I assume collets are the right way to hold end mills and not the chuck.
Would a metric collet set be ok?
Or must it be inch size?
would like to locate in Canada
https://www.ebay.com/sch/i.html?_fo...ic=2&LH_SubLocation=1&_sop=12&_dmd=1&_ipg=200
Also, what is the cheapest possible DRO option for this little machine?
Would a metric collet set be ok?
Or must it be inch size?
would like to locate in Canada
https://www.ebay.com/sch/i.html?_fo...ic=2&LH_SubLocation=1&_sop=12&_dmd=1&_ipg=200
Also, what is the cheapest possible DRO option for this little machine?
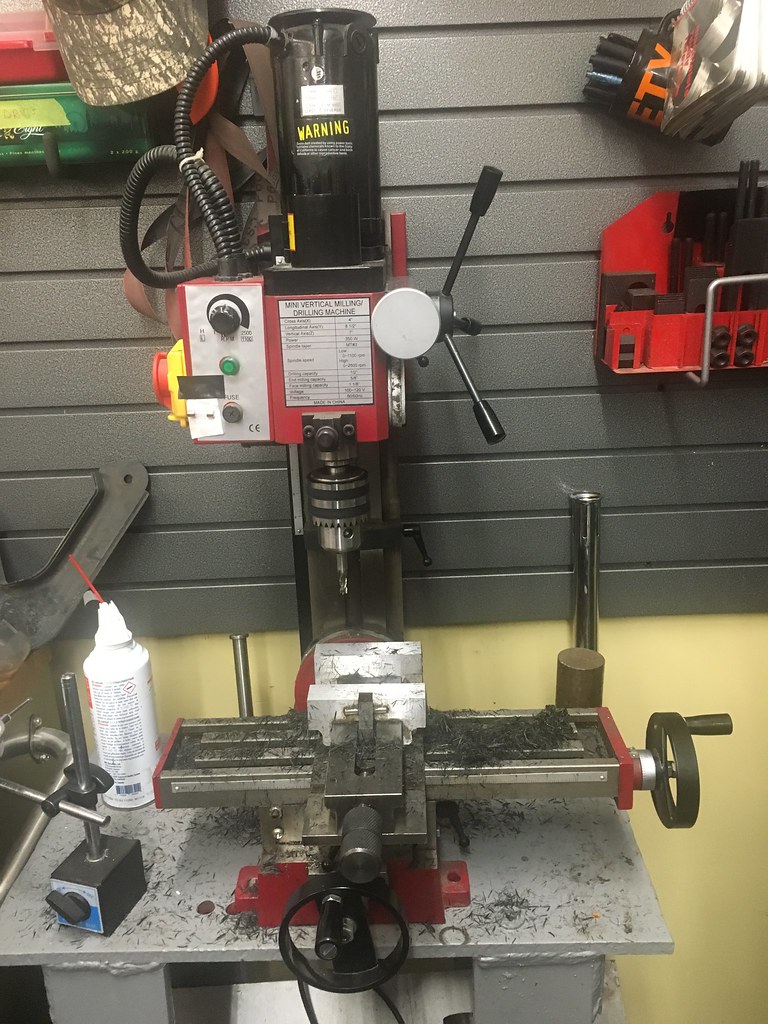