- Joined
- Dec 18, 2019
- Messages
- 6,464
Recently bought a 20lb melting pot for casting lead. Had a lot of trouble maintaining the lead temperature for casting. So I decided to make a PID controller box for the Lee melting pot.
Bought a REXC100 PID controller kit, which included a solid state relay and a weird heat sink. Don't care for the heat sink really, it's adequate, but feels top heavy and strange to me. The kit also came with a type K thermocouple.
To house it all, I ended up getting a surplus ammo box. (100 rounds 50 cal) I will put in a fan on the solid state relay heat sink to keep it cool. Might not be necessary, but it will make me feel better.
The power cord come in from the back through a cable gland. The output of the SSR will be connected to a 110V power socket, where the lead pot plugs in. Also in the design is a power switch, a mini-circuit breaker, and a type K thermocouple socket. I designed this in FreeCAD. It's my best guess at how it will go together. The ammo box has a hinged lid, with a handle both of which are not yet shown. The entry and exit ports for the air will be screened to keep the whatever out. The model isn't quite complete, mostly because I don't know a few of the dimensions for the fan, and a couple other components.
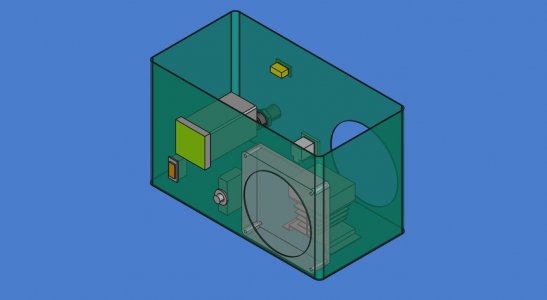
The steel thickness is about 0.056". At this point, I'm not quite sure how to manage the big ~110mm holes in the steel. I am not fond of large hole saws, especially on sheet metal. Haven't seen any annular cutters that big, nor do I want to pay for one that size! I could always drill lots of holes, then file it. Could I use a boring head on a mill? Would I need to stuff the inside of the box with something to give the sheet metal some support?
Is there a way to get a hole saw to work? Found a 100 and 110mm hole saw for $30. How do you keep one of these from grabbing and throwing the box?
Bought a REXC100 PID controller kit, which included a solid state relay and a weird heat sink. Don't care for the heat sink really, it's adequate, but feels top heavy and strange to me. The kit also came with a type K thermocouple.
To house it all, I ended up getting a surplus ammo box. (100 rounds 50 cal) I will put in a fan on the solid state relay heat sink to keep it cool. Might not be necessary, but it will make me feel better.
The power cord come in from the back through a cable gland. The output of the SSR will be connected to a 110V power socket, where the lead pot plugs in. Also in the design is a power switch, a mini-circuit breaker, and a type K thermocouple socket. I designed this in FreeCAD. It's my best guess at how it will go together. The ammo box has a hinged lid, with a handle both of which are not yet shown. The entry and exit ports for the air will be screened to keep the whatever out. The model isn't quite complete, mostly because I don't know a few of the dimensions for the fan, and a couple other components.
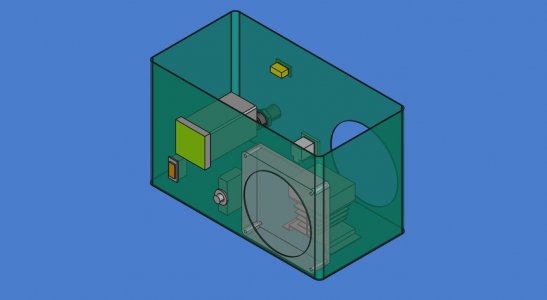
The steel thickness is about 0.056". At this point, I'm not quite sure how to manage the big ~110mm holes in the steel. I am not fond of large hole saws, especially on sheet metal. Haven't seen any annular cutters that big, nor do I want to pay for one that size! I could always drill lots of holes, then file it. Could I use a boring head on a mill? Would I need to stuff the inside of the box with something to give the sheet metal some support?
Is there a way to get a hole saw to work? Found a 100 and 110mm hole saw for $30. How do you keep one of these from grabbing and throwing the box?