- Joined
- Feb 18, 2022
- Messages
- 36
Continued my puttering around in the garage a little last night. Got my saddle lock from Logan.
Also started figuring out what to do for a motor support pedestal. The threads for the pedestal support are a fine thread 5/8-18, which is just odd enough that the local home improvement stores don't carry those bolts, though I was able to find a 5/8-18 set screw, which got me just enough threads that I can work with it. If not, it looks like I could swing by my local Fastenal and pick some up.
Man, if only I had a lathe so that I could thread my....oh right.
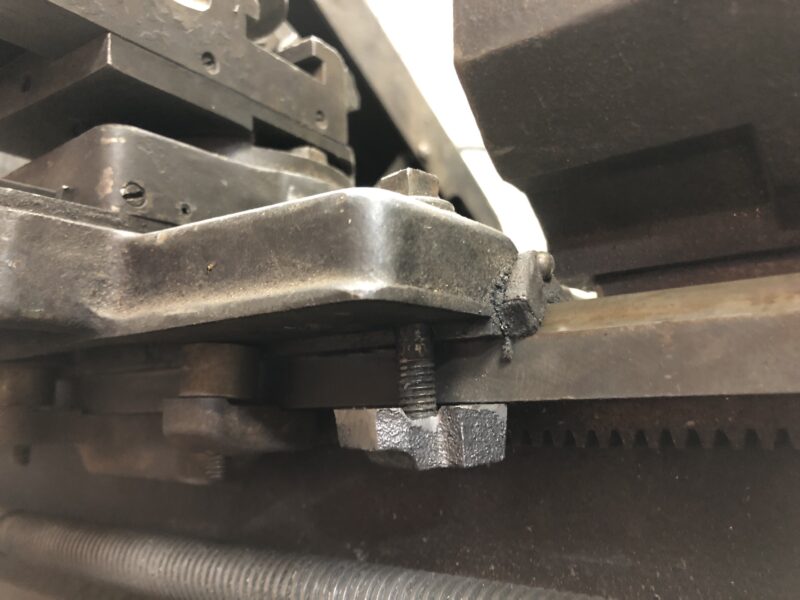
Also started figuring out what to do for a motor support pedestal. The threads for the pedestal support are a fine thread 5/8-18, which is just odd enough that the local home improvement stores don't carry those bolts, though I was able to find a 5/8-18 set screw, which got me just enough threads that I can work with it. If not, it looks like I could swing by my local Fastenal and pick some up.
Man, if only I had a lathe so that I could thread my....oh right.