- Joined
- Oct 14, 2013
- Messages
- 997
A thread in which I pull my mill apart and make it, hopefully, better.
Goals:
Install new swarf covers
Add pressure lube to everything
Re-do the flexible swarf guards
Install DROs on Z and quill
Goals:
Install new swarf covers
Add pressure lube to everything
Re-do the flexible swarf guards
Install DROs on Z and quill
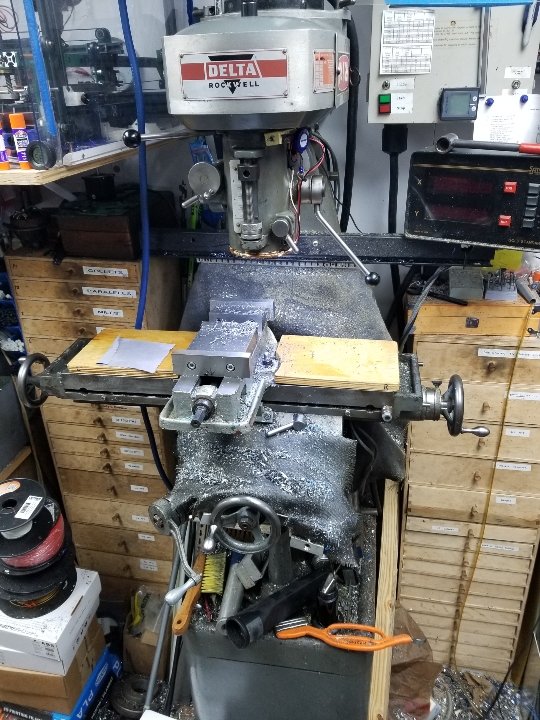