Hello
I have recently found this forum and I’ve been posting a bit on the beginners forum. I’m fairly new to machining and this is my first forum 1 silencer. I’m working on turning the baffles and I have run into a problem. I plan on making these baffles in the following order.
1-Drill the Bore
2-Profile inside of cone
3-Profile outside of cone
4-Part off cone
The soon to be baffle has been clamped in the 3 jaw since step 1 to ensure concentricity. The first blast has been drilled and bored to correct ID. I was originally planning on using a boring bar to profile the inside 60° cone but that would be hard to reach that deep into the baffle when it has a longer skirt. So I got a 1” 60° countersink, I’ve started cutting a little bit with the countersink but I have no way to tell my correct depth and it should be precise otherwise i won’t get the desired .06” thick cone. If there are any forum 1 builders that could lend some suggestions would be appreciated.
I have recently found this forum and I’ve been posting a bit on the beginners forum. I’m fairly new to machining and this is my first forum 1 silencer. I’m working on turning the baffles and I have run into a problem. I plan on making these baffles in the following order.
1-Drill the Bore
2-Profile inside of cone
3-Profile outside of cone
4-Part off cone
The soon to be baffle has been clamped in the 3 jaw since step 1 to ensure concentricity. The first blast has been drilled and bored to correct ID. I was originally planning on using a boring bar to profile the inside 60° cone but that would be hard to reach that deep into the baffle when it has a longer skirt. So I got a 1” 60° countersink, I’ve started cutting a little bit with the countersink but I have no way to tell my correct depth and it should be precise otherwise i won’t get the desired .06” thick cone. If there are any forum 1 builders that could lend some suggestions would be appreciated.
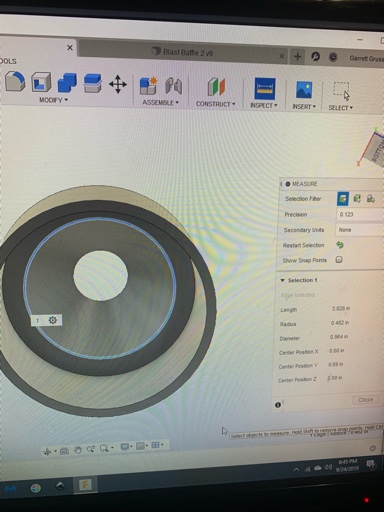
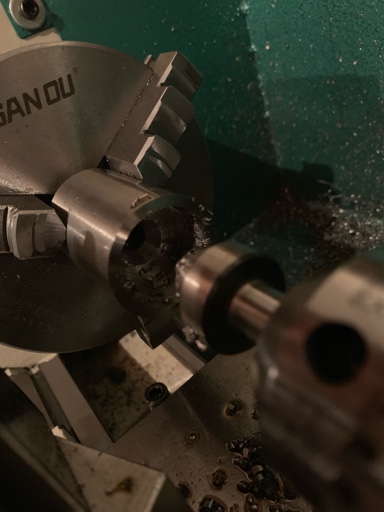