- Joined
- Dec 19, 2018
- Messages
- 130
I'm interested in purchasing this lathe:
Ideally i'm looking for a 8-9" swing with a 1.5" dia through hole primarily for gunsmith imperial threading of barrels and receivers. Would like to keep the cost <$1700 . I really need the weight to be below 450 lbs. as I will need to get this lathe down into my basement and up onto a workbench. Lastly would like the minimum rpm capability either 50 or 100 rpms. I'm having a hard time finding the ideal lathe. This lathe looks like a close match but it looks like it can't be configured to cut 16 and 24 TPI thread pitches. Does anyone know if there is gear combos available (or gears that can be 3D printed) to achieve 16 and 24 imperial pitches ? Thanks is advance !
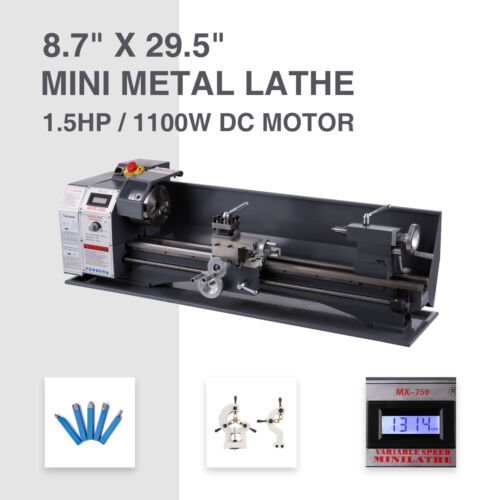
Upgraded 8.7"x 29.5" Mini Metal Lathe 1100W Metal Gear Digital Display 5 Tools 729270372692 | eBay
Find many great new & used options and get the best deals for Upgraded 8.7"x 29.5" Mini Metal Lathe 1100W Metal Gear Digital Display 5 Tools at the best online prices at eBay! Free shipping for many products!
www.ebay.com
Ideally i'm looking for a 8-9" swing with a 1.5" dia through hole primarily for gunsmith imperial threading of barrels and receivers. Would like to keep the cost <$1700 . I really need the weight to be below 450 lbs. as I will need to get this lathe down into my basement and up onto a workbench. Lastly would like the minimum rpm capability either 50 or 100 rpms. I'm having a hard time finding the ideal lathe. This lathe looks like a close match but it looks like it can't be configured to cut 16 and 24 TPI thread pitches. Does anyone know if there is gear combos available (or gears that can be 3D printed) to achieve 16 and 24 imperial pitches ? Thanks is advance !