- Joined
- Oct 13, 2014
- Messages
- 6,703
I started down the same path as Mr Pete when I began my bandsaw conversion. The VFD alone wasn't enough to get down to the real slow speeds needed for cutting steel. I used a bolt on planetary-gear reducing pulley and replaced the direct drive motor with a shaft and step pulley arrangement. Works great, heres a link for anyone interested:
www.hobby-machinist.com
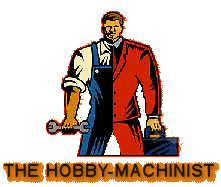
Bandsaw speed reducer build.
Hi All, I recently picked up a nice mid 50's vintage, Boice Crane, 14" vertical bandsaw. It has a three phase motor so I figured I'd simply throw a VFD on it and be able to get down to metal cutting speeds, wrong!... The motor is rated at 1150 rpm and running it at 15hz only gets the blade down...
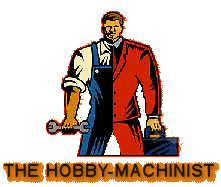