- Joined
- Apr 8, 2021
- Messages
- 155
Hello.
Here in Spain the offer of tools is not very wide, so things like bottoming taps are hard to find. So I usually cut the point of my taps with the angular grinder to make the threads until almost the bottom of the hole (putting oil during the cut to prevent overheating). Buuuuut this time I cut to much and the 3rd tap can't start the thread. So my question is, Is there a way to shorten the taps or only the rule is not to short them too much?
I tried to smooth the point of this tap and it hasn´t work. My question is not to fix it but to prevent this in the future.
thank you
best regards!
EDIT: I forgot the picture!
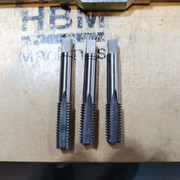
Here in Spain the offer of tools is not very wide, so things like bottoming taps are hard to find. So I usually cut the point of my taps with the angular grinder to make the threads until almost the bottom of the hole (putting oil during the cut to prevent overheating). Buuuuut this time I cut to much and the 3rd tap can't start the thread. So my question is, Is there a way to shorten the taps or only the rule is not to short them too much?
I tried to smooth the point of this tap and it hasn´t work. My question is not to fix it but to prevent this in the future.
thank you
best regards!
EDIT: I forgot the picture!
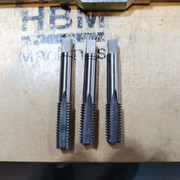
Last edited: