- Joined
- Mar 2, 2021
- Messages
- 84
I finally got around to making myself a “bumper style” squareness comparator.
I machined it out of a piece of 4140 round bar (it’s the only tool steel I had lying around). First step was to machine the round bar into a rectangular prism.
Once squared up in the mill, I ground the faces on the surface grinder, and proceeded to mill away material to create the the “L” shape. I drilled, chamfered and tapped two holes for 1/4-20 threads to attach to the 2”
face of a 1-2-3 block.
I machined the radius on my small rotary table, taking a cue from Stefan’s video where he uses a gage block against a pin in the center of the rotary table to set the radius distance. I machined the radius and added a very generous chamfer to the top edge. Then a thorough debur pass and the machining work was done!
The bumper is shorter than the 1” face, so I used a 0.005” gage block on the surface plate to set the offset (so the bumper floats above the surface plate) and bolted the bumper on to the 1-2-3 block with some 3.25” 1/4-20 bolts. I completed the comparator with a Noga magnetic indicator stand and a 0.00005” DTI.
It works super nice! Previously, I was checking squareness with steel Starrett try squares, a number 3020 for kicking around the shop and a number 20 for “special occasions”.
For those that aren’t familiar with these types of squareness comparators, you butt the bumper against a known square object, adjust the indicator to also touch and rotate back and forth looking for the high spot on the indicator. After zeroing out the indicator on the high spot, you repeat the process on the part to test, and the high spot found there indicates the relative squareness of the part.
Testing random stuff lying on the bench and I’m kind of amazed that I had got this Windy Hill Foundry casting machined square to within 0.0002”! I guess my mill tram jobs aren’t total trash after all, lols.
Testing another project in progress and…not so square. I’m pretty sure the culprit is not deburring well enough before putting it on the surface grinder. Yikes.
I’m pretty excited about to have this comparator, since I can grind in shims to fix squareness and using this tool, now I know just how much to grind!
Very satisfying afternoon project!
I machined it out of a piece of 4140 round bar (it’s the only tool steel I had lying around). First step was to machine the round bar into a rectangular prism.
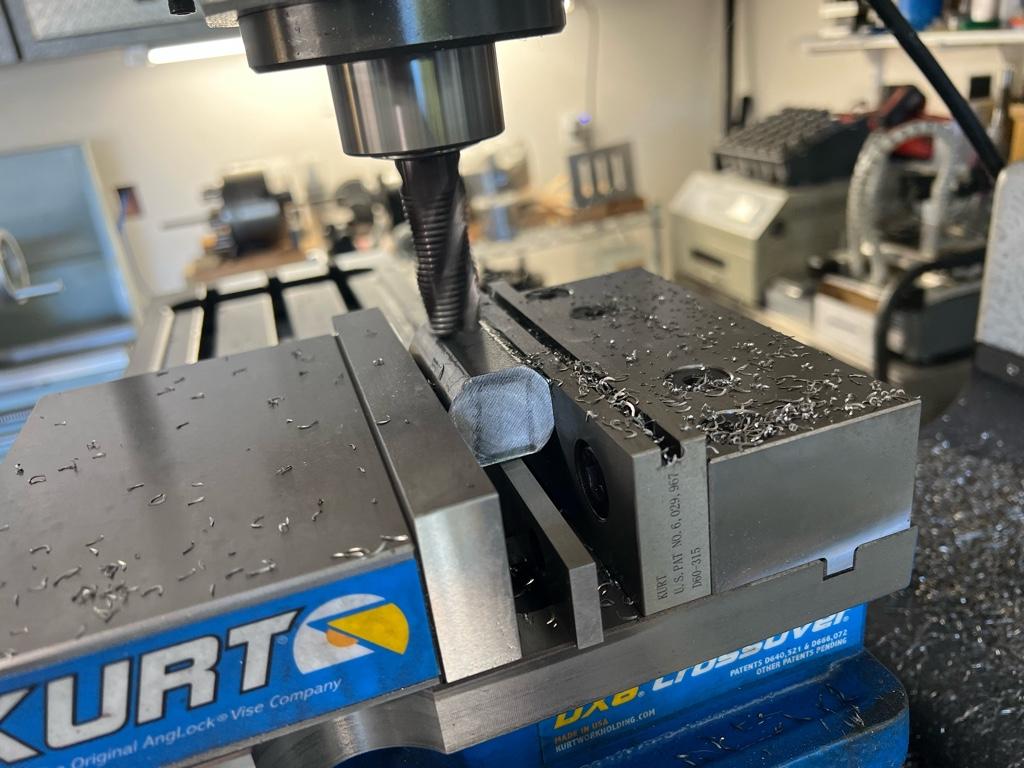
Once squared up in the mill, I ground the faces on the surface grinder, and proceeded to mill away material to create the the “L” shape. I drilled, chamfered and tapped two holes for 1/4-20 threads to attach to the 2”
face of a 1-2-3 block.
I machined the radius on my small rotary table, taking a cue from Stefan’s video where he uses a gage block against a pin in the center of the rotary table to set the radius distance. I machined the radius and added a very generous chamfer to the top edge. Then a thorough debur pass and the machining work was done!
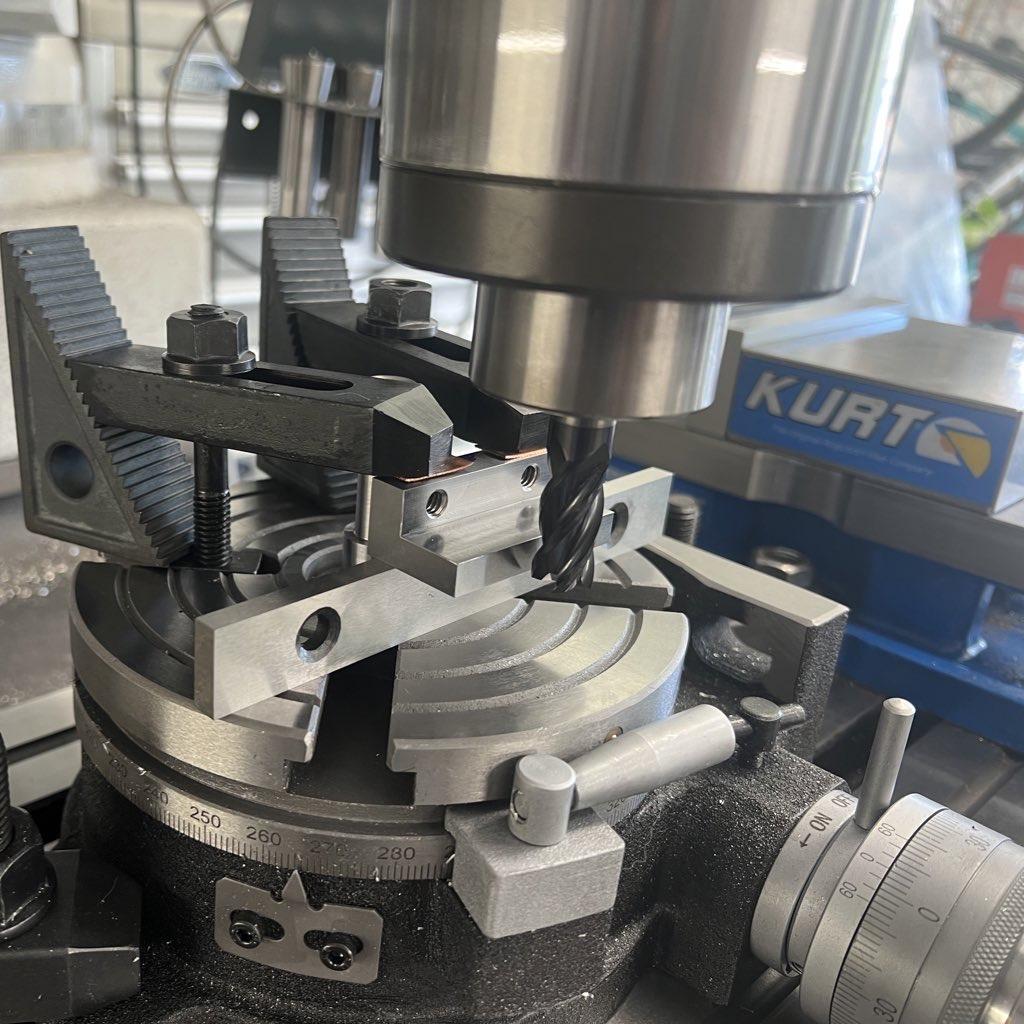
The bumper is shorter than the 1” face, so I used a 0.005” gage block on the surface plate to set the offset (so the bumper floats above the surface plate) and bolted the bumper on to the 1-2-3 block with some 3.25” 1/4-20 bolts. I completed the comparator with a Noga magnetic indicator stand and a 0.00005” DTI.
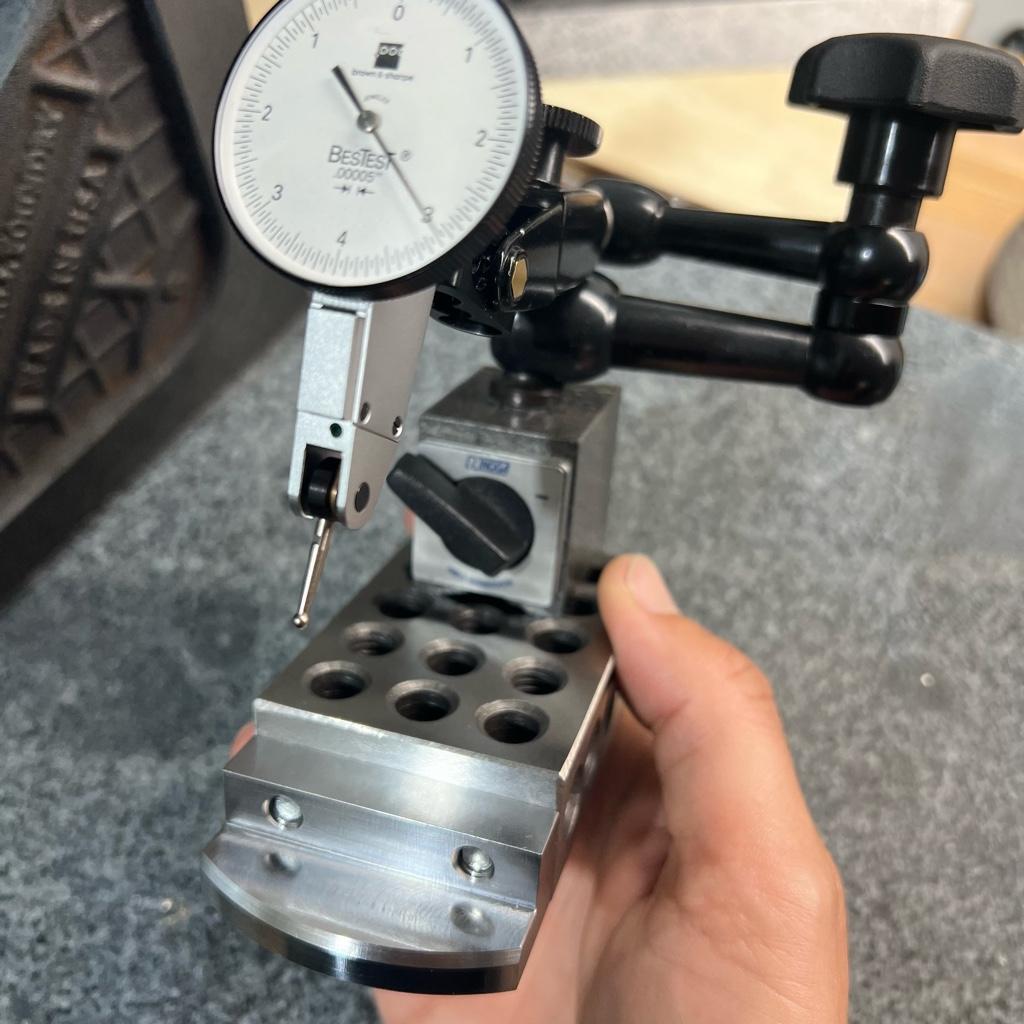
It works super nice! Previously, I was checking squareness with steel Starrett try squares, a number 3020 for kicking around the shop and a number 20 for “special occasions”.
For those that aren’t familiar with these types of squareness comparators, you butt the bumper against a known square object, adjust the indicator to also touch and rotate back and forth looking for the high spot on the indicator. After zeroing out the indicator on the high spot, you repeat the process on the part to test, and the high spot found there indicates the relative squareness of the part.
Testing random stuff lying on the bench and I’m kind of amazed that I had got this Windy Hill Foundry casting machined square to within 0.0002”! I guess my mill tram jobs aren’t total trash after all, lols.
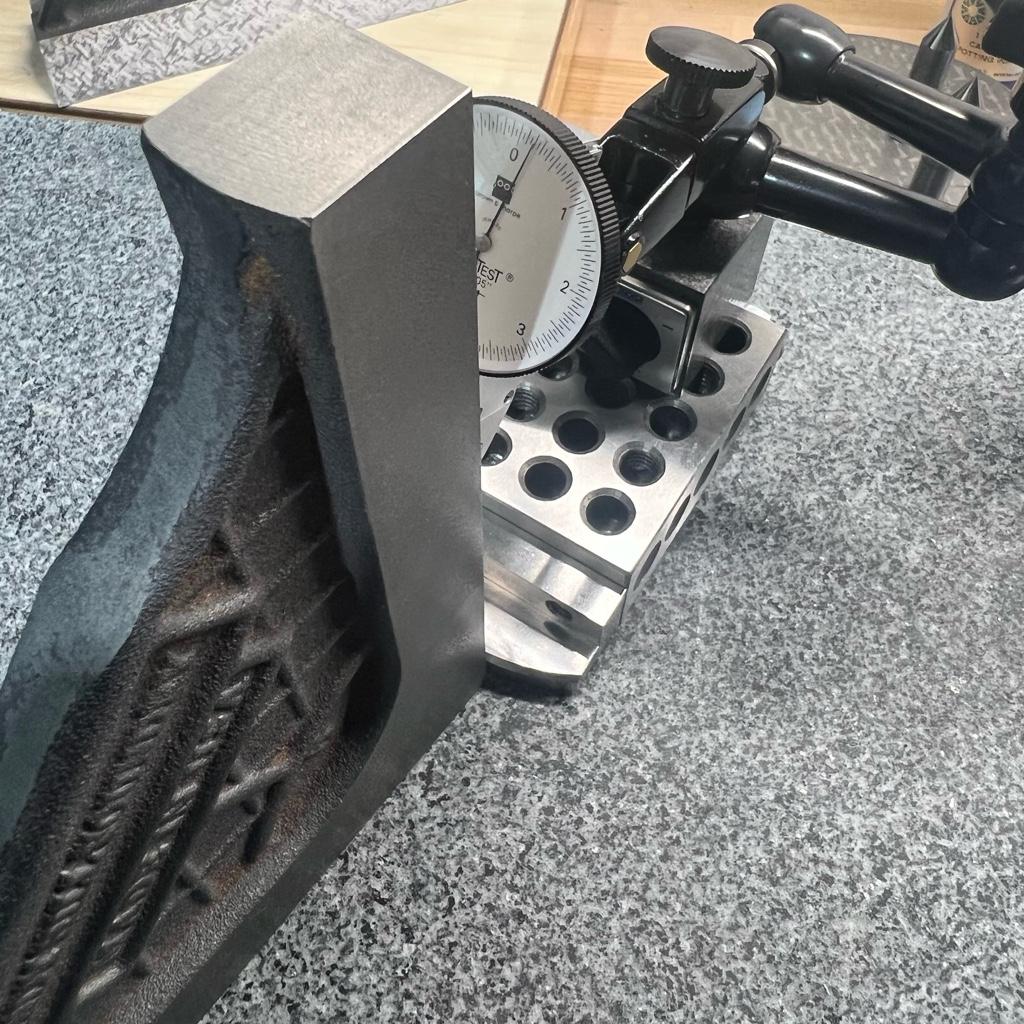
Testing another project in progress and…not so square. I’m pretty sure the culprit is not deburring well enough before putting it on the surface grinder. Yikes.
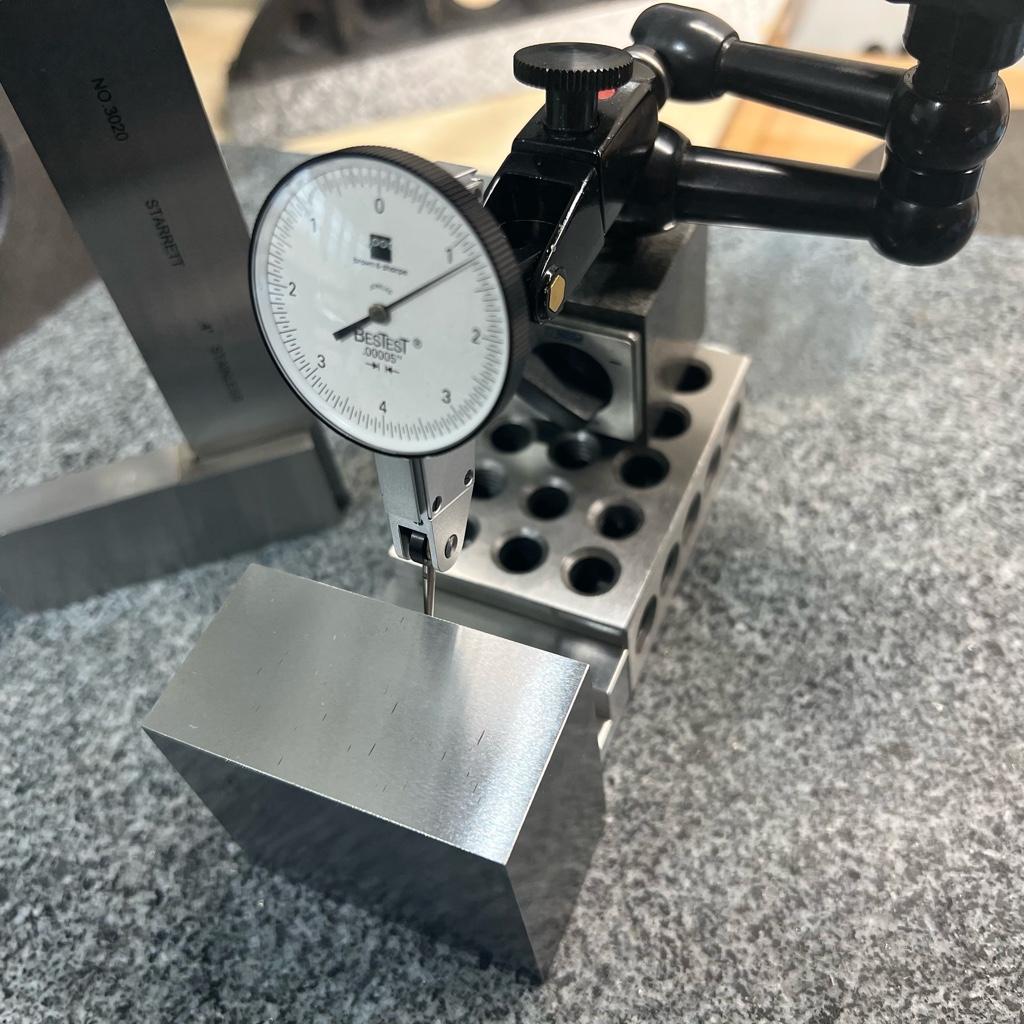
I’m pretty excited about to have this comparator, since I can grind in shims to fix squareness and using this tool, now I know just how much to grind!
Very satisfying afternoon project!
Last edited: