This is my micrometer Stop based on tubalcain's video on YouTube (if you haven't seen his videos you are missing out!)
It fits well, has a graduated dial and the bluing came out perfect!
The dial is off a little bit though, I have learned the hard way that there should be 49 divisions on it, not 50 so it has an extra hash mark (lol), but it looks right. I used red nail polish to highlight the marks.
It just has one problem:. It moves! When I tighten the knob down as hard as I can by hand it seems really tight; I can't move it by hand, but as soon as the carriage touches it, it moves. If I run the carriage by hand it moves with the slightest touch and when the carriage is under power (not threading though!) It pushes it right allong the ways.
Did I build it wrong or does it just take a lot more clamping force to resist the carriage?
Here are a couple pics of the pieces:
Sent from my Pixel 6 Pro using Tapatalk
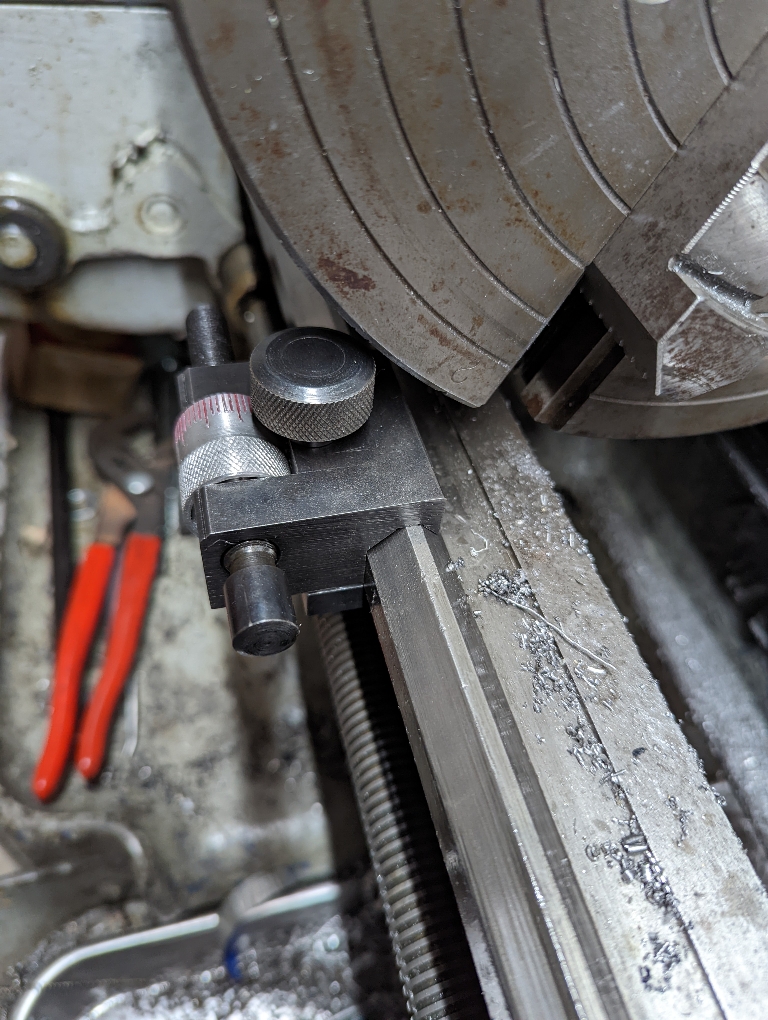
It fits well, has a graduated dial and the bluing came out perfect!
The dial is off a little bit though, I have learned the hard way that there should be 49 divisions on it, not 50 so it has an extra hash mark (lol), but it looks right. I used red nail polish to highlight the marks.
It just has one problem:. It moves! When I tighten the knob down as hard as I can by hand it seems really tight; I can't move it by hand, but as soon as the carriage touches it, it moves. If I run the carriage by hand it moves with the slightest touch and when the carriage is under power (not threading though!) It pushes it right allong the ways.
Did I build it wrong or does it just take a lot more clamping force to resist the carriage?
