- Joined
- Aug 22, 2012
- Messages
- 4,121
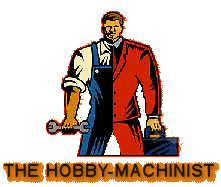
The Giant Binocular
I rounded the ends at 500rpm with the 12mm end mill. Thanks to Bob Korves for suggesting the speed. Virtually a hot knife through butter. all 6 done with the handle I used as an aid. To weld them to the base I clamped a length of steel to the legs as guide to keep the angles correct...
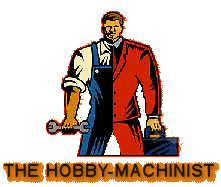
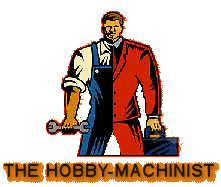
The Giant Binocular
Your idea has merit but not using the satellite dish. I will be flexing the 12" mirrors like this http://www.skyandtelescope.com/wp-content/uploads/Adler-MirrorFlex.pdf It may be worth experimenting with the largest circle you could cut from those mirrors, supporting it on a rubber ring and just...
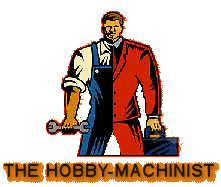
for some aluminium I cut on the table saw. These were cut without a fence.
The chips get everywhere as others have said.