- Joined
- Dec 3, 2017
- Messages
- 1,909
The 6” Atlas could be purchased with Timken taper roller bearings too. The one pictured in this thread has sleeve bearings.
As far as I know, the only thing you couldn’t get on the 6” model was a qcgb.
Also, the OP expressed interest in a 10” model. Pretty sure most links others have posted have been 6” machines.
I recommend the OP spend some time reading in the Atlas and Craftsman machines sub forum, if an Atlas is what you’re looking for.
www.hobby-machinist.com
As far as I know, the only thing you couldn’t get on the 6” model was a qcgb.
Also, the OP expressed interest in a 10” model. Pretty sure most links others have posted have been 6” machines.
I recommend the OP spend some time reading in the Atlas and Craftsman machines sub forum, if an Atlas is what you’re looking for.
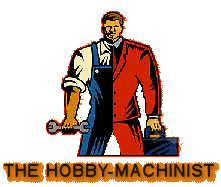
ATLAS, CRAFTSMAN, COMPANION, DUNLAP & AA
Discuss any issues dealing with Atlas & Atlas-Clausing lathes, drill presses, mills, etc. in this forum.
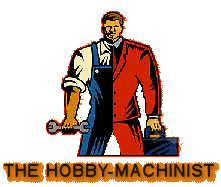