Here are a couple pics of the pieces:
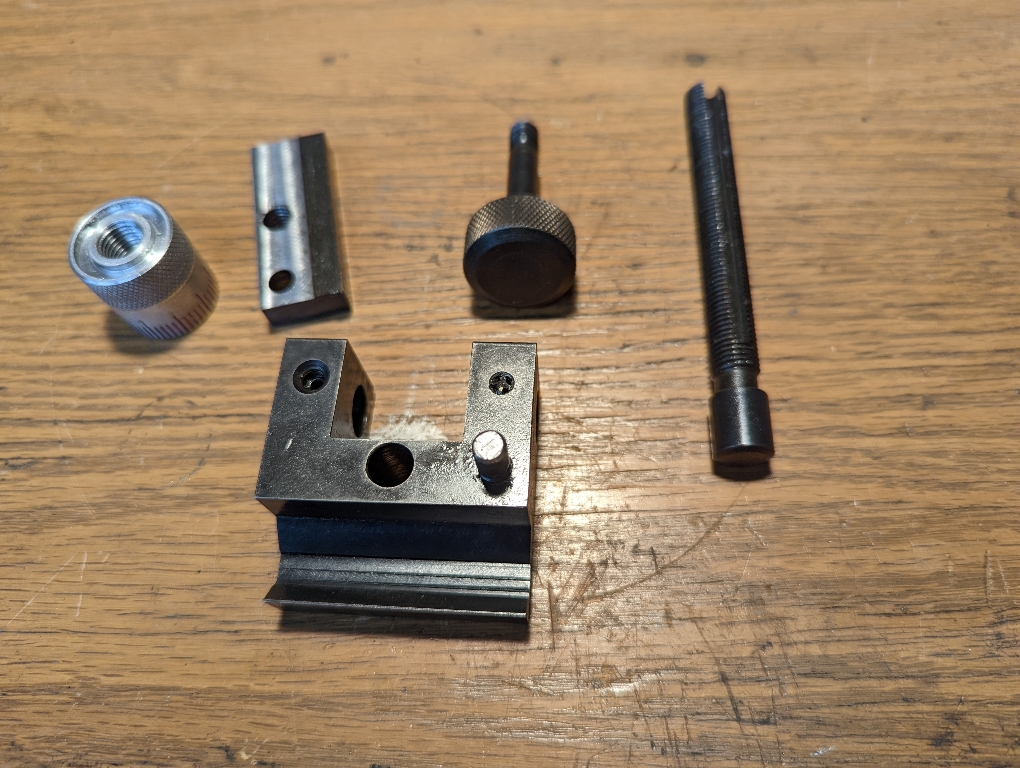
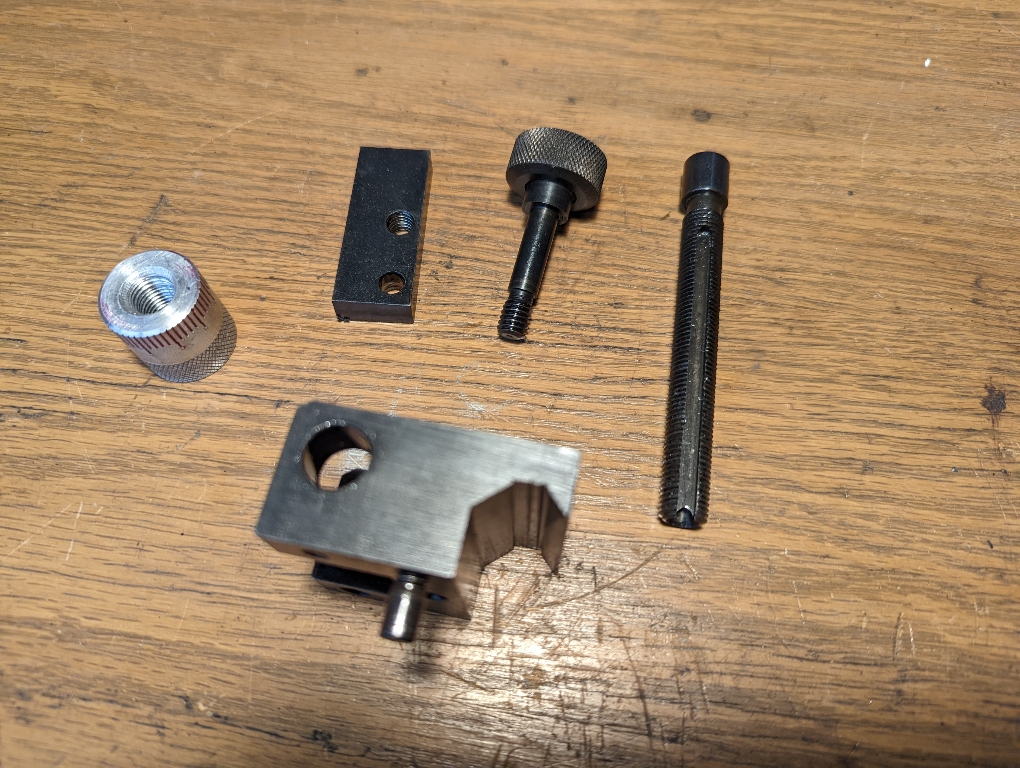
Sent from my Pixel 6 Pro using Tapatalk