F
Firestopper
Forum Guest
Register Today
Got some additional time in on the die table. I had a decent piece of left over 1/4" plate so I went to work on the top for the table. Its 32" X 48" and over hangs a bit over 7" on the indexing end of the table, the sides have two inches of over hang and push end has 1" over hanging. I only needed to rip long one 48" side as the rest was sheared and squared. I did spend a bit of time with a 5" flap wheel producing radius all the way around the edge. I test fitted the table loaded and ended up flipping the plate onto its better face. Ran a 9" hand grinder with new wheel flat for a poor mans surface grind. The table will be primed and painted (frame only) the usual industrial grey to match all other shop made equipment. I decided not to secure the top via fasteners. I had a small 20" piece of 1/8" X 1" x 1" angle iron. Cut six 2" long pieces and radius the corners to finish the clips. Laid out the top and tac welded the clips to entrap the inside of the frame for a drop in snug fit. Removing the top will make it super easy to spay the primer/paint and would also allow any future modifications to the table without interference.
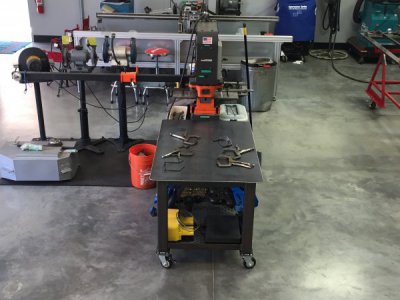
Decided to fab up a push bar out of 12ga. 1" round tubing. Pull a scrap piece that was a little long and laid it out for knurling and two 90º bends. On the lathe, I installed the follow rest and fed the stock in from the spindle spider end as it was jus a bit too long. Dialed in the chuck and spider and set the follow rest up. Placed oil and knurled at 500RPM with .174 of feed. Flipped and repeated. Turned out pretty good, one pass at .042 depth. The proximity carriage stop was used to stop things at the end of pass leaving a nice termination of knurl.
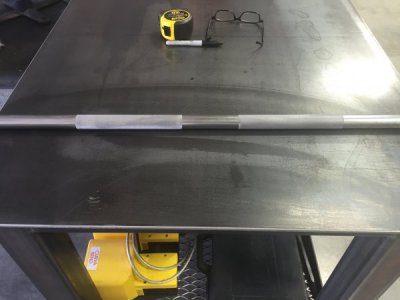
Set up the Ercolina bender and bent two 90º. Laid out for a 40º angle cut on band saw (left /right cut).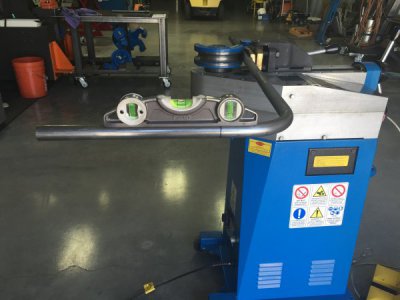
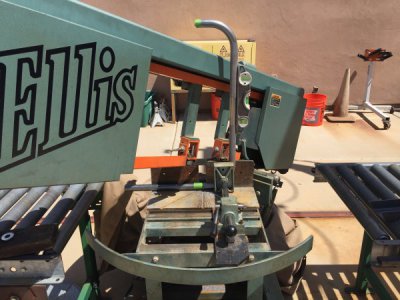
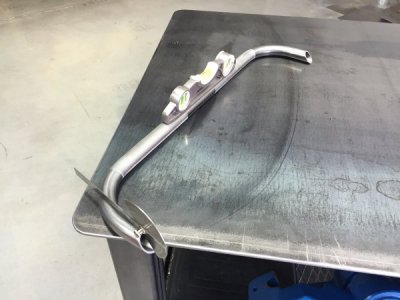
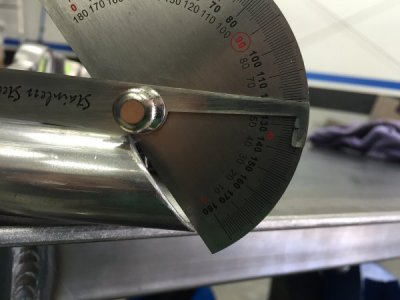
Welded handle.
So the the top of the bar is even with the top surface incase I use the cart/table to move long heavy pieces around the shop.
Leveled, and welded.
Good productive day. Its always fun to build for yourself.
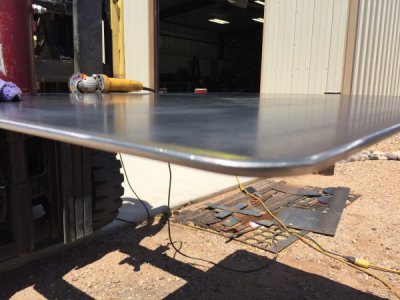
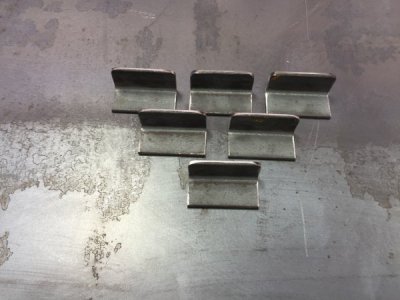
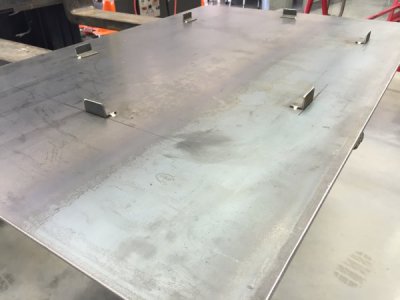
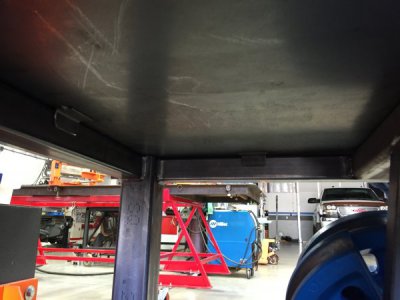
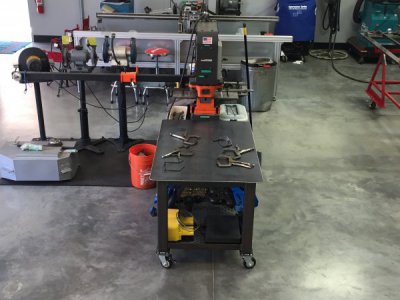
Decided to fab up a push bar out of 12ga. 1" round tubing. Pull a scrap piece that was a little long and laid it out for knurling and two 90º bends. On the lathe, I installed the follow rest and fed the stock in from the spindle spider end as it was jus a bit too long. Dialed in the chuck and spider and set the follow rest up. Placed oil and knurled at 500RPM with .174 of feed. Flipped and repeated. Turned out pretty good, one pass at .042 depth. The proximity carriage stop was used to stop things at the end of pass leaving a nice termination of knurl.
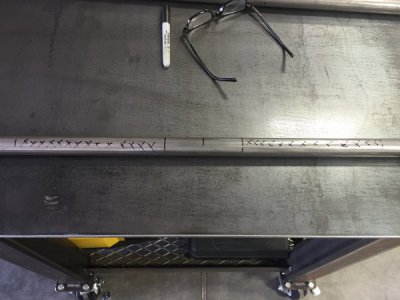
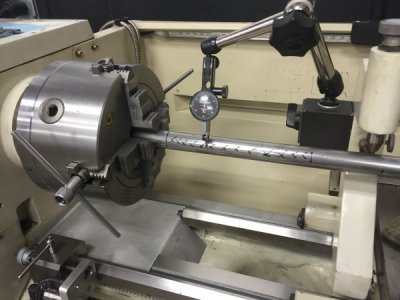
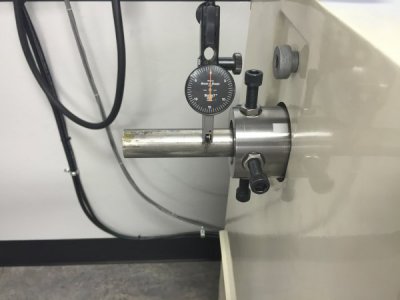
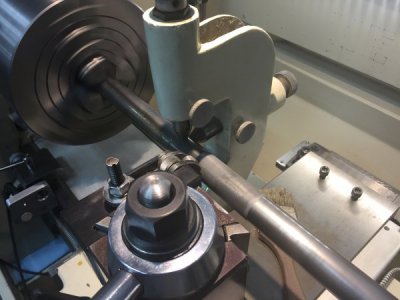
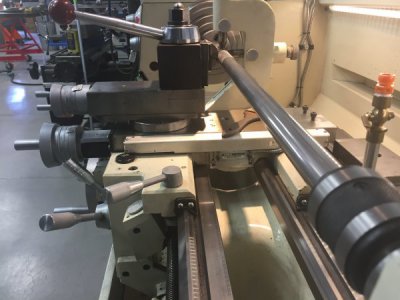
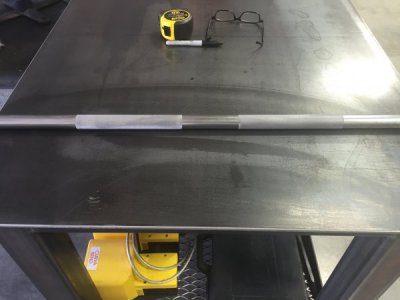
Set up the Ercolina bender and bent two 90º. Laid out for a 40º angle cut on band saw (left /right cut).
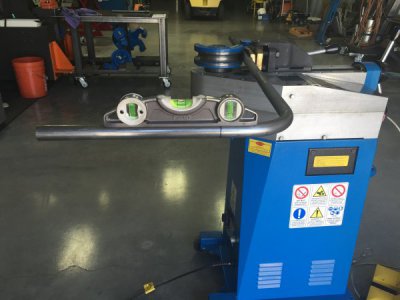
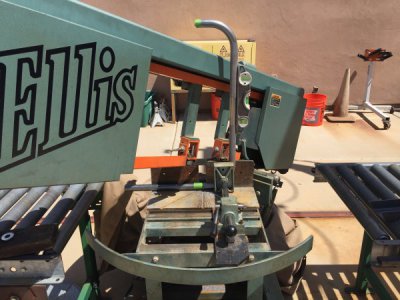
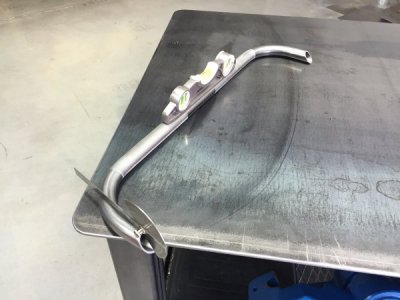
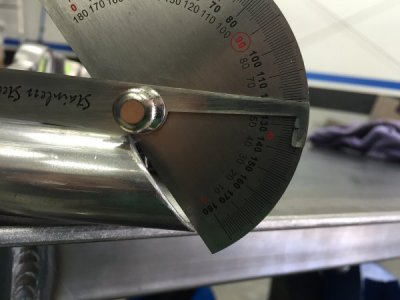
Welded handle.
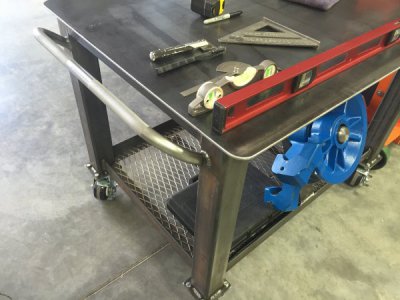
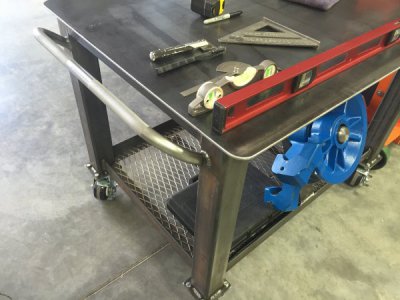
Leveled, and welded.
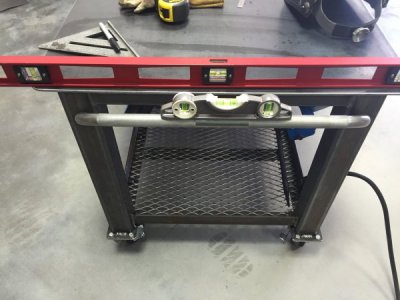
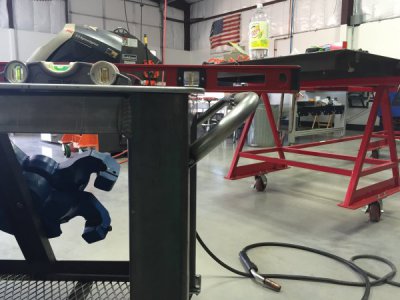
Good productive day. Its always fun to build for yourself.
Last edited by a moderator: