I am wondering if there is any affordable chance of upgrading the tailstock drill chuck on my Sherline lathe. My main use of the lathe is making fishing rod ferrules, and a whole lot of drilling and reaming in thin-walled pieces is involved. I have a feeling that the Rohm chuck that came with it is not the most precise. I really don't know how to assess the quality of a replacement other than price. A $100 chuck like this Jacobs 3/8 looks good to me: https://www.mscdirect.com/product/details/08590655 and is in my budget. If a better chuck would cost way more I would pass.
Since someone would ask, the reason I suspect my chuck is this discussion on the Beginners forum:
www.hobby-machinist.com
If I put a dead center in the headstock and a quality drill rod in the tailstock chuck, I can consistently move the drill rod around wrt to the dead center by rotating the MT0 chuck arbor in the tailstock. I hope that makes some sense.
Since someone would ask, the reason I suspect my chuck is this discussion on the Beginners forum:
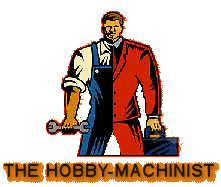
Is it normal for lathe tailstock drill to lift up when contacting work?
As a machining hobbyist and a not-retired person who works long hours often out of town, I think it is safe to admit that I spend more time watching machining videos on YouTube than I do actually machining. Most often in bed when I'm supposed to be sleeping but the ol cranial flywheel can't be...
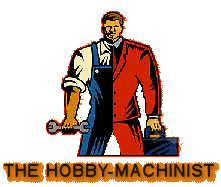
Last edited: