- Joined
- Feb 17, 2013
- Messages
- 336
I ordered a new PM1054TV on May 17/21 and after a few shipping delays it arrived at the Pacific Coast Express trucking depot in Edmonton on September 23/21. I had arranged to have my friend Glenn meet me there with his 1 ton truck and tilt deck cargo trailer. We got the new mill home safely. I had started the day getting the gantry crane adjusted to the highest it can go in the sweet spot in the garage where there is nothing on the ceiling to hit. The beam clamp and chain hoist in place and ready to go.
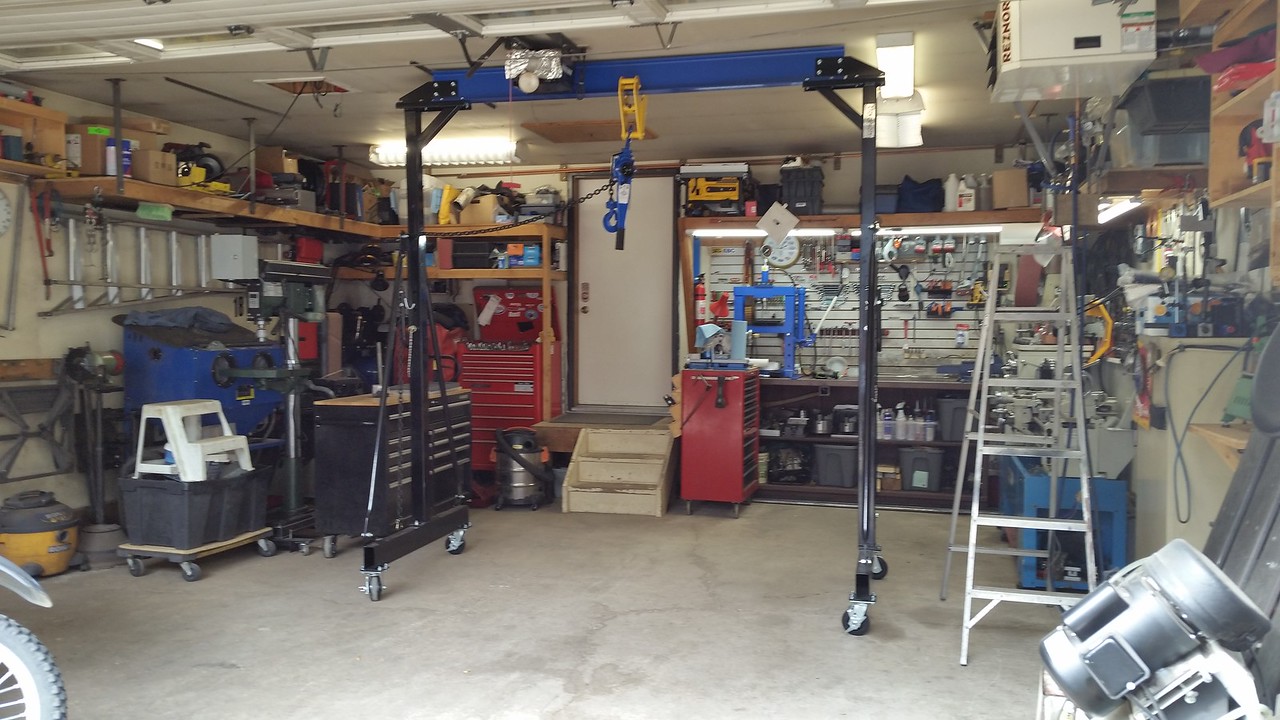
I met Glenn at Pacific Coast Express and they loaded it onto his' trailer deck. The crate was 66" X 66" X 76" tall and the fork lift operator made short work of it. The crate was in perfect condition which made me very happy.
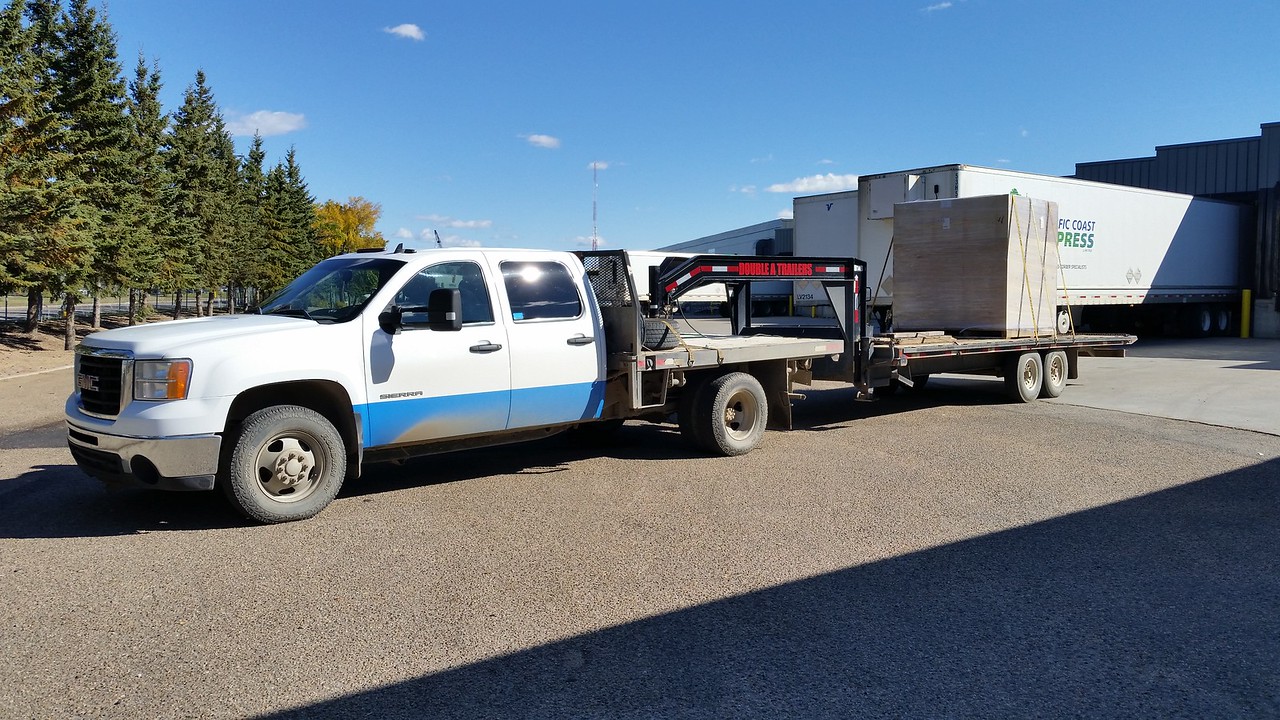
Once at my place Glenn got the trailer backed in with it's tail aligned with the door opening and we double checked the clearance through the 8' tall door opening. We put a strap around the belly of the crate and connected it to the winch cable then put the pallet jack under the downhill side. We lifted the crate just high enough so it would roll down the deck slowly as the winch was rolling the cable out until the bottom edge was off the trailer. Then with the pallet jack raised as high as it would go we put the machine skates under the bottom corners.
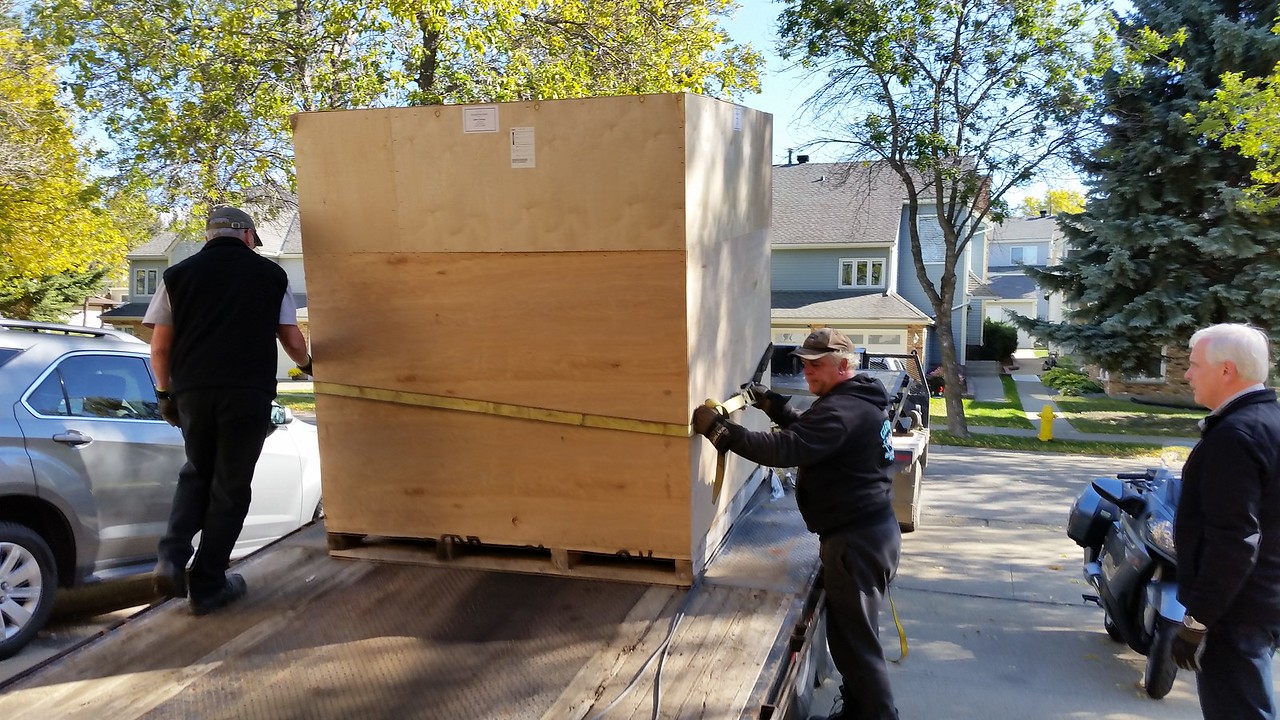
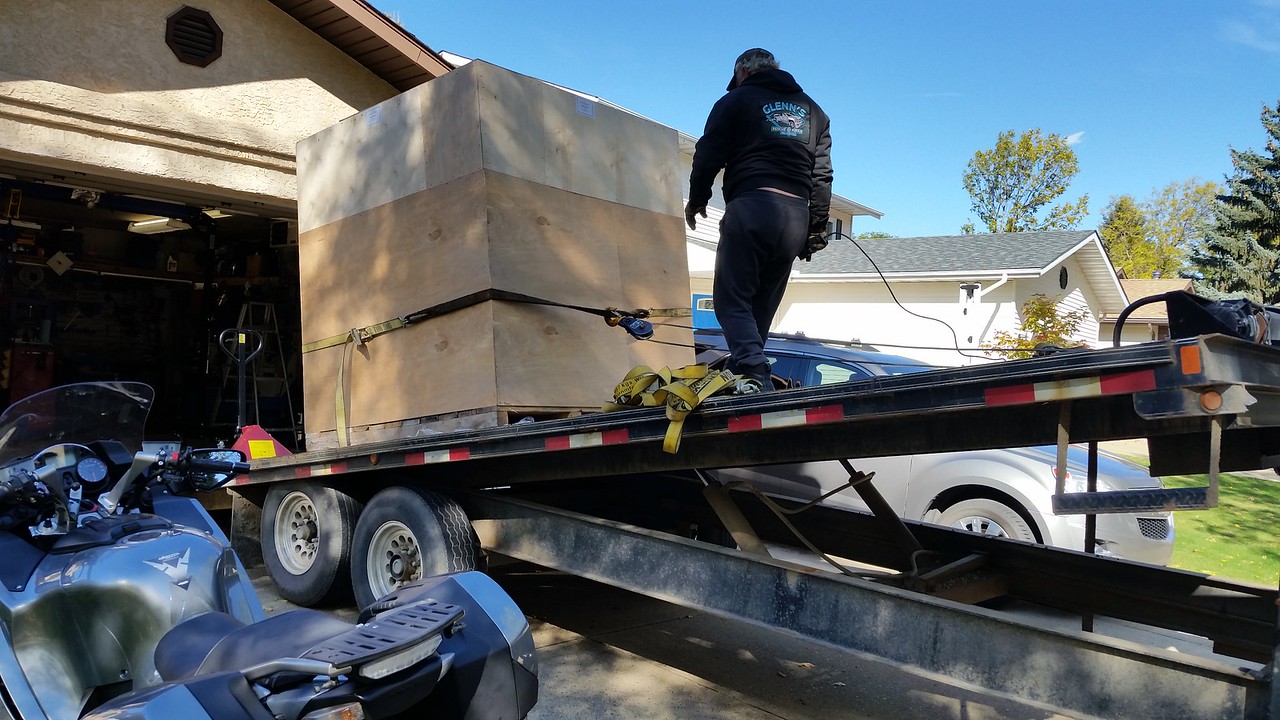
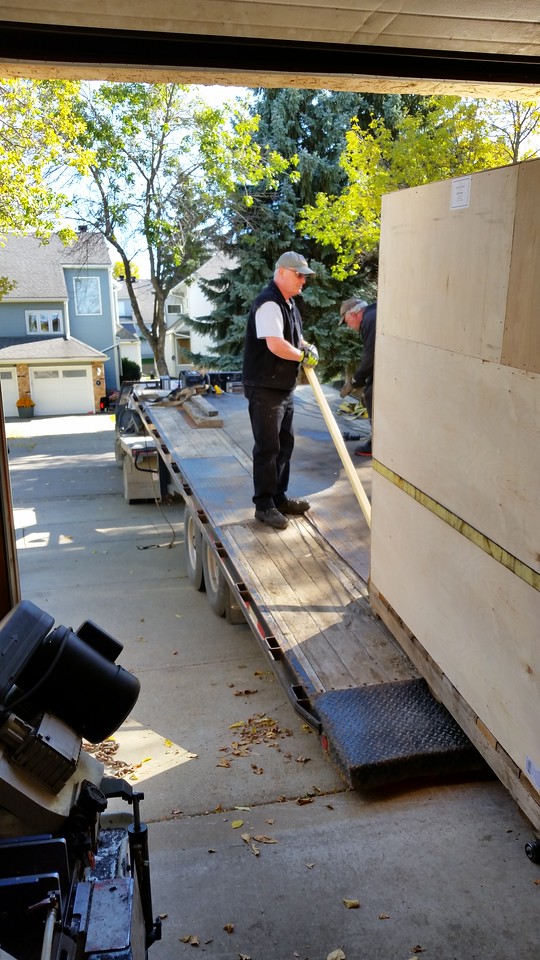
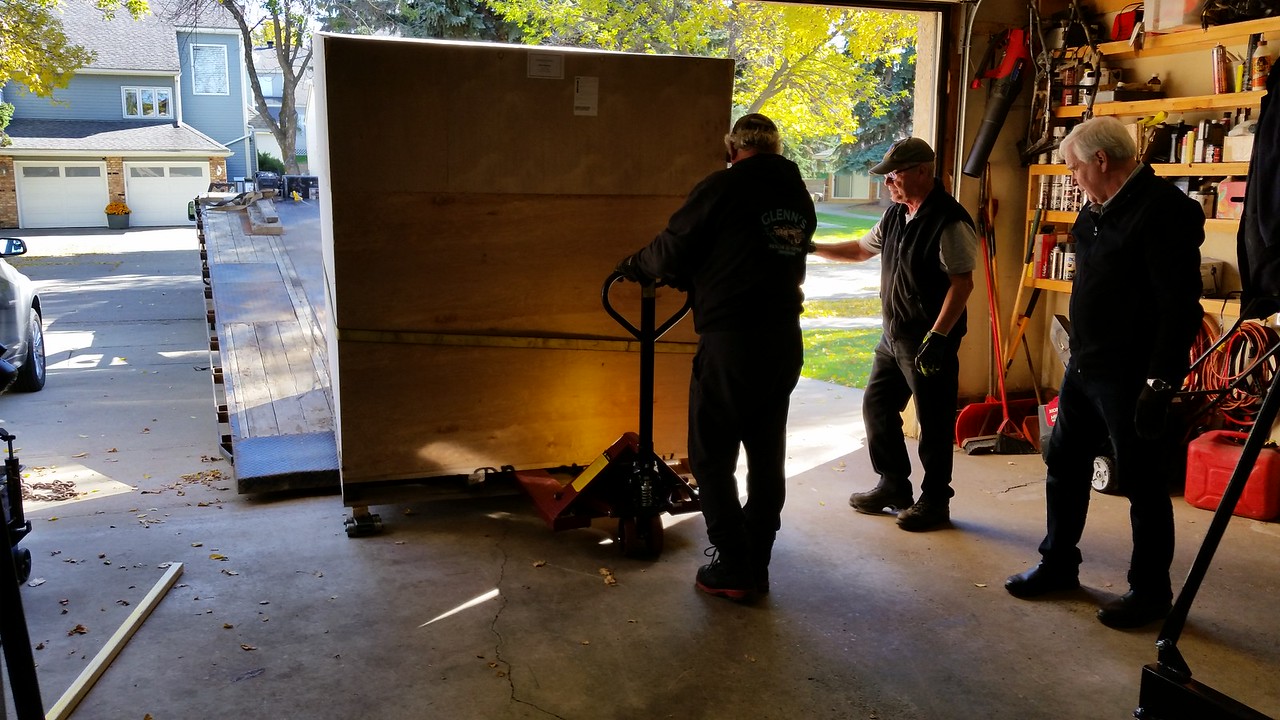
Then we moved the pallet jack to the uphill side. The skates allowed the bottom edge to roll into the garage as soon as the weight was raised and we let it down slowly with the winch.
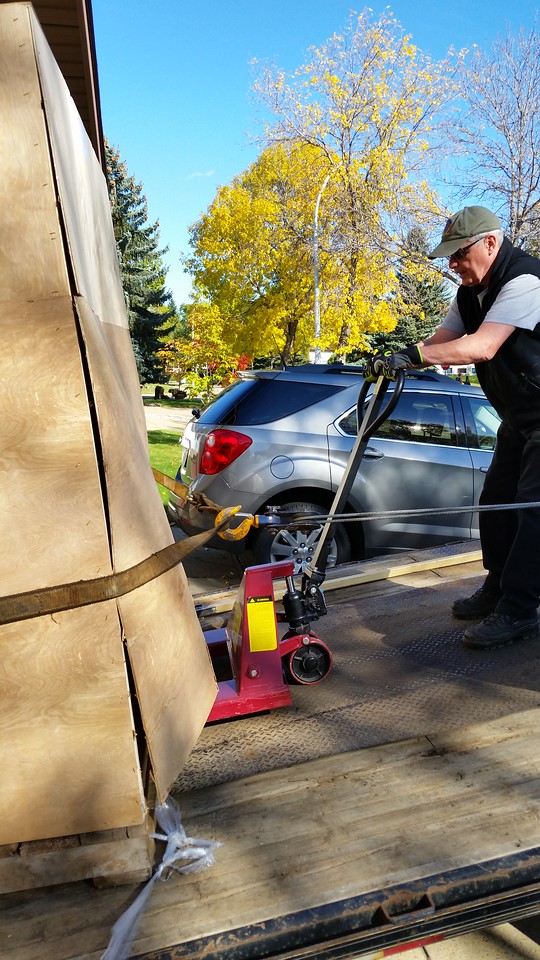
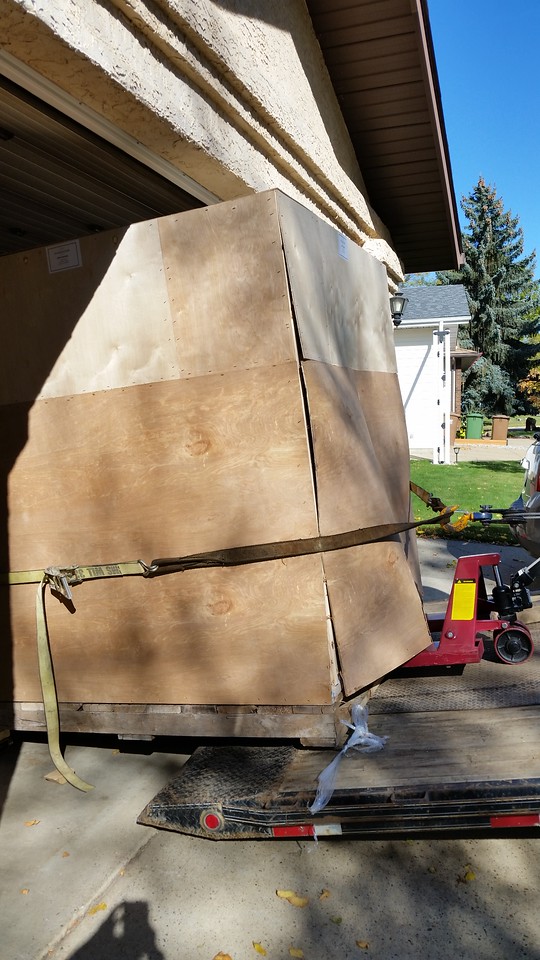
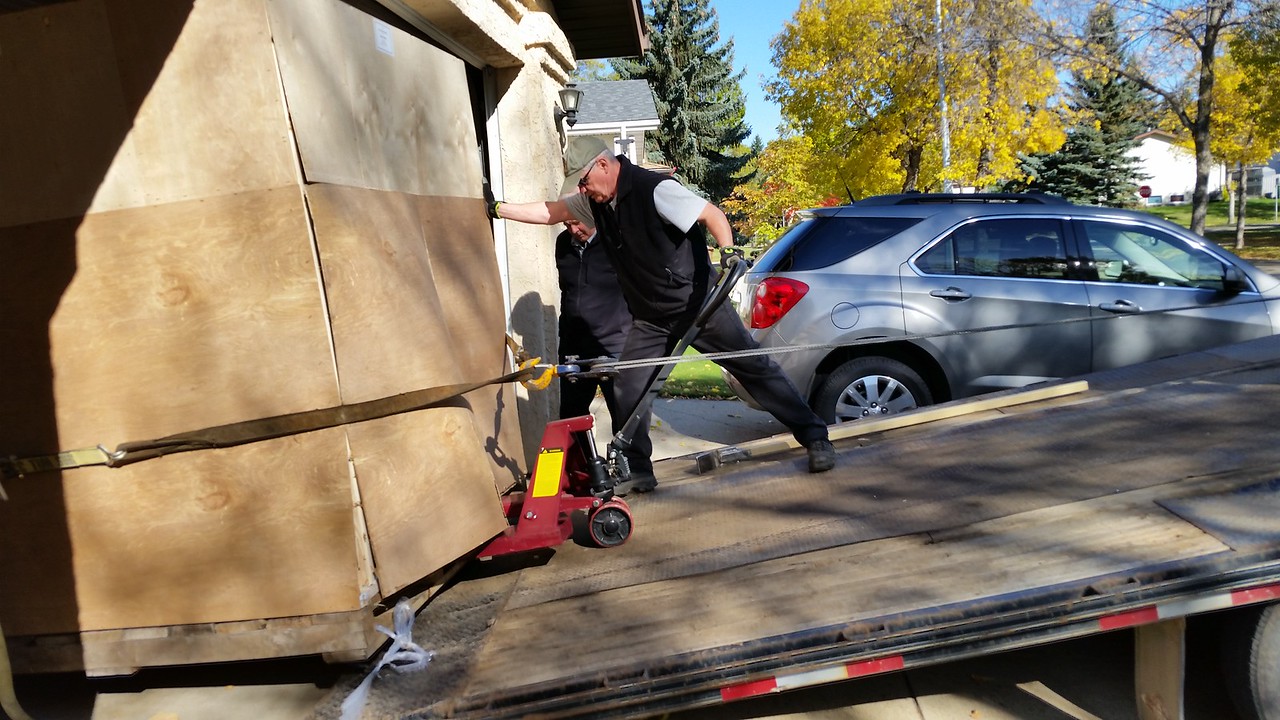
We jacked up the pallet jack as high as it would go and placed the other 2 skates under the front edge and when we lowered the jack the weight was all on the skates and it rolled easily into the garage.
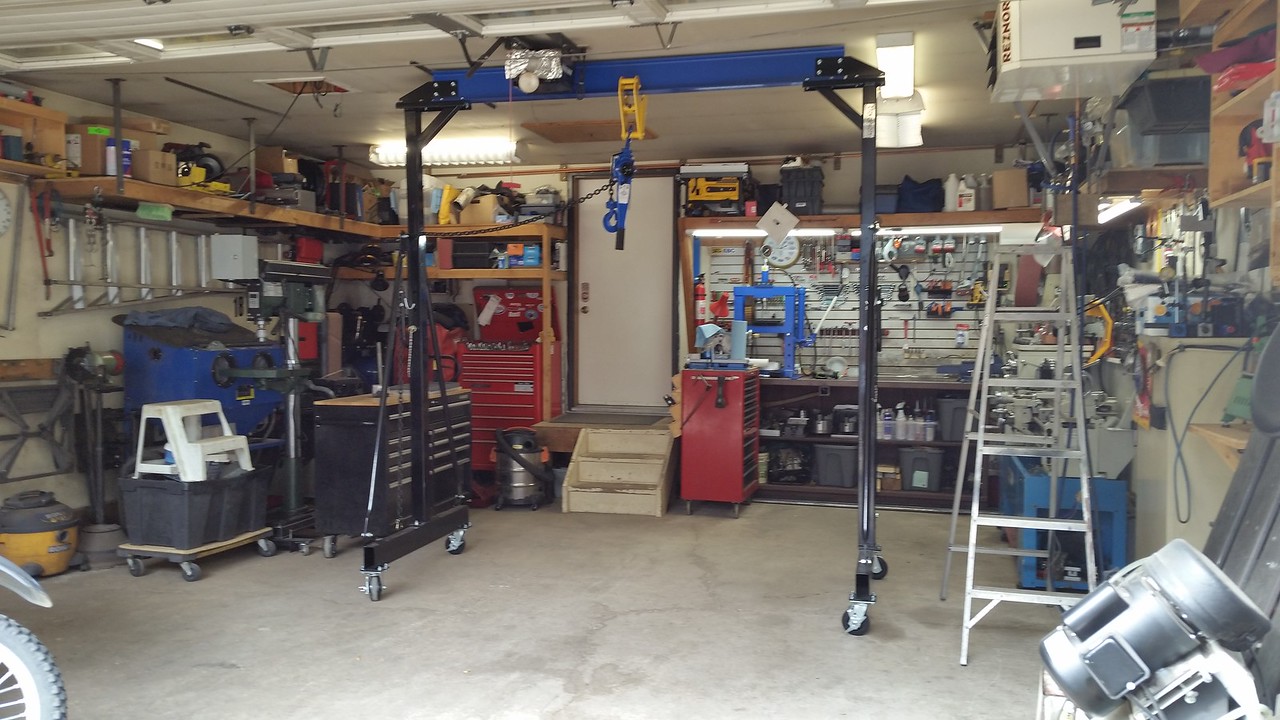
I met Glenn at Pacific Coast Express and they loaded it onto his' trailer deck. The crate was 66" X 66" X 76" tall and the fork lift operator made short work of it. The crate was in perfect condition which made me very happy.
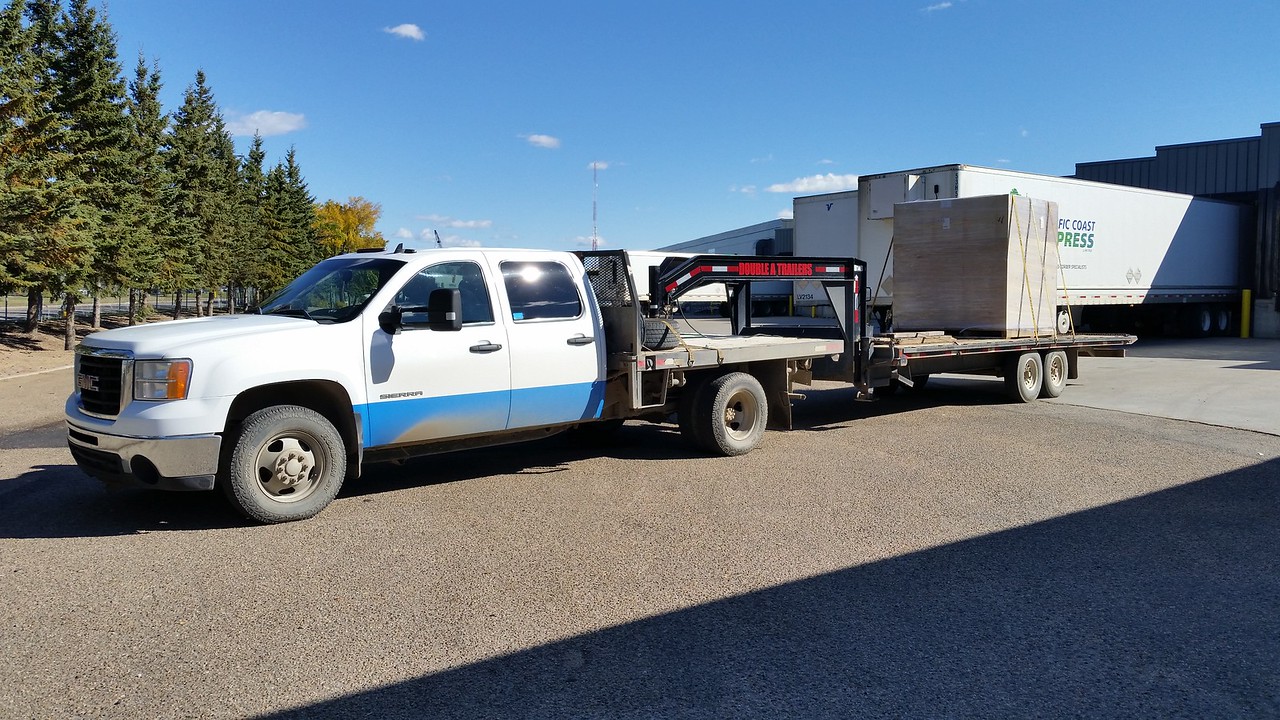
Once at my place Glenn got the trailer backed in with it's tail aligned with the door opening and we double checked the clearance through the 8' tall door opening. We put a strap around the belly of the crate and connected it to the winch cable then put the pallet jack under the downhill side. We lifted the crate just high enough so it would roll down the deck slowly as the winch was rolling the cable out until the bottom edge was off the trailer. Then with the pallet jack raised as high as it would go we put the machine skates under the bottom corners.
