- Joined
- Jan 20, 2016
- Messages
- 602
I am just about finished with the new hardware for mounting the new ballscrews and protecting the motors better. I have a pictures to share.
This is the new Y axis assembly with all of the guards installed. This should keep the chips and coolant off the motor, bearings, and coupler.
Here it is with the covers removed. I anticipate it being much more rigid with the shorter and thicker risers and a thick motor plate, rather than thinner and longer risers attached directly to the motor.
Another angle.
This is the new X axis. This one is also a little bit on the heavy side, but I relieved material everywhere I could to lighten it up. The worst of it is the massive bearing block.
This is the back side. The part on the right will have the electrical connections for the motor (1 for power, one for signal) and the other 2 will be input for the 4th axis and a QD connector for output. This way when I remove the 4th axis, I can just unplug it from the block and cover the connector. The left side is for an air supply. It will have input and output for 2 air connections. One for actuating the brake, one for retracting it. If I ever make a pneumatic fixture or pneumatic vise, the air supply could also be used for that.
Here is the inside. Again it will be better protected and this design should be stronger than the current set up.
All of the parts use pins to make alignment and assembly much easier, so the fit will be much better than my current design. The pins may also add a little bit of strength to the set up as well.
This is the new Y axis assembly with all of the guards installed. This should keep the chips and coolant off the motor, bearings, and coupler.
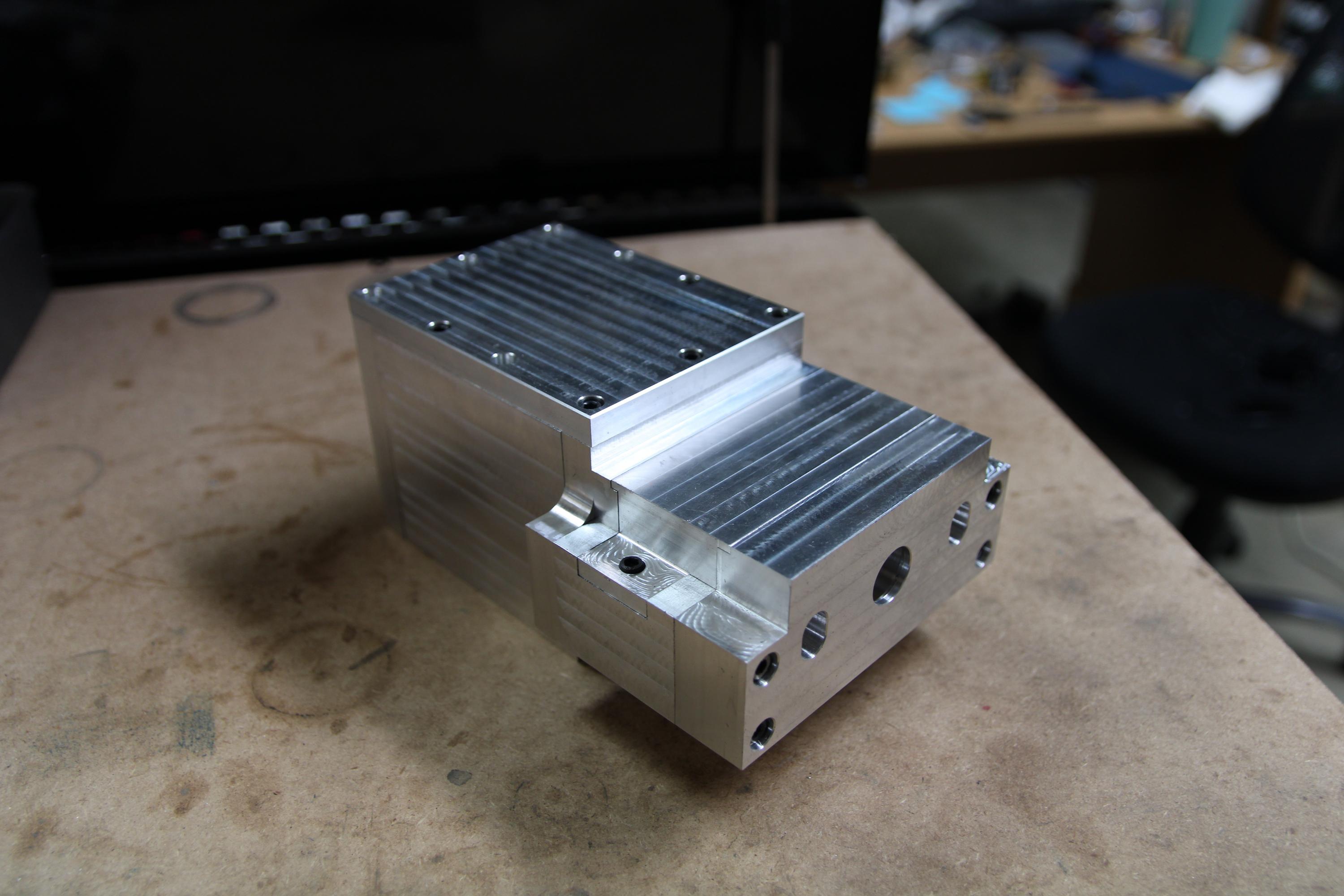
Here it is with the covers removed. I anticipate it being much more rigid with the shorter and thicker risers and a thick motor plate, rather than thinner and longer risers attached directly to the motor.
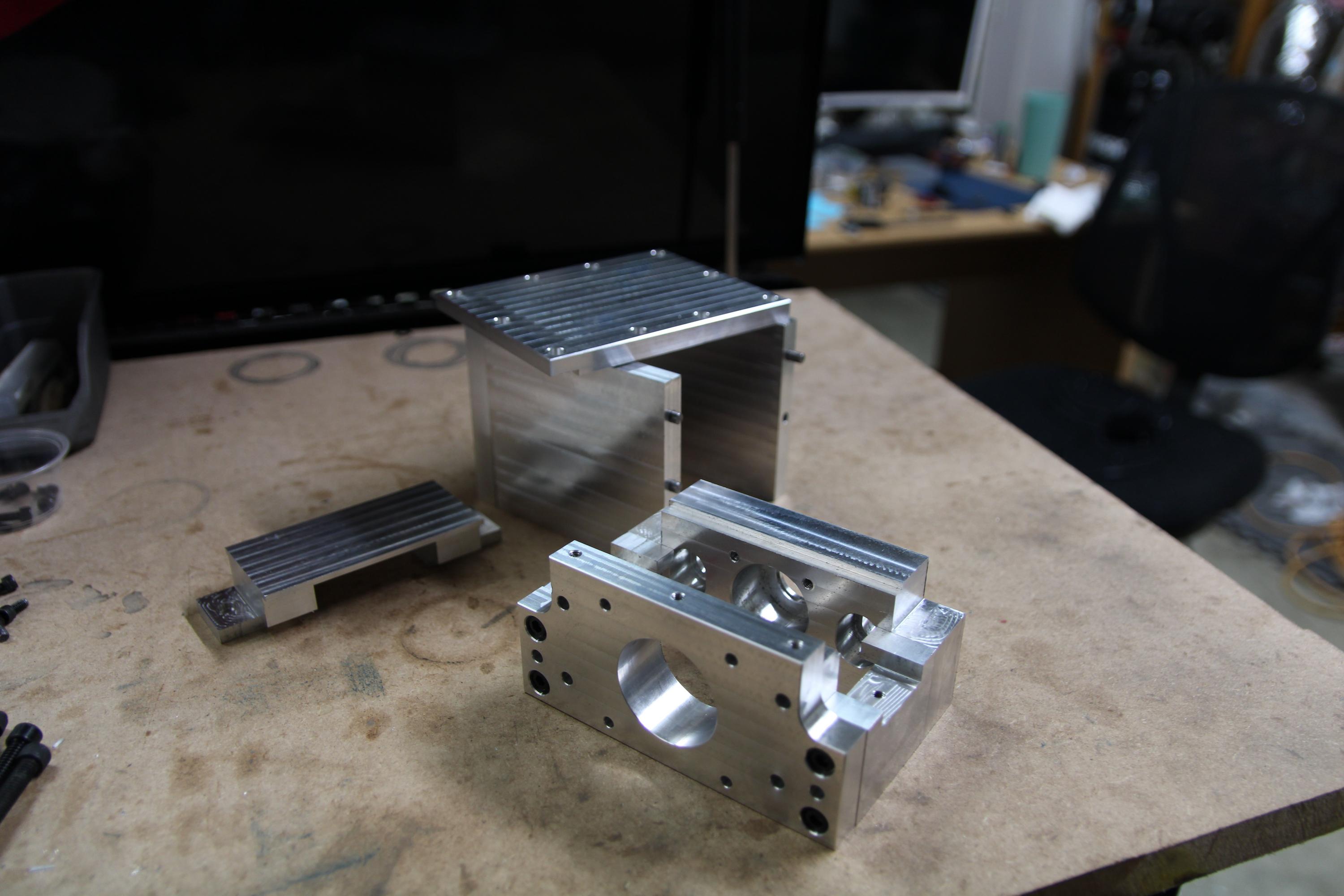
Another angle.
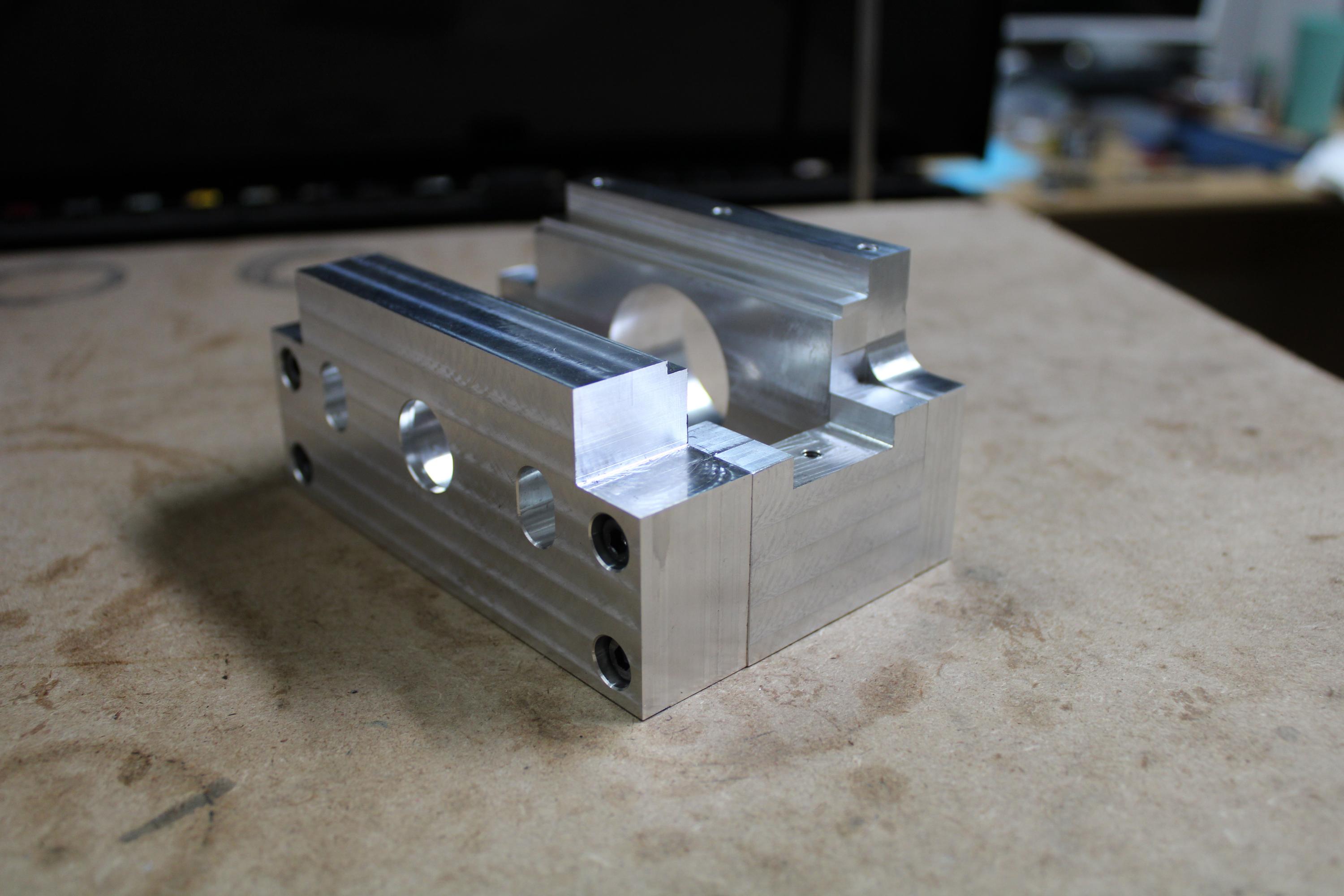
This is the new X axis. This one is also a little bit on the heavy side, but I relieved material everywhere I could to lighten it up. The worst of it is the massive bearing block.
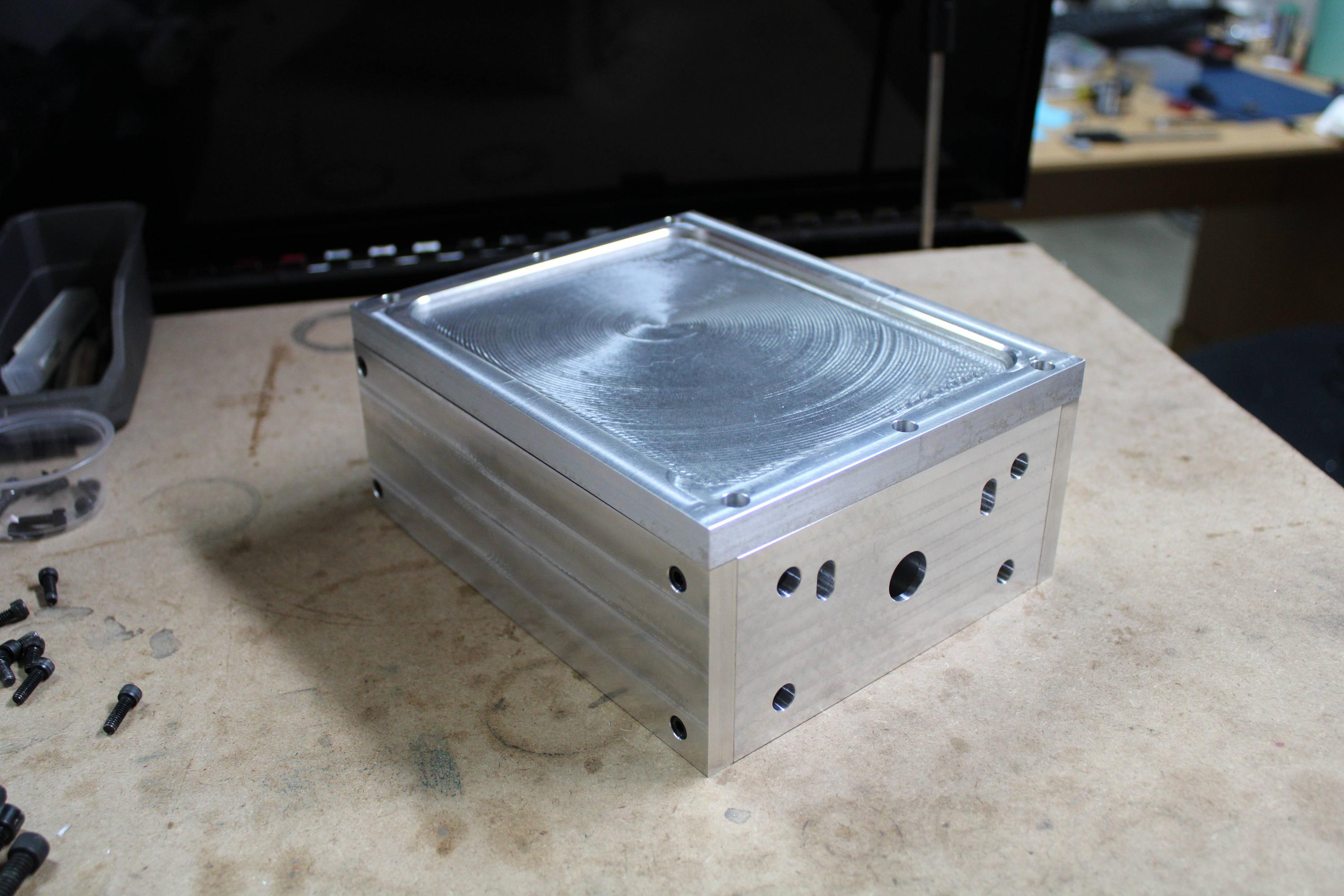
This is the back side. The part on the right will have the electrical connections for the motor (1 for power, one for signal) and the other 2 will be input for the 4th axis and a QD connector for output. This way when I remove the 4th axis, I can just unplug it from the block and cover the connector. The left side is for an air supply. It will have input and output for 2 air connections. One for actuating the brake, one for retracting it. If I ever make a pneumatic fixture or pneumatic vise, the air supply could also be used for that.
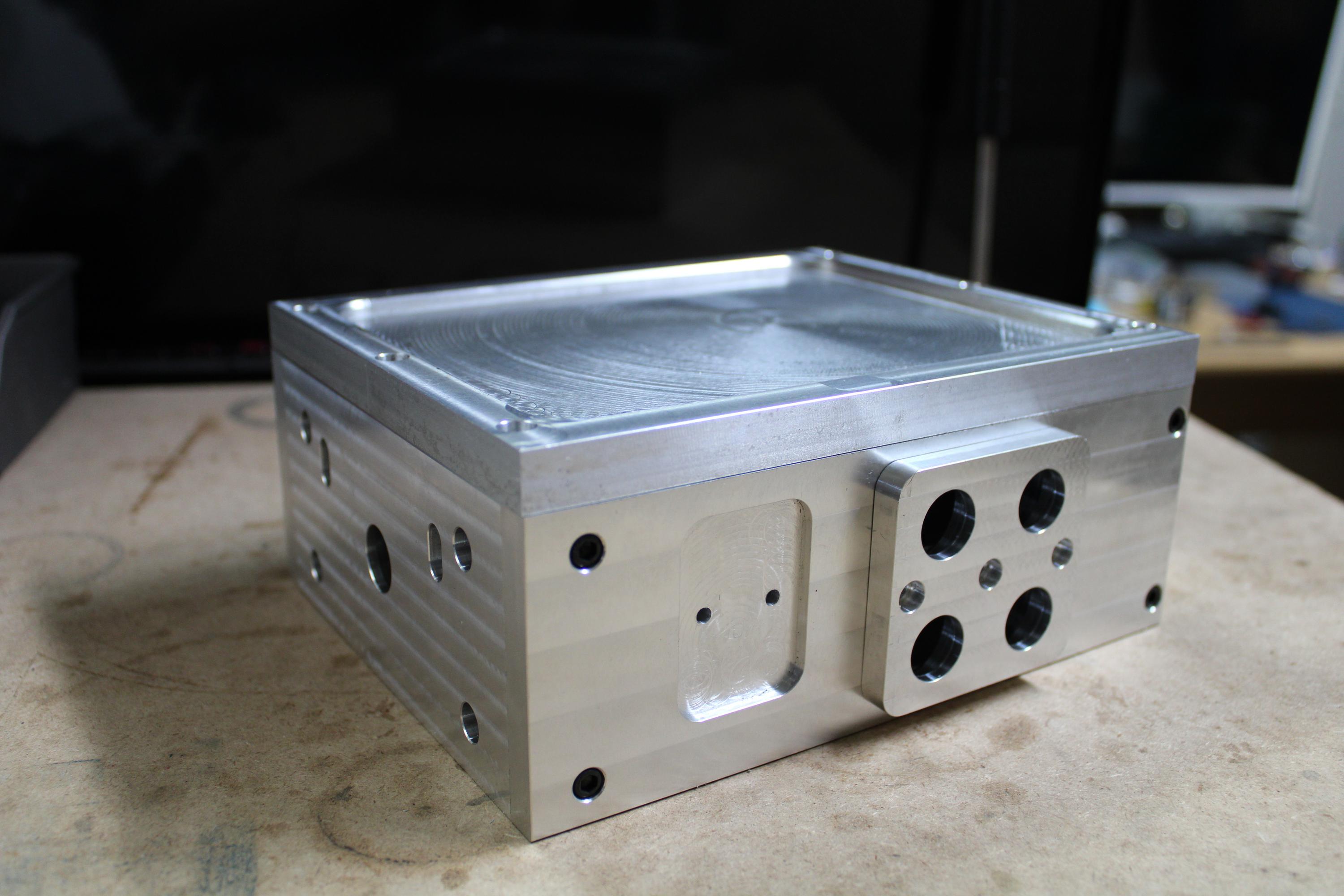
Here is the inside. Again it will be better protected and this design should be stronger than the current set up.
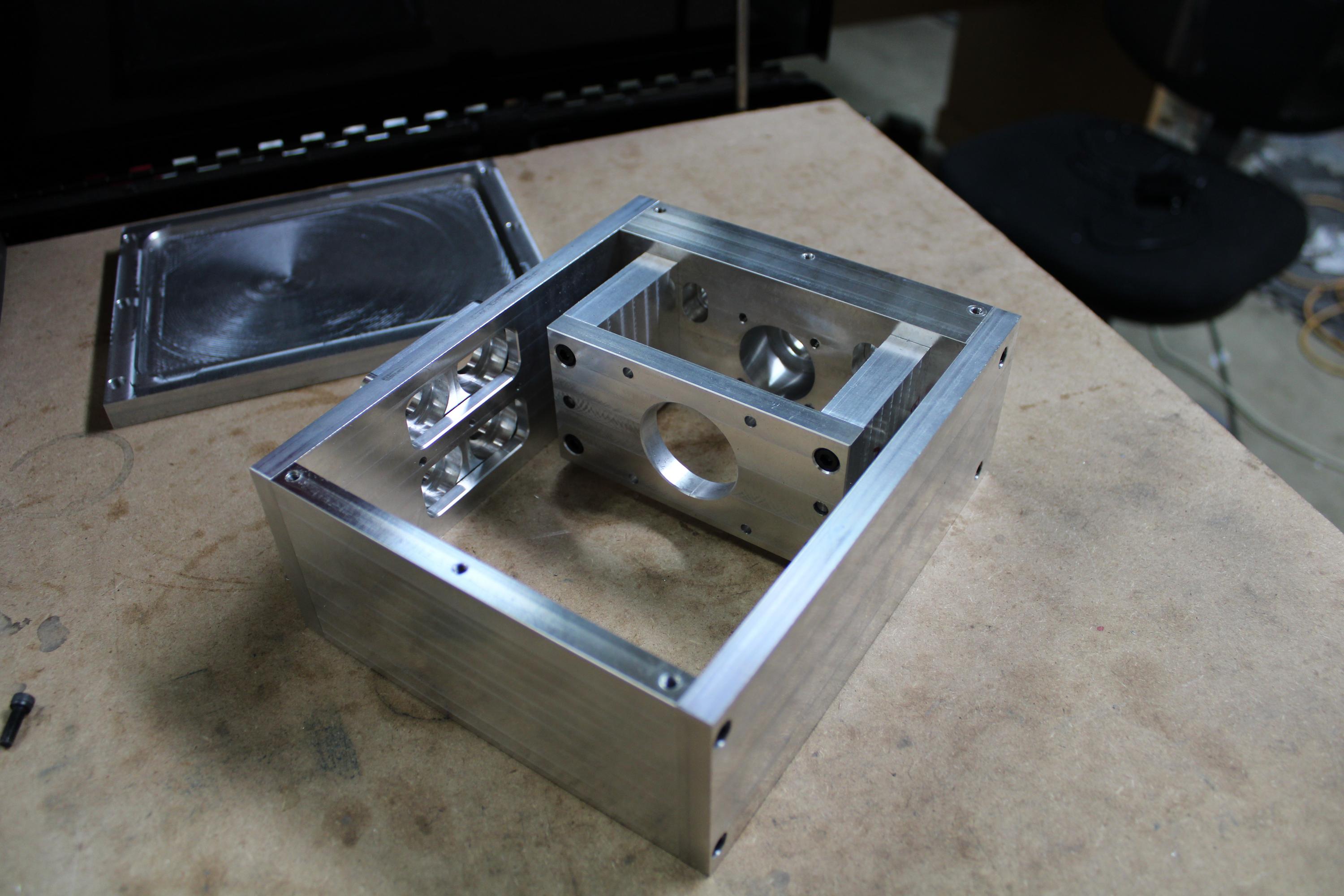
All of the parts use pins to make alignment and assembly much easier, so the fit will be much better than my current design. The pins may also add a little bit of strength to the set up as well.