So I was just cutting a slot in a piece of 4140 steel. DOC was .380" rpm was 2170 (max mill speed) according to the little machine shop calculator my ipm SHOULD be 33, I figure I was going closer to 2 ipm. I made it 75% through the cut with a carbide 1/2” roughing endmill (Chinese) before it burned the corners off the endmill (the sides look good still) so my question is: was I going to fast or too slow?
Sent from my Pixel 6 Pro using Tapatalk
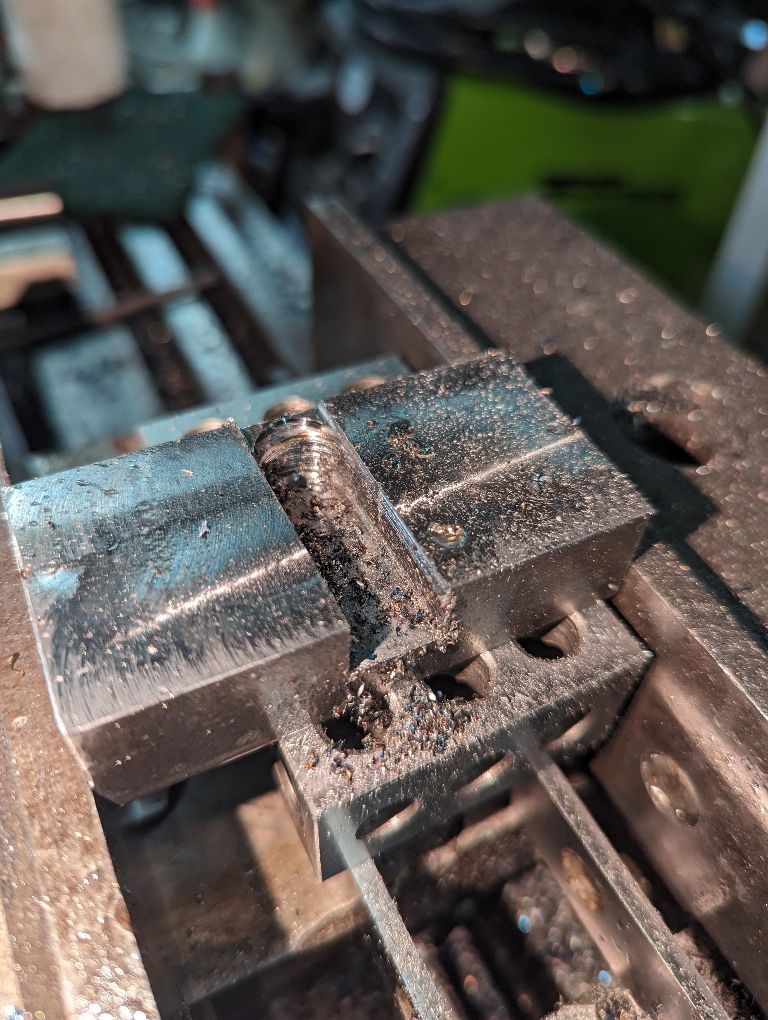
Sent from my Pixel 6 Pro using Tapatalk