I have one of these LMS 3" screwless vises I bought about 12 years ago:
littlemachineshop.com
It worked out okay over the years on a mini-mill, but after getting a larger 5550/Siegx2.7 mill recently I've noticed it's harder and harder to get a good grip on the workpiece with it.
Today for example I had a rectangular piece of 1/8"-thick aluminum to make some holes in. I put a couple of parallels against each jaw of the vise, put the workpiece in on top of them, then push the jaws together as forcefully as possible as I tighten the hex bolt on top of the vise. No matter how much I pushed, the workpiece ended up just sliding back and forth.
I thought maybe there was some grit inside the vise, so I disassembled, cleaned and reassembled it, but this didn't cure the problem.
Is there some issue with my technique, or should I be thinking about a new vise? (A larger one having been on my wanted list for a while anyway.)
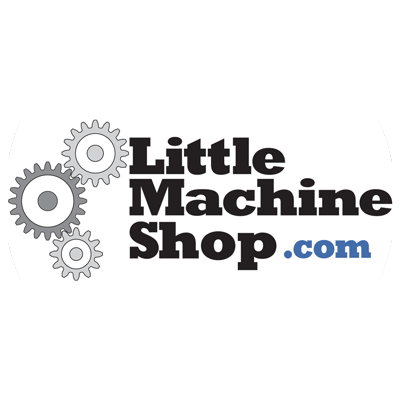
Vise, 3" Screwless 1590
Screwless Vises 1590 Hardened and Precision Ground; Square and Parallel within 0.0005"; Ground "V" Way; This high precision toolmakers screwless vise ...
It worked out okay over the years on a mini-mill, but after getting a larger 5550/Siegx2.7 mill recently I've noticed it's harder and harder to get a good grip on the workpiece with it.
Today for example I had a rectangular piece of 1/8"-thick aluminum to make some holes in. I put a couple of parallels against each jaw of the vise, put the workpiece in on top of them, then push the jaws together as forcefully as possible as I tighten the hex bolt on top of the vise. No matter how much I pushed, the workpiece ended up just sliding back and forth.
I thought maybe there was some grit inside the vise, so I disassembled, cleaned and reassembled it, but this didn't cure the problem.
Is there some issue with my technique, or should I be thinking about a new vise? (A larger one having been on my wanted list for a while anyway.)