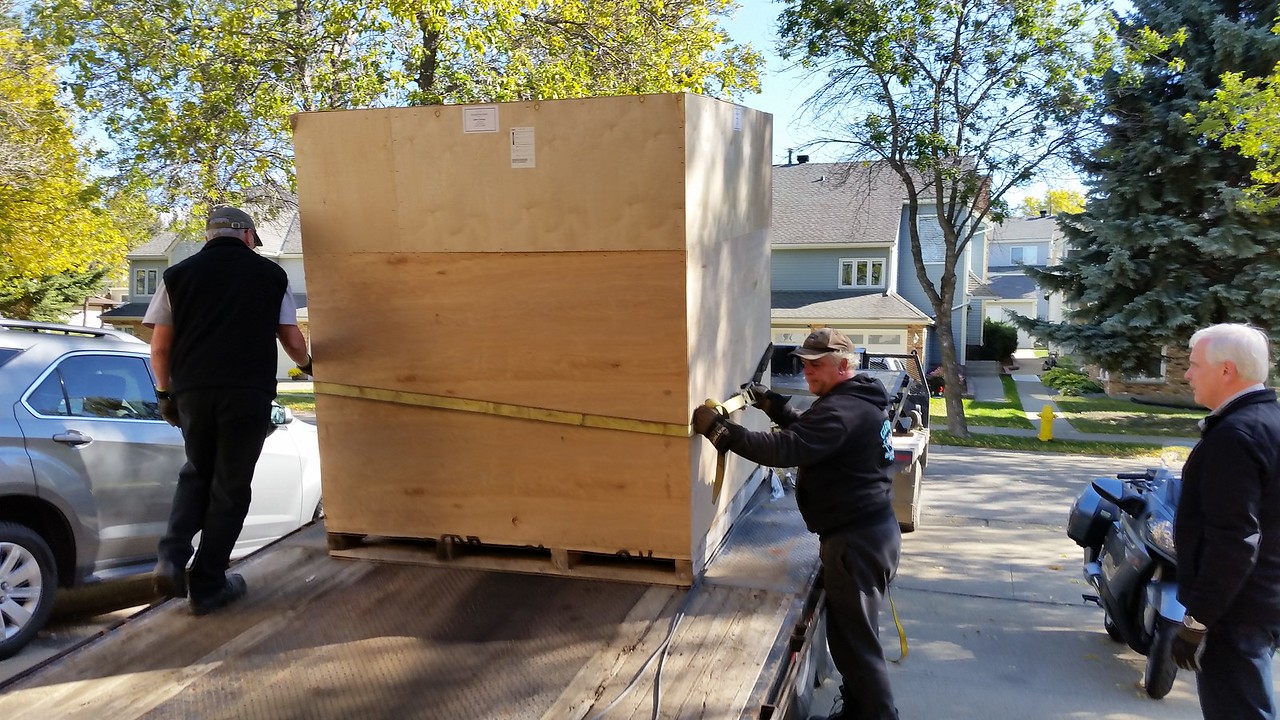
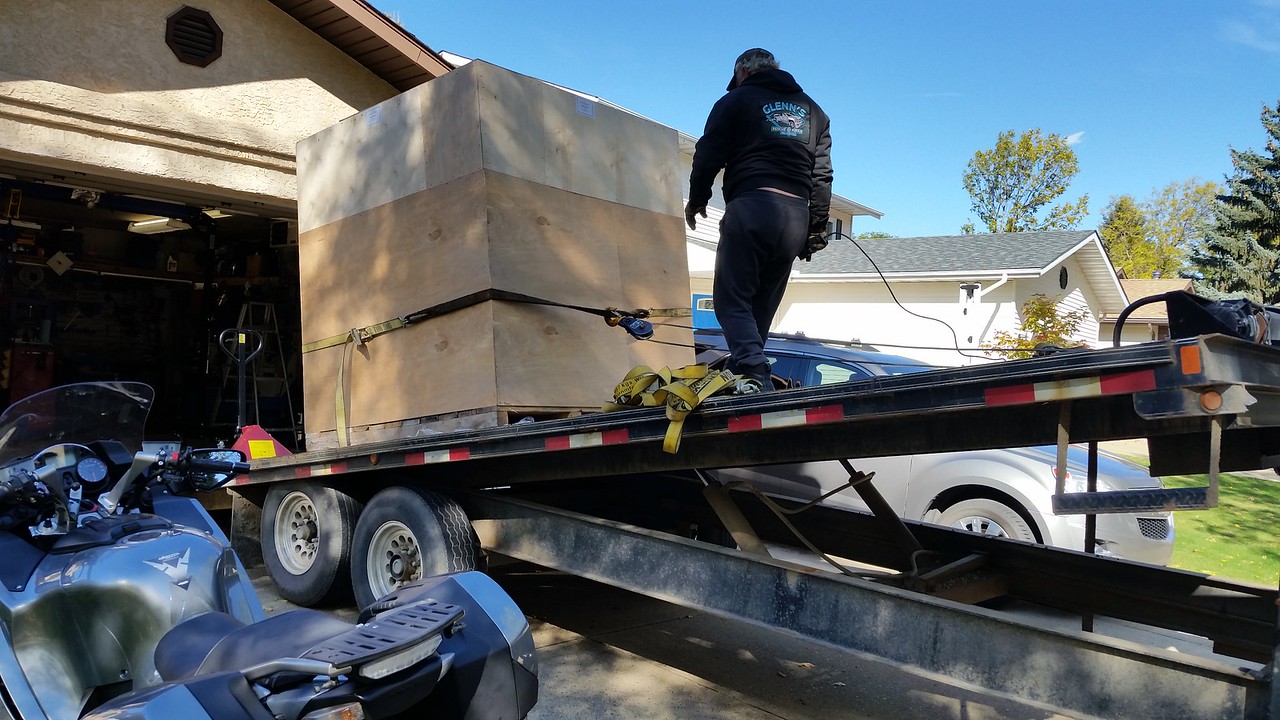
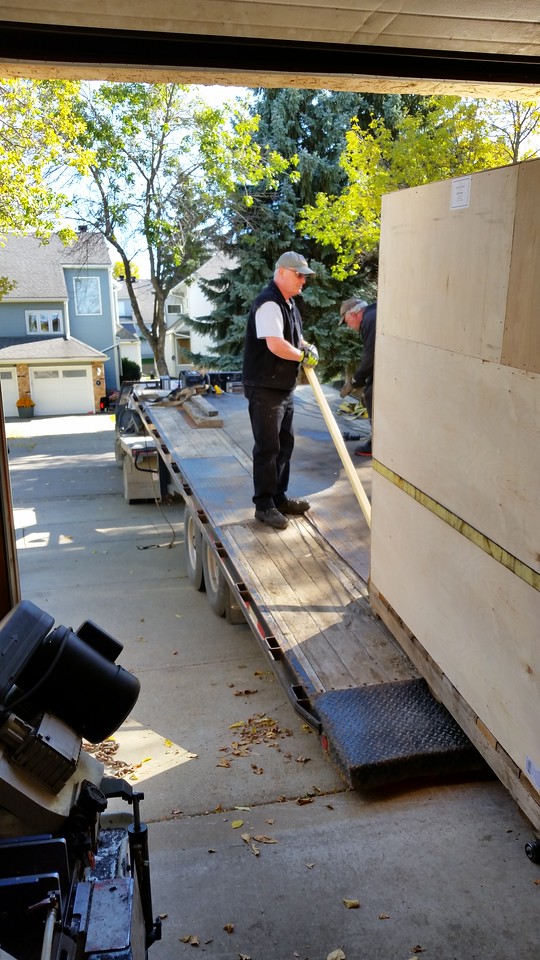
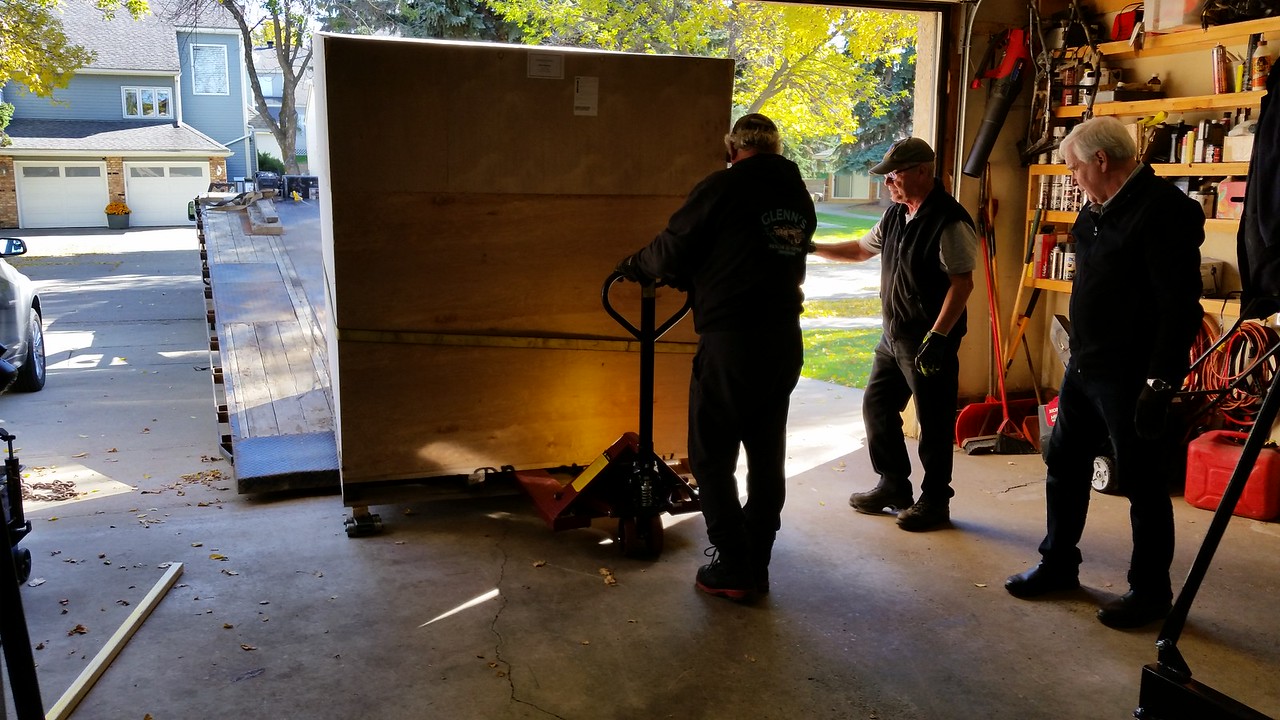
Then we moved the pallet jack to the uphill side. The skates allowed the bottom edge to roll into the garage as soon as the weight was raised and we let it down slowly with the winch.
