- Joined
- Feb 17, 2013
- Messages
- 336
The next morning I decided that installing the Z axis DRO scale would involve moving the knee full travel bottom to top at least a few times to measure scale alignment. After I did it once I decided to put a hold on the DRO install while I installed the Z axis power feed. It takes 90 rotations of the knee lift crank to go full travel and my shoulder was complaining after half travel. The power feed install threw a curve at me when the extension shaft would not engage the threads on the original shaft. After a bit of head scatching I realized the original shaft was too long and after careful measurements I cut off .600" to make it fit. It went smoothly from that point. I only needed one .010" shim to get the gear mesh set correctly.
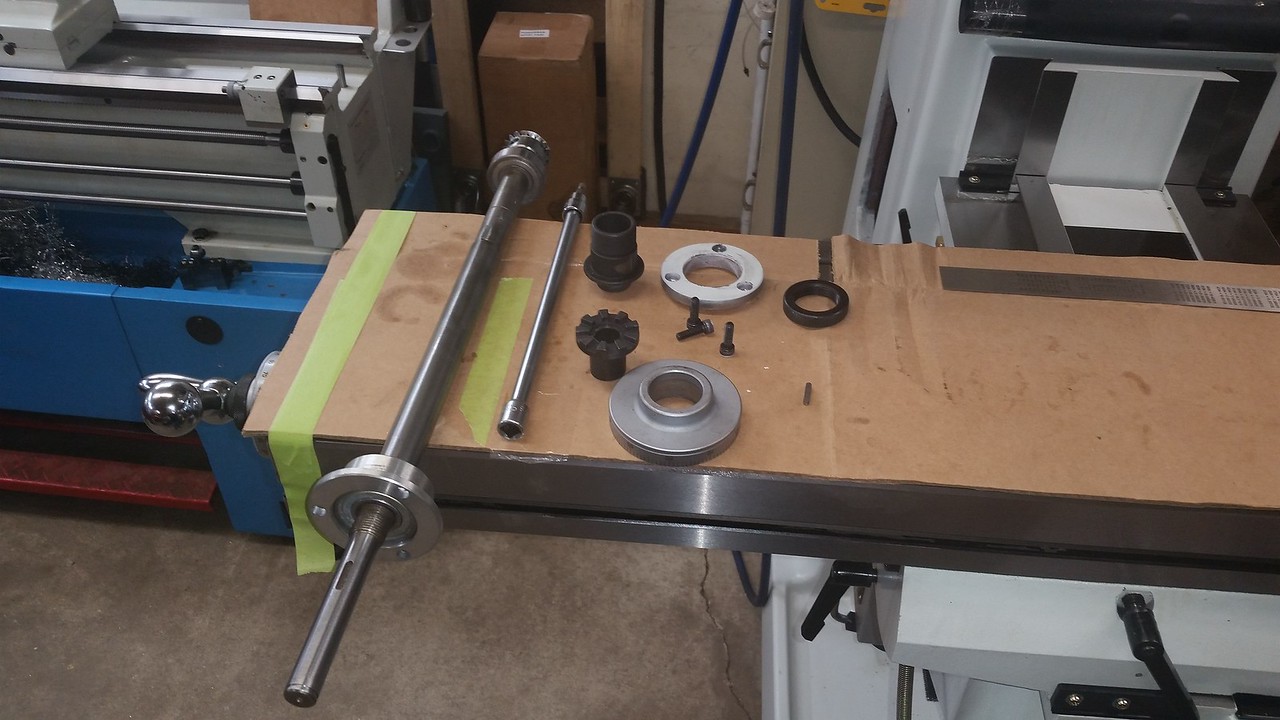
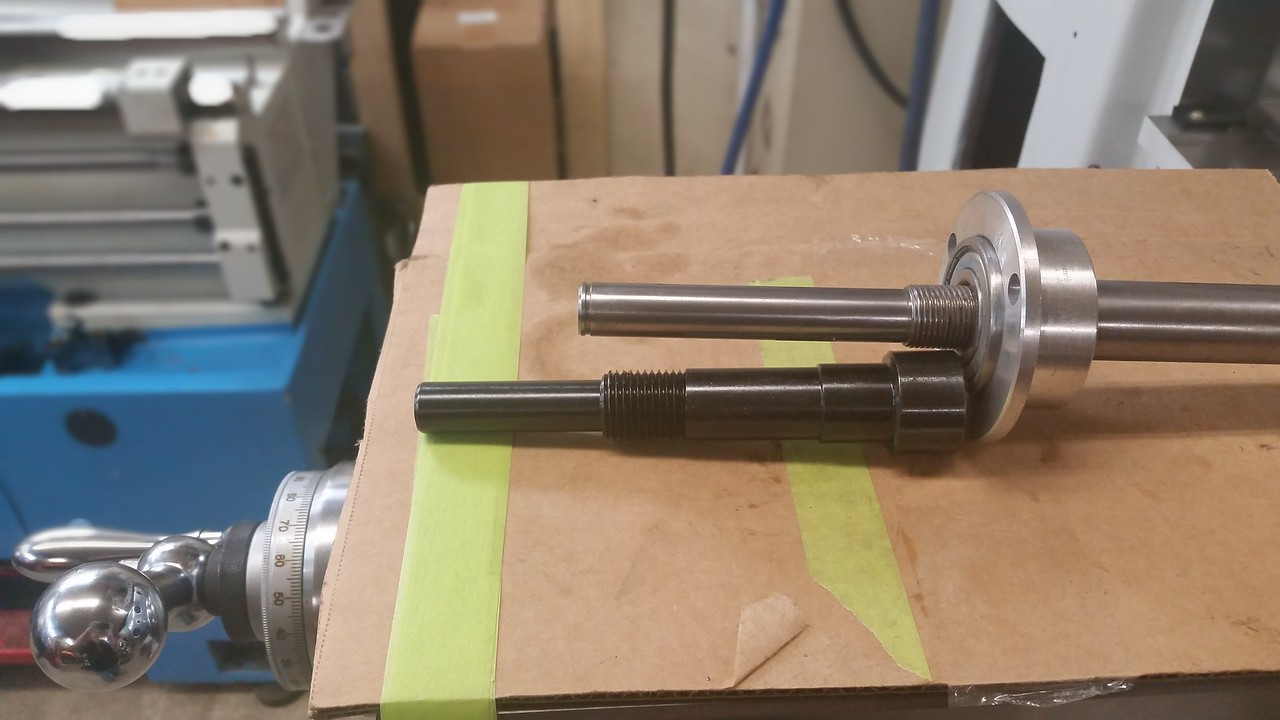
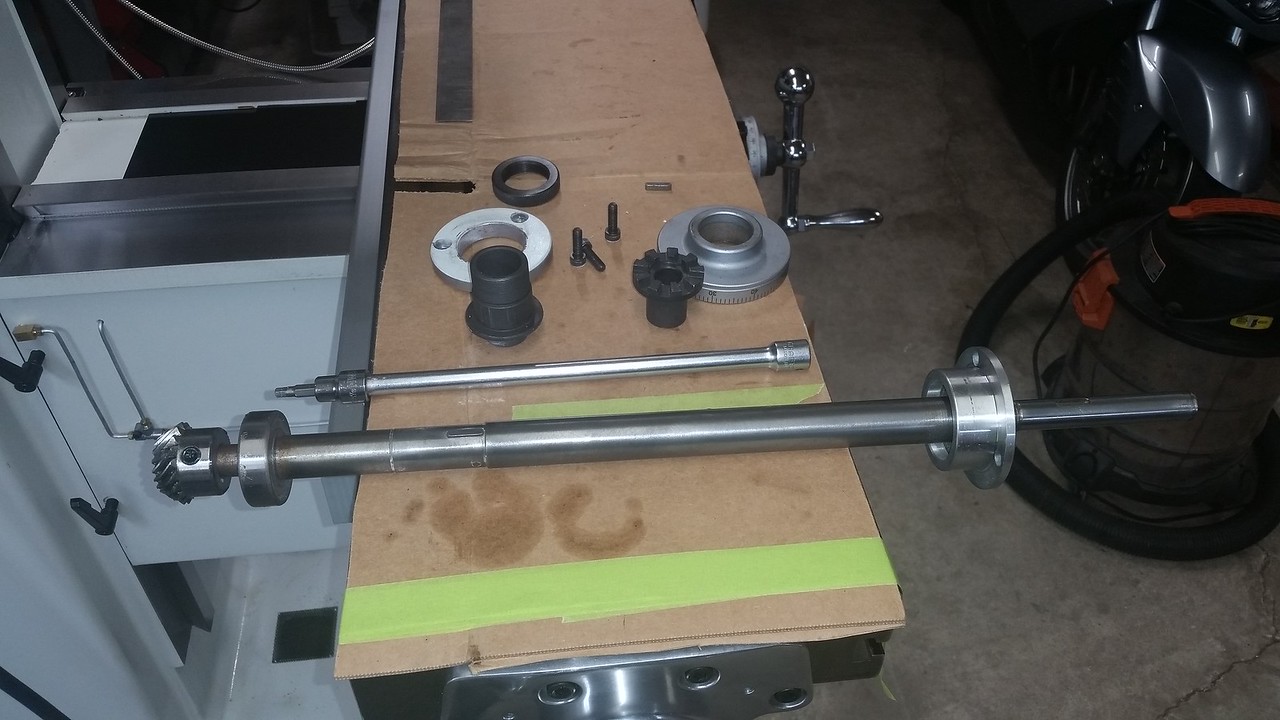
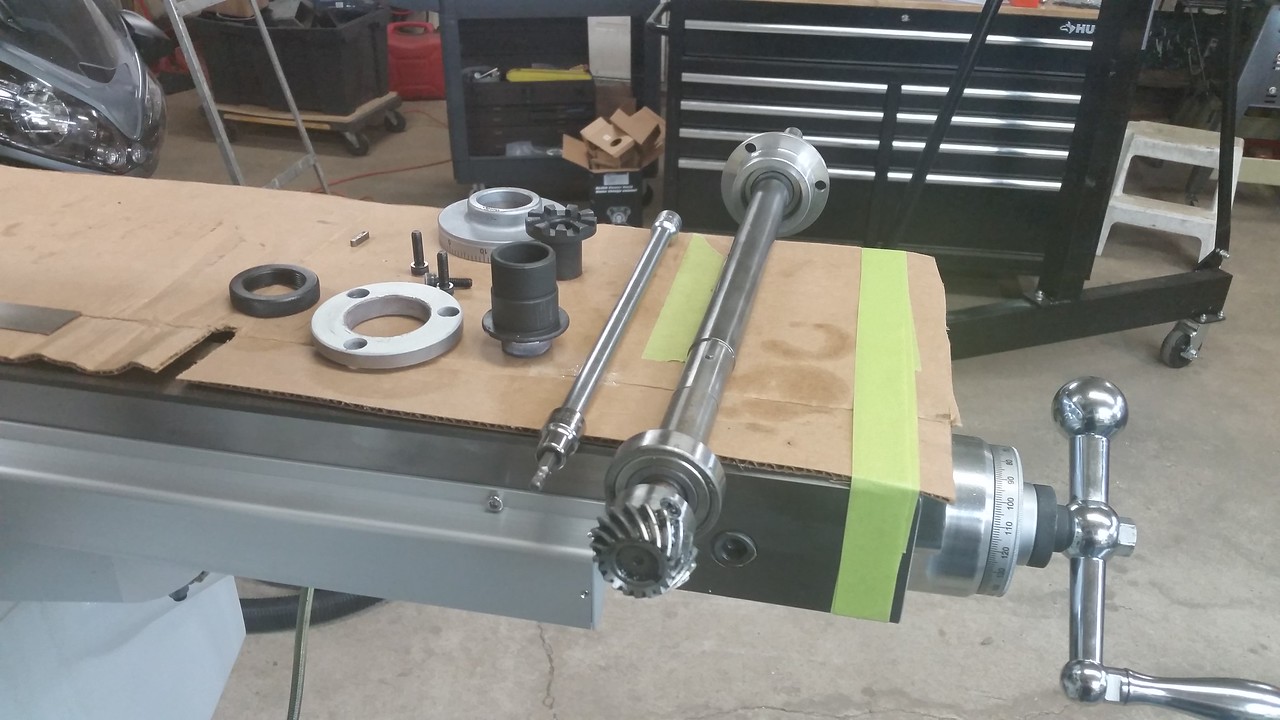
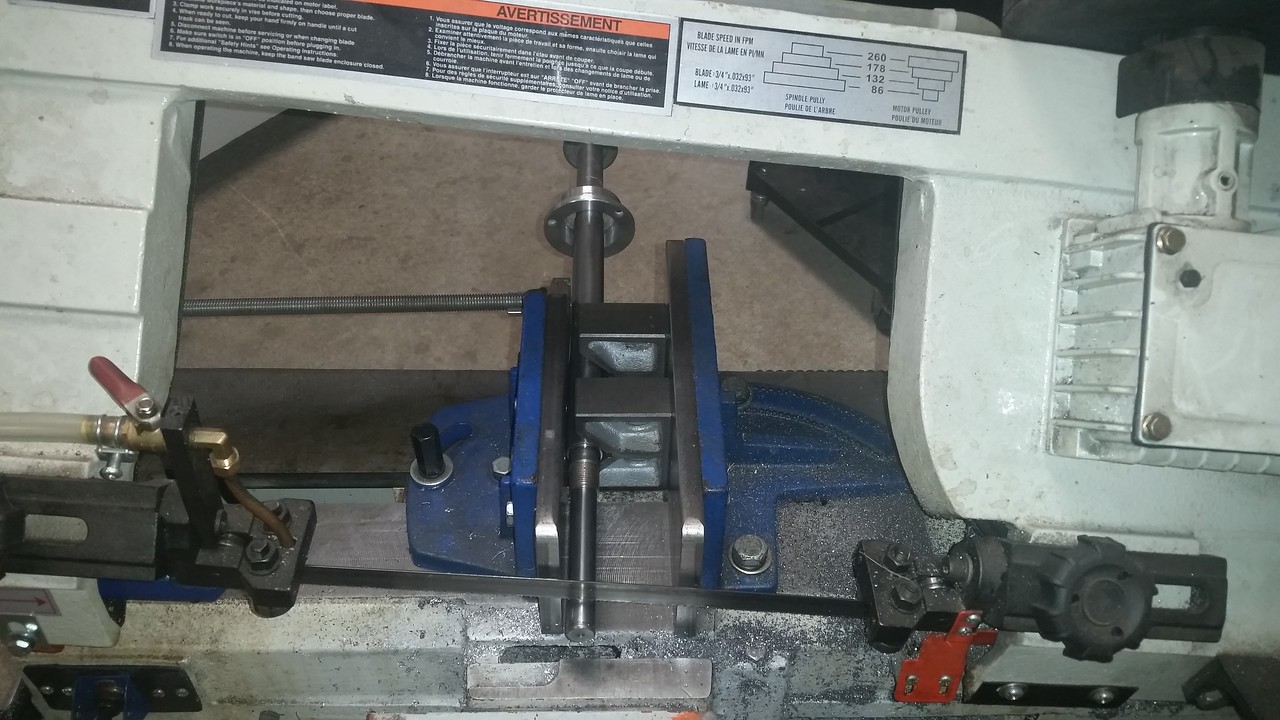
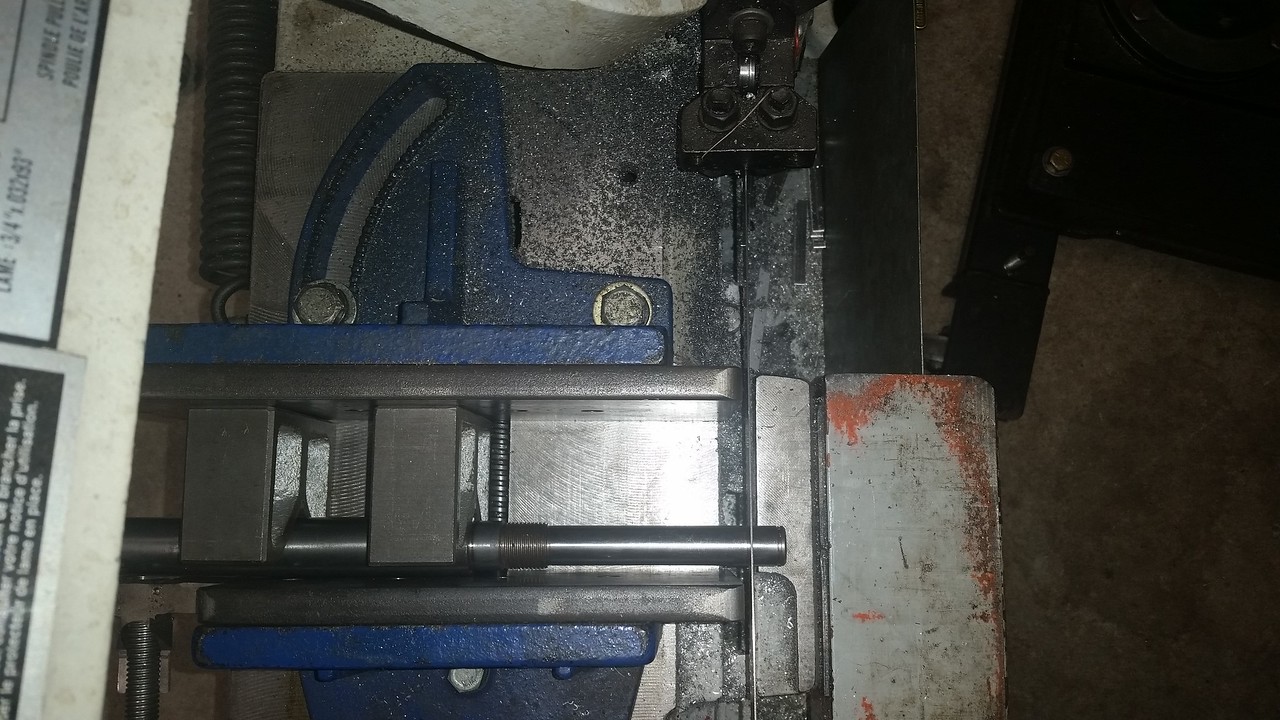

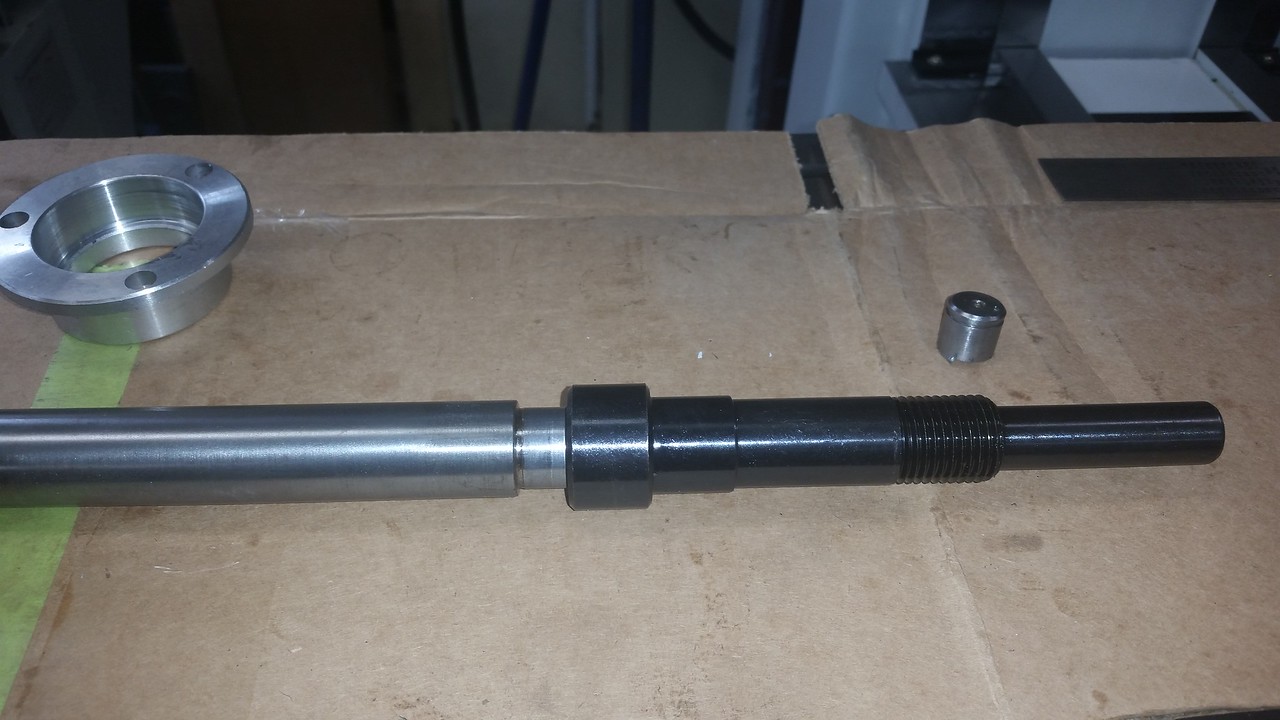
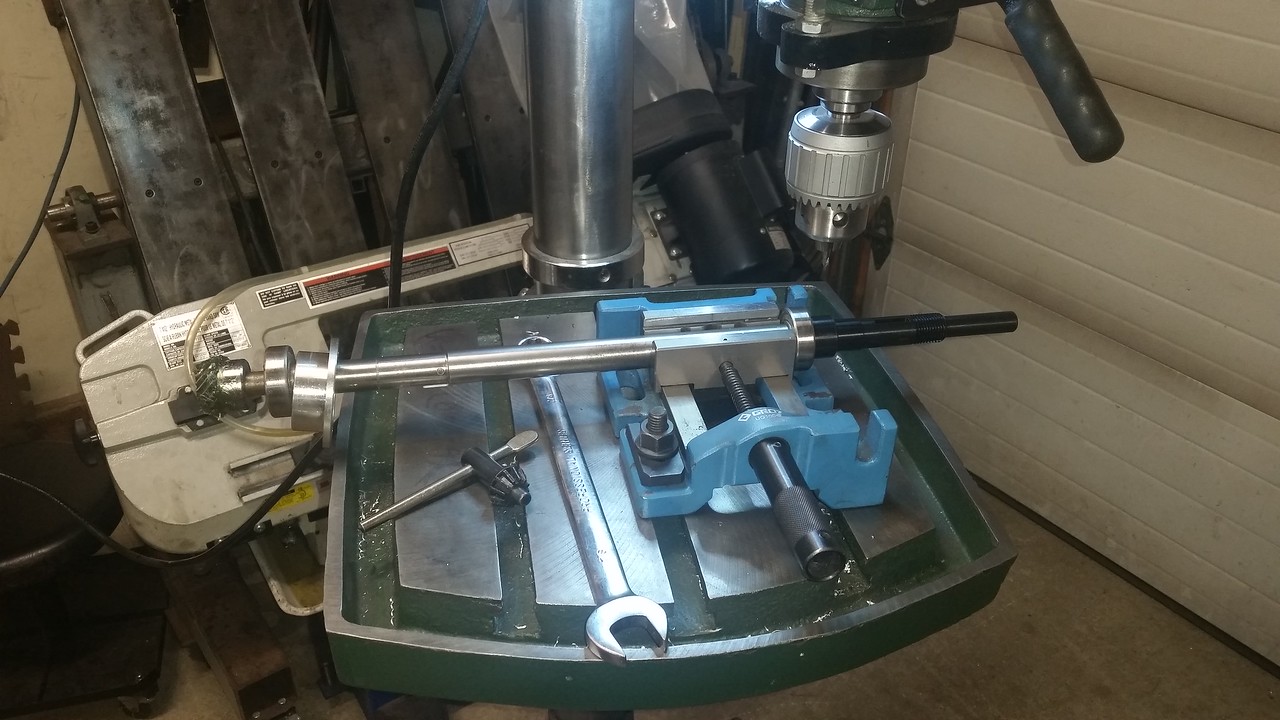

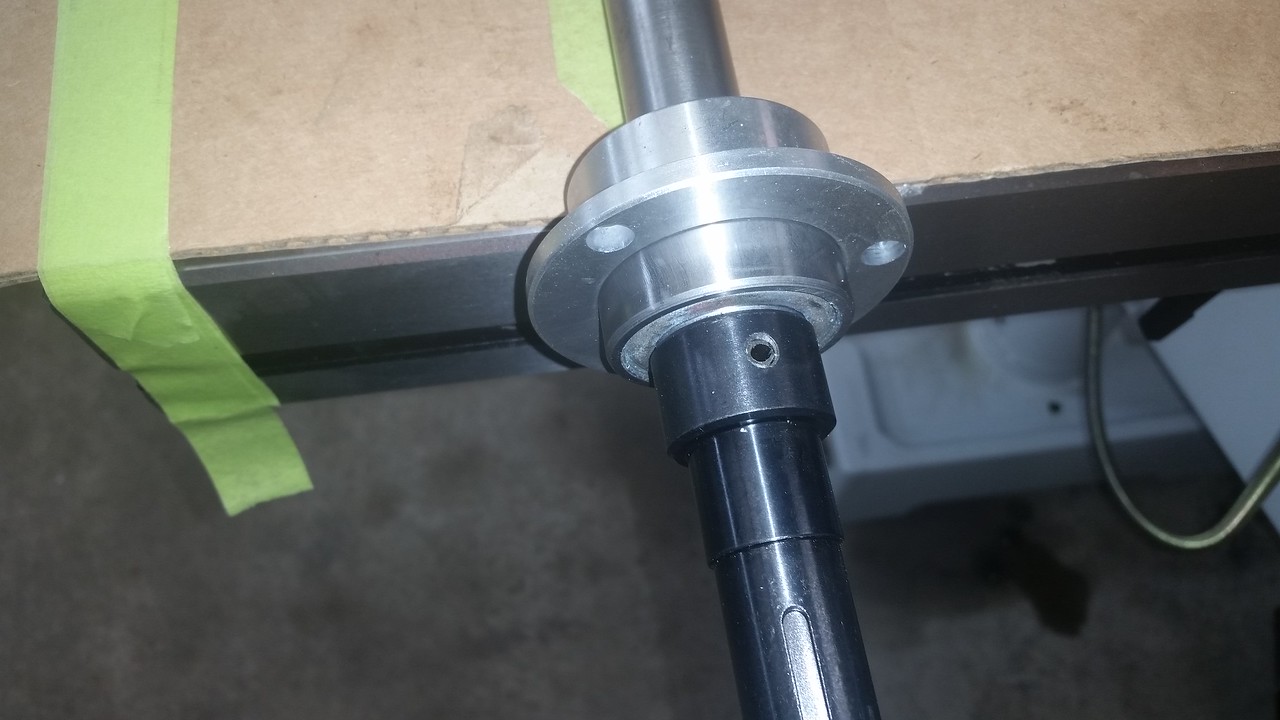
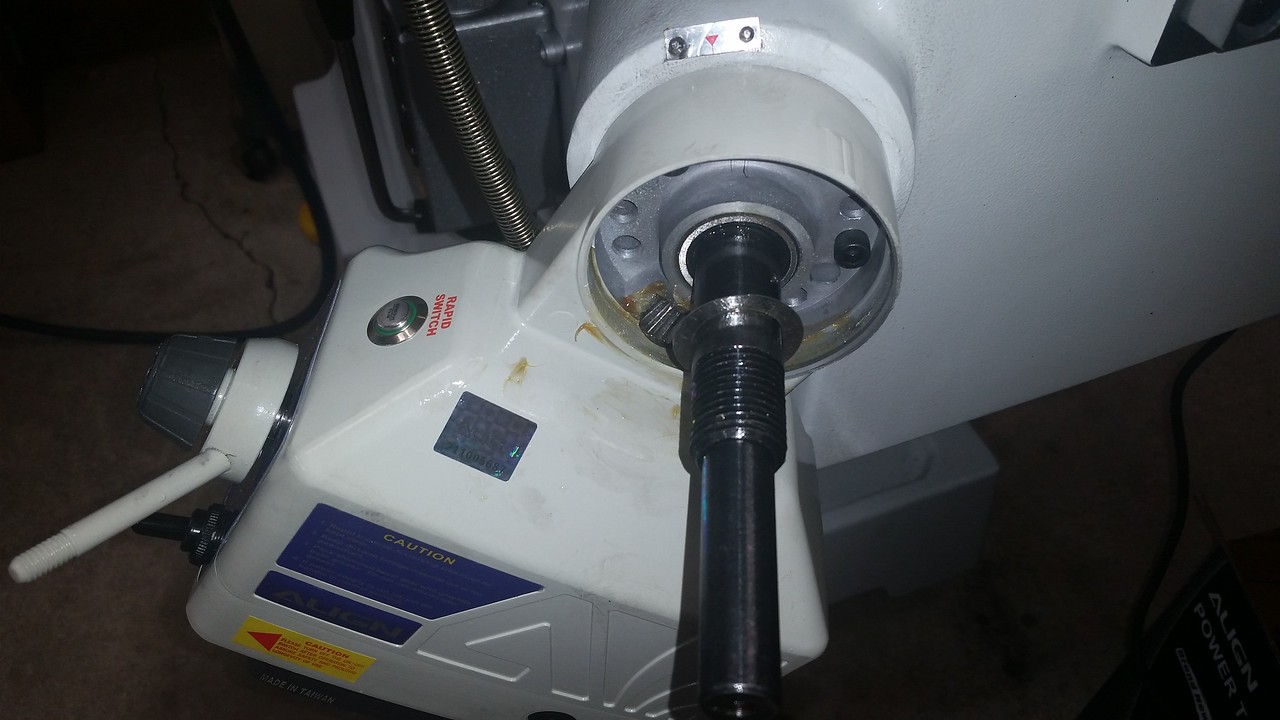
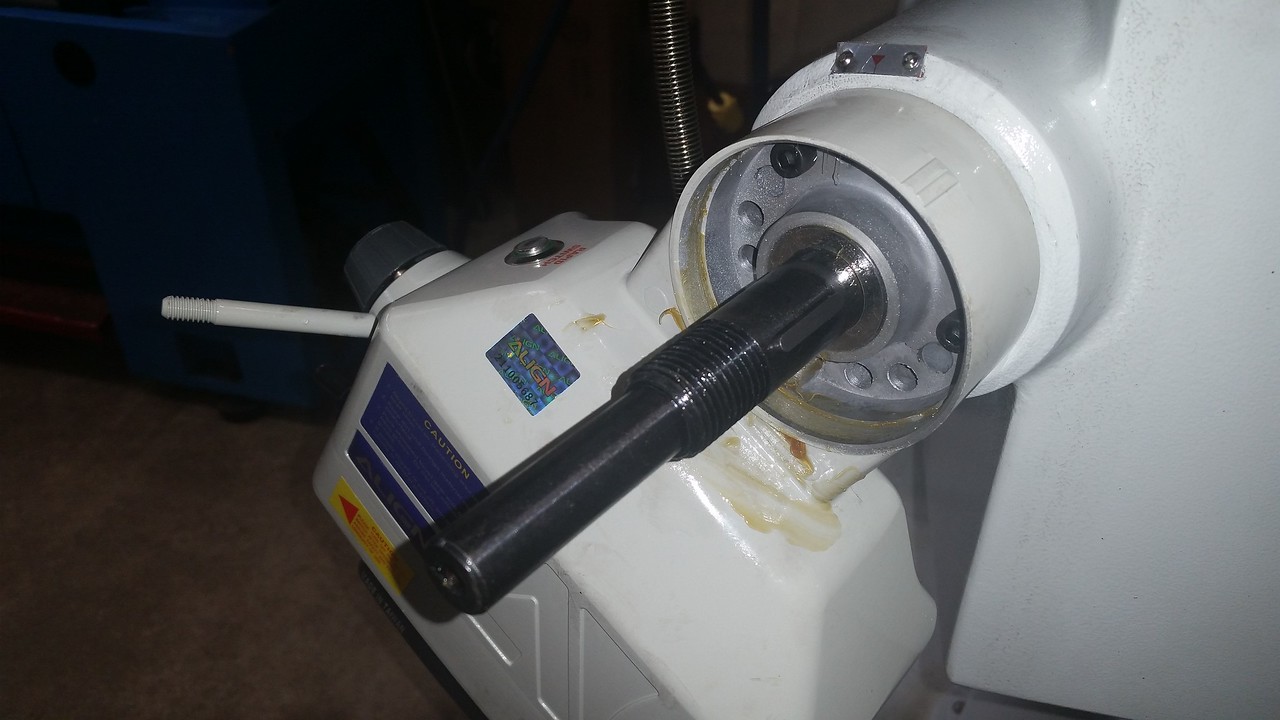
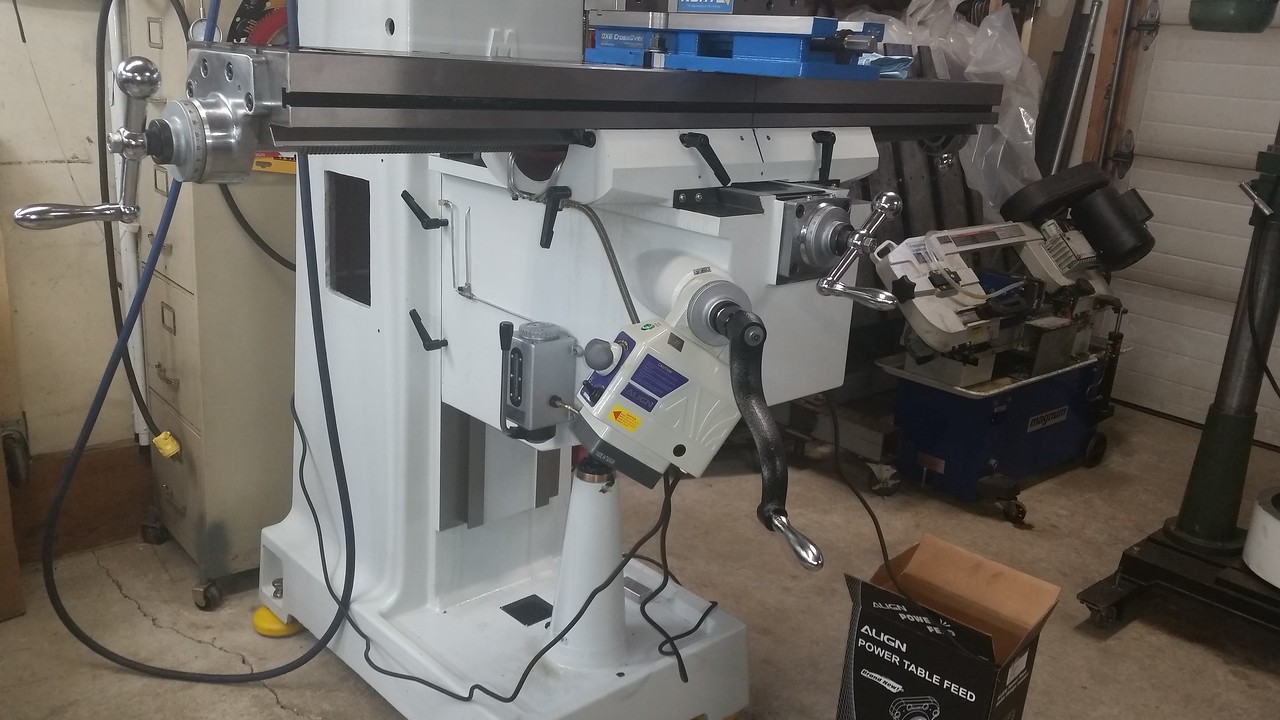
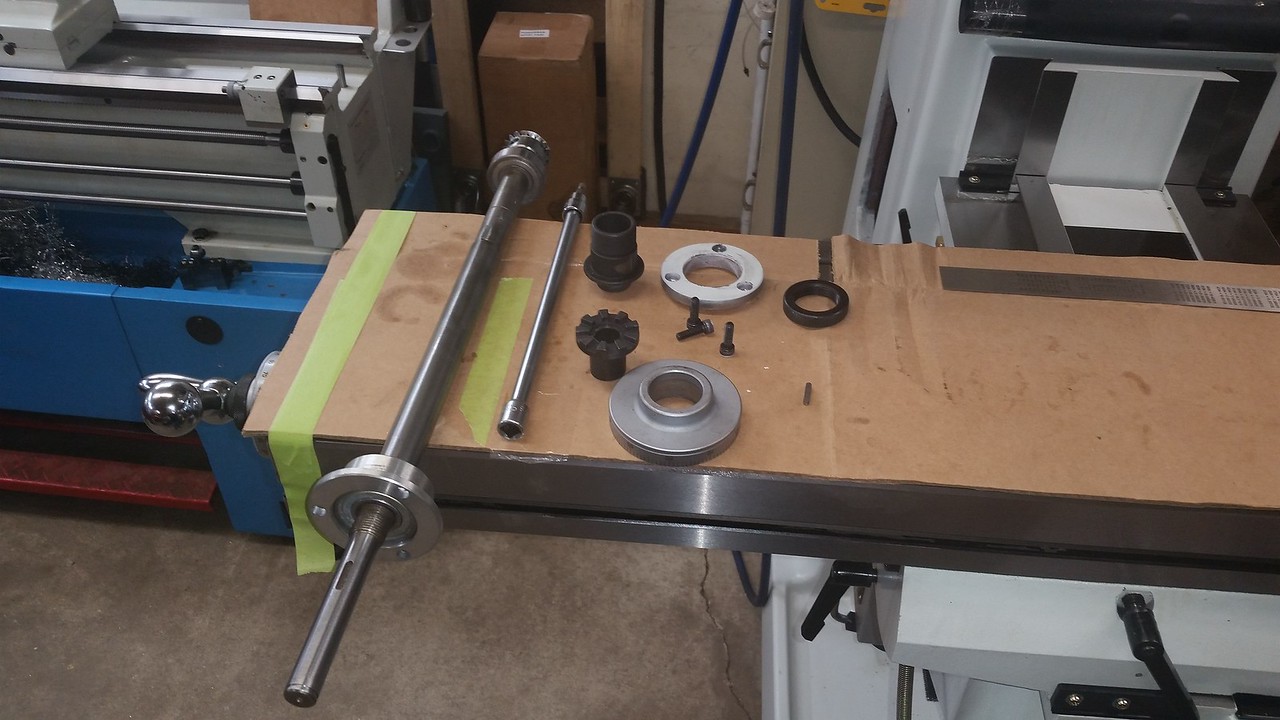
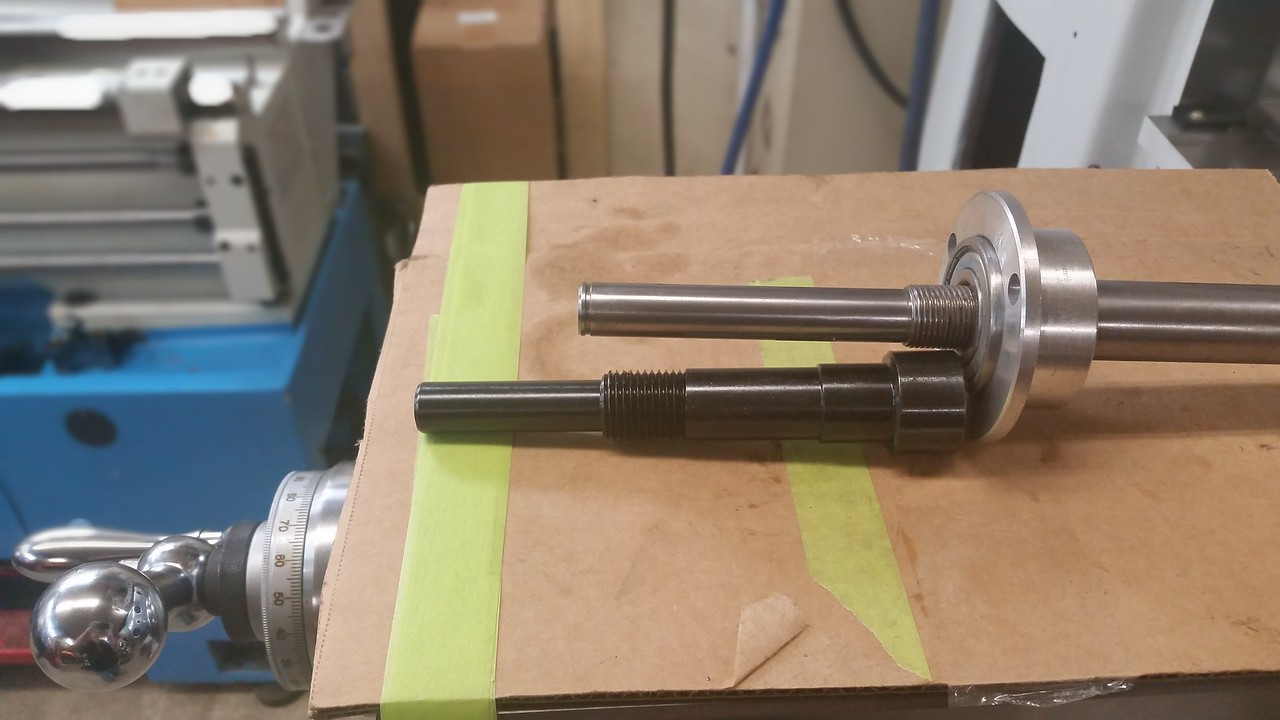
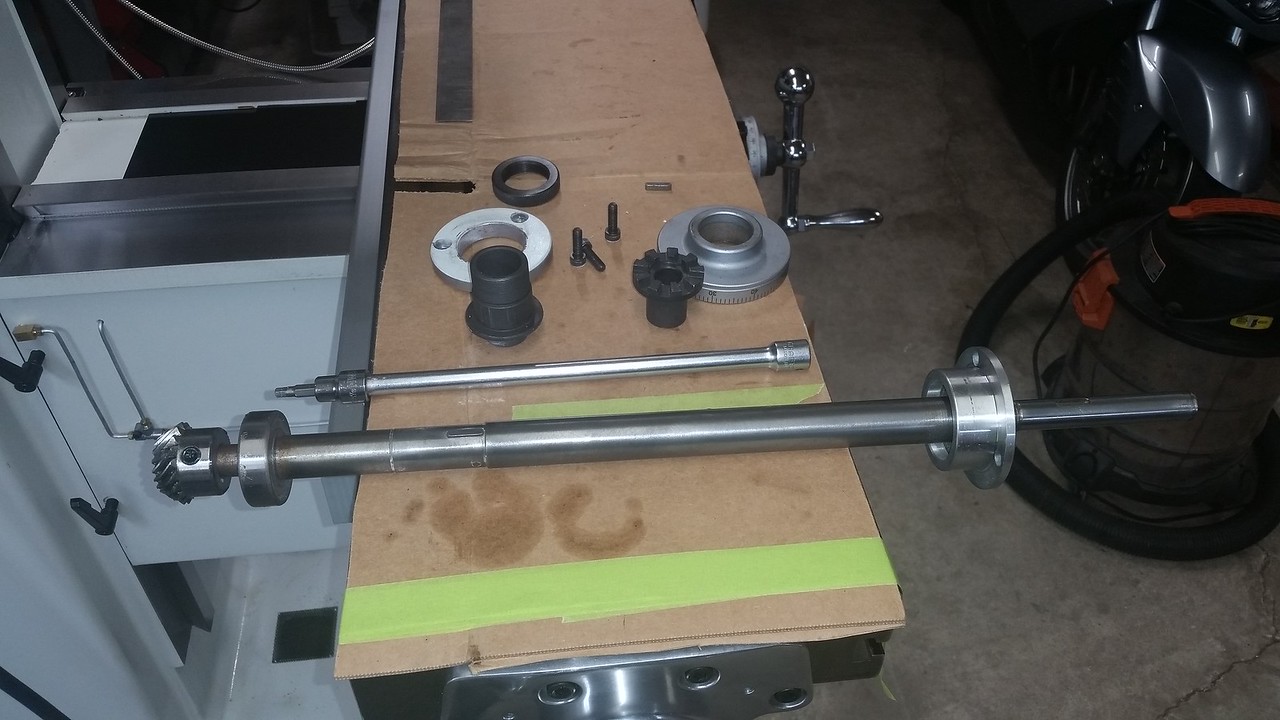
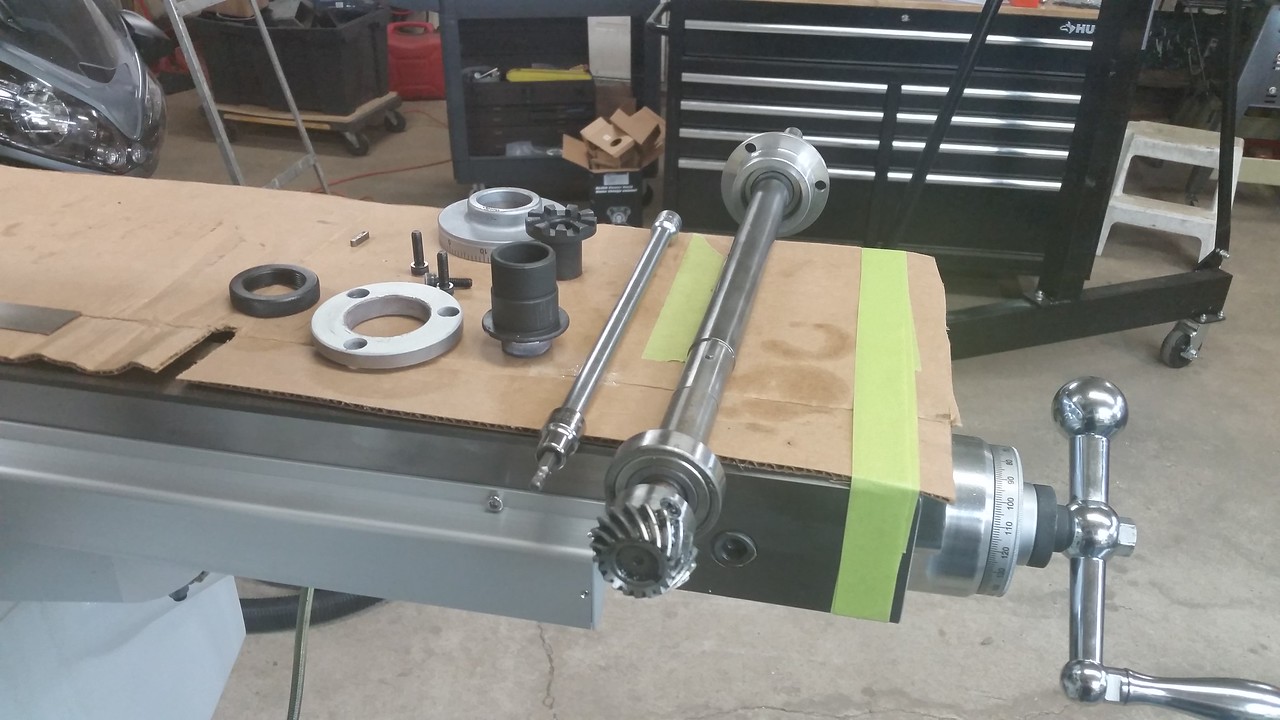
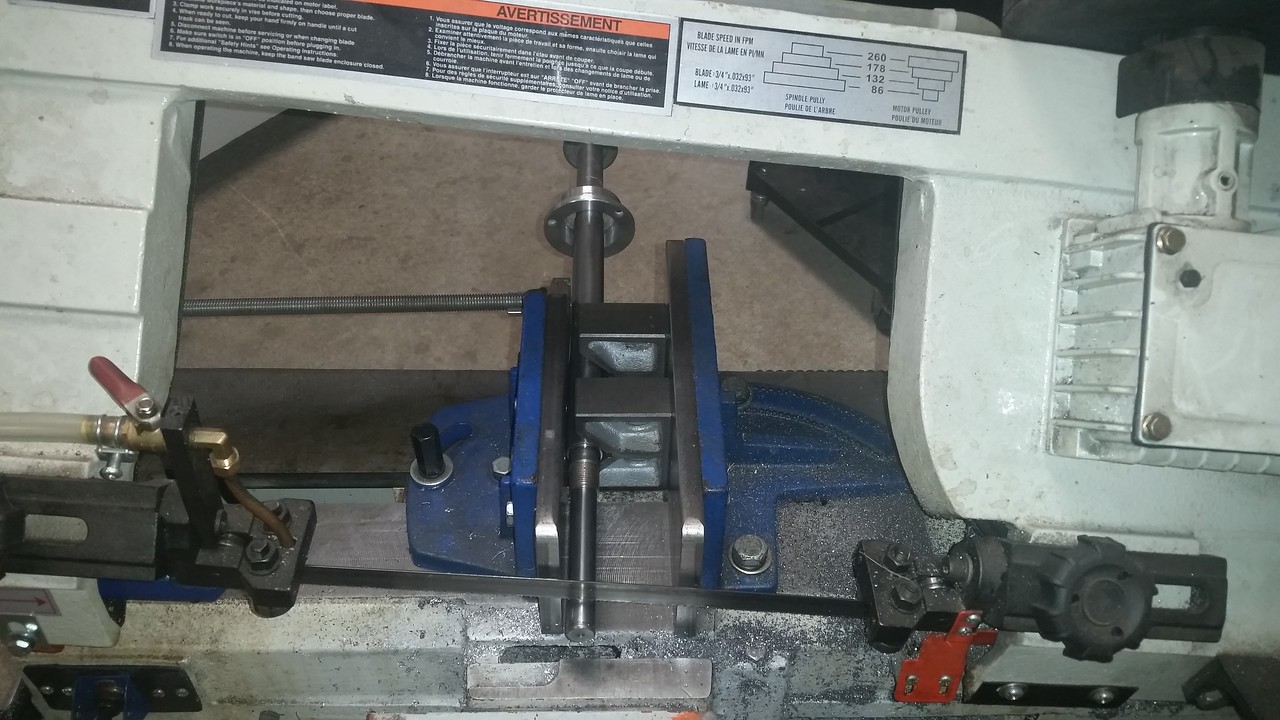
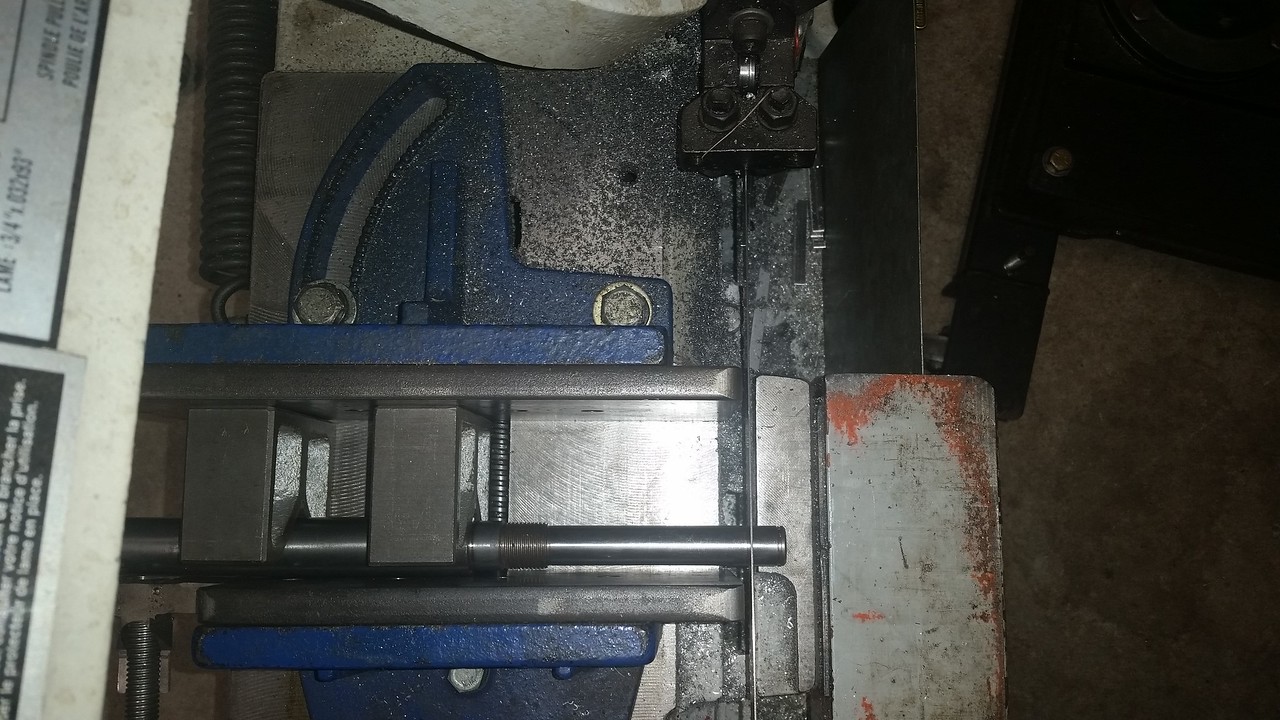

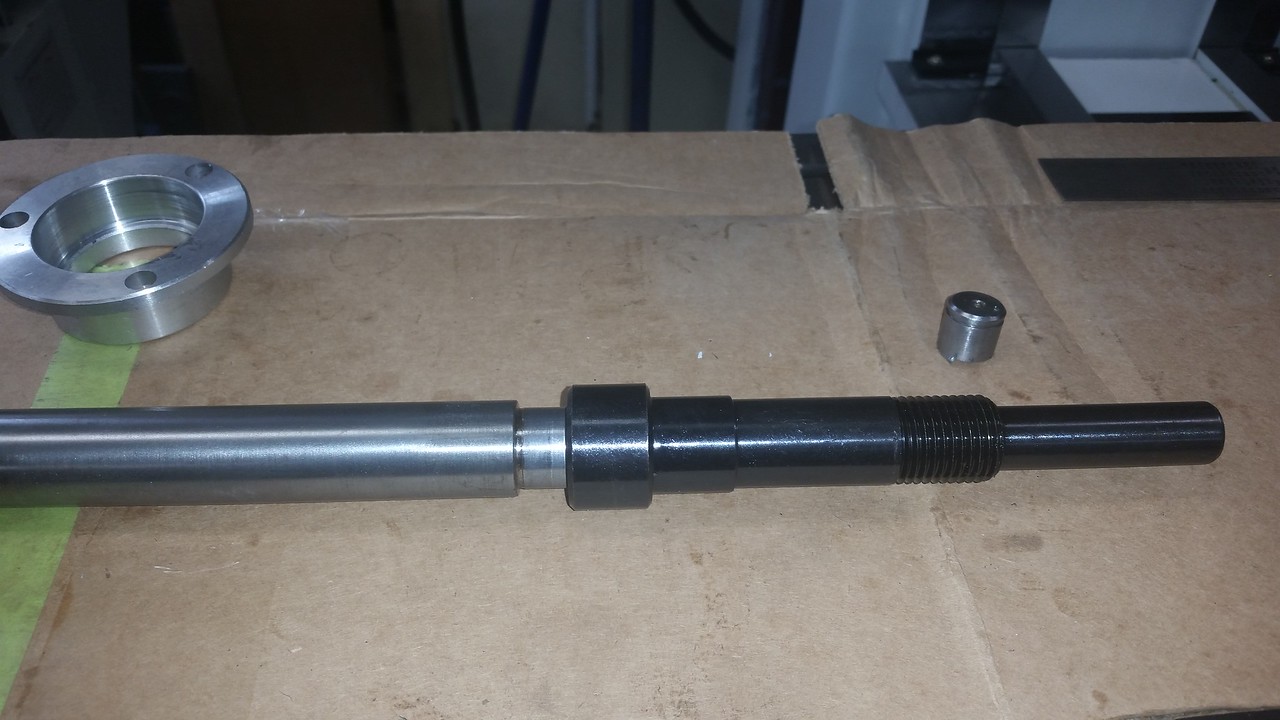
