- Joined
- Dec 18, 2019
- Messages
- 6,441
This week came home with a used MSC carbide grinder. Found it on the Market Place. Price was ok, but knew this was going to be a project. It is indeed looking like it will take a while to get it in shape. Has pretty good bearings, it takes quite a while to wind down, so much so that I asked the guy if it was still plugged in. I thought the power switch was broken or constant on. No, just a long coast down.
Got it home without much problem and started to look at it. Hmm, a little ugly. Some knucklehead had jammed in something, hitting the socket head cap screws on one side. The usual Allen wrenches wouldn't fit. The silicon carbide wheel was totally worn down, and the white alumina wheel was pretty worn, but I knew that when I first saw the listing. What did surprise me was how expensive new type 2 wheels were. I'll nearly double the value of the grinder by putting new wheels on.
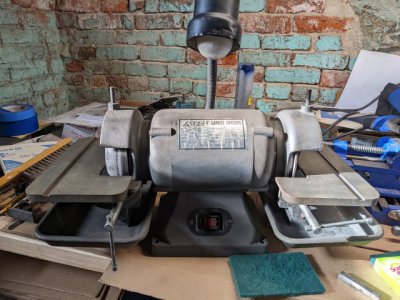
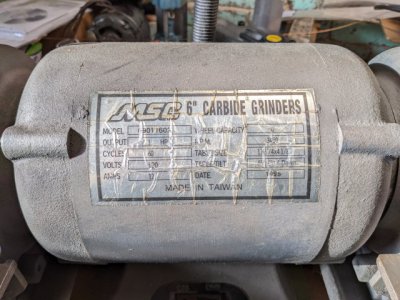
This grinder has been figuratively used and put away wet. I don't think it has ever been cleaned. There's crud, grease and carbide and alumina grit everywhere. So I have been cleaning this up. I used Krud Kutter to get out the bulk of the carbide dust, wetting it down and scraping and removing it. I've gone through quite a bit of paper towels doing this. I have cleaned the water trays, and the front side of the grinder.
Removing the wheels were a little tricky without air in the shop. The easy way would be to use an impact wrench. But I managed to eventually remove both the RH and LH threaded nuts. One wheel came off easy, the other wheel had the damaged SHC screws. I used a file and a piece of HSS to scrape out the steel that had be smeared into the hex recess. It wasn't quite enough, so for one of the screws I had to tap in an allen wrench with a hammer into the socket.
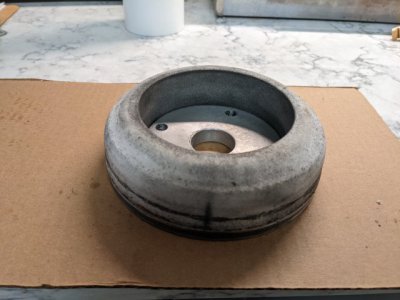
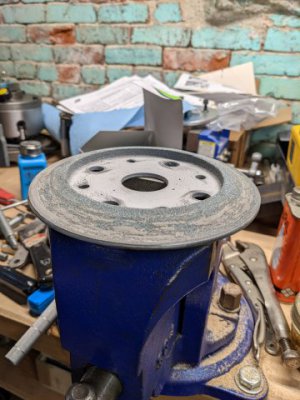
Had an interruption in the form of a non-functional hot water heater interfere with this project. It's good to get back to this.
Ordered and received a diamond point tool. Now it appears I need to make a tool holder as it is pretty short. Think I can dress the white wheel.
Got it home without much problem and started to look at it. Hmm, a little ugly. Some knucklehead had jammed in something, hitting the socket head cap screws on one side. The usual Allen wrenches wouldn't fit. The silicon carbide wheel was totally worn down, and the white alumina wheel was pretty worn, but I knew that when I first saw the listing. What did surprise me was how expensive new type 2 wheels were. I'll nearly double the value of the grinder by putting new wheels on.
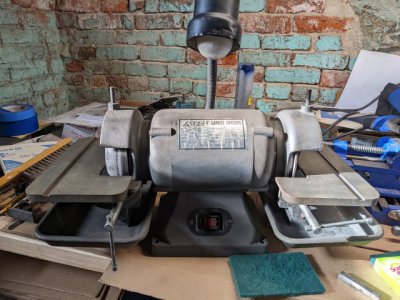
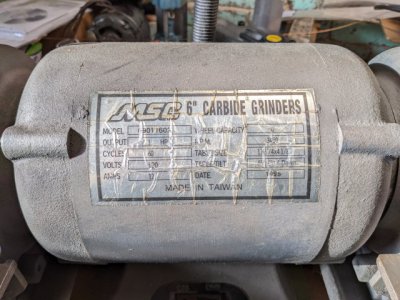
This grinder has been figuratively used and put away wet. I don't think it has ever been cleaned. There's crud, grease and carbide and alumina grit everywhere. So I have been cleaning this up. I used Krud Kutter to get out the bulk of the carbide dust, wetting it down and scraping and removing it. I've gone through quite a bit of paper towels doing this. I have cleaned the water trays, and the front side of the grinder.
Removing the wheels were a little tricky without air in the shop. The easy way would be to use an impact wrench. But I managed to eventually remove both the RH and LH threaded nuts. One wheel came off easy, the other wheel had the damaged SHC screws. I used a file and a piece of HSS to scrape out the steel that had be smeared into the hex recess. It wasn't quite enough, so for one of the screws I had to tap in an allen wrench with a hammer into the socket.
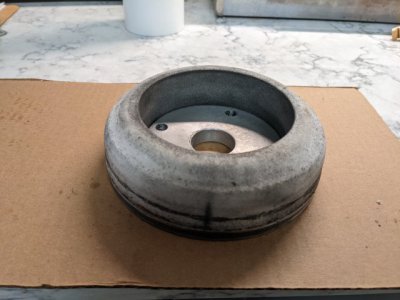
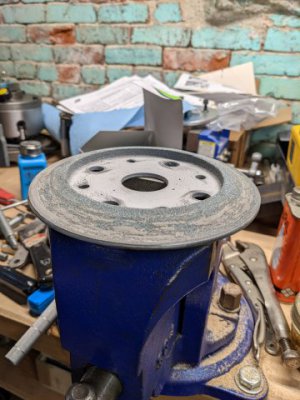
Had an interruption in the form of a non-functional hot water heater interfere with this project. It's good to get back to this.
Ordered and received a diamond point tool. Now it appears I need to make a tool holder as it is pretty short. Think I can dress the white wheel.