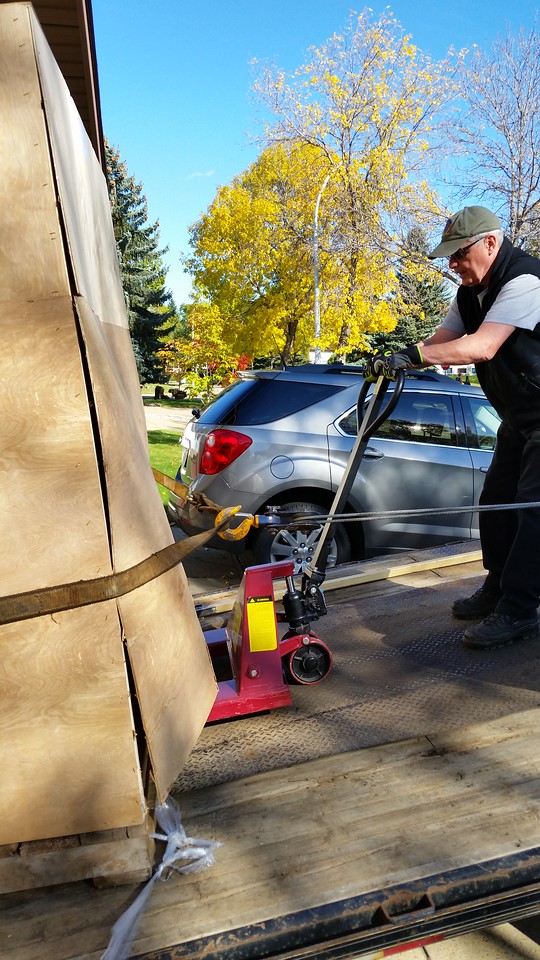
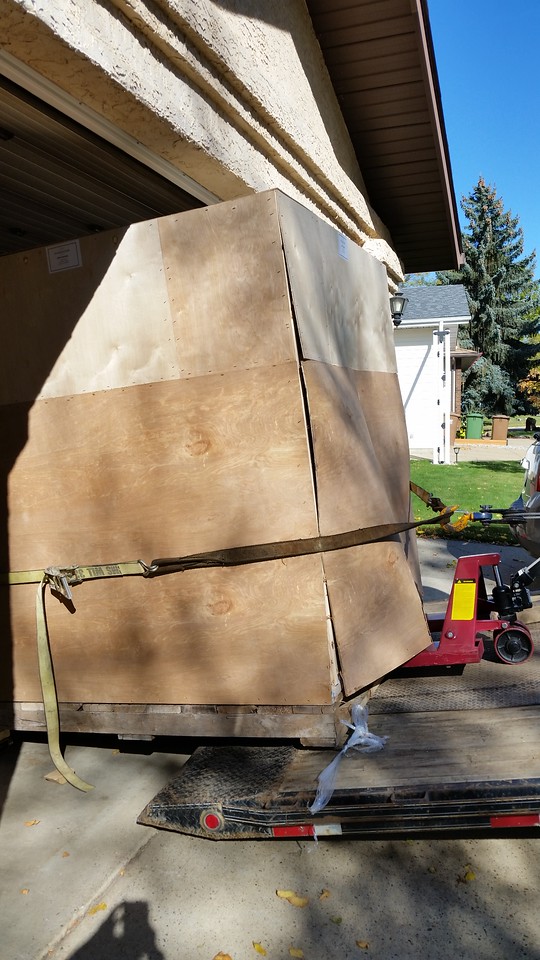
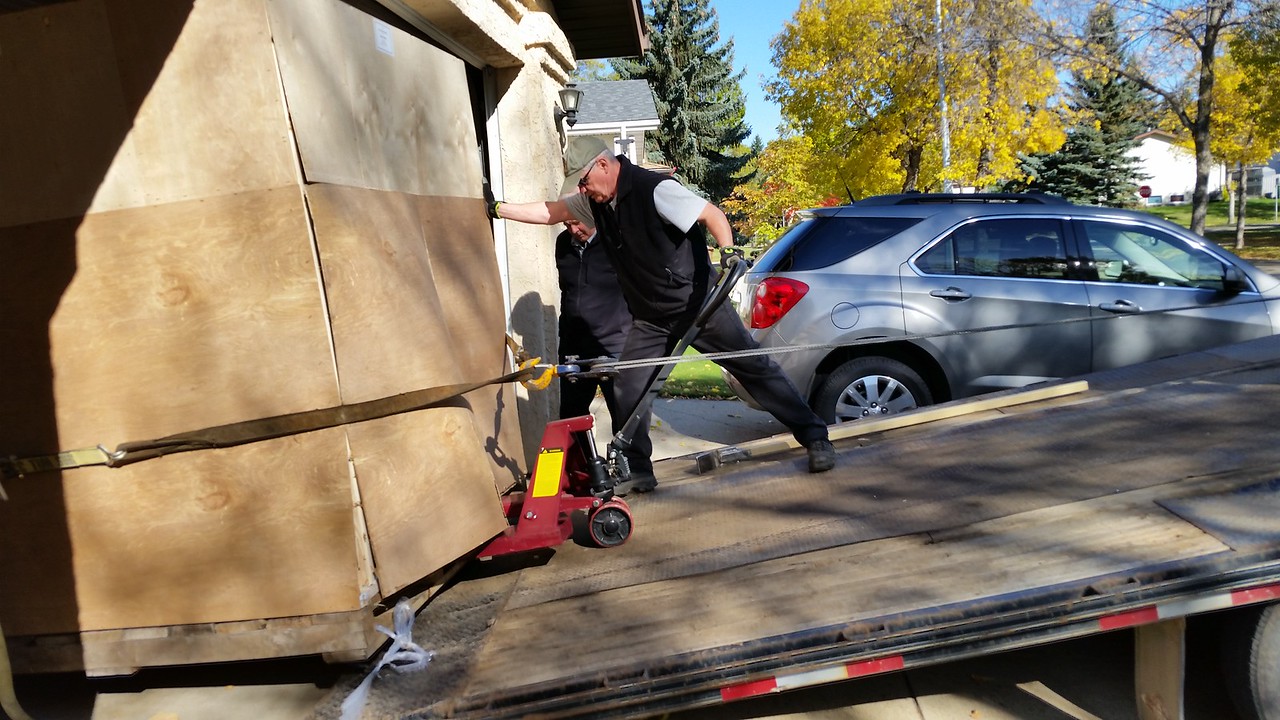
We jacked up the pallet jack as high as it would go and placed the other 2 skates under the front edge and when we lowered the jack the weight was all on the skates and it rolled easily into the garage.