- Joined
- Nov 26, 2018
- Messages
- 261
I will write with more detail tonight
Sorry for delay, the posts above effective said what I would have said about buying options. One benefit of making a low speed press as your first project with gears, is that the mechanics are very forgiving. You aren't giving this a 100k mile powertrain warranty so the involute profile need not be exact. In regard of craftsmanship and what to make or buy. You may as well cut your own pinion. Indexing precise components is an intimidating yet rewarding experience. Also you may want to later change the pinion to a larger diameter if you find that the retract takes too many revolutions and the forces is needlessly minimal.
For making the rack, if you go about those tapered end mills, don't rely on Z zero being a function tool tip contact and depth. like a thread, take a shallow progression of cuts place a reference pin between the tooth flanks and measure to rack back surface to pin tangent, then machine to full depth.
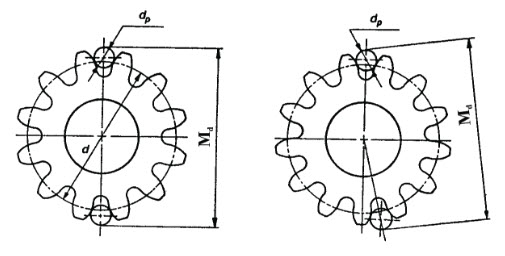
Dimension Over Two Balls | WENZEL America
The standard parameters that are output when inspecting a gear are helix, profile, pitch, and runout. However, I find almost every customer asks for an additional parameter to be output – dimension over two balls (or pins). In this blog, I explain what this measurement entails as well as why it...

