H
Hukshawn
Forum Guest
Register Today
I made an ER collet chuck for my lathe a while back, finally put it to an actual use today.
Apparently when I bored it out and turned it to size, I left nothing but a HAIR of metal left. I chucked up a piece of 3/4" bar, just TOUCHED the tool to the metal and *boink* just fell off... Can't win lately.
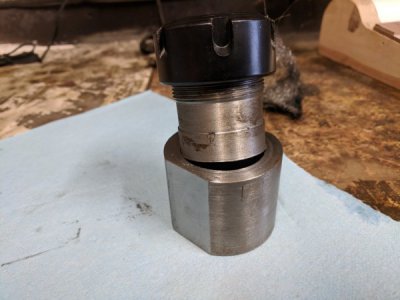
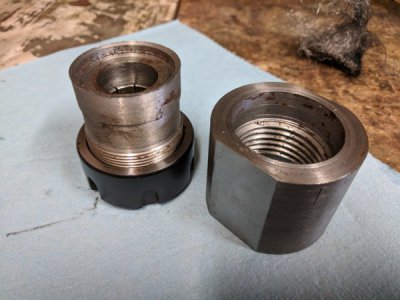
Apparently when I bored it out and turned it to size, I left nothing but a HAIR of metal left. I chucked up a piece of 3/4" bar, just TOUCHED the tool to the metal and *boink* just fell off... Can't win lately.
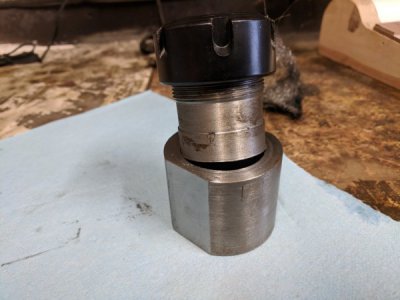
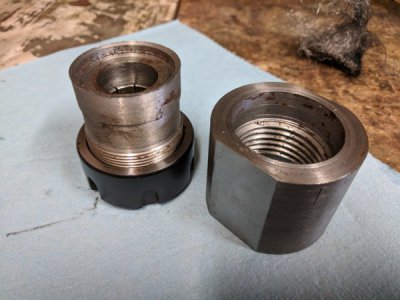