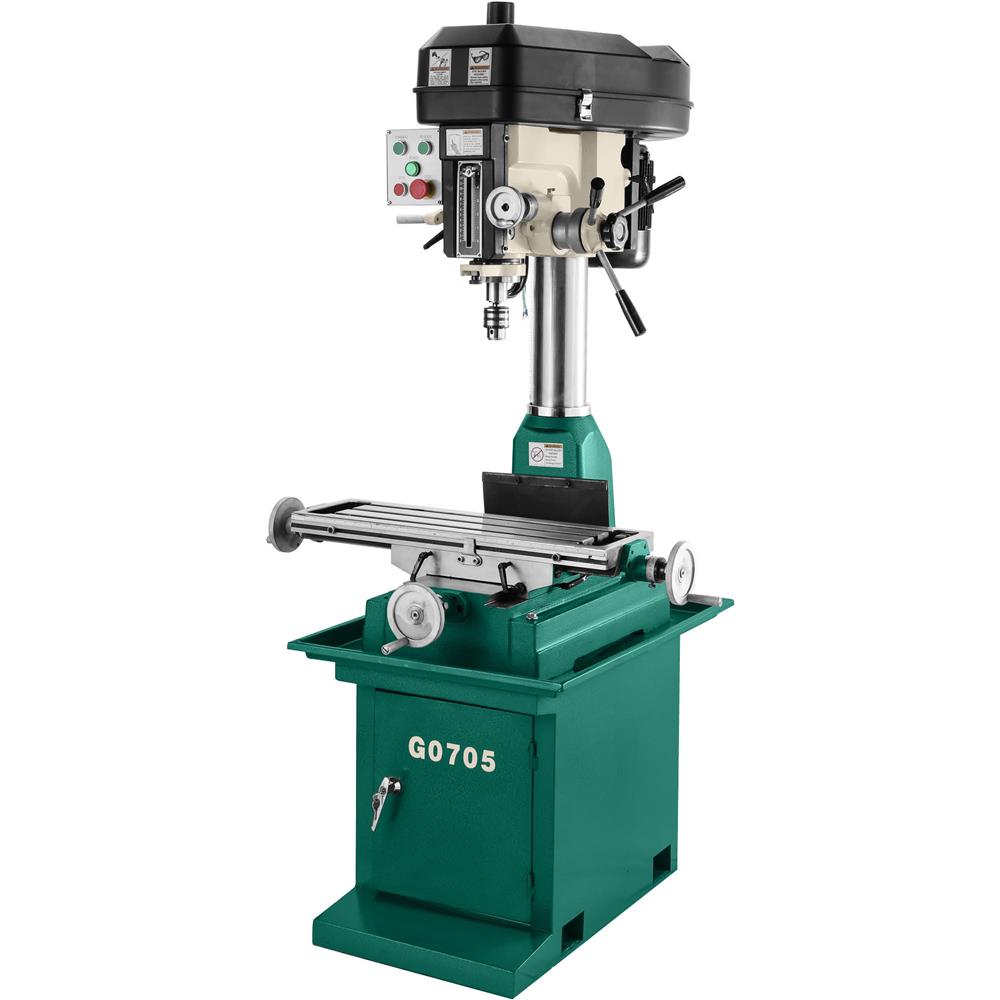
8" x 29" 2 HP Mill/Drill with Stand
<h1>G0705 8" x 29" 2 HP Mill/Drill with Stand</h1> <h2>A competitively priced mill worthy of being the cornerstone of your shop.</h2> <p>The G0705 8" x 29" 2 HP Mill/Drill has a 2 HP motor and enough table space to make quick work of just about any machining job you can throw at it.</p> <p>The...