- Joined
- Jul 18, 2011
- Messages
- 224
The 'CLASSIC CARS & HOTRODS' section looks a little bare so I thought I'd add some pics of my current project and a couple of the things I've machined for it.
It's a 1974 HQ Holden Belmont which is the Aussie interpretation of the US GM 'A' body cars (Chevy Nova is one example). It was bought new by my grandfather, passed down to my dad and then finally to me. By the time I got it, it needed to be restored and I spent the best part of ten years part time restoring it.
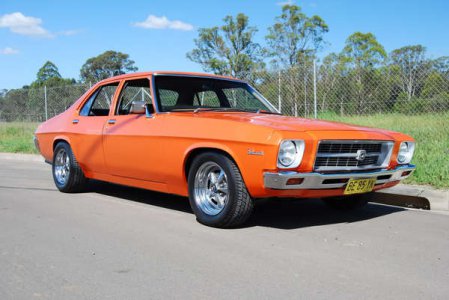
If you look carefully in this engine bay photo you might notice some of the things I've machined for it, I'll put some more detailed pics in following posts.
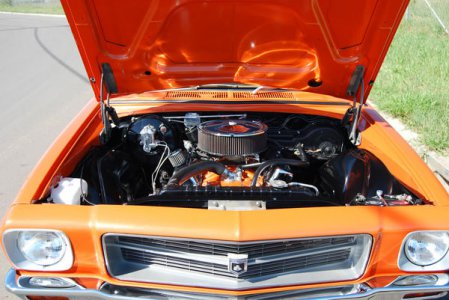
It's a 1974 HQ Holden Belmont which is the Aussie interpretation of the US GM 'A' body cars (Chevy Nova is one example). It was bought new by my grandfather, passed down to my dad and then finally to me. By the time I got it, it needed to be restored and I spent the best part of ten years part time restoring it.
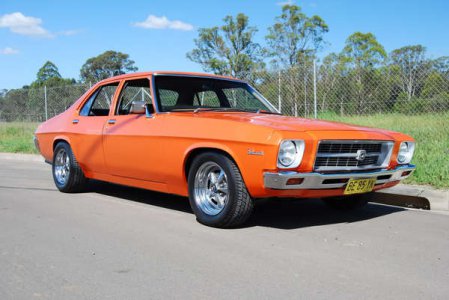
If you look carefully in this engine bay photo you might notice some of the things I've machined for it, I'll put some more detailed pics in following posts.
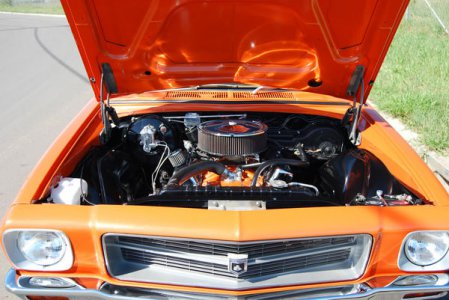
Last edited: