Hello all those with more experience threading on a lathe than I (probably everyone!) So the one thing I never took the time to learn or got around to was threading. Well now I have a project that needs to be threaded on the lathe so I thought I would try and learn finally. I ran my first real cutting test yesterday and the results are functional. It screws in well and is not a sloppy fit however it is not right at least I don’t think so. I was hoping you more experienced guys could help me diagnose the issues.
In the attached picture you see a 5/8” 11tpi end results and what you also see is the left half of the thread matches the angle of the cutting bit while the right side not so much. I had the compound set at 30 degrees validated with an external protractor and the cutting tool at 90 degrees to the work. So, was my feed to aggressive? Did I not have the right angle on my compound rest?
Thanks much!
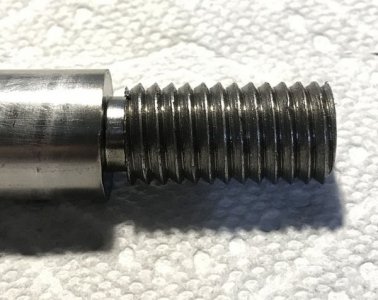
In the attached picture you see a 5/8” 11tpi end results and what you also see is the left half of the thread matches the angle of the cutting bit while the right side not so much. I had the compound set at 30 degrees validated with an external protractor and the cutting tool at 90 degrees to the work. So, was my feed to aggressive? Did I not have the right angle on my compound rest?
Thanks much!
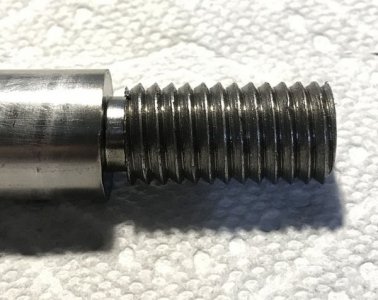