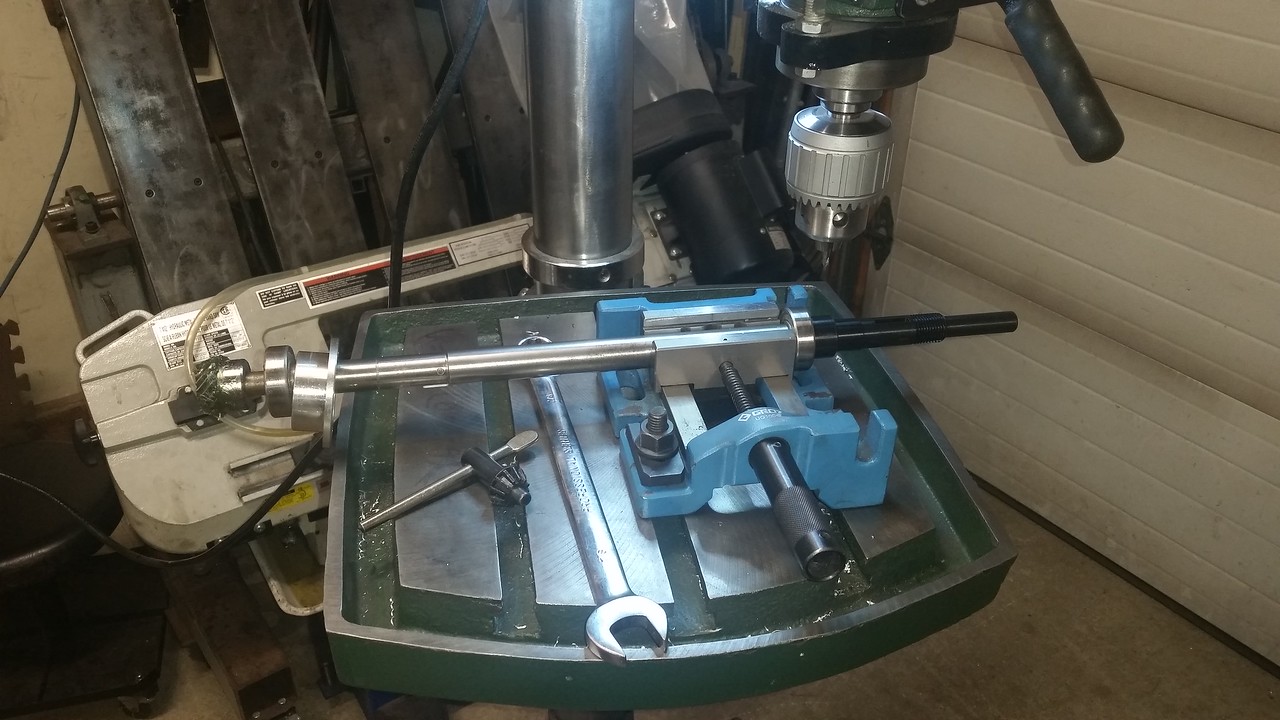

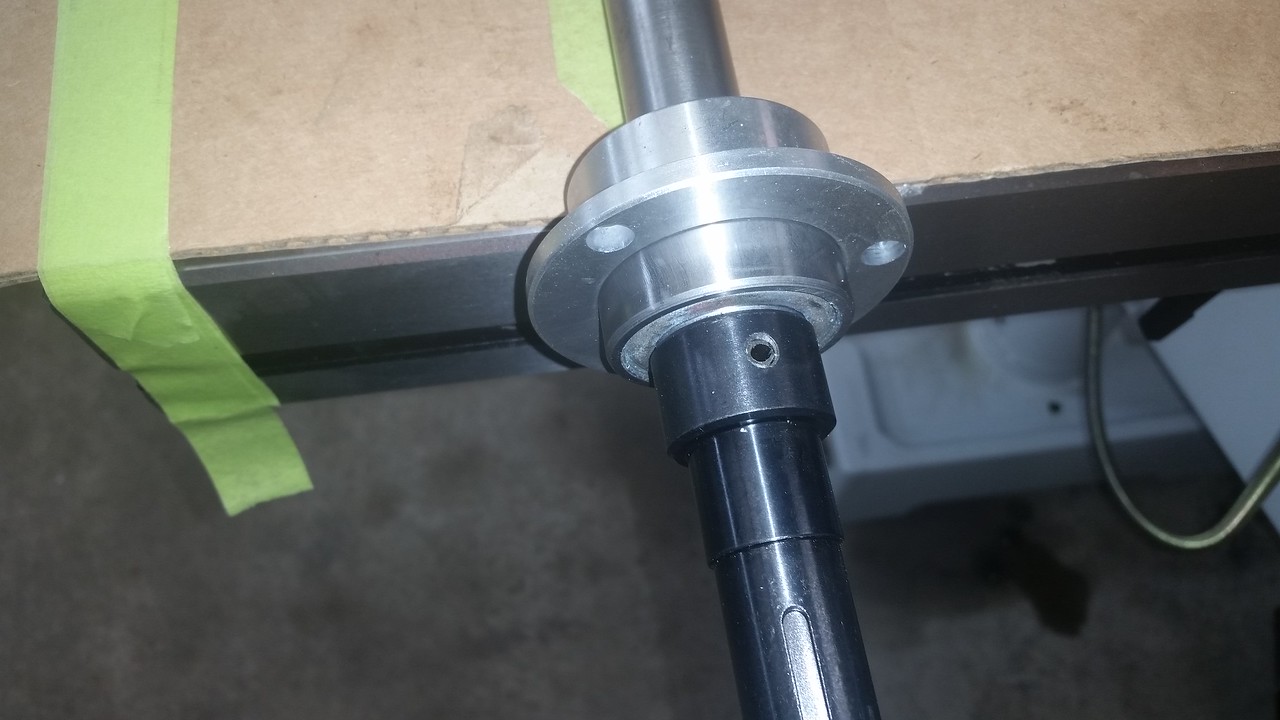
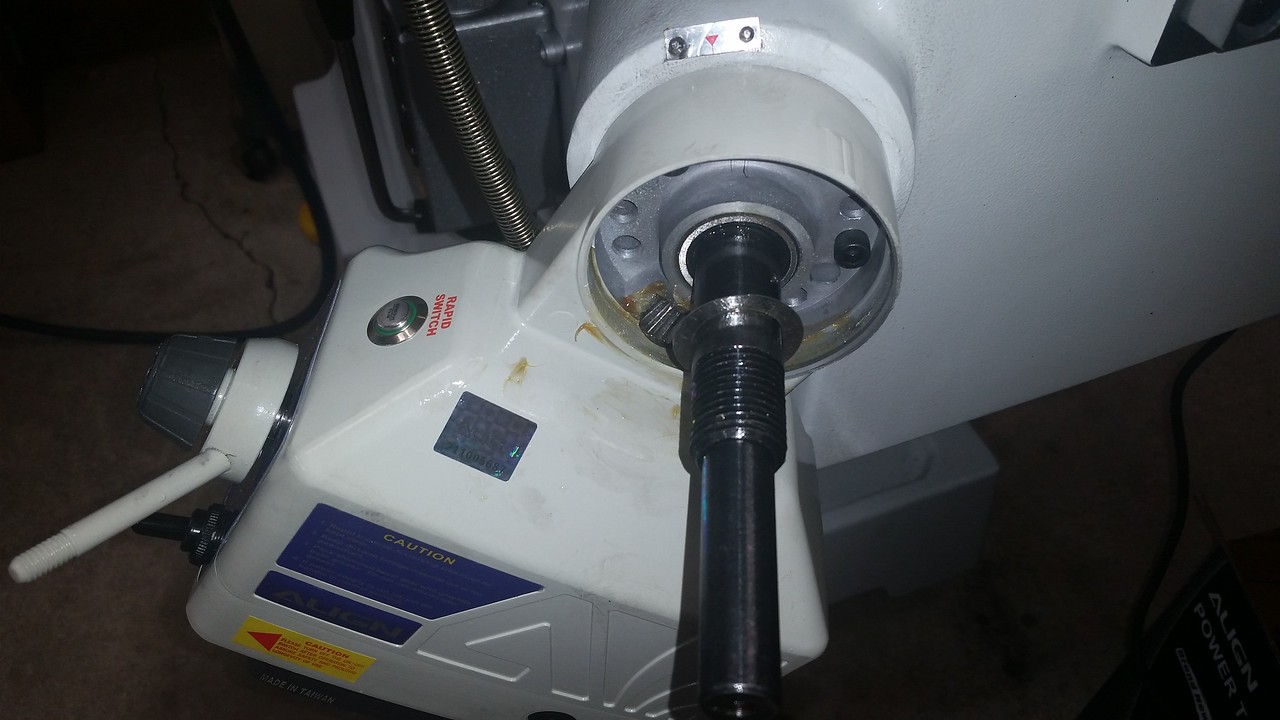
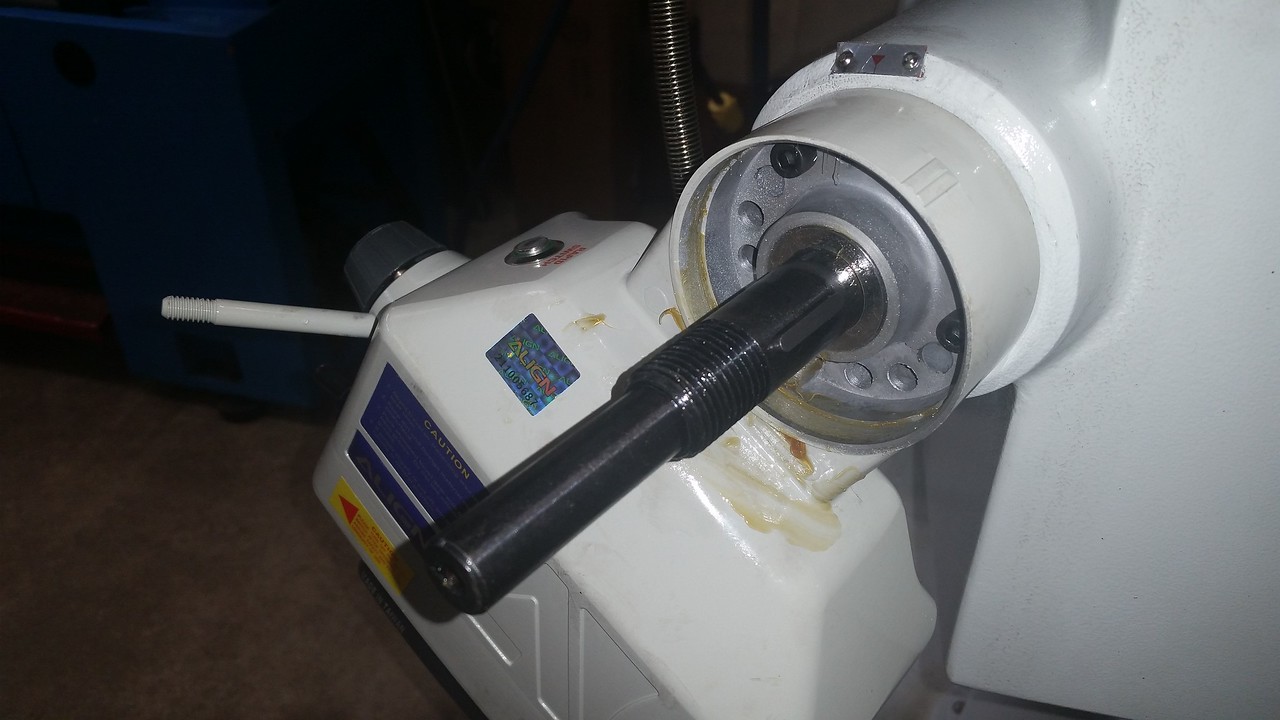
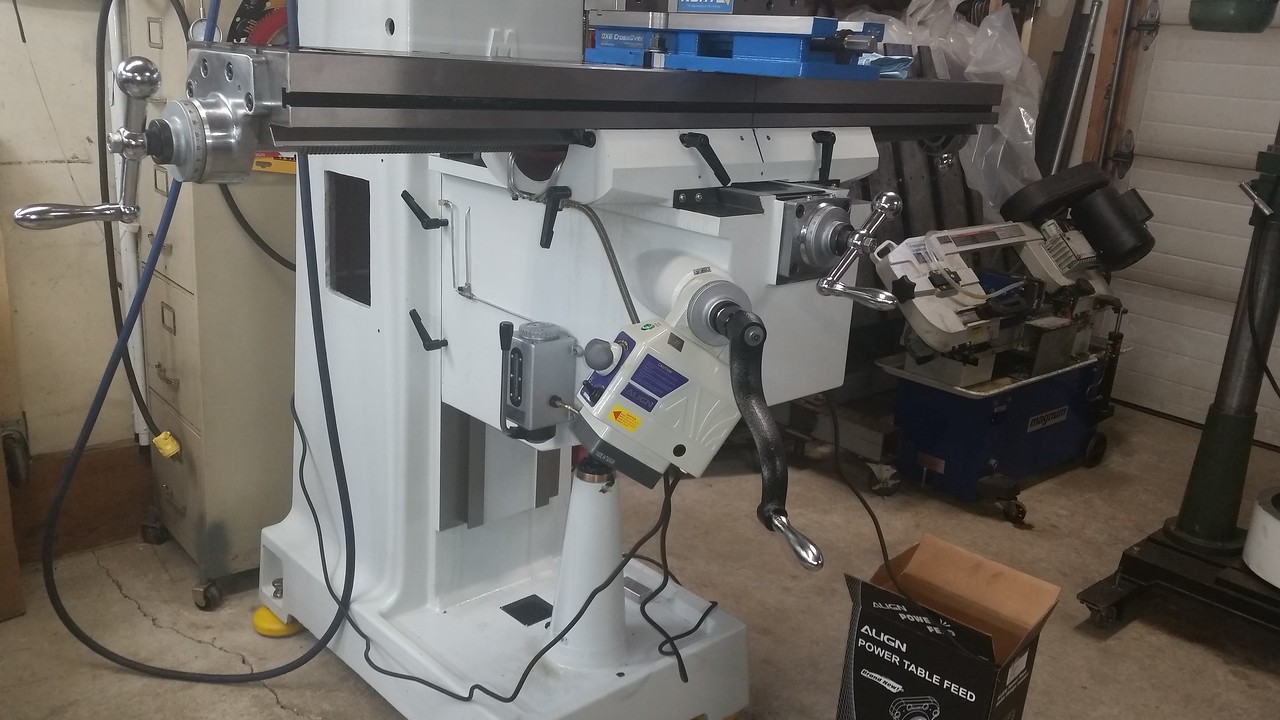